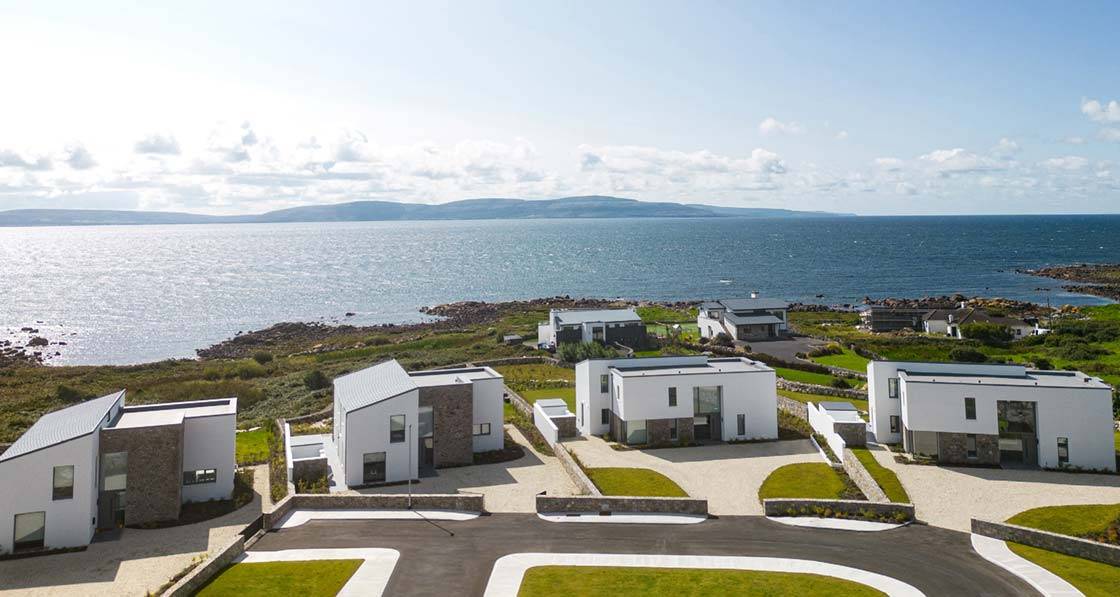
- Feature
- Posted
Bay window
Click here for project specs and suppliers
Development type: Cluster of four detached homes Method: Full-fill cavity wall, strip foundations, air-to-water heat pump
Location: Brownfield site in Furbo, Co. Galway
Standard: Passive house classic and A1 BER
Heating cost: €19-21 per month space heating cost.
See 'In detail' panel for more information.
You’ll travel a long way to find a more beautiful site than Radharc na Chaoláire in Furbo, Co. Galway. The four certified passive houses, designed by Helena McElmeel Architects, have uninterrupted views over Galway Bay, with the Burren and the hills of Clare in the distance.
‘Radharc’ means view in Irish, but Chaoláire would not be as easily understood beyond Connemara. It translates as ‘narrowing of the bay’ and is how generations of seafarers living in the Gaeltacht referred to the stretch of water which the houses overlook.
Choosing a name like this is not just a sop to tradition. These houses were designed with reference to the built heritage of the area and constructed using local materials and local skills.
Architect and passive house designer Owen Morgan of Helena McElmeel Architects worked closely with Helena on the project.
“It was great,” he says, “to have a local team from the Connemara Gaeltacht delivering passive houses in the middle of Furbo. The other great thing about it is that passive is becoming normal. This is becoming the best way of doing things.”
Since establishing her practice in Galway just over ten years ago, McElmeel has been at the forefront of sustainable building in the west. She has witnessed the growing awareness of and appetite for passive house in both the industry and among the wider public.
“It's been much easier over the last few years than it was at the beginning,” she says, “when it was much more niche. It’s far easier to take clients with us on the passive journey now. Many want to go passive right from the start.”
Most of the projects underway at the practice are passive or EnerPHit, and many of those have either been certified or are scheduled for certification.
