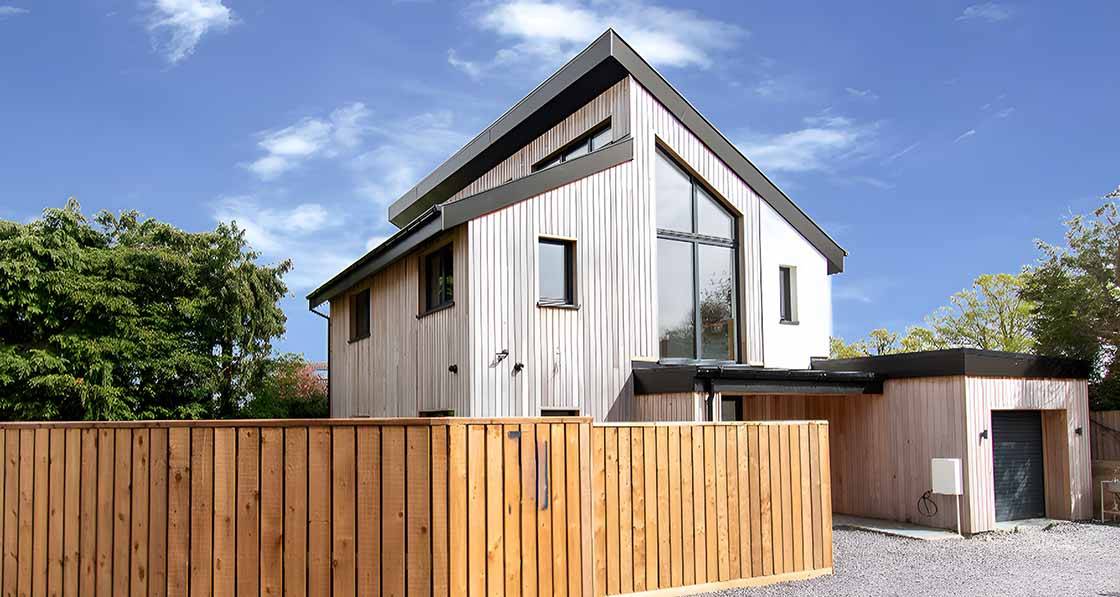
- New build
- Posted
Ace of Herts
Fancy owning an energy positive, timber-based passive house in one of the most desirable locations in England, without the hassle of having to build it yourself? A new three-house development nearing completion in Hertfordshire may be just the ticket.
Click here for project specs and suppliers
Method: Timber frame, insulated foundations, bio-based materials, hot water heat pump, PV
Location: St Albans
Standard: Passive house classic (pending), HQM and EPCs of A and comfortably above 100 in each case
Energy cost: Estimated net profit of £370-670/yr.
See 'In detail' panel for more information.
What if a small development could prove a point? What if it could prove two? A new development in St Albans hopes to do just that: firstly, that world-class sustainable building could be the norm and, secondly, that it makes sense for the institutions financing house building and buying to consider energy use.
James Fisher, who developed the scheme along with business partner Troy Pickard says that, from the outset, the plan was to develop sustainable homes.
The two met while Pickard was working on another project and discovered that their interests aligned, specifically to create a development that acted as a kind of pilot light, signalling how residential building could be better. “He was fed up with the industry’s resistance to new techniques. In the end we decided we had the perfect combination of skills,” Fisher said.
The project, located at 1-3 Haven Place, Park Street Lane in St Albans, consists of three dwellings, all detached and constructed using an offsite timber frame system on a semi-rural brownfield site, with units one and two being three-storey and unit three being two-storey. All three are set to be certified to the passive house plus standard.
Fisher and Pickard functioned as their own main contractor, something that allowed them to control every aspect of the build and, they hoped, prove that sustainable house building was economically viable.
“I’ve spent 25 years telling everyone to be more energy efficient. The exceptionally large homebuilders, because the planners don’t know about development finance, are able to get away with [not doing] it. They just want to make as much money as they can.”
As a result, 1-3 Haven Place’s experimental nature led to the third, two-storey, unit in particular being a focus for proving the point. “Will we recoup it? This is the experiment that we are going to have on that third home. It will have an EPC [Energy Performance Certificate] of 120. That’s groundbreaking for the south of England; it barely uses any energy across the year. We will find out if there’s a value case,” he said.
