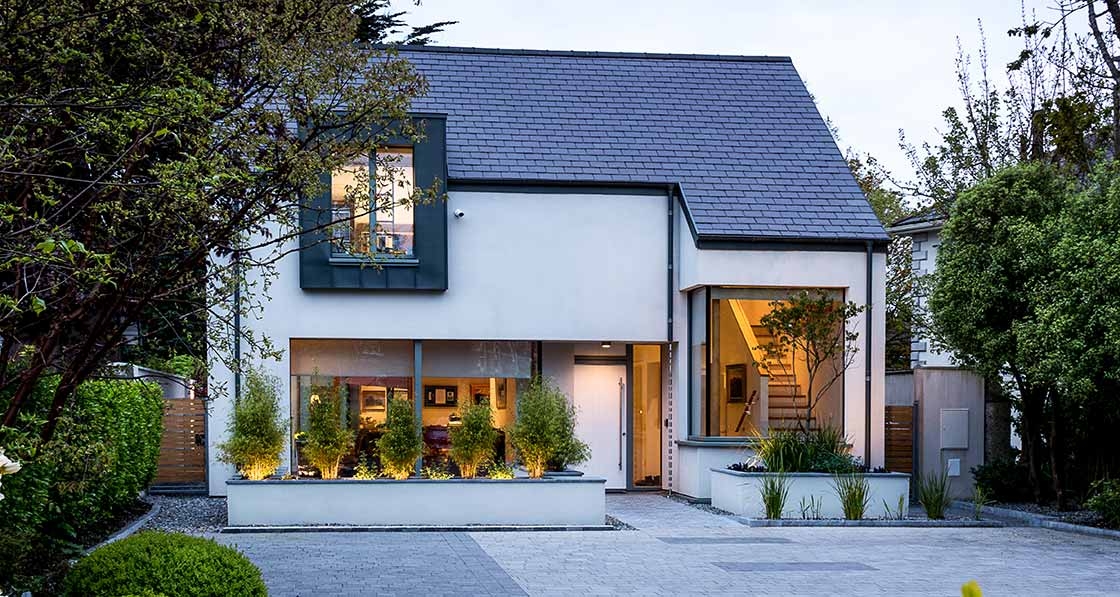
- New build
- Posted
A1 passive house overcomes tight Cork City site
Designing a dwelling to take advantage of the sun’s free heat is a big part of what makes a passive house passive. So how do you meet the low energy standard when your narrow site faces away from the sun and is overshadowed by neighbouring houses and trees, while simultaneously hitting an A1 building energy rating – and with a stunning, architecturally expressive design?
Click here for project specs and suppliers
€224 annual estimated heating costs
Building type: 323 sqm detached blockwork house
Completed: September 2016
Location: Cork City
Build method: Concrete block with external insulation
BER: A1
Standard: Certified passive house
This new home in Cork City shows how to meet the passive house standard on a narrow and tight site with unusually poor solar gain. The property was previously home to a two-storey dwelling with several extensions, and the client, who wishes to remain private, initially hired Wain Morehead Architects to renovate it.
But the internal spaces of the old house were poorly organised, and the client ultimately decided to knock it in favour of a new, energy-efficient, bright and modern house. Wain Morehead is one of Ireland’s leading passive house design practices, so it’s no surprise they ultimately decided to aim for that standard here.
“We wanted to be confident that whatever design standard we chose had a track record and would deliver not just in terms of design, construction and performance, but also in terms of the quality of all the elements of our home,” says the client.
However, good solar gain is a key part of reaching the passive house standard — and there were big problems getting enough here. The long and narrow site is overshadowed to differing degrees by dwellings on three sides, as well as by mature trees. The site also faces north-east, and is bounded with 2.4m-high walls that obscure any low-lying sun.
This article was originally published in issue 22 of Passive House Plus magazine. Want immediate access to all back issues and exclusive extra content? Click here to subscribe for as little as €10, or click here to receive the next issue free of charge
What architects John Morehead and Jennifer Kenefick came up with was a design comprising two double-storey sections connected by a single-storey link. The building wraps around an internal courtyard that takes advantage of the sun at all times of the day, making use of the site depth while acknowledging existing building lines. The path of the winter sun through the sky was used to guide the trimming of trees along the southeast boundary, helping to optimise solar gain.
The finished design aims to balance light, connectivity of the internal spaces and integration with the surrounding landscape, while maintaining privacy. However, the project was held up during the planning process, and planning permission had to be appealed. This delayed construction and required the architects to re-design the rear of the house, reducing its width and changing the internal layout, but also compromising solar gain to this part of the dwelling.
