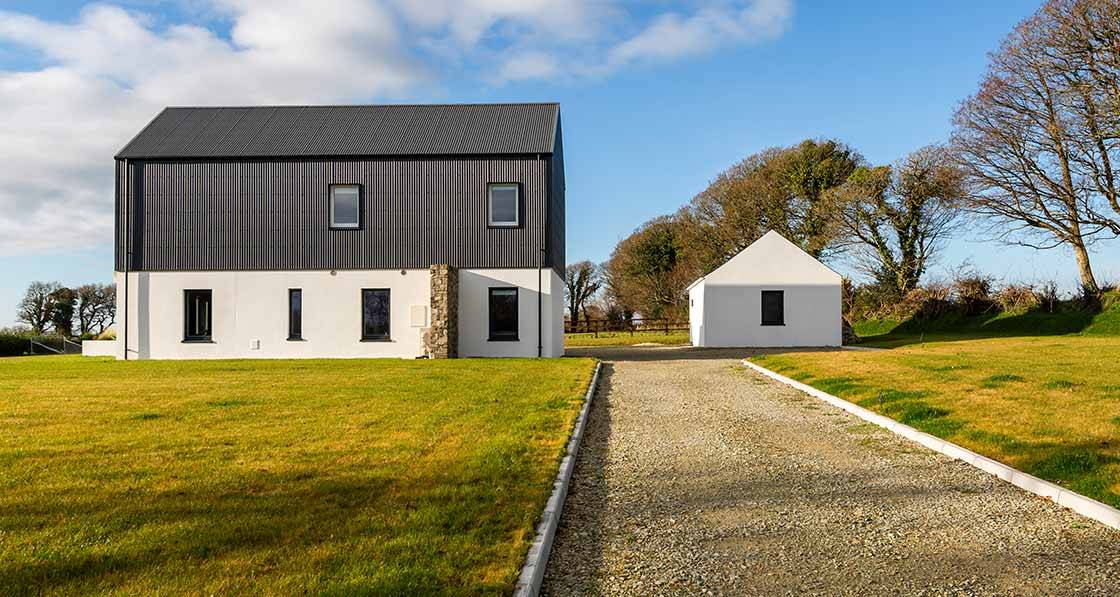
- New build
- Posted
Airtight delight
The proof in the pudding with a notionally low energy building is in the eating. Since moving into their new passive house a little under two years ago, the Murray family’s heating costs have been scarcely believable – in a home that also blitzes the embodied carbon targets in the RIAI 2030 Climate Challenge.
Click here for project specs and suppliers
Development type: 219 m2 detached dwelling
Method: Timber frame, insulated foundations, bio-based materials, heat pump
Location: Co. Wexford
Standard: Passive house classic (pending) and A1 BER
Heating cost: €12 per month space heating cost.
See 'In detail' panel for more information.
It’s hard to know exactly where to start with David and Maria Murray’s new home. This exemplar passive house in rural Wexford offers everyone from industry professionals to self-builders a reference project of tremendous breadth and depth. It also achieves several firsts, not least one of the best airtightness results that we’ve ever seen here at Passive House Plus. In addition, the house has managed to achieve what appears to be a genuine first: an A1 BER rating without the use of PV or other onsite microgeneration.
This is David Murray’s pet project. A wood scientist and longstanding Passive House Plus reader, David meticulously detailed the build from the moment ground was broken right through to occupancy, and is monitoring the building like a hawk. In the back of his mind is an audacious aim: to see if the house can meet the holy grail of net zero carbon emissions, taking account of embodied carbon and operational energy use.
The project brought together some of the most respected names in passive house building in Ireland. Shoalwater Timberframe looked after the structure, Andy Lundberg of Passivate provided the energy consultancy, Gavin O’Sé of Greenbuild did the airtightness testing, Niall Crosson of Ecological Building Systems did the wall and roof U-value calculations, and Damien Mullins of HeatDoc managed heating, ventilation and cooling.
Interesting to note however, neither the main contractor, Knockbine Construction, nor the architect, Isabel Barros, had ever built passive before, and nor had either built with timber frame, though Barros had designed a timber frame extension.
With such ambitious targets in his sights, why did David Murray go with first timers in these key positions?
He explains that he stumbled across Barros’ website and simply loved the designs. “They were exactly what we were looking for: a kind of vernacular architecture, but with a cap tilt to the old farmhouse style of the area.” Ultimately, he points out, this house is a family home, and getting the design right was every bit as important as performance and carbon reductions.
This article was originally published in issue 47 of Passive House Plus magazine. Want immediate access to all back issues and exclusive extra content? Click here to subscribe for as little as €15, or click here to receive the next issue free of charge
“One of the most important requests that David has always mentioned is that he did not want a ‘box’” says Barros, adding that Murray asked her to really challenge the simple box mentality common to many passive house designs.
“The complexity of achieving a highly efficient building with an interesting design is often significant,” says Barros. “I consistently strive for excellence in design, aiming to create innovative buildings that respect the landscape and the environment.” Murray notes too that since Passivate were already on board as energy consultants, he had a freer hand when it came to design. Moreover, the fact that Barros, like Shoalwater, was Wexford-based, also spoke in her favour. “We wanted to keep everything as local as possible,” says Murray, “local is a big part of this – to keep costs and emissions as low as possible.”
