- Design Approaches
- Posted
Green Rooms
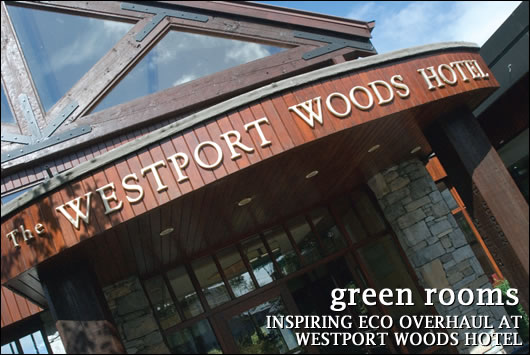
Hotels typically take a heavy toll on the environment, with large amounts of energy used for heating, hot water, lighting, air conditioning and laundry, and huge amounts of waste being landfilled each year. John Hearne visited the Westport Woods Hotel and discovered a highly successful approach to reducing environmental impact that is also yielding substantial dividends in terms of cost savings and positive publicityAs you enter the carpark of the Westport Woods Hotel, there are few outward signs of the radical environmental makeover the hotel has undergone in the past five years. Occupying a heavily wooded space just minutes from the town centre, the new Energy Cabin which stands between the main building and the adventure centre is about the only external sign of what has taken place here.
“Five years ago,” says general manager Michael Lennon, “we would have had 240 tonne of landfill. This year it’ll be under thirty. We were putting about 3Kg per sleeper into landfill, now we’ve it down to about 0.7 of a Kg per sleeper. That is the real big one.” But it’s not just about the waste stream. Overall energy consumption at the hotel fell by 400,000kWh between 2004 and 2006. In that time, C02 emissions were reduced by 125 tonnes. This year, thanks to a shift away from fossil fuels and a switch to a green electricity supplier, emissions are estimated at 350 tonnes, down from 826 tonnes in 2006. Overall, energy usage has fallen by 14.5% since 2004, this despite the fact that the area of the hotel has increased following the addition of a spa and a larger bar area. Every year over the past five, the hotel has managed to drastically improve its environmental profile, thanks to a range of measures Lennon has implemented over that time.
It began, he says, with ISO 14001. Having developed a keen interest in environmental issues while working in the hospitality sector abroad, Lennon decided to go after the environmental standard when he took over the running of the Westport Woods. It was a process that turned up all sorts of issues, leading eventually to the development of a comprehensive programme of recycling, composting, water conservation and energy and carbon reduction initiatives. Lennon established a green team, comprising members of management and the various departments. Together, they developed an environmental policy and began to move towards an entirely new way of doing things. Five years later, there are few aspects of the hotel’s operation that have been untouched.
With the cost of landfill rising and the hotel heavily dependent on traditional methods of waste disposal, this was one of the first areas to be targeted. Michael Lennon explains that change came about through a combination of things, some little, some not so little. “We managed it by going through the whole process of estimating, by reducing packaging, by recycling, by putting in a composter, by segregating waste.”