The overall lack of solar gain meant the building fabric needed even more insulation to meet passive house targets for space heating demand. This was provided by walls of Quinn Lite blockwork externally insulated with 250mm of Kingspan Aerowall graphite-enhanced EPS, a Kore insulated foundation system, and a warm roof system – filled with cellulose insulation from local manufacturer Ecocel – with wood-fibre sarking insulation.
Explained
The Energy Performance Coefficient (EPC) and Carbon Performance Coefficient (CPC) measure the energy and carbon efficiency of buildings under the Irish building regulations. Here we compare the EPC and CPC for this dwelling to Ireland’s proposed nZEB standard and to the current (2011) and past versions of Part L of the Irish building regulations. The lower the fraction, the better the score - so for instance a house with an EPC of 0.4 is 60% better than the 2005 regs.
The environmental impact of the concrete in the foundations was reduced in two ways. Firstly, as insulated foundation supplier Kore explain, the use of an insulated raft foundation can reduce the quantity of concrete used by up to 50% compared to a strip foundation.
Secondly, the concrete included ground granulated blast furnace slag (GGBS) – a by-product of the steel industry that can replace portland cement use up to high percentages – 66% in this case – leading to substantial carbon dioxide emissions reductions in the manufacturing process.
Roadstone - who supplied the GGBS in this case - don’t publish embodied CO2 figures on their GGBS. Had the GGBS come from Ecocem, who do, the net effect would have been a reduction of some 4.5 tonnes of CO2, equivalent to preventing a typical passenger car driving for almost 37,000 KM. The concrete construction also extended to the first floor, with precast concrete slabs and stairs. This made it somewhat challenging for the architects to maintain airtightness around the slabs, and to integrate the precast concrete staircases.
However, contractor Brian Twomey of Michael Twomey & Son is a certified passive house consultant and was ultimately able to get the finished house just inside the target of 0.6 air changes per hour.
The other big challenges, according to John Morehead, included access to and around the narrow site, the difficulty of fixing into the lightweight blocks, and the amount of time needed to allow the wet trades to dry out.
The finished house is primarily heated via supply air by a Nilan Compact P unit, which includes an exhaust air heat pump combined with passive heat recovery ventilation, with back-up coming from a Nilan Air 9 air-towater heat pump, which distributes heat via underfloor heating only during the coldest winter periods.
The client says: “The biggest change for us is that there has been very little forced heat or cooling input. It wasn’t unexpected, but the uniformity of temperature throughout the house is a pleasant surprise, and the fact that we don’t constantly have to turn boilers on or off or adjust thermostats is great.”
The architects are now monitoring the house for its energy consumption, indoor humidity, carbon dioxide, temperature, and for the energy production of the solar PV array. The house was also recently commended at the 2017 RIAI Architecture Awards in the sustainability category.
Explained
Passive solar gain is the term used to describe ‘free’ heat energy from the sun. In the northern hemisphere, architects can design buildings to take advantage of solar gain by orienting the main glazed surfaces to the south.
Maximising solar gain is a key element of passive house design. However, designing for solar gain must be balanced with the risk that lots of southfacing glazing can lead to overheating and uncomfortable glare in summer.
So how is the house performing?
Since the clients moved in, Wain Morehead Architects have been monitoring indoor temperature, humidity and CO2 at two locations in the house, as well as the dwelling’s overall energy demand, and the generation of the solar PV array.
While technical difficulties have interrupted monitoring, there is a complete set of data available for February 2017. One of the monitoring modules, located in the highly-insulated but little-glazed northern part of the house, shows indoor temperatures remaining remarkably even at around 22C, with little difference between maximum and minimum daily temperatures, bar a couple of spikes — the largest of which came on Feb 22, though the clients cannot recall exactly what might have caused this.
Monitoring graphs
https://passivehouseplus.ie/magazine/new-build/a1-passive-house-overcomes-tight-cork-city-site#sigProId6b314aaa93
Relative humidity generally remained between 45% and 55% (40% to 60% being the recommended indoor range), with CO2 ranging between 500 and 900 parts per million, suggesting good indoor air quality. CO2 only peaked over 1,000ppm on February 22.
The overall energy demand was 5.6 kWh/m2/yr for the month of February, equating to 67.45 kWh/ m2/yr for a full year if February is an average month — close to the primary energy demand of 65 kWh/ m2/yr as calculated in PHPP. While the solar PV array only produced 89.63kWh for all of February, this increased to 176.47 kWh in April. Overall energy demand declined to 4.22 kWh/m2 in April (or 50.61 kWh/m2/yr, if April is used as an average month).