“The more we build and the more evidence we collect about how they're performing, the more confident we can be in saying, ‘This works. These houses perform like they say on the tin.’” In Furbo, the client – Nikolai Burkhart, a Germany-based developer – bought into the idea of passive almost as soon as it was suggested. “The client was keen to build to the best possible standard – A1-rated, passive house, with a high standard of interior fit out,” says McElmeel.
Relying on wet plaster for airtightness isn't foolproof. Depending how the scratch coat is done, the plaster might look fine but could still be leaking.
The site may have wonderful views, but that is not to say that it was without challenges. Any Connemara builder will tell you: when you work out here, you have to negotiate with a large quantity of rock. It takes a great deal of patience, and a lot of work with heavy plant to prepare the site ahead of construction.
In addition, there had been an ‘underutilised’ commercial building to the front. “This was in need of some TLC, to say the least,” says McElmeel, who adds that there are plans to develop another portion of the site, which she hopes will contribute more fully to the streetscape and the community in general.
In designing the houses, the architects set out to reflect what can already be seen in the area.
“You’re asking, where are the forms that we can play with? You're looking at the lean-to sheds which you’ll find up and down the side roads perpendicular to the sea all along the coast here. You’re also looking at the stone walls that enclose those structures, their monopitch roofs and render finishes. You have remnants of that left, but there's an awful lot of clutter in the way now, which makes it hard to see the vernacular.”
She notes too that the detailing of these structures tends to be neat and clipped, with an absence of over-hangs. And no brick. There’s very little brick in Galway generally, which tends to constrain the palette of materials.
At treated floor areas of between 242 m2 and 245 m2, the houses are large and feature complex junctions. Yet a form factor of three reveals a relatively compact design, a factor which McElmeel explains, helps reduce embodied carbon by reducing material quantities used.
The central design challenge, McElmeel explains, comes back once again to those views.
The developer wanted to maximise window sizes on the southern elevation to make the most of what is a unique selling proposition.
The architect, on the other hand, was focused on performance and comfort, and that meant optimising the glazing for thermal integrity and overheating prevention.
This meant that window placement and size was the subject of what McElmeel calls “tense debate”.
Getting the mix right involved finding the sweet spot between these competing objectives. Low G glass played a role in reducing heat transference but couldn’t be relied upon exclusively, says Owen Morgan. PHPP modelling was used to explore the possibilities.
Using the data to demonstrate unambiguously that overglazing would be a problem did a lot of the hard work in the argument. The design team was also able to show how framing views using smaller windows can be just as effective as installing vast expanses of glass.
In the end, developer and architect went through window size and placement room by room. This approach worked, delivering a passive standard thermal envelope with minimal overheating risk: 2.3 per cent of the year above 25C on house one, 2 per cent on house 4 and 1 per cent on houses 2 and 3.
This article was originally published in issue 48 of Passive House Plus magazine. Want immediate access to all back issues and exclusive extra content? Click here to subscribe for as little as €15, or click here to receive the next issue free of charge
McElmeel points out that when it comes to overheating, you cannot rely on mitigation, and you can’t rely on occupant behaviour.
“All of the houses are occupied now. There’s been a handover, but they’re rented. You could have different occupants next year, and there’s no guarantee that documents will be read. People shouldn’t need information to live there comfortably.”
With an owner-occupier who’s just built their forever home, you can talk about shading and mitigation strategies, but for developer- led projects, that isn’t going to work.
Moreover, as McElmeel points out, you won’t find overhangs or elaborate facia or soffit detailing in this part of the country. If you want your building to sit well amid existing structures, you’re going to have to leave those out.
While most of the practice’s projects at present are timber frame, all four houses at Radharc na Chaoláire are masonry-built. The developer’s construction partner – Noel Mannion and his team, NCP Togail Teo – specialised in block-built houses. Though the company had long experience in traditional building, this would be their first passive house.
“It was a significant step up for the construction team,” says McElmeel. “They were using materials, techniques and detailing that they hadn’t come across before.”
This meant that the architect spent a lot of time onsite working with the build team. In addition, the contractor undertook training as part of their commitment to deliver.
Owen Morgan pays tribute to foremen Mick Conneely and Ciarán Ó Conaire, who fully bought in to the passive process and worked hard to deliver the spec.
