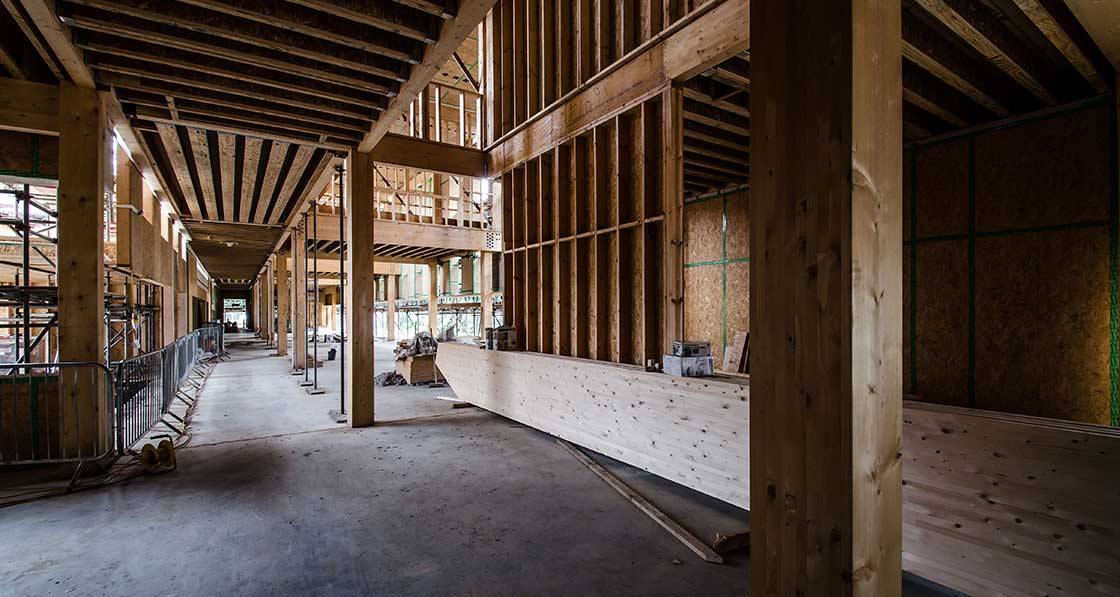
- Guides
- Posted
Timber frame & mass timber: the Passive House Plus guide to structural timber construction
Fuelled by the need to build quickly and to increasingly tight sustainability standards, the market for timber frame and mass timber construction is growing rapidly. This detailed guide covers many of the main established and emerging techniques, and looks at key issues to address if you’re considering a timber-based build.
Additional words by Jeff Colley
Timber frame construction has traditionally proven a popular choice for people interested in sustainable building for a variety of reasons, not least because of its ability to reduce environmental impacts compared with traditional concrete-based construction: less embodied energy, a lighter carbon footprint and, in its prefabricated forms, arguably less waste on site.
Timber frame has long been the dominant build method in Scotland and has risen rapidly in the UK and Ireland due to the need to build rapidly while meeting tightening building standards. The market share of timber frame in Ireland grew from very little to in the region of 30% of new home builds during the Celtic Tiger years, and although it was marketed as boasting superior energy efficiency compared to masonry, in truth its rise – at a time when the construction industry was paying little more than a cursory regard to energy – owed more to the ability to build quickly and overcome onsite labour shortages.
While arguments abound about whether timber frame is superior or inferior to other build methods in terms of energy efficiency, the reality is that it’s possible to build well or badly using any build method. Whatever the approach, the key is quality control and attention to detail. It’s true that many of the exemplary low energy buildings published in this magazine and its predecessor Construct Ireland over the last sixteen years are timber framed, and that, especially in the infancy of low energy building, concrete-based approaches – with a heavy reliance on onsite skills to deliver airtightness and correct installation of insulation – often weren’t at the races.
But these days the playing field has levelled out as the industry has learned how to adapt cavity wall construction towards low energy requirements or switch to alternative concrete-based approaches – ranging from insulating concrete formwork, with its inherent airtightness and continuity of insulation, to externally insulated single leaf construction – with the ultimate choice between systems depending more on clients’ individual preferences and circumstances, including budgets.
