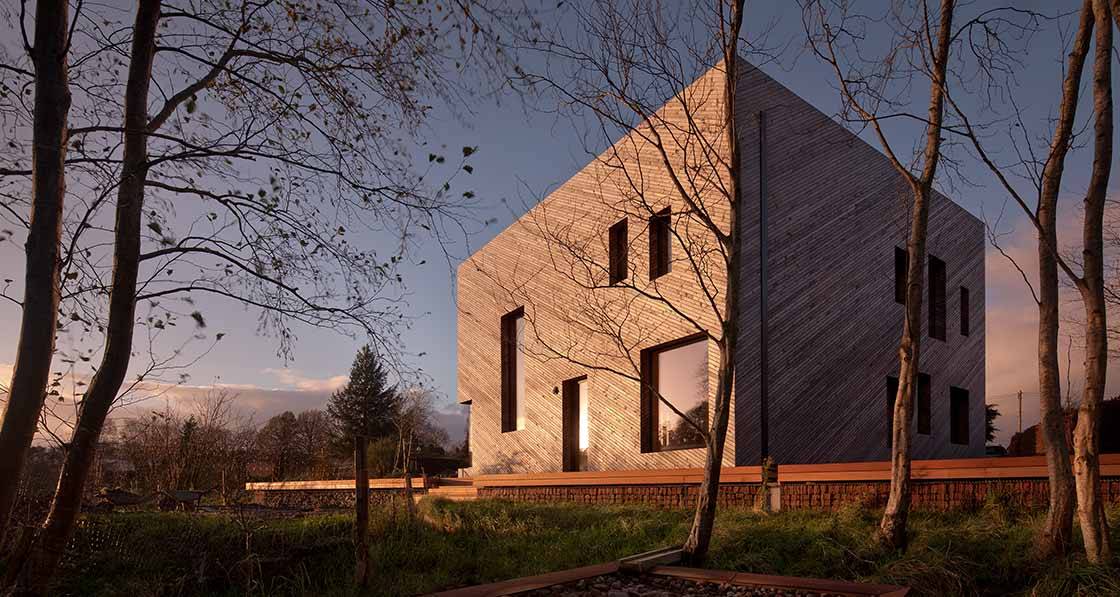
- New build
- Posted
Boxing clever
This all-wood passive-certified home in the village of Kippen was built directly by its architect owners, who not only achieved the passive house standard but did so with an ecological approach that sought to use building materials ultra-efficiently and make it easy to deconstruct and recycle the building at the end of its life.
Click here for project specs and suppliers
Building: 170 m2 detached home and office
Build method: Stick-built timber frame
Site & location: Village site, Kippen, Scotland
Standard: Passive house classic certified
Budget: £250,000 (build costs)
ENERGY BILLS £20 PER MONTH FOR SPACE HEATING ONLY, EXCLUSIVE OF CHARGES
The term ‘self-build’ can be a little vague these days — even meaningless — when you can class as a self-builder anyone who plays some sort of significant role in the construction of their new build home.
As a self-builder you might have a lot to do with the day-to-day aspects of the project either by getting stuck in or project-managing the work yourself, but you can also have very little to do with it by farming out all the work to the professionals.
Mhairi Grant and Martin McCrae certainly rolled up their sleeves when it came to building Ostro, a hugely striking two-storey, detached timber framed and clad passive house located near Stirling, Scotland. In fact, the sheer amount of work that they did themselves makes this a self-build in the truest sense of the word.
This includes building the timber frame (stick-built, no kit or panel system), installing all of the ground floor and wall insulation, applying all the airtightness products, doing all the plumbing and general joinery, laying the floors, fitting all the plasterboard and other internal linings, the kitchen and bathroom fittings and tilings, and all the decorating.
They also did the external drainage for the ground floor slab, the external timber cladding, all the external landscaping and the sedum roof covering.
This article was originally published in issue 37 of Passive House Plus magazine. Want immediate access to all back issues and exclusive extra content? Click here to subscribe for as little as €10, or click here to receive the next issue free of charge
So what did they not do? They didn’t do the site excavation and preparation, the pouring of the slab, the fitting of the windows, the roof insulation and waterproofing, the wall-plastering, the specialist interior carpentry, the electrical work and the installation of the solar PV and solar thermal systems.
The result of their highly resourceful endeavours – all on a budget of £250,000 – is a very distinctive, box-shaped certified passive house with lots of hallmarks of Scandinavian architecture in its use of natural timber cladding, unfussy details and a clear, simple shape.