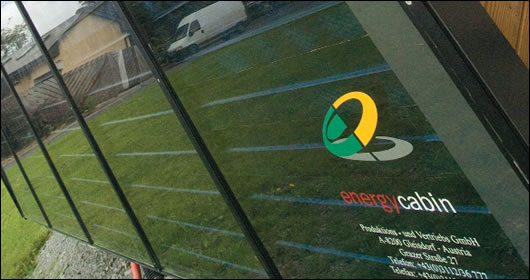
An energy cabin offers a self-contained combination of 30kW wood pellet boiler and solar panels which together will be used to provide space heating and hot water for the adjacent adventure centre
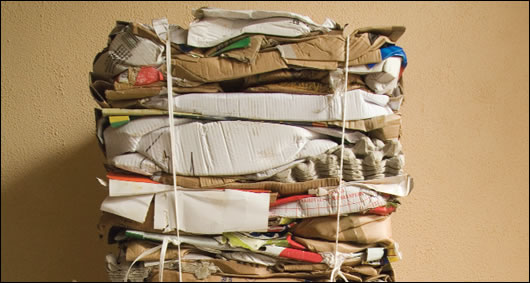
Waste that would be landfilled is avoided through concerted efforts at the Westport Woods Hotel, with cardboard bundled for recycling
Because a very substantial element of hotel waste is organic, the composter was the key investment. Lennon brought in a Swedish machine called a Big Hanna and through a leasing arrangement, he managed to actually generate a cashflow of e2,500 per year by netting leasing fees against the savings from avoiding landfill. “That was a no brainer.” He says. “We have thirteen acres of trees around the hotel. This was the first environmental thing we got involved in - I planted 2,000 trees. You’ve a lot of leaves, then there’s the grass mulch in the summer. We mix it with the kitchen waste compost and it makes a great compost.” The Big Hanna system is a flow-through composter. Using heat rather than chemicals, food waste is converted into usable compost within eight to ten weeks. The unit in the Westport Woods comfortably deals with the hotel’s entire organic waste stream. Capital investment is only part of the story however. A little joined-up thinking about the way in which waste is generated in the first place lead to fundamental changes in supply logistics. “A good example is the cornflakes in the morning. We buy them in bulk and we put them out in bowls that we clean ourselves. It’s simple little things. We don’t buy any sachet sugars, it would all be bulk sugar, tomato ketchup wouldn’t be coming in little plastic packets.”
With the composter taking care of organic waste, a process of segregation at point of disposal takes care of recylables. “Everything that can be separated and recycled, is.” says Gearóid O h-Aghmail, who runs the hotel Green Team and polices all the new systems. “We separate tins, plastic bottles and plastics, cardboard is crunched and glass is crushed in a separate machine. That glass is then reused in construction. We’re building pathways down at the back of the hotel and this glass goes in as foundation filler there. Between that and the compost being fed to the trees, we have a couple of complete cycles.”
The vital element in transforming the hotel’s environmental profile has been behavioural change. The transition to a more sustainable footing could not have happened without the buy-in of everyone working in the hotel. “The culture was like at home in the house,” says O h-Aghmail, “everything was chucked into the bin and somebody took it away.” The green team established by management to drive these changes came into its own now. “Each department has a rep who’s part of our green team, so every couple of months we get together; the kitchen, the reception, office, leisure centre, spa, restaurant and bar. Everyone buys in and everyone keeps an eye on how his or her department is doing.” But it has not, he stresses, been as easy as it sounds. “Everybody wants to save the planet, but no one wants to turn off a light switch. That’s the human condition, that’s the nature of things. But as well as that, it’s everyday pressure. You’re working in an intense environment, and when you’re really trying to handle day to day problems, you don’t always remember to turn off the light. We did get [people to] buy-in but it takes a while, it still takes effort, and it’s far from perfect. I wouldn’t give the impression that it’s anything other than constant effort.”
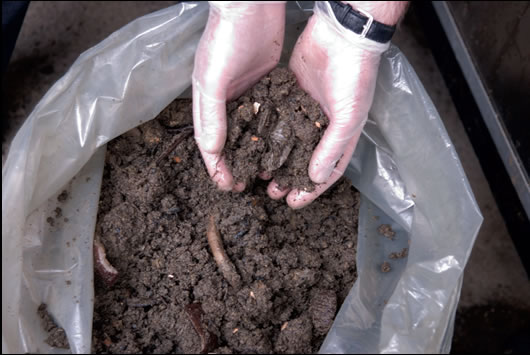
Food waste in the Big Hanna compostor; after 8 to 10 weeks this process creates a rich compost
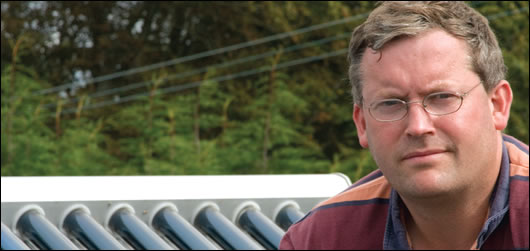
Michael Lennon, the owner of the Westport Woods Hotel has spearheaded the greening of the hotel