“Everyone knew what they had signed up to do,” says Morgan, “and they wanted to make it happen. Yes, there were times when it was challenging, but they stuck to the task and delivered on every target.”
Building during COVID and the outbreak of war in Ukraine caused both supply and scheduling challenges, as they did on every site, but the biggest challenge that the build team faced was airtightness.
The views might be stunning, but achieving a passive standard building envelope on a site exposed to the Atlantic winter is no picnic, particularly with block construction. Morgan also pays tribute to veteran passive house specialist Roman Szypura of Clioma House, who went above and beyond in teaching and training the build team.
-
Armatherm thermal breaks prevent thermal bridging where a steel column meets the floor Armatherm thermal breaks prevent thermal bridging where a steel column meets the floor
-
Intello airtightness & vapour control layer under a Speedline metal furring ceiling channel. Intello airtightness & vapour control layer under a Speedline metal furring ceiling channel.
-
Alma Vert thermal break at thresholds Alma Vert thermal break at thresholds
-
Thermally-broken Internorm HF310 timber/ alu clad windows Thermally-broken Internorm HF310 timber/ alu clad windows
-
Thermally broken stainless steel Ancon bracke Thermally broken stainless steel Ancon bracke
-
Insulated roof upstand Insulated roof upstand
-
Underfloor heating Underfloor heating
-
Pro Clima Aerosana Visconn wall chases Pro Clima Aerosana Visconn wall chases
-
Plastering ahead of services being installed Plastering ahead of services being installed
-
Ubbink ductwork install on-going Ubbink ductwork install on-going
https://passivehouseplus.ie/magazine/feature/bay-window#sigProId97541dee36
“Relying on the wet plaster as your airtightness on blockwork isn't as foolproof as it might seem,” says Owen Morgan. “Depending how the scratch coat is done, the plaster might look fine but could still be leaking.”
The builder ended up acquiring a fan in order to run tests and address each leakage as it arose. That skill set improved as the project matured; the magic 0.6 ACH was secured far more quickly on house 4 than house 1.
McElmeel says that the single-mindedness of the contractor was crucial to the success of the airtightness strategy. “It just wasn't going to beat them... but that's not a given.”
The design team also made efforts to reduce the embodied carbon of concrete used onsite. Fifty per cent GGBS from Ecocem was used in poured concrete from Coshla Quarries, including the raft foundation, though GGBS was not integrated into the blockwork.
Designed as rentals, the homes require little user engagement. People shouldn’t need to read documents to live there comfortably.
In addition, engineer John Britton and his team worked hard to make the concrete that was used work as hard as possible, by keeping structures lean and well-detailed. As has been pointed out, these are big houses, aimed at the very top of the market.
The interiors, which Owen Morgan describes as ‘a project within a project’ are beautifully finished. With this high-end passive scheme on the west coast, and a number of high density passive social housing projects announced by Cairn Homes on1 the east coast, there are clear signs of passive house breaking through at both ends of the market.
But would such a high-density scheme have been possible in Furbo?
Helena McElmeel points out that higher density housing isn’t possible in the area due to the absence of local authority sewage and wastewater treatment infrastructure – and nor are there any plans to provide these essential services.
Each of these houses had minimum site sizes and maximum density restrictions due to the need to have individual treatment systems. Shared treatment systems are discouraged in private developments by the local authority, following some bad experiences related to maintenance and upkeep during the Celtic Tiger era.
The real success of this project lies in the way in which it managed to keep so much within the parish. As well as making use of the stone excavated in boundary walls, the design incorporated a range of locally- sourced materials, including the distinctive stone – granite externally and green Connemara marble internally.
It’s that combination of local skills and local materials that really makes this project such a passive house exemplar.