“We are extremely pleased with the CO2 levels and temperature stability within the dwelling during both of these periods,” says architect Jennifer Kenefick. “The lack of solar gain and robust envelope performance is very apparent in the ‘indoor remote module’ temperature results, located in the northern section of the house.” She added that in May, it was found a circulation pump in the underfloor heating circuit was operating permanently, even though there was no heating demand. A software upgrade is expected to address this issue and further reduce energy demand.
“Our early monitoring in the autumn of last year, identified a shut down in the ventilation system that had taken place after a power failure when the building was not occupied. Monitoring is extremely useful during the drying out, handover and commissioning periods.”
But how has the house been performing in the warm weather in June and July? In June the exterior temperature in the courtyard peaked at 27.2C at 3pm on 19 June. The highly glazed kitchen area peaked at 26.3C that evening, and average temperatures in the kitchen remained above 25C for just over a week. Meanwhile the remote monitor in the northern block – which is highly insulated but with very little glazing – peaked at 23C on 19 June. “The remote station in the northern block is extremely stable,” says John Morehead. “The kitchen is more volatile but dumps heat as the high level windows open and as the client wishes.”
Selected project details
Architect: Wain Morehead Architects
M&E engineer, heat pump and ventilation: Nilan Ireland
Civil & structural engineer: Allen Barber Consulting Engineers
Passive house certifier: Mosart
Main contractor: Michael Twomey & Son
Quantity surveyor: Richard Leonard & Associates
Landscape design: John Butler Landscaping
Mechanical contractor & airtightness tester: Energywise Ireland
Electrical contractor: Owers Electrical
Audiovisual controls: Future Homes
Airtightness testing: Clean Energy Ireland
Cellulose insulation: Ecocel
Wood fibre insulation & breather membrane: Ecological Building Systems
Floor insulation: Kore
Wall insulation & additional floor insulation: Kingspan
External insulation system: Baumit
Airtightness system: Siga
Windows & doors: Smartwin
Roof windows: Velux
Curtain walling: AMS
Curtain walling installation: 20/20 Glazing
Zinc cladding: Weatherseam
Dry lining: Fermacell
Lightweight concrete blocks: Quinn Lite
Radiators: ATC
Solar PV: Sharp
Monitoring station: Netatmo
Floor screed: SMET
Timber flooring: Junckers
Kitchen and fitted furniture: Classic Kitchens Carrigaline
Sanitaryware: Irish International Traders Cork / Eden Tiles & Bathrooms
Lighting: Erco Lighting Ltd / Cork Lighting
Lighting controls: Legrand / Future Homes
Heating controls: Nilan / Heatmiser
Low energy appliances: Neff, Bosch, Samsung
Roof slates: Burlington Stone
Slate internal thresholds, window boards & countertops: Ceco Products, using slate via Burlington Stone
Rainwater harvesting: Ireland Waste Water
Paints: Dulux
Slate: Lagan Building Solutions
GGBS: Roadstone
1 The ground floor features a raft foundation consisting of 300mm Kore EPS300 insulation and radon barrier; 2 Primary space heating and ventilation is provided via the Nilair ventilation ducting system; 3 The floor build-up also features a layer of 80mm Kingspan TF70 insulation boards that also contains ventilation ductwork channels; 4 Secondary space heating is provided by a Nilan Air 9 air-to-water heat pump via zoned underfloor heating; 5 The walls of the house are insulated externally with 250mm of Kingspan Aerowall platinum EPS; 6 Frame for the Gyproc suspended ceiling system, for housing of services within the airtight layer, at the kitchen light-well.
In detail
Building type: 323 sqm (287 sqm TFA) detached two-storey externally insulated blockwork house.
Space heating demand (PHPP): 14 kWh/m2/yr
Heat load (PHPP): 8 W/m2
Primary energy demand (PHPP): 66 kWh/m2/yr
Heat loss form factor (PHPP): 3.88
Overheating (PHPP): 3% (of time indoor temp greater than 25C)
Energy performance coefficient (EPC): 0.143
Carbon performance coefficient (CPC): 0.145
BER: A1 (22.23 kWh/m2/yr)
Heating costs: €224 per year estimate, based on PHPP calculated figure of 1602 kWh/yr at an electricity price of 0.014c per kWh.