Walking through the hotel, it’s easy to see the impact of that constant effort. Anywhere that does not require illumination doesn’t get it. There are no standby lights glowing on the TVs in the bedrooms while green bins in place throughout the hotel facilitate waste segregation at source. “We changed all our bulbs to CFLs.” says Michael Lennon. “Instead of a 50 Watt halogen, you have an 8 Watt CFL. In some of the retrofitting in our corridors, I’m taking out two 28 Watts which’d be 56 and I’m putting in four by 1 Watt LEDs in their place, plus a fluorescent which is 13 Watt, so I’ve reduced the wattage from 56 to 17 and it’s giving the same light. The 13 Watt is compact fluorescence, and that’s on motion sensors.” When ordering new treadmills for the gym last year, Lennon found a unit which requires no external power. Instead, it’s user driven. An inbuilt dynamo illuminates the onboard display during the workout. “We have timers in all sorts of places.” says O h-Aghmail. “We have timers on office equipment, on fans, toilets and ice making machines. Our ice making machine comes on at night-time. When we come to a seriously heavy weekend then you have to leave it on all the time, but in the normal course of events, midnight to eight o’clock in the morning, it makes its ice.” Conversely, the removal of timers from some systems facilitated further savings. “Water in urinals.” says Michael Lennon. “I’ve one set of urinals with a sensor on it so that rather than a flusher flushing every half hour, it only flushes with load, so if it isn’t being used in the middle of the night, it won’t be flushing.” Hippo bags have been fitted in each of the hotel’s 150 toilets, bringing the flush down from 9L to 6L. “Water hasn’t been a big cost yet, but it is going to become a bigger cost and as we look at our cost centres we will do something on water. If we don’t have much activity in our pool, we won’t backwash religiously every week, we might do it every fortnight. In the summer when there is a heavy load we might backwash more. It’s done on the water quality – we take readings.”
Monitoring is of course a vital element of the equation. A CEMS (continuous emissions monitoring systems) records all energy use. “Each Monday,” says Gearóid O h-Aghmail, “I go round and I read all the gas metres and we have all our electricity meters on a computer system linked to a bureau in Kilkenny. Every day you can read what happened the previous day.” Information on gas, water and electricity use is collected and input into a spreadsheet which gives a range of comparative calculations, including energy and resource use per room and per sleeper. Thanks to the range of initiatives – but primarily staff behavioural change – electricity use is down 23,000kWh in the first seven months of the year. “From a financial point of view, if we continued to use the same amount of energy as we did in 2003, at today’s prices, we’d be paying a hell of a lot more, you’re talking twice the price, and it would be worse, because there would be no restriction on it.”
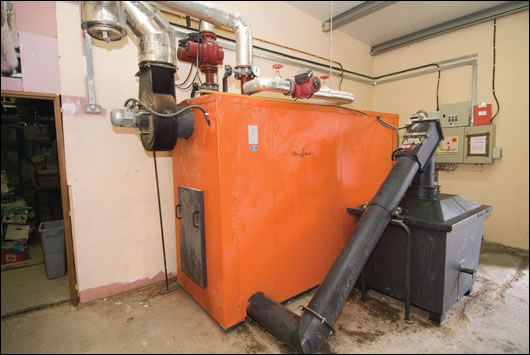
A 150kW Heizomat multi fuel biomass boiler has been in situ now for seven months
As with any hotel, heating remains one of the major overheads. Having reduced the heating load as much as possible, Lennon went on to replace existing fossil fuelled boilers with renewable energy technologies. In all, three separate biomass boilers, together with two sets of solar panels look after the heating loads of the hotel proper, the spa, leisure centre and adventure centre. The first boiler, a 150kW Heizomat, was provided by Clearpower and has been in situ now for seven months. “The advantage of the Hiezomat,” says Simon Dick of Clearpower “is that they’re a fairly rugged boiler. It can take a range of fuels and it’s very efficient technology…In the Westport Woods, it was the first boiler into an LPG mix… They wanted to operate wood as the lead, then bring in the other LPG boilers if the heat demand was getting ahead of what the wood boiler could provide.” The link-up is fully automated. “If the wood is coming in at 70 degrees, the gas can be set to come in if the water temperature drops to say 65 degrees.” Looking after about half of the entire heat load, the boiler is fed by augur from an adjacent dry-lined store which can take fully 40 tonnes of wood pellets at a time. The pellets are pumped in by the delivery lorry, while two large sweeper arms installed in the store ensure an even feed of fuel into the hopper. Because the burning process is highly efficient, there’s very little waste ash generated. Any that is produced is taken and fed into the food composter where it acts as a drying agent and speeds the production of the compost. So far, says Gearóid, so good. “January and February were very significant. It was the first time in forty years that the hotel didn’t use oil. It was one of those moments.”