Selected project details
Client: OceanView4U
Architect: Helena McElmeel Architects
Structural engineer: Britton Consulting Engineers
Civil engineer: Profe Engineering
Energy consultant: 2Eva
Project management: Helena McElmeel Architects
Main contractor: NCP Togail Teo
Quantity surveyors: Atlantic Quantity Surveyors
Mechanical contractor: Sheeran Heating & Plumbing
Electrical contractor: Eamon Lynch Electrical
Airtightness consultant: 2Eva
Passive house certifier: Earthcycle Technologies
Bonded bead insulation: Envirobead
Cavity wall installer: OCI insulation services
Thermal breaks at thresholds: Partel
Thermal blocks: Mannok
Thermally broken brackets: Ancon, via Leviat
Thermal break pads: Armatherm
Roof insulation: Isover
Additional roof insulation: ALM HM Ireland
Above deck roof insulation: Unilin
Airtightness products: Ecological Building Systems
Airtightness consultant: Clioma House Ltd
Windows and doors: Internorm, via Interlux
Internal electric blinds: Apollo Blinds
Heat recovery ventilation: Brink, via Kernohan Distribution
HRV installer: HRV West
Air-to-water heat pump: Samsung, via Joule
Screeds: Cemflor
Concrete products: Coshla Quarries
GGBS: Ecocem, via Coshla Quarries
Engineered oak flooring: Trunk Flooring
Zink and flat roofs: Vertex Roofing
Landscaping: Colin Cooney Designs / Bill Madden Nurseries Ltd
Lighting: Hicken Lighting
Water conserving fittings: Waterloo Bathrooms Dublin
Wastewater treatment system: Biocell Water
Fit-out: Barry Hanley Carpentry
Fitted furniture/kitchens: AMC Kitchens
Loose furniture: Nordic elements
In detail
Building type: A cluster of four detached, two-storey passive certified houses located in Furbo, Connemara, Co, Galway. The detached houses come in two types; however, each one has a distinctive interior design, colour palette & furnishings.
Size: 260 – 270 m2 gross floor area, 242 – 245 m2 treated floor area.
Site type & location: Brownfield site in Furbo village centre, Connemara, Co. Galway.
Completion date: Phased completions April 2023 – August 2023.
Budget: Not disclosed.
Passive house certification: Passive house classic certified
Space heating demand: 12.6 – 13.9 kWh/m2/yr
Heat load: 12.5 – 13 W/m2
Primary energy non-renewable: 48 – 49 kWh/m2/yr
Primary energy renewable: House 1, 2, 3 & 4-27 kWh/m2/yr
Heat loss form factor: 3-3.03
Overheating: 1-2.3 per cent of year above 25C
Number of occupants: 3.1 occupants (all houses)
Energy performance coefficient (EPC): 0.135 – 0.137
Carbon performance coefficient (CPC): 0.084 – 0.085
BER: A1 (17.45 – 18.41 kWh/m2/yr)
Environmental assessment method: Not applicable
Embodied carbon: Analysis on-going
Measured energy consumption: Bills / POE not available currently on this project.
Energy costs: In the absence of monitored data, Passive House Plus calculated the space heating costs for the homes. Based on the PHPP-calculated space heating demand and a relatively conservative assumed coefficient of performance (COP) of 3 to 1 – far below the stated seasonal COP, the annual electricity demand per home for space heating ranged from 1,016 – 1,135 kWh/yr. A price comparison on Bonkers.ie for a rural home on a smart meter found the best rates for this electricity use at €227- €253/ yr per house, based on Energia’s Smart Data 30 per cent tariff. This figure includes VAT at 9 per cent and is based on 55 per cent of heat pump running time at day rate, 34 per cent at night rate and 11 per cent at peak rate. As ever with electrical heating analysis in Passive House Plus, standing charges are omitted for a simple reason: the standing charges apply irrespective of electrical heating use, for any property connected to the grid.
Airtightness: 0.59 to 0.64 ACH at 50 Pa Thermal bridging: For passive house certification the thermal bridges and associated heat losses were calculated for all construction details for each house type and inputted into each PHPP. MOLD software was used for these calculations.
Key measures taken to reduce thermal bridging included the use of Mannok Aircrete 7 blockwork courses at raft level and at parapets, Ancon thermally broken stainless steel support connections to outer leaf blockwork, Partel Alma Vert thermal breaks to all door thresholds and window cill connections, Armatherm pads under any steel columns brought down to raft level.