But timber frame is arguably the most ‘tried and tested’ method of construction in the world, with over 70% of the population in the developed world living in timber frame housing, albeit of wildly divergent quality.
In Ireland and most of the UK, masonry remains the predominant choice, but the superior speed of off-site, prefabricated timber frame construction allowed it to grow market share here to up to 35% during the boom years.
In Britain, timber frame manufacturing has doubled since the turn of the century, with industry turnover up 10% from 2007. Experts predict that the method will continue to grow in popularity in England and Wales, catching up on the 75% market share it currently enjoys in Scotland.
1 The Horyuji Temple in Japan, the world’s oldest timber building, is 1,300 years old; 2 the 18 storey Mjøsa Tower, currently under construction, is on course to be the world’s tallest timber building.
This article was originally published in issue 28 of Passive House Plus magazine. Want immediate access to all back issues and exclusive extra content? Click here to subscribe for as little as €10, or click here to receive the next issue free of charge
What is timber frame?
A timber-framed house is a house where the primary load-bearing structure is made of timber. A typical design features a frame of beams and posts that make up the internal and external structure of the building and supports the entire home without the need for interior load-bearing walls.
But there are lots of variations in timber frame construction design thanks to the essential versatility of the basic material, which in turn enables enormous flexibility of design. Indeed, as there are usually no interior load-bearing walls, your floor plan can be as open as you like and can be adapted to suit your changing needs.
In the past there was a common misconception that a timber-framed house was essentially the same thing as a log house/ cabin or a timber-clad house. You can of course clad a timber-framed house with anything you want: wood, fibre-cement or other building boards, brick, render, or stone. In Ireland it is popular to build the external leaf with rendered blockwork, though alternative options such as rendered cement fibreboard can provide the same aesthetic and performance. Moisture barriers are incorporated within the wall structure itself.
System types
At the most basic level, there are essentially two types of timber frame construction: stick-built (built on site) or prefabricated (built in a factory and erected on site).
Prefabricated timber frame can be further divided into two types: open panel and closed panel.
Open panel systems are structurally engineered panels that form the inside load-bearing leaf of the external wall, typically comprising studs, rails, plywood or OSB sheathing on one side and a breather membrane on the other. They are manufactured in the factory ready for fitting to the frame on site, after which the external joinery (doors and windows) wiring, plumbing and insulation is then installed.
Closed panel systems are where the wall panels are made in their entirety in a factory, including the insulation – and in some cases even the wiring, plumbing, window and door linings and possibly even the external cladding, leaving very little on-site work.
The two big advantages of prefabricated systems in general, of course, are speed and quality. With most of the work done in a factory, it reduces the amount of time needed on site compared to stick-built or masonry homes. The factory environment that makes greater economies of scale possible also enables greater quality control, particularly in relation to insulation and fittings.
Cork-based Cygnum Timber Frame has developed a strong operation in producing closed panel systems for clients all over Ireland and the UK. Technical sales director Heber McMahon says: “We have a lot of automation in our factory, more so than most other companies to eradicate human errors.” This is particularly the case when it comes to important details like designing in the appropriate fire protection to partition walls, cavity barriers and plasterboarding.
McMahon says that new building regulations have created a massive amount of paper work for builders, “whereas we take over a lot of that for them because we’re manufacturing it [offsite]”.
Perhaps the one big disadvantage of prefabricated frames is that it can be difficult to modify the structure once the frame is finished. Because of this, the design should be exactly right for the plot, and the work should only be done by a competent frame erection team to ensure it lines up perfectly with whatever foundations are in place A relatively recent innovation in timber construction is SIPs (structural insulated panels), which are essentially insulated timber panels assembled together, often without the need for a timber frame. SIPS are usually made up of two sheets of OSB sandwiching a rigid core of polyurethane foam – though other insulants can be used – giving strong structural strength with high levels of insulation for use in walls, roofs and floors.
Ensuring breathability is crucial.