In the same vein, Knockbine, who came strongly recommended, were also based in Wexford. Using professionals without experience of this type of building also helped to prove a point. This isn’t rocket-science. With the right team, it’s possible for anyone to adopt ambitious targets.
Isabel Barros agrees. “Collaboration was so important on this project. The clients were very active and educated, and that helped tremendously. Everyone from the timber frame manufacturer to the windows supplier and the main contractor and passive house consultants were all great communicators.”
As a qualified wood scientist with 26 years of experience working with timber frame and engineered wood products, Murray is passionate about the role timber products will play in both the housing and the climate crisis – while recognising the need for sustainable forestry management, coupled with efficient use of precious timber resources to displace more polluting materials. “I believe we’re on the verge of a timber revolution because governments have finally realised that in order to reduce the carbon emissions from construction, the best way to do that is to build with more timber, but in the most resource-efficient way possible, rather than looking at wood as simply a big carbon sponge.”
The house is a showcase of low carbon building products, and engineered wood solutions in particular. The closed panel walls, which were manufactured offsite, feature 300 mm I-studs, fully filled with blown Gutex Thermofibre, and held in place by Smartply Airtight on the inside and Medite Vent on the outside. Similar buildups were used in the living room vaulted roof and flat roof over the entrance lobby. Cold attics were also blown with Gutex Thermofibre to a depth of 450 mm.
The other great advantage of timber frame is that once you get onsite, things happen quickly. Within three weeks, the house was fully weather-tight and airtight, which meant that first and second fix trades could work in a dry and clean environment.
The house is not entirely concrete free. The design team opted for external blockwork for cost and aesthetic reasons – and expediency. The contractor was an experienced and excellent blocklayer. Instead of traditional strip foundations, the insulated raft used 43 per cent less concrete.
So, to that airtightness result, 0.08 air changes at 50 pascals, with a Q50 value of 0.081. “The fact that those numbers are so close,’ says David Murray, ‘is a very good indication of just how airtight the building is.”
It’s an astonishing result and was achieved with Smartply Airtight (which was previously called Propassiv) in all walls and ceilings, a product that in lab conditions has been shown to retain its integrity up to 2,000 pascals. This result also goes some of the way towards explaining how the design team achieved an A1 BER without the use of PV.
I believe we’re on the verge of a timber revolution because governments have realised the best way to reduce carbon in construction is to build with timber.
David Murray explains that when the provisional BER came in, he was very disappointed to see that they’d only managed an A2. “I wasn't happy with that, so I asked the architect if there was any way to get it up to A1.” There was. They could harvest the heat from the shower drains. The showers had already been installed however, so it was too late for that.
“I talked to other people and found out that as part of our pathway certification, we were going to have to do thermal bridging analysis on all of our junctions. A lot of people use the accredited details, but we were able to prove that there was zero thermal bridging in this house.”
Again, this is no mean feat. The building is anything but simple. It is composed of three separate boxes, set at different heights and with three different roof types, generating a range of complex junctions.
-
Insulated foundations with services for heat pump and ventilation unit in small plant room on ground floor (avoiding ducting in attic) Insulated foundations with services for heat pump and ventilation unit in small plant room on ground floor (avoiding ducting in attic)
-
Bespoke airtight intermediate floor junction using Smartply Airtight. Floor is set back and insulated with rigid Gutex Multitherm wood fibre insulation to eliminate thermal bridging at the floor perimeter Bespoke airtight intermediate floor junction using Smartply Airtight. Floor is set back and insulated with rigid Gutex Multitherm wood fibre insulation to eliminate thermal bridging at the floor perimeter
-
Smartply Airtight on the inside combines with Medite Vent on the outside of wall panels, to provide airtightness, vapour control and breathability as well as structural racking strength Smartply Airtight on the inside combines with Medite Vent on the outside of wall panels, to provide airtightness, vapour control and breathability as well as structural racking strength
-
Meticulous detailing of junction between two roofs to eliminate thermal bridging. The junction was formed to allow loose wood-fibre insulation to fully fill all around the end of the steel beam. Thermal Modeling confirmed the junction was thermal bridge free and fRsi-value maintained internally Meticulous detailing of junction between two roofs to eliminate thermal bridging. The junction was formed to allow loose wood-fibre insulation to fully fill all around the end of the steel beam. Thermal Modeling confirmed the junction was thermal bridge free and fRsi-value maintained internally