Thermal bridging: Externally insulated Quinn Lite blockwork walls, all junctions thermally modelled, all external structural elements thermally isolated from thermal envelope, insulated raft foundation, thermally broken window frames & all window reveals insulated, first two courses of Quinn Lite blocks to all internal blockwork walls. Y-value (based on ACDs and NSAI certified details): 0.0342 W/m2K
Ground floor: Raft foundation consisting of 300mm Kore EPS300 insulation, followed above by 200mm concrete containing 66% Roadstone GGBS, 80mm Kingspan TF70 (containing ventilation ductwork), 50mm Smet Fast Floor hemihydrate screed with solid oak floor finish. 50mm Kingspan TF70 perimeter insulation. U-value: 0.08 W/m2K
Primary walls: Baumit NanoporTop external insulation composite system including 18mm weathertight render on 250mm Kingspan Aerowall insulation on 215mm Quinn Lite B7 block on the flat, on 15mm internal plaster (airtight layer). U-value: 0.11 Wm2K
Dormer cheek: Standing seam zinc cladding followed inside by Tyvek Metal Underlay, 18mm SmartPly ToughPly, 50x38mm battens, pro clima Solitex Plus membrane, 60mm Gutex Ultratherm, 18mm OSB 3, 225mm timber with full fill Ecocel insulation, 18mm OSB 3, Siga Majpel vapour control layer, 20mm service cavity, Fermacell board. U-value: 0.14 W/m2K
Pitched roof: 500x300mm Blue Bangor roof slates externally, followed inside by 50x35mm slating battens @205mm c/c, 50mm counter battens, Solitex Plus roofing membrane, 60mm Gutex Ultratherm, 225mm rafters with full fill Ecocel insulation, 18mm OSB 3, Siga Majpel vapour control layer, 50mm service cavity with Rockwool Flexi, Fermacell board. U-value: 0.13 W/m2K
Zinc roof: Standing seam zinc roof cladding externally, followed inside by Tyvek metal underlay, 18mm SmartPly ToughPly, 50x25mm battens @260mm c/c, 50mm counter battens, pro clima Solitex Plus roofing membrane, 60mm Gutex Ultratherm, 225mm rafters with full fill Ecocel insulation, 18mm OSB 3, Siga Majpel vapour control layer, 50mm service cavity with Rockwool Flexi, Fermacell board. U-value: 0.13 W/m2K
Windows: Pro Passivhausfenster GmbH SmartWin passive house certified triple glazed aluminium-clad timber windows, with argon filling and an overall U-value of 0.7 W/m2K
Roof windows: Velux GGU-K-0082230 triple glazed, krypton-filled roof window, PHI certified, overall U-value: 0.7 W/m2K. Carey Glass patent glazing system over pantry, krypton filled, glazing U-value: 0.4 W/m2K
Heating system: Primary space heating is provided by the Nilan Compact P air-to-air heat pump & passive ventilation system via NilAIR ventilation ducting system. Secondary space heating is provided by a Nilan Air 9 air-to-water heat pump (external) unit via zoned underfloor heating during coldest weather. There is a 180L domestic hot water storage tank heated by the Compact P by utilizing exhaust air, while a 250L pre-heating hot water storage tank is heated by the Air 9 only when hot water demand is high. The Compact P can also provide additional cooling, with hot water generated as a by-product.
Ventilation: Nilan Compact P with Nilan Air 9 air-to-water heat pump. Compact P providing mechanical ventilation with heat recovery. Passive House Institute certified. Electricity: 8 x 250Wp solar photovoltaic panel array with average annual output of 2kW.
Lighting: Low energy LED lighting throughout. Generally, Erco LED wallwashers, Starpoint downlighters / spotlights. Exterior lighting integrated with overall lighting design. Green materials: Fermacell dry lining board, Ecocel insulation, Gutex Insulation, all timber from PEFC / FSC certified sources, 66% GGBS cement, Rockwool insulation, low VOC paints. Water conservation: Euro Rainwater Harvesting System with 1250L concrete tank to supply non potable water uses.
Image gallery
-
First floor presentation layout First floor presentation layout
-
Ground floor presentation layout Ground floor presentation layout
-
Site plan Site plan
-
Temperature 01 Temperature 01
-
Temperature 02 Temperature 02
-
Dormer cill to wall detail Dormer cill to wall detail
-
Monopitch roof ridge detail Monopitch roof ridge detail
-
Dormer jamb to wall detail Dormer jamb to wall detail
https://passivehouseplus.ie/magazine/new-build/a1-passive-house-overcomes-tight-cork-city-site#sigProId3d456fd2d2