According to the Structural Timber Association in the UK, there are two fundamental applications for SIPs – a full load-bearing structural wrap or infill walling, where the panels are specified as infill to the timber frame. A similar system is Glavloc from Cork, which makes a high-performance timber and EPS-based build system designed to enable simple, rapid build to passive house or NZEB levels.
Single or double stud
Timber frames can be designed with double stud or single stud structures. Double stud is typically used when the wall thickness needs to be more than the 200mm possible with single stud – a good example being the 300-400mm twin stud wall that MBC Timber Frame Ltd have used on many passive house projects published in back issues of this magazine. But arguably a more important advantage of double stud is that it cuts out cold bridging, particularly given that the ratio of timber to insulation in a single stud building can up to 25pc compared with 15pc in a double stud set-up.
“The twin wall, double stud system is designed to cut out that cold bridging, so you increase the thickness of the insulation around the studs. But you end up with spaced studs, so you get much better cold bridge-free structure,” says Meade.
Breathability and thermal mass
Ensuring breathability is crucial in a timber frame construction. Most build-ups become more breathable, ie more vapour open, towards the outside of the construction.
So, an airtightness and vapour control layer toward the inside and a more open breather membrane towards the outside of the build up, allows vapour and any moisture absorbed during the building phase to diffuse out of the construction.
According to Niall Crossan of Ecological Building Systems, the thermal insulation in between these two layers should also be breathable – otherwise the timbers will take longer to dry out if wet and the natural path of vapour diffusion will be significantly reduced. He recommends natural insulation like hemp, woodfibre or cellulose – all of which the company provide. “Aside from their lower environmental impact, they also present the technical advantage of hygroscopicity, which helps offset interstitial condensation risk within the structure.”
When compared with bricks and mortar, there is a common perception that timber frame is a relatively ‘lightweight’ building method, but it can be made ‘heavier’ to offer greater thermal mass, such as by using a heavier density insulation material. “It can all add up and you’re still not looking at anywhere near the density levels of concrete,” says Jasper Meade. Adding density can help significantly to reduce the fluctuation of temperatures over the winter but also decrement delay in summer – where the building is capable of absorbing and delaying the release of daytime heat until the night, when temperatures may be significantly lower. Other solutions can involve laying concrete screeds on first floors or building a structure with exposed heavy beams.
Cladding
Timber frame houses need a layer of external cladding to protect them from moisture, ideally with a ventilated cavity. As mentioned above, timber-framed houses can be clad with a wide range of external leaves including brick or block, but also cement fibreboard, stone, metal and timber.
Indeed, there is a bit of a current fashion for timber cladding. Jasper Meade of Welsh closed panel timber frame manufacturer PYC is a fan, arguing that it can be incredibly practical in the long-term. “It’s all about the detailing, if the rest of the detailing is correct then it has very good longevity,” he says.
Carbon footprint
One of the biggest selling points of timber frame construction amid growing environmental awareness and the demand for sustainable methods of building is that it is low-carbon – as long as the forests from which the timber comes are well-managed and replanted.
Timber frame can help to reduce the embodied energy of construction, for a couple of reasons: timber products tend to be less energy intensive to manufacture than steel or concrete, and the material itself acts as a carbon sink.
Growing trees soak up CO2, meaning that timber products can lock in place emissions for the lifetime of the building. It is estimated that during photosynthesis, 0.9 tonnes of CO2 is stored in every cubic metre of wood. When the building is demolished, the timbers can often be very easily recycled when they go out of use – though this will depend on the specifics of the build spec.
An average timber frame house uses approximately 5-6 cubic metres more wood than a traditional masonry house (which also has roof and floors in wood), thereby saving up to 12 tonnes of CO2. And according to Wood Knowledge Wales, if all houses in the UK built since 1945 had been timber frame, over 300 million tonnes of CO2 would have been saved.
According to David Murray of MEDITE SMARTPLY, while tightening energy performance requirements under building regulations are ensuring that new builds are moving in the right direction in terms of energy used to operate buildings, there’s been insufficient focus on embodied energy – and such is the urgency of the climate crisis, it may no longer be acceptable to justify considerable CO2 emissions to construct new buildings even if those buildings are designed to emit little over their lifetime.