-
Spandrel panel designed to allow full fill insulation around the ridge beam, and join up with Gutex Multitherm sarking insulation on top of FFI-Joist rafters Spandrel panel designed to allow full fill insulation around the ridge beam, and join up with Gutex Multitherm sarking insulation on top of FFI-Joist rafters
-
Raised Heel truss allows the full 400mm depth of wood fibre insulation to overlap with the 300mm of wall insulation, to eliminate thermal bridging at the roof-wall junction Raised Heel truss allows the full 400mm depth of wood fibre insulation to overlap with the 300mm of wall insulation, to eliminate thermal bridging at the roof-wall junction
-
Pitched Warm Roof: Medite Vent panels provide structural sarking strength to FFI-Joist rafters, and are water vapour diffusion open to the outside, which ensures that the roof can ‘breathe’ Pitched Warm Roof: Medite Vent panels provide structural sarking strength to FFI-Joist rafters, and are water vapour diffusion open to the outside, which ensures that the roof can ‘breathe’
-
Metsa Wood Kerto LVL ridge beam and FFI-Joist rafters. This roof space will be fully filled with loose-blown Gutex Thermofibre wood-fibre insulation. (Note the correct gap between OSB web-stiffener and bottom flange, this ensures that the I-joist transfers the load correctly to the LVL beam) Metsa Wood Kerto LVL ridge beam and FFI-Joist rafters. This roof space will be fully filled with loose-blown Gutex Thermofibre wood-fibre insulation. (Note the correct gap between OSB web-stiffener and bottom flange, this ensures that the I-joist transfers the load correctly to the LVL beam)
-
Medite Vent sarking and Gutex Multitherm cut at precise angle to eliminate thermal bridging where warm roof meets external wall Medite Vent sarking and Gutex Multitherm cut at precise angle to eliminate thermal bridging where warm roof meets external wall
-
Medite Vent sarking panels and Gutex Multitherm insulation cut at precise angle to join and eliminate thermal bridging at ridge Medite Vent sarking panels and Gutex Multitherm insulation cut at precise angle to join and eliminate thermal bridging at ridge
-
Smartply Airtight forms critical airtight and vapour control layer on ceiling (prevents any moisture from passing into attic, which was then insulated with loose blown wood fibre insulation) Smartply Airtight forms critical airtight and vapour control layer on ceiling (prevents any moisture from passing into attic, which was then insulated with loose blown wood fibre insulation)
-
Thermally broken double soleplate overlapping upstand of insulated raft foundation to eliminate thermal bridging at wall to floor junction Thermally broken double soleplate overlapping upstand of insulated raft foundation to eliminate thermal bridging at wall to floor junction
-
Fakro LWT highly insulated and airtight loft ladder taped to Smartply Airtight ceiling panels. (Note the 3 seals for superior airtightness) Fakro LWT highly insulated and airtight loft ladder taped to Smartply Airtight ceiling panels. (Note the 3 seals for superior airtightness)
-
Factory fitted Smartply Airtight forms airtight and vapour control to all external walls, flat roof and vaulted ceilings. Holes pre-drilled for loose blown wood fibre insulation Factory fitted Smartply Airtight forms airtight and vapour control to all external walls, flat roof and vaulted ceilings. Holes pre-drilled for loose blown wood fibre insulation
-
Ventilation supply duct sealed with Pro Clima Tescon Vana airtight tape. (Note, dust caps remained in place until after occupancy when duct covers were fitted and commissioned) Ventilation supply duct sealed with Pro Clima Tescon Vana airtight tape. (Note, dust caps remained in place until after occupancy when duct covers were fitted and commissioned)
-
Ventilation kitchen extract duct sealed to Smartply Airtight OSB ceiling using Pro Clima Orcon F flexible airtight solid acrylic sealant Ventilation kitchen extract duct sealed to Smartply Airtight OSB ceiling using Pro Clima Orcon F flexible airtight solid acrylic sealant
-
All joints in Smartply Airtight sealed with Pro Clima Tescon Vana airtight tape. Carefully planned pre-drilled holes ensure that loose fill wood fibre insulation can fully fill all voids to eliminate thermal bridging. (note, holes taped after pumping insulation) All joints in Smartply Airtight sealed with Pro Clima Tescon Vana airtight tape. Carefully planned pre-drilled holes ensure that loose fill wood fibre insulation can fully fill all voids to eliminate thermal bridging. (note, holes taped after pumping insulation)
-
Shoalwater Airtightness Quality Control Station was critical to locate and seal any penetrations in the airtight layer of the home before wall and ceiling finishes were applied. Shoalwater Airtightness Quality Control Station was critical to locate and seal any penetrations in the airtight layer of the home before wall and ceiling finishes were applied.