An energy cabin, just arrived onsite, offers a self-contained combination of wood pellet boiler and solar panels which together will be used to provide space heating and hot water for the adjacent adventure centre. “It’s a 30kW wood pellet boiler.” Paul Kellet of Energy Cabin explains, “and it’s got 12M2 of solar panels, though it’s actually a single panel. It’s got 800L of hot water storage, it’s got the pumps and controls for all that, and, most importantly, it’s got a wood pellet store included. It’s factory fitted to Austrian standards and it takes about 5 tons of pellets.” The system defaults in the first instance to the solar panels, only calling for energy from the wood pellet boiler if the heat load cannot be met by the solar alone. “It’s designed to collect about 5000 kWh a year for free, that’s the direct contribution, and then the indirect contribution is the fact that the boiler doesn’t have to start up to heat a small amount of water. The 800L is always hot and available.” Embedded software monitors that 800L buffer store and if it cannot meet the heat requirement, the boiler switches on. The inbuilt modem facilitates remote monitoring and diagnostics, while the system can be sized either to take the entire heat load, or to integrate with existing high or low temperature systems. Using the Energy Cabin with an existing heat source, says Kellet, means you don’t run the risk of oversizing the system. “I think the nice thing for hotels is using it as the add on. We recommend to size the biomass system to heat 60% to 70 % of the heat demand of the building, a rough sizing guideline. Don’t size it to meet the coldest day of the year, because if it’s sized to meet 60% to 70% of peak demand, chances are it’s going to meet 90% of it. You’re making the most use of your investment…”
Igneus in Enniscorthy, Co. Wexford supplied the third biomass boiler onsite. Once commissioned, this 220kW DanTrim multi fuel boiler, supplemented by a suite of roof-mounted solar panels, will take on the heat load of the leisure centre. “The boiler has got two separate feeding systems.” Gerald O’Donoghue of Igneus explains. “I’ve designed it in that way; with the flick of a switch, they can go over from pellet to wood chip or vice versa. They’re giving themselves the best of both worlds.” This flexibility is no accident. Ongoing management of the trees around the hotel generates a lot of waste wood, much of which is now drying onsite. This, together with a test crop of willow recently planted will in the future be chipped and used in the boilers. Currently, a wood pellet silo from McAree Engineering, installed alongside the Dan Trim boiler stores and feeds the pellets on demand. “It’s a 3M galvanised bin.” Paul McGrath of the company explains. “It’s rolled out on a machine, there’s insulation an inch deep inside, there’s another single sheet inside that again and the bin holds something around 34 tonne.” The pellets are pumped in directly, are gravity fed to an augur box, and delivered from there to the pellet intake. “It has a galvanised lid, a galvanised cone, and there’s an access in the top of the bin to the lid so you can look down and see what’s going on.”