“Carbon reduction is only measured or incentivised in terms of energy efficiency, such as space and water heating through Part L,” he says. “Today though, materials account for a higher percentage of carbon emissions, so this should be incentivised.”
Durability
Though in markets like Ireland the concrete lobby has in the past sought to capitalize on people’s lack of familiarity with timber frame by raising doubts about its durability, in fact the evidence paints a different picture: the oldest example in the UK is a stave church built in the 11th century, while even older examples include the age-defying Horyuji Temple in Japan, which is still pristine some 1,300 years after it was built.
A study carried out by the BRE on more than 100 timber frame houses that had been built up to the end of 1975, found their performance to be “similar to traditionally built dwellings of the same age and, given proper maintenance, they were found likely to remain in that way for the foreseeable future”.
Acoustics
The science of sound transmittance is about much more than just the structure of a building, taking in anything from building form, to finishes and material densities. But with good design and quality construction, timber frame buildings can achieve superlative acoustic performance, as developer Michael Bennett’s low-cost passive house scheme in Enniscorthy demonstrates.
As reported previously in Passive House Plus, acoustic tester Ted Dalton of Dalton Acoustics recorded levels of 63 and 69dB at the party walls he tested in the homes – a marked improvement on the regulatory target of 53dB or higher. “The higher result [of 69dB] is akin to the kind of sound insulation we attempt to design into walls between commercial cinemas,” says Dalton. “I’ve never seen a result like this on a party wall.”
Quality is critical to results like these: Bennett built the homes with one of Ireland’s leading timber framers, Shoalwater Timber Frame, and the impressive result owed to a combination of factors including high levels of airtightness, and a carefully conceived build-up including high density cellulose, ProPassiv OSB, and two layers of Gyproc wall boards, one of which has strong acoustic properties – with joints staggered to reduce noise levels.
Metal web joists
One innovation that has proven popular in recent years is metal web floor joists, which offer advantages including the ability to run building services seamlessly through the joists. Care may be required on the overall floor/ceiling build-up to ensure that penetrations don’t compromise fire safety.
Fire prevention
There’s a common conception that timberframed homes are inherently at greater risk of fire because of wood’s combustibility. However, timber frame construction and its components are highly regarded by many in the matter of fire safety and can meet all fire standards under current building regulations.
All buildings, irrespective of construction type, must meet very stringent regulations with respect to fire safety. The plasterboard in timber frame buildings will help to protect the underlying structure from high temperatures.
“The real danger of fire in any building is time, and so making sure that there is time to escape and for time to extinguish the fire, so compartmentalizing and fire stopping between sections of buildings is crucial to get that right,” says Meade. “But also ensuring that if you’re using timber, you’ve got material which chars and smokes.” Wood chars at a known rate. The argument goes that at high temperatures, the outer char layer protects the wood underneath and prevents structural collapse.
Height
Although timber frame tends to be restricted to in the order of three to four storeys in the UK and Ireland, recent innovations in timber engineering mean that mass timber methods are starting to be used to build to remarkable heights. In the last few years, timber structure buildings of up to 18 storeys have been completed while two timber buildings clocking in at over 80 metres tall are currently under construction – the 24-storey HoHo Wien in Vienna, and Mjøsa Tower – an 18-storey Norwegian Tower nearing completion that’s on course to be the tallest timber building ever built.
Housing crisis
In Ireland, where there is a serious crisis in the supply of new homes, there is strong feeling among some in the industry that the benefits of timber frame are not well understood by policy makers, and therefore not incentivised.
Pre-fabrication can enable rapid-build without compromising build quality, but the very term prefabricated is a problem, because of its association with cold and cheap-feeling prefab units.
Where advocates may want timber frame to be recognised for the high-quality builds being produced and its sustainability, speed is still the biggest draw of timber frame, as it was during the last Irish property boom when over 30% of the homes built in Ireland each year were made of timber.
Timber structural elements
When it comes to the methods of constructing the main structural elements of a building, there are lots of timber-based options, each with their own advantages.