It’s no surprise to learn that the couple run an architectural and design company – Paper Igloo – that now specialises in sustainable and passive house projects, and designed Ostro between themselves. But the fact that it took some six years from start to finish doesn’t diminish the scale of their self-building triumph, particularly when you learn what their primary motivation was.
“It was due to a combination of three things,” says Mhairi. “We wanted, and needed, to keep the costs down as we wanted to be mortgage free. Like most people who are either self-employed or have a small one or two-person company, our monthly income is variable, which makes large fixed costs such as a mortgage very difficult and stressful to manage.
“Secondly, we enjoy the hands-on aspect of building as a contrast to our daily design work, which involves time spent mostly on a computer. And finally we also wanted to learn more about the passive house aspects of house building that would let us be more informed when designing them for other people in the future.”
Before moving to the semi-rural conservation village of Kippen, near Stirling, the couple lived in a nice old tenement flat in Glasgow that they had renovated themselves but in which they struggled to get the room temperature above 14C in winter. They were considering renovating another flat when Mhairi attended a half-day course in passive design, “which I thought was incredible – I couldn’t understand why all new buildings weren’t built to this standard”. She then qualified as a passive house designer.
They searched for a suitable plot for a few years before finding one in Kippen and broke ground in 2014 — though not before talking to loads of people and driving all the way down to Totnes in Devon to stay in Adam Dadeby’s passive house B&B to experience the reality of heat recovery ventilation.
“So we stayed overnight, I remember the first thing we did when we went into the room, we were trying to find the valve to put our hands up to it, to see if there’s a draft and to listen to it and that kind of thing,” recalls Mhairi. So as well as talking to other architects, “you want to know that the physical reality of it is going to live up to the science, and that it’s actually going to be as comfortable”.
At the start of the project, it helped that the couple had a bit more free time on their hands, and they did the most work in the first two years. This included Martin taking 12 weeks off at one stage to build the timber frame with two joiners. They estimate that this alone saved them tens of thousands on the build, but another factor in that decision was that they couldn’t find carpenters at the time who would do an I-Joist wall or twin frame to enable thermal breaks, never mind factory-built timber panels.
Martin did the timber frame, while Mhairi did the plumbing and tiling.
“Six years ago there was hardly anyone,” says Martin. “We couldn’t find anyone to be able to build a passive house frame, whereas now we’ve worked with Eden Insulation and other companies quite a lot and they’ll do something for you. So what we built in that time, they will build you on site in four days.”
The couple were able to cover-off a number of jobs individually. For instance, Martin did the aforementioned timber frame, while Mhairi did all the plumbing and tiling, but they worked together on jobs for the most part.
“When it came to things like plasterboard and insulation fixing, and so on, we just did that together because a lot of jobs require two people for manoeuvring materials, all that kind of thing,” Martin says.
After the first couple of years, the couple spent another four long summers on the distinctive timber cladding. “That was really what we did for four years, which seems incredible when you look back now,” recalls Mhairi. “But it didn’t really occur to me until our neighbour said last year after we had finished, ‘You’ll be so looking forward to summer this year because you won’t have to clad anything. And I thought, ‘Oh yeah, it’ll be really nice’.”
Martin admits that, aside from them being busier at work by that stage, one of the reasons the cladding took four long years was the decision to mount it diagonally, which is much trickier than placing it horizontally or vertically. The cladding is mounted on vertical battens but “when you get to a small triangle at the corner of the wall, there’s nothing to support it. So I had to prefabricate triangles with stainless steel straps screwed on and then offer it up as a unit. It was a tiny little thing, but time consuming.”
-
Self-builders Martin and Mhairi, together with their friend, architect Eamon McGarrigle (centre), installing the Isoquick EPS insulated formwork system Self-builders Martin and Mhairi, together with their friend, architect Eamon McGarrigle (centre), installing the Isoquick EPS insulated formwork system
-
Airtightness taping around wire penetrations Airtightness taping around wire penetrations
-
Continuous external wrap of 100 mm thick wood fibre insulation boards Continuous external wrap of 100 mm thick wood fibre insulation boards
-
Airtightness detailing around windows Airtightness detailing around windows
-
The 300 mm reinforced concrete slab was power floated to form floor finish throughout ground floor The 300 mm reinforced concrete slab was power floated to form floor finish throughout ground floor
-
Erection underway of the stick-built timber frame walls Erection underway of the stick-built timber frame walls
-
The walls were built with a doublestud timber frame, with wood fibre insulation to both studs, and a further 60 mm in between the studs to form a thermal break. The walls were built with a doublestud timber frame, with wood fibre insulation to both studs, and a further 60 mm in between the studs to form a thermal break.