-
New airtightness record set! At completion of timber frame, airtightness tester Gavin O’Se of Greenbuild confirms that an n50 of 0.08 ACH and ap50 of 0.081 m3/hr/m2 is “the best air change rate for a home that we have tested”. It was also the first time that he was able to use his smallest diameter fan (in a window opening!) to create the required 50Pa of pressure difference New airtightness record set! At completion of timber frame, airtightness tester Gavin O’Se of Greenbuild confirms that an n50 of 0.08 ACH and ap50 of 0.081 m3/hr/m2 is “the best air change rate for a home that we have tested”. It was also the first time that he was able to use his smallest diameter fan (in a window opening!) to create the required 50Pa of pressure difference
-
Roman Szypura of Clioma House performing a pressure test for Gutex Thermofibre loose blown wood fibre insulation. To remove the insulation, the hopper is put into vacuum mode – easy to recycle at end of life Roman Szypura of Clioma House performing a pressure test for Gutex Thermofibre loose blown wood fibre insulation. To remove the insulation, the hopper is put into vacuum mode – easy to recycle at end of life
-
Service zone insulated with Gutex Thermoflex wood fibre insulation. Note, horizontal service battens eliminate repeat linear thermal bridges along wall studs Service zone insulated with Gutex Thermoflex wood fibre insulation. Note, horizontal service battens eliminate repeat linear thermal bridges along wall studs
-
Fermacell wall and ceiling lining, made from recycled gypsum and recycled cellulose fibers Fermacell wall and ceiling lining, made from recycled gypsum and recycled cellulose fibers
-
Thermal bridge-free door thresholds formed with Bosig Phonotherm structural insulation board, sealed with Extoseal Encors waterproof sealing tape Thermal bridge-free door thresholds formed with Bosig Phonotherm structural insulation board, sealed with Extoseal Encors waterproof sealing tape
-
Raised attic flooring using TR26 supports and Smartply Loft packs to facilitate full 400mm depth of wood fibre insulation to be pumped underneath Raised attic flooring using TR26 supports and Smartply Loft packs to facilitate full 400mm depth of wood fibre insulation to be pumped underneath
-
400mm of loose blown Gutex Thermofibre wood fibre insulation in attic, with Smartply Loft pack flooring above fixed to TR26 raised support joists. (Note raised collar tie to facilitate standing access in attic) 400mm of loose blown Gutex Thermofibre wood fibre insulation in attic, with Smartply Loft pack flooring above fixed to TR26 raised support joists. (Note raised collar tie to facilitate standing access in attic)
-
Broadband fibre cable located within airtight service zone and sealed around conduit with Pro Clima Orcon F flexible airtight solid acrylic sealant Broadband fibre cable located within airtight service zone and sealed around conduit with Pro Clima Orcon F flexible airtight solid acrylic sealant
-
OSB web in Metsa FFI-Joists enables safe and easy routing of all electrical, plumbing and ventilation services within the floor zone OSB web in Metsa FFI-Joists enables safe and easy routing of all electrical, plumbing and ventilation services within the floor zone
-
Insulated front door, made from Medite Tricoya Extreme and set into Accoya wood frame Insulated front door, made from Medite Tricoya Extreme and set into Accoya wood frame
-
VarioTherm modular wall heating panels provides hidden comfortable warmth between bedrooms and bathrooms upstairs VarioTherm modular wall heating panels provides hidden comfortable warmth between bedrooms and bathrooms upstairs
-
VarioTherm modular wall heating panels provides hidden comfortable warmth between bedrooms and bathrooms upstairs VarioTherm modular wall heating panels provides hidden comfortable warmth between bedrooms and bathrooms upstairs
-
Sensors permanently installed in five positions throughout the thickness in North and South facing external bathroom walls to continuously monitor hygrothermal performance (temperature, relative humidity, dew point) compared to design calculations, and provide technical assurance for the long-term durability of products. (Note, the airtight layer was re-sealed) Sensors permanently installed in five positions throughout the thickness in North and South facing external bathroom walls to continuously monitor hygrothermal performance (temperature, relative humidity, dew point) compared to design calculations, and provide technical assurance for the long-term durability of products. (Note, the airtight layer was re-sealed)
-
Hygrothermal sensor mounted on the external face of Medite Vent, protected by breather membrane – resealed after – in the ventilated cavity Hygrothermal sensor mounted on the external face of Medite Vent, protected by breather membrane – resealed after – in the ventilated cavity
-
Smartply Airtight being put through the ringer in terms of product airtightness testing – at pressure differentials of plus 2000 and minus 2000 pascals Smartply Airtight being put through the ringer in terms of product airtightness testing – at pressure differentials of plus 2000 and minus 2000 pascals
-
Metsa Wood FJI engineered timber I-studs minimise repeat thermal bridges through walls, while Medite Vent breathable racking board ensures the wall is water vapour diffusion open to the outside Metsa Wood FJI engineered timber I-studs minimise repeat thermal bridges through walls, while Medite Vent breathable racking board ensures the wall is water vapour diffusion open to the outside
-
Smartply Airtight being put through the ringer in terms of product airtightness testing – at pressure differentials of plus 2000 and minus 2000 pascals Smartply Airtight being put through the ringer in terms of product airtightness testing – at pressure differentials of plus 2000 and minus 2000 pascals
-
Metsa Wood Kerto LVL used to form strong L-corners to allow insulation to fill into corners to eliminate thermal bridging. Also used for top and bottom rails Metsa Wood Kerto LVL used to form strong L-corners to allow insulation to fill into corners to eliminate thermal bridging. Also used for top and bottom rails
-
Gutex Thermoinstal fitted around window and door reveals to eliminate thermal bridging Gutex Thermoinstal fitted around window and door reveals to eliminate thermal bridging
-
3mm expansion gap between Smartply Airtight OSB panel edges, prior to joints being taped with airtight tape 3mm expansion gap between Smartply Airtight OSB panel edges, prior to joints being taped with airtight tape
-
Closed panel to soleplate junction. The Smartply Airtight OSB and Medite Vent breathable panels oversail the soleplate for a precision fit and to facilitate mechanical fixings through the panels into the soleplates Closed panel to soleplate junction. The Smartply Airtight OSB and Medite Vent breathable panels oversail the soleplate for a precision fit and to facilitate mechanical fixings through the panels into the soleplates
-
Intermediate floor of Smartply Strong Deck (OSB/4) T&G, screwed to Metsa Wood FFI-Joists, for superior strength and acoustic performance Intermediate floor of Smartply Strong Deck (OSB/4) T&G, screwed to Metsa Wood FFI-Joists, for superior strength and acoustic performance
https://passivehouseplus.ie/magazine/new-build/airtight-delight#sigProIdf4669d03b0
To take just one example, at one point, a pitched roof intersects with a flat roof. The ceiling I-joist sits on a steel beam alongside a raised heel truss resting on a second steel beam.