Architect Heather McNeill, director at AD Practice in St Albans, says Fisher came to the practice because of its reputation for energy efficient designs. (McNeill’s previous work on an Enerphit Plus project in nearby Harpenden was featured in issue 43 of Passive House+).
“We'd done some work on his own house before, and he knew about the passive house stuff we were doing. With this, he wanted to do a showcase project,” she said.
Working with Fisher, McNeill says, it soon became obvious that Fisher was committed to building ultra-low energy homes: “Certainly he feels there should be a drive toward passive house.”
Similarly, Fisher was more than confident in choosing AD Practice. “We knew that Heather and the practice have a strong appetite for passive house. There was no sales [effort] required,” he said.
-
The existing bungalow on site which was demolished The existing bungalow on site which was demolished
-
Bolted flitch plate at glulam roof beam and post connection Bolted flitch plate at glulam roof beam and post connection
-
Stainless steel ductwork for the MVHR system Stainless steel ductwork for the MVHR system
-
Fronta WA breather membrane protects the frame, with battens and counterbattens awaiting cladding Fronta WA breather membrane protects the frame, with battens and counterbattens awaiting cladding
-
The existing bungalow on site which was demolished The existing bungalow on site which was demolished
-
Site cleared in preparation for the new build Site cleared in preparation for the new build
-
Ground floor build-up features a passive house certified Isoquick insulated raft foundation system Ground floor build-up features a passive house certified Isoquick insulated raft foundation system
-
Ground floor build-up features a passive house certified Isoquick insulated raft foundation system Ground floor build-up features a passive house certified Isoquick insulated raft foundation system
-
Ground floor build-up features a passive house certified Isoquick insulated raft foundation system Ground floor build-up features a passive house certified Isoquick insulated raft foundation system
-
Erection of the timber frame structure which was prefabricated offsite by passive house stalwarts PYC Erection of the timber frame structure which was prefabricated offsite by passive house stalwarts PYC
-
Timber frame walls with Smartply Airtight OSB airtight layer Timber frame walls with Smartply Airtight OSB airtight layer
-
Timber frame walls with Smartply Airtight OSB airtight layer Timber frame walls with Smartply Airtight OSB airtight layer
https://passivehouseplus.ie/magazine/new-build/ace-of-herts#sigProIdf4ab187a6c
Nonetheless, the project was breaking new ground for AD Practice, which hitherto had concentrated its efforts on retrofits.
“This was our first new build passive, because we started the hard way with retrofits, and it was the only one that has got more than one unit,” McNeill said.
The three cellulose-insulated timber frame buildings were prefabricated offsite by passive house stalwarts PYC in Welshpool, and sit on an Isoquick insulated foundation system.
The right mortgage provider will give a 1.5 per cent discount. Will the market respond to that? I think it will.
Planning, often contentious in the south of England, was a challenge as the modern, timber-clad houses sit in counterpoint to the nearby bungalows and traditional houses in the leafy locale.
Two of the houses have their bedrooms on the ground floor, responding to the site. “It’s a very wooded site. The fact that the two houses are ‘upside-down’ was done to make the most of the view, and it was also a case of [avoiding] overlooking with neighbours,” McNeill said.
However, AD Practice was able to design dwellings that offer significant architectural interest and also respond to a common problem with British houses: a lack of light inside. “Obviously, they do look very different, but they're not really on a street view, so that did give us a possibility to do things that are a little different. They’re obviously highly glazed,” McNeill said.
This article was originally published in issue 47 of Passive House Plus magazine. Want immediate access to all back issues and exclusive extra content? Click here to subscribe for as little as €15, or click here to receive the next issue free of charge
This touches on a common misconception about passive houses: that they must have small windows. In fact, the houses at Haven Place deliver more light than is traditional across the UK’s housing stock.
“They do follow the traditional north side having very few openings, but we were concerned with getting natural light, and ventilation in during the summer.”
“From our point of view, if you were to take a site and design a traditional passive house, it probably wouldn't look like these. The forms didn’t lend themselves to it, but it had an architectural vision. It shows what can be done with some effort,” she said.
Green financing
A notable part of the plan for 1-3 Haven Place was to prove that energy-efficient houses made economic sense, both in terms of energy saving and also financing.
Indeed, the UK government has been encouraging mortgage lenders to develop green mortgage products since publishing its Clean Growth Strategy in 2017.
Fisher said that getting developers, and planners, to recognise this was important as he felt homebuyers would clearly see the benefit.