-
The walls were built with a doublestud timber frame, with wood fibre insulation to both studs, and a further 60 mm in between the studs to form a thermal break. The walls were built with a doublestud timber frame, with wood fibre insulation to both studs, and a further 60 mm in between the studs to form a thermal break.
-
The walls were built with a doublestud timber frame, with wood fibre insulation to both studs, and a further 60 mm in between the studs to form a thermal break. The walls were built with a doublestud timber frame, with wood fibre insulation to both studs, and a further 60 mm in between the studs to form a thermal break.
-
Wood fibre insulation to the inner studs Wood fibre insulation to the inner studs
-
Pro clima Intello Plus vapour control membrane to ceiling Pro clima Intello Plus vapour control membrane to ceiling
-
Spano Durelis Vapourblock airtight vapour control board to walls Spano Durelis Vapourblock airtight vapour control board to walls
https://passivehouseplus.ie/magazine/new-build/boxing-clever?highlight=WyJ3ZWxscyIsIndlbGwiLCJ3ZWxsZSIsIndlbGxuZXNzIiwid2VsbGluZyIsIid3ZWxsIiwid2VsbCciLCJ3YXRlciIsIndhdGVycyIsIndhdGVyJ3MiLCJ3YXRlcmluZyIsIndhdGVyZWQiLCJiaWxsIiwiYmlsbHMiLCJiaWxsaW5nIiwiYmlsbGVkIiwiYmlsbCdzIiwiYmlsbCciLCJiaWxsaW5ncyIsImJ5IiwiYmlsbCBieSJd#sigProId6b471d9c52
He did ask a builder to quote to finish the job at one stage, but the builder wouldn’t do it. Part of the problem with living in central Scotland compared to somewhere like London, he says, is that finding a contractor interested in executing finer detail work is far harder.
The couple had sold their Glasgow flat much quicker than they anticipated and rented various flats in Kippen for a couple of years before moving into a caravan next to the site for nine months as the build progressed.
During one miserable winter spent in the caravan (which had to double as their office) they discovered that not only was their mattress going mouldy, but they received a £2,000 top-up electricity bill for the four-bar electric heater that was running almost permanently. So they decided to move into their unfinished but weather-proofed, warm and dry building next door in 2016 and essentially camp in it.
They plaster-boarded one room and not long after got the kitchen fitted.
One useful reference for the couple was the book Details for Passive Houses published by IBO, the Austrian Institute for Healthy and Ecological Building. Although most of the tips were more relevant to masonry construction with external insulation, “it did open my eyes to perimeter insulation and how you might achieve continuity at certain junctions,” says Mhairi.
They must also have been taking careful notes regarding airtightness given the impressive score the house achieved of 0.19 air changes per hour. This did prove among the biggest challenges of the build, however, particularly the job of incorporating the membrane during the timber frame construction.
“We were really pleased… that was quite a nice moment,” says Mhairi.
Mhairi praises Niall Crossan and his team at Ecological Building Systems for the tips and advice that they received while doing one of the company’s workshops in Athboy, Co Meath.
“They’re so interested in promoting better buildings and better construction, and so we found them really helpful for things like that.”
The couple were keen from the beginning to use as many natural materials as possible, starting with the PEFC/FSC-sourced, untreated timber frame and cladding but also wood-fibre insulation which, Mhairi notes, “is much more pleasant to work with than phenolic insulation or mineral wool and creates, in conjunction with the other wall products, a vapour open construction.”
The flat roof has a sedum covering for biodiversity and water-saving. Mhairi and Martin also salvaged materials from other sites for landscaping, and kept a tight control on construction waste, so much so that no skips were required during the build.
With the projected energy use of their home based on PHPP (Passive House Planning Package) calculations, the couple felt confident enough that the heating demand could be met by something really simple and modest.
So instead of a heat pump, they opted for infra-red heating panels (all individually thermostatically controlled) with a back-up post heater in the ventilation supply ducts, while most hot water is provided by good old-fashioned evacuated tube panels.
“It still amazes us how much solar input we get from the evacuated tube panels, says Mhairi. “They are quite aggressive, even in the shoulder seasons. We are often surprised how much dedicated solar thermal seems to be overlooked in Scotland as a viable renewable technology, with many people preferring to use PV [for electricity]. For a house such as ours with only a small PV array, no heat pump and no battery, solar thermal still makes a lot of sense for hot water demand.”
As well as monitoring electricity consumption, which has been in line with their projections, they have also installed temperature and humidity sensors in various places to validate what they are feeling in their bones as they occupy the space.