“With meticulous detailing and brilliant craftsmanship by Shoalwater on site,’ says Murray, ‘they designed this junction and encased these steel beams completely in insulation – eliminating all thermal bridging.”
That approach was replicated across the project, so that when Andy Lundberg modelled these junctions, he found zero heat loss anywhere.
That combination of exceptional airtightness, exceptional thermal detailing and workmanship nudged the final DEAP calculations just high enough to secure an A1.
David Murray is also keen to emphasise the importance of getting building science right, through combining a robust airtightness strategy with breathable fabric build-ups, to ensure interstitial condensation never poses a problem.
“If you look at the wall build-up, you’ve obviously got the Smartply Airtight board which does as it says on the tin, but also has an integrated vapour control layer on the inside, then you have your breathable wood fibre insulation, then the Medite Vent breathable fibre board on the outside. So, it's a diffusion open wall. Building physics have been carefully thought through, and was a critical element alongside energy and comfort.”
Murray says that many people don’t understand that wood performs better than other materials in controlled moisture environments, defined in service classes in Eurocodes. “As trees grow, they are not only 50 per cent carbon, they are also 50 per cent water,” he says. “So why don’t trees rot? It’s a controlled environment, controlled by nature.”
When converted to wood products, moisture content is reduced to anything from 4 to 18 per cent moisture content, depending on the product and application. “When the products are used in controlled environments in construction they absorb and release small amounts of moisture, just like they did in the forest between winter and summer,” Murray explains. “In this way wood ‘breathes’ and the natural moisture buffer property of wood is a major benefit in building healthy and durable homes.”
That combination of exceptional airtightness and exceptional thermal detailing and workmanship nudged the final DEAP calculations just high enough to secure an A1.
Another kind of buffering was a factor in the decision to opt for wood fibre insulation: temperature buffering due to the material’s high heat storage capacity, to help keep the building cool in summer. “This both delays and reduces overheating which was a key consideration in the design,” he says.
Just to ensure that everything is doing its job, sensors have been installed at five different intervals within the wall build-up. These will measure dew point, humidity and temperature, and this data will help to provide much needed ‘real life’ hygrothermal performance data to compare to design values – findings which are bound to be of interest to other designers considering similar fabric buildups.
This leaves the big question. Has the house achieved net zero carbon? David Murray admits that at the beginning of this project, he had no idea whether to set any kind of net zero objective.
“At first, Maria and I just wanted a comfortable passive house, built with as many sustainable materials as possible to ‘do our bit’ for the environment, but then the wood science geek in me took over. I knew that wood is approximately 50 per cent carbon, so I wanted to build on that fact – literally.” Between research and talking to people in the industry, however, it became clear that at the very least, the project offered an opportunity to see if that elusive target was in reach.
There are two elements to the equation – emissions arising from operational energy, and from the construction of the house.
Building passive ensures that the former will be as low as possible in terms of space heating, and water efficiency measures help with hot water too – with aerated taps and the decision to omit baths. Thereafter, it is a matter of deriving whatever energy is required from renewables, preferably onsite. The building’s reduced space heating and hot water demand are provided by a 6 kW Mitsubishi EcoDan air-to-water heat pump.
“There are so many definitions for net zero,” says Murray. “From day one, we decided that if we were going to do this, we were going to be very open and honest about it. I’m not saying this building will achieve net zero, but we’ll do our best to get there. We’ll do the operational part, and we’ll do whatever we can on the materials part.”
Murray says the decision to install PV panels has been held back until enough data has been collected to say exactly how much energy the house will need, and consider the embodied carbon involved in producing PV panels and batteries. This means that while the house has been wired for PV, the decision to install an array will be delayed until there’s reliable data on both sides of this equation. The same goes for any offsetting which may be required to complete the decarbonisation process.
Regardless of the outcome of this exercise, the house itself remains a monument to great planning, great architecture, and great execution, and data from the 6 kW EcoDan heat pump’s MELCloud dashboard supports this: the heat pump showed an average output for 2023 of 1,878 kWh/yr for space heating, and 4,404 kWh for hot water, breaking down as 9 kWh/m2/yr for space heating, far below the passive house target of 15 kWhm2/yr, and 21 kWh/m2/yr for hot water. Measured hot water demand in most houses is dwarfed by space heating demand, but as in most passive houses, that dynamic is turned on its head.