BRETTSTAPEL
This rarely seen method which literally means “stacked planks” is a form of solid timber construction that does not use glues or nails. It’s made by connecting softwood timber posts together with hardwood timber dowels.
The advantage of this relatively simple method of construction is the capacity to use low-grade timber to form load-bearing solid timber wall, floor and roof panels. The dowels have a lower moisture content than the posts, so over time the dowels expand to achieve moisture equilibrium, thus ‘locking’ the posts together and creating a structural load-bearing system.
Methods like CLT and Brettstapel can enable use of lower quality wood being adhered together to form strong structural elements. As an example, Brettstapel was used to form the curved walls of the Pod building at the Burry Port school in Wales, which houses the school’s performance and recreational spaces. The Brettstapel system was manufactured in Ireland by Cygnum, using Welsh softwood — low grade timber that would otherwise end up in pallets, woodchip or fence posts, thereby boosting its sustainability credentials.
Low-grade timber often includes a lot of Irish/British produce of fairly poor quality because it’s grown on poor quality soils. However, Jasper Meade of PYC insists that certainly in the case of brettstapel, there is a “phenomenal” amount of timber in the wall structure, so it needs to be of decent quality, while CLT is typically made out of a high-quality European timber and there’s a high-quality process involved in manufacturing it.
CLT
Cross laminated timber (CLT) is a structural two-way spanning solid wood panel product that can be used to form walls, roof and floor panels as well as shear walls. It is produced by stacking a number of layers of timber, known as lamellas, at 90º to the layer below, and subsequently glued to create panels of up to 24m in length and 3m in width, which can encompass between three and seven layers.
CLT may prove particularly advantageous in high-rise or commercial buildings, where the cost reductions from using lorries and cranes come into their own, though the material is becoming popular for smaller-scale buildings too. Firms like PYC have also used it on projects where the internal finishes need to be exposed and not plasterboarded. “With CLT you’ve always got to put thickness of insulation on the outside of it, so that might be done with wood fibre or studs with cellulose inside it,” says Jasper Meade of PYC.
David Murray, head of innovation at MEDITE SMARTPLY, says panelised timber frame is cost-effective and proven technically for medium rises of up to six storeys, meaning CLT tends to be used less in small projects. That said, as past issues of Passive House Plus have attested, CLT has been used on small scale passive house projects too – notable examples including buildings built using CLT from British manufacturer Eurban, Spanish manufacturer Egoin and innovative modular passive house builder, Kiss House.
I-JOISTS
These strong, lightweight ‘I’ shaped engineered wood structural members are an increasingly popular choice. An I-joist comprises two main parts, the web and flange. The web is sandwiched between a top and bottom flange, creating the “I” shape. The flange can be made from laminated veneer lumber or solid wood finger-jointed together for ultimate strength. Besides offering a higher strength-to-weight ratio than conventional wood joists and thereby outstanding resistance to shearing, twisting or splitting, I-joists are ideal for projects that seek to use minimal timber and lots of insulation.
GLULAM
The popular name for glued laminated timber, glulam is a manufactured timber product made by bonding together individual laminates (layers) of solid timber boards with durable, moistureresistant structural glues. The laminations are usually made of spruce or pine but also larch, douglas fir, or even hardwoods like oak. One of the greatest advantages of glulam is that it can be manufactured in a wide variety of shapes, sizes and configurations, and is commonly used for points in a timber frame that requires a stronger structural support.
GREEN OAK FRAME
Often referred to as exposed timber frame, this is the most traditional timber frame building method. The oak is often jointed using mortise and tenon joints, which are draw-pegged with tapered oak pegs. The structure is integrally braced with curved oak bends jointed into the frame. The massive oak skeleton is then infilled with insulating panels and made waterproof by a system of perimeter trims and water bars before being rendered on the outside, leaving the timbers exposed.
-
BRETTSTAPEL BRETTSTAPEL
-
CLT CLT
-
GLULAM GLULAM
-
Green Oak Frame Green Oak Frame
-
LARSEN TRUSS LARSEN TRUSS
https://passivehouseplus.ie/magazine/guides/the-ph-guide-to-structural-timber#sigProIdbd1b9807e9