Ecology Building Society, the development mortgage provider on the build, provided a discount based on the building’s planned performance, something Fisher said was worth noting and could have a positive impact on developments by supporting a drive to aim higher when it comes to sustainability.
“The right mortgage provider will give a 1.5 per cent discount. Will the market respond to that? I think it will,” he said.
Other factors changed the calculations slightly, but not disastrously, and they were felt universally across the industry, such as material cost increases due to the perfect storm caused by Covid, Brexit and Russia’s invasion of Ukraine.
“We got hit by the supply chain crunch and cost rises. We have cedar cladding [for example],” he said.
The development stays true to the original principles of passive house, in that it really does rely almost entirely on internal gains from appliance use, optimised passive solar gains, high quality heat recovery ventilation, and high performance fabric, rather than on hydronic heating.
And as the scheme nears completion, there are already signs that the strategy is working. Across a warm weekend at the end of March, Fisher noted the temperatures throughout the day were hovering around 16 C - before the electrical connections had been turned on, and therefore without the benefit of any internal gains “from anything basically”, and with no heat recovery ventilation.
Two direct electric radiators - described by Fisher as “belt and braces” have been provided for each house to boost temperatures as a last resort, but these are expected to be ornamental. An electric towel rail has been fitted in all bathrooms – in recognition of the fact that people tend to look for higher temperatures when coming out of showers or baths. Fisher may add post heaters to the ventilation system if the houses require it in reality.
Although the development is small compared to those of the mainstream UK homebuilders, Fisher says 1-3 Haven Place has the potential to act as a harbinger of how to build better. Noting the International Capital Market Association’s Green Bond Principles – which include passive house among the benchmarks for green building – he says there is no reason to think energy-efficient buildings will be difficult to finance.
The industry realising this, he says, would transform the country’s housing landscape. “When you watch Grand Designs or George Clarke, all the people who do passive houses are self-builders. We don’t see many passive houses for sale. I felt I had to do my bit to change that,” he said.
“We have houses here that are meeting the UK’s future housing needs.”
Selected project details
Client: Surreal Estate Developments
Architect: AD Practice
Mechanical/electrical engineer: 21° (formerly known as Green Building Store)
Structural engineer: PYC
Energy consultant: Ashby Energy Assessors
Project management: Surreal Estate Developments
Main contractor: Surreal Estate Developments
MVHR system: Ubbink
MVHR contractor: Apex Ventilations
Airtightness testing: Ashby Energy Assessors
Passive house certifier: Mead Consulting
Build system,wall, roof and floor insulation: PYC
Insulated foundation system: Isoquick, via Build Homes Better
Building boards: Medite Smartply
Windows and doors: 21° (formerly known as Green Building Store)
Cladding: Millworks
External slab screed: Base Concrete
PV/heat pump: Solinvictus
Marking quality and sustainability
Developer James Fisher, whose day job is the head of strategic relationships at the Building Research Establishment (BRE), stressed that the project was independent of the company. However, there is an interesting overlap, as Fisher is putting the development through the BRE’s Home Quality Mark (HQM) certification process.
Rooted in BRE’s BREEAM standard for sustainable construction of commercial and industrial standards, HQM was introduced in 2015.
However, BRE has a history of offering sustainability certification in the residential sector. Immediately predating HQM was the UK’s Code for Sustainable Homes voluntary standard, which was developed with input from BRE, implemented by the British government in 2007 and withdrawn in 2015, when some aspects were folded into Building Standards. Prior to the code, BRE’s EcoHomes rating scheme performed a similar function from 2000 to 2007.
Jennifer Dudley, product manager for residential housing at BRE, said that HQM’s foundation in BREEAM means that it is rooted in science, but the two standards differ as HQM reflects the specificities not only of residential construction, but of how people live in homes.
“It’s designed to be a holistic view of sustainability, but with the homeowner and improving the home for the occupant at its core. At its heart it's a BREEAM scheme; it’s built on the same 30 years of history and science as the BREEAM,” she said.
Homes rated under HQM are independently evaluated by a BRE-licensed assessor who analyses a dwelling’s overall running costs, the impact on the occupant’s health and wellbeing, the home’s environmental footprint, its resilience to flooding and overheating, and transport links.