While the space heating use is lower even than PHPP predicted, the hot water use is above average – in spite of the absence of any baths in the house, the use of aerated taps and showerheads, and the fact that the heat pump doesn’t heat a Quooker tap in the kitchen. It’s worth noting that this isn’t a reflection of the heat pump’s performance, but rather that the household is using a relatively high amount of hot water. Is this a simple matter of comfort taking – the phenomenon where people take back some of the benefits of an energy efficient house, in this case with longer showers?
Irrespective, the extra usage comes at limited cost: after some adjustments by heating contractor HeatDoc in December 2023, the heat pump’s seasonal coefficient of performance has been 3.98 – a figure that includes space heating and hot water, and at the coldest time of the year.
It's a diffusion open wall. Building physics was a critical element alongside energy and comfort.
With the house now bedded in, Murray plans to engage in some formal post occupancy evaluation in the near future with HeatDoc and Dr Shane Colclough of Energy Expertise, including energy use, temperature and indoor air quality monitoring. Given that all internal finishes and wood panels in the fitted furniture used materials designated as no added formaldehyde (NAF) or ultra-low emitting formaldehyde (ULEF), Murray is also keen to monitor formaldehyde levels in the home too. But the anecdotal experience has been largely very positive.
After the family moved in, temperatures got as high as 28 C on a couple of days, but there were mitigating circumstances. This was during a heat wave, when temperatures in Wexford got as high as 32 C, Murray hadn’t turned the ventilation system on (to allow the dust to settle), and the heat pump hadn’t been set to weather compensating mode yet. Heat waves aside, the house has averaged constant temperatures of 20-21 C during winter and 21-24 C during summer months.
Some indoor air quality experts express scepticism about anything other than powerful overhead cooker extractors for the critical issue of cooking fumes, Murray’s experience of the installed down draft hob extractor suggests it works well and eliminates cooking smells quickly with no lingering smells, so he assumes it’s also taking away any pollutants from cooking.
What’s more, Murray’s impression of the whole house ventilation strategy is that it’s dealing with everything the family can throw at it – including the tests posed by one fourlegged member. “Even with a labrador sleeping in his cosy corner people comment that there’s no dog smell in the house, so the ventilation system must be working well,” says Murray.
“Pity it doesn’t eliminate the dog hairs but at least that’s not a passive house issue.” With the house now fully up and running, David and Maria are thrilled with the experience of living in a home characterised with consistent, even temperatures and a constant supply of fresh air.
‘People have asked us, “would you do anything differently?” says David. “We’re very lucky in that we’re able to say “no”. We’re just delighted with how it's gone.”
Selected project details
Client: David & Maria Murray
Architect: Isabel Barros Architects
Civil / structural engineer: Tanner Structural Designs
Energy consultant: Passivate
Main contractor: Knockbine Construction
Mechanical contractor: Heat Doc
Electrical contractor: Custom Electric
Airtightness consultant: Greenbuild
Build system supplier: Shoalwater Timber Frame
Wall insulation: Ecological Building Systems
Roof insulation: Ecological Building Systems
Thermal breaks: Ecological Building Systems
Airtightness products: Medite
SmartPly / Ecological Building Systems
Windows and doors: True Windows / McNally Joinery
Mechanical ventilation: Zehnder, via Heat Doc
Heating system: Mitsubishi, via Heat Doc
Embodied carbon
Murray aimed to reduce the upfront carbon as much as practicable, considering climate, materials durability and longevity of performance. Only products with Environmental Product Declarations (EPDs) were used where possible, with an emphasis on products likely to assist the building to achieve a low embodied carbon score.
The house’s embodied carbon was calculated by John Butler, using PHribbon, taking into account the carbon emitted in the manufacture of the construction materials, in transporting them to site and in the construction process itself. On top of that, the assessment included projected emissions from maintenance, repair and replacement of materials over the building’s projected lifespan – based on a highly pessimistic 50-year lifespan as per the EU’s Level(s) framework, instead of the marginally less pessimistic 60 years assumed in the UK – and finally the emissions estimated to be released at the building’s end of life.
One great bone of contention here for advocates of biogenic materials like timber and wood-based insulation is the treatment of sequestered CO2 in whole life carbon calculations. When trees are growing, they draw CO2 from the air through photosynthesis, and store it in every part of the tree – trunk, branches, roots and leaves. When cut down and processed, the materials produced retain any stored CO2, and only release it at their end of life, assuming the material is incinerated or allowed to decompose – a phenomenon which may only occur to a limited extent in landfills. So you could be forgiven for thinking that if the timber is designed to be reused, an embodied carbon calculation would assume that CO2 remains stored. But you would be wrong. The applicable EN standard, EN 16485, determines that even if the timber is eventually reused – including some easily extractable materials in this case, such as the blown wood fibre insulation – the benefit of the stored CO2 passes on to the next use at that point. And because embodied carbon calculation goes from cradle to grave, the CO2 stored in the building tracks the building’s projected life.