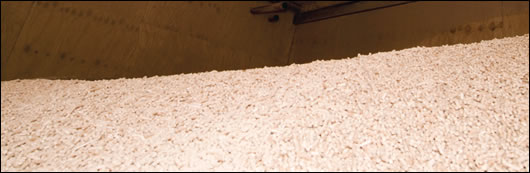
The boiler is fed by augur from an adjacent dry-lined store which can take fully 40 tonnes of wood pellets at a time
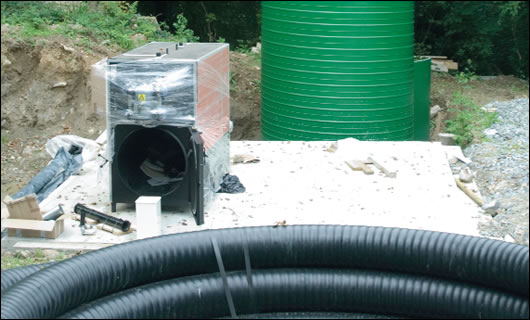
A 3M galvanized wood pellet silo before being installed alongside the Dan Trim boiler stores
26M2 of evacuated tube solar panels by Kloben in Italy, also supplied by Igneus, have been installed on the roof of the leisure centre. These will supplement the work of the biomass boiler, O’Donoghue explains. “Basically, there’s a dual coil tank being installed there that will look after the hot water needs in the leisure centre, and there’s also a heat exchanger installed at the swimming pool. This will attempt to keep the pool up to temperature, and if it can’t do that, then the wood pellet boiler kicks in.”
This winter will see further building work at the hotel. An existing bedroom wing will be extended upwards and outwards to create larger bedrooms and more of them. Maintaining the sustainable ethos that has characterised all of the hotel’s developments, insulation levels and energy reduction methods will exceed existing building regulations by some 40%. “It’s an existing building and that presents its own difficulties.” says energy consultant on the project, Michael Doyle. “The approach is what can you do with such a project to maximise the potential with insulation, air tightness, low energy lighting, the whole gamut.” The new development will incorporate high grade insulation, glazing and a range of sustainable technologies, while the existing metering system will be upgraded to provide management with the necessary data to successfully manage the new building.
Though much of the detail is yet to be nailed down, a range of other sustainable innovations are being investigated, including a combined heat and power plant (CHP), a rainwater harvesting system and a district heating system to manage the disparate elements of the heating set up. And of course, the constant struggle to keep everyone in an energy conservation frame of mind will continue, no matter how the capital is spent. It’s also worth noting that in addition to the environmental and financial benefits arising from the Westport Woods approach, the hotel has also managed to reap a very substantial PR dividend. It’s been heavily featured in more than one TV programme and has won several awards for its innovative and holistic approach to energy management. “From an environmental point of view, from a practical point of view and from a management point of view, the whole thing is pretty comprehensive.” Gearóid O h-Aghmail concludes.
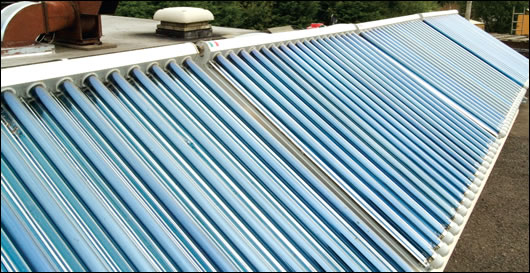
26M2 of evacuated tube solar panels by Kloben in Italy have been installed on the roof of the leisure centre
SELECTED project team members:
Client: Westport Woods Hotel
Heating contractor: Igneus
Heating contractor: Clearpower
Heating contractor: Energy Cabin
Building energy consultant: Michael Doyle
Wood pellet silo: McAree Engineering
- Articles
- Design Approaches
- Green Rooms
- energy cabin
- ISO 14001
- biomass
- boilers
- rainwater harvesting
- district heating
- wood chip
- pellet
Related items
-
Firebird rebrand emphasises sustainability & innovation
-
Grant invests in biofuel tech for oil boilers
-
Steeply sustainable - Low carbon passive design wonder on impossible Cork site
-
Focus on whole build systems, not products - NBT
-
International - Issue 29
-
Passive Wexford bungalow with a hint of the exotic
-
The House of Tomorrow, 1933
-
1948: The Dover Sun House
-
The dazzling Dalkey home with a hidden agenda
-
Mayo passive house makes you forget the weather
-
Green Room 2018 to focus on nZEB and corporate sustainability on 2 May
-
A1 passive house overcomes tight Cork City site