“Broadly, one of things that HQM does that is different is we looked at the change in the sector over the last decade, [and so we decided] to look at the quality of the process, so it looks at things like handover and aftercare. “We have a number of minimum requirements to meet any level of stars across HQM, so there is an entry level, and we have what you might call the menu of credits above that,” Dudley said.
Internally within HQM, a certain amount of tradability is allowed, meaning buildings do not have to score highly in every area in order to be certified. However, Dudley said the standard has measures in place to ensure that buildings are not given overly optimistic ratings, for instance with mediocre fabric offset by large renewable energy systems. “Another difference is we introduced indicators: every home gets a triple bottom line indication and there are backstops within those, meaning you have to achieve some credits in each area,” she said.
As noted in BRE’s HQM Technical Manual, backstop indicators seek to ensure that “key issues (specific to that indicator) are not overlooked when targeting a high score [...] For example, to achieve a score of three in the 'wellbeing' indicator, a home must achieve three credits in the 'daylight' issue.”
BRE says that HQM includes measurement of embodied carbon as part of a wide-ranging assessment of the environmental impact of construction materials. This measures impact compared to benchmark values in Ecopoints. However, this means that although carbon impacts are measured, they cannot easily be reported.
Dudley acknowledges this, but says carbon is considered and further developments in HQM will address it more directly. For example, with version 7, BRE wants to move away from Ecopoints and explicitly measure embodied carbon impacts and introduce additional carbon reporting functionality that covers both embodied carbon and operational carbon emissions from energy water and refrigerant gases.
“We have an energy category for operational [energy use], we have a materials category, [and] we have things like pollution and water, things that relate to carbon. We measure and analyse each separately, but don't report it yet,” she said.
“It currently outputs an Ecopoint and doesn't translate hugely well into how industry talks about carbon,” she said. This will change as HQM adapts to version 7 of BREEAM, which is expected to be published later this year and integrated into HQM after that: “We’re looking to shift that for version 7, which is to draw out these things and standardise the metrics, including embodied carbon,” Dudley said.
Version 7 is also intended to bring deeper integration with the EU taxonomy for sustainable activities, with BRE noting that customers have, despite the UK’s exit from the bloc, recognised the benefit of aligning to the taxonomy. In addition, Dudley said, stakeholders beyond developers and homeowners have expressed interest in HQM, notably investors seeking better environmental, social and governance (ESG) and socially responsible investing (SRI) rankings.
In the meantime, Dudley says BRE sees HQM as a rating that will be easy for buyers to understand but also rooted in rigorous standards and real, scientific testing. “The independent, third-party element of the certification is important. It's not self-claimed.
“BREEAM recognises performance that goes beyond legislation. By recognising current best practice and outstanding performance levels. So BREEAM moves forward in line with legislation and best practice,” she said.
In detail
Development type: Three detached, offsite timber frame homes
Dwelling 1: 287 m2, three-storey
Dwelling 2: 281 m2, three-storey
Dwelling 3: 157 m2, two-storey
Site type & location: Brownfield site (demolition of existing bungalow), semi-rural location, just outside St. Albans in Hertfordshire
Completion date: Expected April 2024
Budget: £3,000/m2 including professional fees but excluding land purchase
Passive house certification: Passive House Plus certification pending across all three units
Space heating demand (PHPP): 13 kWh/m2/ yr (unit 1), 12 kWh/m2/yr (unit 2) and 15 kWh/m2/ yr (unit 3)
Heat load (PHPP): 11 W/m2 (unit 1), 10 W/m2 (unit 2) and 11 W/m2 (unit 3)
Primary energy non-renewable (PHPP): 102 kWh/m2/yr (unit 1), 94 kWh/m2/yr (unit 2) and 136 kWh/m2/yr (unit 3). Primary energy renewable (PHPP): 72 kWh/m2/ yr (unit 1), 76 kWh/m2/yr (unit 2) and 106 kWh/m2/ yr (unit 3)
Heat loss form factor (PHPP): 2.99 (unit 1), 3.02 (unit 2) and 3.51 (unit 3)