In a house like this – brimming with timber, cellulose and wood products, there’s a lot of CO2 stored in the finished building – 58 tonnes, to be precise. It may have taken eighty-five tonnes of carbon dioxide equivalent (CO2e) to build the house – the upfront emissions stage of the building’s whole life cycle assessment – but a more conventional build with cavity walls and strip foundations would have meant even more. The reason is pretty intuitive: even if you ignore the carbon stored in the building, it takes a lot less CO2 to process timber and wood products than it does to fire the kilns to make cement, and a lot less CO2 to transport lighter materials to site than heavy, bulky concrete products.
And for as long as this building lasts – which, given the combination of cutting edge building physics knowhow and architectural quality, could be hundreds of years, the vast bulk of that CO2 will remain stored.
In detail
Building type: Detached, part single-storey, part two-storey, four-bedroom family home.
Floor area: 219 m2 (206 m2 TFA).
Platform timber frame / I-stud and I-joist construction.
Site type & location: Rural site, 800 m from Crossabeg village in Co Wexford. 10 km from Wexford town.
Completion date: Occupied since July 2022, but practical completion in July 2023.
Budget: Not disclosed.
Passive house certification: Passive house classic, certification pending
Space heating demand: 13.29 kWh/m2/yr
Heat load: 8.42 W/m2
Primary energy non-renewable: Pending
Primary energy renewable: Pending
Heat loss form factor: 3
Overheating: PHPP, 3 per cent of year above 25 C
Number of occupants: Two adults, two children and a dog
Energy performance coefficient (EPC): 0.149
Carbon performance coefficient (CPC): 0.138
BER: A1 (23.59 kWh/m2/yr)
Embodied carbon: 426 kgCO2e/m2 for RICS life cycle stages A1 through C5, but excluding operational use (B6 & B7). Calculated using PHribbon. Assessed in accordance with Level(s) framework and RICS 1st edition (but using estimates of actual transport distances in most cases). Meets the RIAI 2030 Climate Challenge target for buildings of over 133 m2 of 450 kg CO2e/m2.
Whole life carbon: To be assessed, pending installation of PV array.
Measured electricity use (heating and hot water): 2,239 kWh/yr (January-December 2023). Total output of heat pump in 2023 was 6,282 kWh. Monitoring data for January-March 2024 indicates an annualised requirement of 9 kWh/m2/yr for space heating, and 21 kWh/m2/yr for domestic hot water. Heat pump electricity use and heat output for January-March 2024 indicates an average seasonal COP comfortably in excess of 4. On this basis, and a 1 Year Fixed Smart Electricity tariff from SSE from Bonkers.ie, the estimated space heating costs are €12/month.
Airtightness: n50: 0.08 ACH at 50 Pa (q50 = 0.081 m3 hr/m2 at completion of timber frame, and 0.19 ACH at 50 Pa (q50 = 0.205 m3/(hr.m2) at final completion stage.
Thermal bridging: Whole House Y-factor = 0.028576
Critical junctions modelled by Passivate. Insulated foundation system. Double plate / thermally broken soleplates insulated between. Any gaps under soleplates (in between structural shims) fully filled with foam insulation. Bosig Phonotherm at door thresholds. Reveals made with Bosig to fit door frames exactly. I-studs (walls) and I-beams (vaulted roof & flat roof). 13 per cent reduced bridging from solid studs to I-studs plus a further 8 per cent reduction for horizontal service zone battens. All insulation layers continuous. Walls and roofs fully filled with loose blown Gutex Thermofibre to ensure no gaps blown at higher density. Window reveals insulated with rigid Gutex Thermoinstal wood fibre insulation. I-joist floor zone stepped back around full perimeter and insulated with rigid Gutex Multitherm wood fibre insulation. Raised heel truss to allow full continuity of Thermofibre insulation thickness at ceiling level (ventilated cold roof). Fakro insulated and airtight attic ladder. Rigid Gutex Multitherm wood fibre insulation over I-beams on vaulted roof. Horizontal service zone battens at 600 mm centres horizontally to reduce linear bridges in line with studs (minimal point bridging = 8 per cent reduction in U-value). Insulated and airtight front door made with Medite Tricoya Extreme (MTX) and Accoya frame.