“We have found that the temperature, as you might expect, is extremely stable – hovering around the 20 C mark internally. We have had some days down to about -4.4 C externally recently. What has surprised us is that we thought there would be more variation and stratification at the top of the double height, however this is also quite stable within a range of a couple of degrees.”
Indeed, Mhairi comically notes that when they lived in their old flat, she found herself wearing bed socks most nights, and extra jumpers for “when the boiler goes off at 10 o’clock at night”. And that now they often have to physically open the door to figure out how cold it is outside, and whether they need hats and gloves.
The couple have no regrets about all the specification decisions they made over the course of the six-year build. But Martin admits that one thing they might change if they had the chance to turn back time is to go for a mono- pitched roof so that they could mount more PV panels and qualify as a passive house ‘plus’ and therefore charge, for practically nothing, the electric car they are planning to buy.
While they weren’t able to find contractors willing to do things like the cladding or any other complicated or detailed work, they did manage to find a cabinet maker who made their beautiful staircase and a rather neat drinks cabinet with a very slick opening mechanism.
“That was quite a nice little moment in the project where, for what felt like the first time ever in our lives, we actually commissioned someone to do this,” says Mhairi. “It was so interesting to be the client and very pleasurable after spending about five years slogging it out.”
Selected project details
Clients: Martin McCrae & Mhairi McCrae (nee Grant)
Architect: Paper Igloo
Structural engineer: Clyde Design Partnership
Energy consultant: Paper Igloo
Passive house certification: Etude
Main contractor: Client self-build
Electrical testing: Knowire Ltd
Airtightness testing: Stuart King Architecture & Design
Timber supply (for stick-built frame): Rowan Timber Supplies
Wood fibre insulation: Gutex, via Ecological Building Systems
Additional wood fibre insulation: Steico, via Passivhaus Store
Green roof system: Bauder
Additional roof insulation: Knauf
Airtightness products: pro clima, via Ecological Building Systems
Windows & doors: Unilux
Roof windows: Lamilux
Larch cladding: Rowan Timber Supplies
Internal wall board: Fermacell, via SIG
Linoleum flooring: Forbo
Self-build insurance: Titan Insurance Services
Space heating: Yandiya IR panels, via Edensprite
MVHR: Paul Heat Recovery Scotland
Wastewater heat recovery: Recoup
Lighting controls: Schneider Electric
Heating controls: Salus & Nest
Water-saving fittings: Crosswater
Bathroom fittings: Martin Craig Bathroom Design Studio
Designing for deconstruction & embodied carbon
Words by Mhairi Grant (architect, builder and client)
One of our ambitions for the design of Ostro was to create a dwelling with low environmental impact. While embodied carbon wasn’t a direct consideration, it is interesting to realise retrospectively that a number of our ecologically driven decisions resonate well with a low embodied carbon approach.
We gave a lot of consideration to our construction method and the materials used to create the building, such as our choice of timber frame, wood-fibre insulation and untreated timber cladding. Our aim was one of reduction – to make all of the layers within the construction work as hard as they could and ideally perform more than one function so as to reduce the overall quantity of materials required.
One example of this approach would be the ground floor construction: we dispensed with a floor covering on the ground floor, which might typically have included an additional screed with a timber, tile or carpet floor finish, and instead exposed our power floated structural slab throughout.
The choice of a twin-wall timber frame with loose-batt wood-fibre insulation was a consequence of two decisions. Our aim of achieving sustainability gold level in the Scottish government’s technical standards meant we had to pay attention to the Scottish Ecological Design Association’s guide to designing for deconstruction.
We wanted to use an insulation material that could be readily separated from the structural frame at some point in the future should the building ever need to be deconstructed. This approach allows either component to be replaced without destroying the other, and therefore each can potentially be re-used or recycled.
Secondly, we wanted to work with a material that was non-toxic, formed from a by-product, and relatively dense to better the decrement delay of the building fabric.
When we were considering the outer skin of the building, our selection of untreated timber cladding boards stemmed from a desire to use a durable, long lived and low maintenance material, and importantly, one which we could apply ourselves without specialist training.
As the years have passed we have become more aware of the environmental importance of reducing embodied carbon within our designs, and so we recently decided to engage Tim Martel of PHribbon to undertake an embodied carbon calculation on our completed building (see graph).
We found the outcomes really interesting: in particular a comparison of our chosen construction method with a more common form of construction, such as cavity wall. Another point of note was the RICS assumption regarding current practice of incineration of post-construction timber in the UK. This has opened our eyes to the impact that incorporating a more circular approach to construction could have on the industry as a whole.
In detail
Building type: 170 m2 (treated floor area) detached two-storey timber frame house.