Ground floor: 75 mm Cemfloor screed, followed underneath by 160 mm PIR insulation (0.022 W/mK), 150 mm reinforced concrete raft (50 per cent GGBS), on Monarflex RMB400 radon barrier on T3 blinding. U-value: 0.132 W/m2K.
Walls: External sand / cement render, followed inside by 100 mm blockwork, 200 mm cavity pumped with EnviroBead Plus EPS Bead insulation (0.033 W/mK), 100 mm blockwork, internal plaster finish (airtight layer). U-value: 0.155 W/m2K (thermal bridges and from wall ties were calculated and included in the U-Value calculation).
Sloped roof (all houses): Mono-pitch zinc roof with VM Plus Zinc, followed underneath by 118 mm Warmdex (18 mm plywood with 100 mm PIR Insulation (0.020 W/mK), on plywood deck, on 220 mm joists with full fill Metac (0.034 W/mK). U-value: 0.093 W/m2K.
First flat roof type (all houses): Alkorplan PVC membrane on 120 mm Xtratherm (now Unilin) FR/ALU (0.022 W/mK), on plywood deck, on 180 mm joists with full fill Metac (0.034 W/mK), Ceiling zone with 50 mm Metac (0.034 W/mK). U-value: 0.086 W/m2K
. Second flat roof type (houses 1 and 2): Alkorplan PVC membrane on 120 mm Xtratherm (now Unilin) FR/ALU (0.022 W/mK), on plywood deck, on 150 mm joists with full fill Metac (0.034 W/mK), Ceiling zone with 50 mm Metac (0.034 W/mK). U-value: 0.092 W/m2K.
Windows & external doors: Internorm HF310 timber/ alu thermally-broken triple glazed windows. Low G value glass to south façade. U-value: 0.69 W/m²K. Internorm HT400 timber/alu entrance door. U-value: 0.7 W/m²K. Internorm HS330 timber/alu lift-sliding door. Low G to south façade. U-value: 0.72 W/m²K.
Heating system: 8kW Samsung AE080RXYDEG EU air-to-water heat pump. SCOP 4.44. 230L stainless steel Duplex LDX 2101 Cyclone pre-insulated unvented pressurised hot water cylinder. Underfloor heating to ground and first floors.
Ventilation: Brink Flair 400 heat recovery ventilation system — Passive House Institute certified to have heat recovery rate of 89 per cent.
Potable water use: 118 l/p/day, calculated using the DEAP water efficiency calculator. Low flow aerators (5 lpm) to taps to reduce water consumption. Dual flush WCs. Almost half of the total relates to the 12l/ min overhead rain shower, offsetting the benefits of the low flow rate taps and lower flush volumes to WC cisterns – to be avoided on future projects.
Electricity: Currently no PV systems on site.
Appliances: Low energy use kitchen appliances were sourced – details of which were included in the PHPP energy models for the houses.
Sustainable materials: Metac insulation was used under the deck on all roofs, made from up to 75 per cent recycled glass. Partel Alma Vert (made from recycled PET bottles) thermal breaks were used to the custom designed thermal breaks to all thresholds and window cills. 50 per cent GGBS cement used in all poured concrete on site including raft foundations. Dry-jointing to the dry-stone walls, particularly to the rear, to support biodiversity insects and wildflowers. Stone used on houses was sourced in a nearby quarry. The decorative stone and Connemara marble were also sourced locally. Stone excavated on site was used for the boundary walls. Native wildflower planting to the southern area of the garden with all boundary walls dry stone construction.
Image gallery
-
House type A - East elevation House type A - East elevation
-
House type A - North elevation House type A - North elevation
-
House type A - South elevation House type A - South elevation
-
House type A - West elevation House type A - West elevation
-
House type A - First floor House type A - First floor
-
House type A - Ground floor House type A - Ground floor
-
House type B - East elevation House type B - East elevation
-
House type B - North elevation House type B - North elevation
-
House type B - South elevation House type B - South elevation
-
House type B - West elevation House type B - West elevation
-
House type B - First floor House type B - First floor
-
House type B - Ground floor House type B - Ground floor
https://passivehouseplus.ie/magazine/feature/bay-window#sigProId29524c3a34