Ground floor (top to bottom): Tile or timber floor finishes; 100 mm reinforced concrete slab incorporating underfloor heating pipes; Polythene separating layer; insulated foundation system incorporating bespoke design high density EPS structural ring beam to support external and internal loadbearing walls, with 3 x 100 mm layers of high density continuous EPS floor insulation; radon membrane / DPM with all joints taped and sealed; 50 mm T3 blinding; 200 mm T2 permeable hardcore; compacted T1 structural hardcore bed design and inspected by structural engineer. U-value: 0.10 W/m2K
Walls (outside to inside): Sand and cement render on 100 mm block outer leaf (ground floor)/ corrugated metal cladding with 50 mm ventilated cavity on 50 mm horizontal treated timber battens, on 100 mm block outer leaf (first floor); 50 mm vented and drained cavity; Proclima Solitex Fronta WA breather membrane; 12 mm Medite Vent vapour diffusion open category 1 structural outer sheathing panel with 3 mm expansion gaps and all joints taped with Proclima Tescon Vana airtight tape; 300 mm Metsawood FJI 38/45 I-Studs fully filled with Gutex Thermofibre loose-fill wood fibre insulation; 12.5 mm Smartply Airtight OSB3 panel with integrated vapour control layer with 3 mm expansion gaps with all joints taped with Proclima Tescon Vana airtight tape; 50 mm battened service zone insulated with 50 mm Gutex Thermoflex wood fibre insulation; 12.5 mm Fermacell board made from gypsum and recycled paper fibres; Plaster skim coat. U-value: 0.11 W/m2K
Roof (outside in): Pre-finished Tata Steel corrugated metal sheets (type 1) or Cembrit Berona fibre cement roof tiles (type 2); Ventilation zone of 50 mm treated roofing battens and 25 mm treated counter battens; Proclima Solitex Plus breather membrane; Prefabricated truss rafters with 400 mm raised heel for continuous insulation depth at eaves; Ventilated attic space; 400 mm Gutex Thermofibre loose fill wood fibre insulation; 12.5 mm Smartply Airtight OSB3 panel with integrated Vapour Control Layer with 3 mm expansion gaps with all joints taped with Proclima Tescon Vana airtight tape; 2x 35 mm (un-insulated) counter-battened service cavity to suit 70 mm sealed recessed LED downlights; 12.5 mm Fermacell board made from gypsum and recycled paper fibres; Plaster skim coat. U-value: 0.09 W/m2K
Pitched ceiling: Cembrit Berona fibre cement roof tiles; ventilation zone of 50 mm treated roofing battens and 25 mm treated counter battens; Proclima Solitex Plus breather membrane; 80 mm Gutex Multitherm wood fibre insulation board (Tongue & groove); 12 mm Medite Vent vapour diffusion open category 1 structural sarking panel with 3 mm expansion gaps and all joints taped with Proclima Tescon Vana airtight tape; 300 mm Metsawood FJI 38/45 I-Studs fully filled with Gutex Thermofibre loose-fill wood fibre insulation; 12.5 mm Smartply Airtight OSB3 panel with integrated vapour control layer with 3 mm expansion gaps with all joints taped with Proclima Tescon Vana airtight tape; 35 mm battened service cavity (un-insulated, because of Multitherm on outside); 12.5 mm Fermacell board made from gypsum and recycled paper fibres; Plaster skim coat. U-value: 0.10 W/m2K
Flat roof: VM Zinc Plus standing seam cladding; VM Zinc breather membrane; 18 mm Smartply Ultima OSB4 roof decking panel; 50 mm treated batten ventilation zone; Tescon Naideck nail sealing tape under battens; Proclima Solitex Plus breather membrane with all joints taped with Tescon Vana tape; 12 mm Medite Vent vapour diffusion open category 1 structural sarking panel with 3 mm expansion gaps and all joints taped with Proclima Tescon Vana airtight tape; Tapered firring pieces to give a fall of 3 degrees, with tapered void fully filled with Gutex Thermofibre loose fill wood fibre insulation; 300 mm Metsawood FJI 38/45 I-Beams fully filled with Gutex Thermofibre loose-fill wood fibre insulation; 12.5 mm Smartply Airtight OSB3 panel with integrated vapour control layer with 3 mm expansion gaps with all joints taped with Proclima Tescon Vana airtight tape; 35 mm battened service cavity (un-insulated); 12.5 mm Fermacell board made from gypsum and recycled paper fibres; Plaster skim coat. U-Value: 0.10 W/m2K
Windows & external doors: True Windows / UAB Doleta triple glazed IV-98 softwood + aluclad inward opening windows; Argon filled (2nd and 3rd glazing) 90 per cent, 20.0 mm; 3 x Saint-Gobain Planiclear 4 mm glazing with Planitherm XN low-e coating on first glazing; Solar factors: g-value = 0.54; shading coefficient = 0.62; Frame thermal transmittance (Uf): 1.1 W/m2K.; Glass thermal transmittance (Ug 0o related to vertical position): 0.5 W/m2K; Spacer thermal conductivity (Psig): 0.03 W/m2K. Overall U-Value of windows: 0.79 W/m2K
Heating system: Mitsubishi Ecodan 6kW R32 air-to-water heat pump, with a 200 litre hot water cylinder.
Ventilation: Zehnder Comfoair Q350 SI TR heat recovery ventilation system, certified passive house component with a stated efficiency of 96 per cent; A+ energy rating; 41 dB
Potable water use: Target was 40 per cent reduction in potable water use (RIAI 2030 Climate Challenge); Dual flush toilets throughout; Aerated taps and shower heads; 3 bar pressurized system and all fittings rated for 3 bar; Quooker tap uses less energy than a kettle and reduces wastewater. Calculations using https://watercalculator.uk/calculator/ pending.
Electricity: Pre-wired for PV but not yet installed. Client keen to wait for at least two years of data, plus fully understand the embodied carbon impact.