Overheating (PHPP, calculated percentage of year above 25 C): 6 per cent (unit 1), 7 per cent (unit 2) and 8 per cent (unit 3)
Assumed occupancy: 2 adults & 2 children for each dwelling
Environmental assessment method: BRE’s Home Quality Mark 4 stars targeted across all three units. Result pending
Airtightness (At 50 Pascals): Interim results after second test. Final results & test pending. 0.28 ACH (unit 1), 0.23 ACH (unit 2) and 0.34 ACH (unit 3)
Energy Performance Certificate (EPC): Results will be confirmed after final set of airtightness tests. 107 A (unit 1), 111 A (unit 2) and 120 A (unit 3)
Embodied carbon: No assessment has been completed
Measured energy consumption: Properties not yet occupied
Thermal bridging: The PYC engineered I-beam has solid ‘flanges’ on both sides which are connected by an 8 mm web of OSB, which, being so narrow reduces thermal bridging to extremely low levels. The complex shape of the I-beam is easily filled with pressure injected Warmcel insulation to the required high densities maintaining insulation continuity. Y-factors (from SAP) calculated for each home, at 0.0276 W/m2K (dwelling 1), 0.0274 W/m2K (dwelling 2) and 0.031 W/m2K (dwelling 3)
Estimated energy bills: All houses estimated to be generating net profits on energy costs, considering bills versus feed in tariff payments. Costs calculated from SAP 2012 worksheet. Inclusive of all heating & hot water costs but exclusive of standing charges
Dwelling 1: -£371.05
Dwelling 2: -£604.32
Dwelling 3: -£670.04
Ground floor: The Passive House Institute certified Isoquick insulated raft foundation system from Build Homes Better has been used on all plots and has been designed for a 250 mm reinforced concrete slab, using the EM10 edge profile. Units 1 and 2 had 250 mm EPS, and a U-value of 0.11 W/m2K, while unit 3 had 300 mm of EPS, and a U-value of 0.09 W/m2K. The floor system is PHI certified
Walls (across all three dwellings): 45 mm service void; 12.5 mm Smartply Airtight OSB board; 300 mm I-beam fully filled with Warmcel cellulose fibre insulation; 12 mm Medite Vent breathable sheathing board; Proclima Fronta WA breather membrane. U-Value 0.125 W/m2K
Roofs (across all three dwellings): 45 mm service void; 12.5 mm Smartply airtight OSB board; 300 mm I-beam fully filled with Warmcel cellulose fibre insulation; 12 mm Medite Vent breathable sheathing board; Proclima Solitex Plus breather membrane. U-Value 0.126 W/m2K
Windows and external doors: timber framed Ultra (now GBS98) triple glazed windows with a U-value of 0.75 W/m2K. Ultra (now GBS98) timber triple glazed doors or insulated panel doors with a typical U-value between 0.71-0.79 W/m2K
Roof windows: The clerestory roof windows are Velux GGU solar passive house roof windows with a U-Value of 0.51 W/m2K. These are triple & double glazed units that are also fitted with automatic opening mechanisms
Heating and hot water systems: LG Therma V 5 kW heat pump to provide hot water only, as there is next to no space heating system demand requirement. As a backup, a pair of 2 kW direct electric panel heaters are provided in each house - one in the kitchen area and one on a landing. Electric towel rails have also been provided in bathrooms
R32 refrigerant, monobloc units connected to 300 litre World Heat/Therma V hot water cylinders. MCS certified SCOP 3.1 at 55 C flow temp (KIWA 00033/056 HP). 3 kW immersion for weekly legionella cycle. Supplied by Solinvictus
Ventilation system: PHI-certified heat recovery ventilation systems in each case. Ubbink Ubiflux Vigor 400 (in units 1 and 2), with 89 per cent heat recovery, 228 m3/hr. @ 39 Pa (average of two fans); Ubbink Ubiflux Vigor 325 (in unit 3), 91 per cent heat recovery, 186 m3/hr. @ 33 Pa (average of two fans)
Water: Low flush volume WCs have been specified throughout
Photovoltaic systems: Solinvictus supplied in-roof PV arrays linked to SMA hybrid inverters with BYD battery storage systems to provide electricity for each house. 10 kW SMA Smart Energy three phase inverter with 10.2 kWh BYD battery in each house. Units 1 and 2 each feature a 16.56 kWp array with 36 JA Solar 460 W panels, with expected yearly generation of 10,383 kWh and 10,632 kWh respectively, and average shading factors of 1.0 and 0.9, respectively. Unit 3 has a 11.96 kWp array with 26 JA Solar 460 W panels, an expected yearly generation of 9,759 kWh, and an average shading factor of 1.0. MCS standard estimation method used for generation figures
Sustainable materials: Focus areas include material sourcing, sustainable timber & environmentally friendly surface coatings