Location: Kippen, Stirlingshire, Scotland
Completion date: January 2020
Budget: Approx £250,000. Includes professional fees & VAT where applicable. Does not include significant labour cost due to self-build nature of project.
Passive house certification: Passive house classic certified
Space heating demand (PHPP): 15 kWh/m2/yr
Heat load (PHPP): 11 W/m2
Primary energy renewable (PHPP): 37 kWh/m2/yr
Primary energy non-renewable (PHPP): 79 kWh/m2/yr
Heat loss form factor (PHPP): 3.48
Overheating (PHPP): 4 per cent of year above 25 C
Number of occupants: 3 (from PHPP)
Environmental assessment method: Section 7: Sustainability ‘gold’ Level; assessment method as per Scottish Technical Standards
Airtightness (at 50 Pascals): 0.19 air changes per hour
Energy performance certificate (EPC): A 94
Measured energy consumption: 6,392 kWh or 37.59 kWh/m2/yr measured annual energy consumption (October 2019 to October 2020) based on electricity meter readings.
Thermal bridging: Continuous external wrap of 100 mm thick Gutex woodfibre insulation, external and internal window / door reveals insulated, thermally broken window frames, continuity of wall-to-ground insulation, continuity of wall-to-roof insulation, SVP insulated. All junctions were numerically analysed in PSI Therm software and calculated thermal bridge values entered into PHPP.
Energy bills (measured or estimated): Based on projected figures for final energy demand (delivered energy) for space heating in PHPP, uSwitch.com suggests an annual space heating bill of £239.70, or £19.98 per month, using the cheapest tariff available of 17.967p per kWh. This is exclusive of VAT and standing charges, which increase the total to £351.72 annually, or £29.30 per month.
Ground floor: Minimum 600 mm compacted Type 1 sub-base laid in 150 mm deep layers, followed above by 50 mm cleaned and compacted stone blinding, 300 mm thick Isoquick EPS insulated formwork system, 1200 gauge Visqueen ‘Ecomembrane’ DPM (100% recycled polyethylene), 300 mm reinforced concrete slab power floated to form floor finish throughout ground floor. U-Value: 0.122W/m2K.
Walls: Stick-built on site twin-wall timber frame with 20 mm thick Siberian larch cladding (untreated & unfinished) externally, followed inside by 45 x 50 mm deep treated timber vertical battens forming drained and ventilated cavity, 100 mm thick Gutex Multitherm tongue and groove wood fibre insulation boards, 12 mm thick Spano Durelis Populair vapour diffuse racking board, 45 x 95 mm deep vertical timber studs with 100 mm compressed Gutex Thermoflex flexible wood fibre insulation in between, 60 mm continuous layer of Gutex Thermoflex flexible wood fibre insulation forming thermal break, 45 x 145 mm deep vertical timber studs with 160 mm compressed Gutex Thermoflex flexible wood fibre insulation between (9 mm thick plywood gussets holding two timber leafs together), 12 mm thick Spano Durelis Vapourblock airtight vapour control board, joints and all screw holes taped with Pro Clima Tescon Vana tape, 45 x 45 mm timber battens forming service cavity, and 12.5 mm plasterboard internally. Note: in double height areas construction matches above except for the inner stud is 245 mm deep and filled with 260 mm compressed insulation. Average U-values: 0.1 W/m2K for 145 mm stud walls & 0.086 W/m2K for 245 mm stud walls.
Roof: Flat roof with 1° fall finished with Bauder XF301 extensive sedum blanket on Bauder SDF drainage mat, followed beneath by Bauder Plant-E felt capping sheet, on Bauder KSA-Duo felt underlayer, on 120 mm Bauder PIR insulation, on 140 mm Bauder PIR FA-TE insulation, on Bauder DS1-Duo torch-applied vapour barrier, on 18 mm plywood, on min. 25 mm deep x 45 mm wide firring battens to create 1 degree fall fully filled with Knauf Eko Roll mineral wool insulation, on 18 mm plywood deck, on 300 mm deep JJI 300B+ I-Joists to form roof structure with static airspace between, on pro clima Intello Plus AVCL to ceiling, with 15 mm TE Wallboard plasterboard to form ceiling. U-Value: 0.072 W/m2K. Roof has fully insulated parapet to perimeter finished in matching felt Bauder waterproofing system.
Windows & external doors: Unilux triple glazed aluminium-clad thermally broken timber frame windows, with argon gas filling. Overall whole-window average U-Value for the project of 0.82 W/m2K.
Roof windows: Lamilux CI System Glass Element F Energysave triple glazed aluminium clad thermally broken rooflights pre-installed to proprietary insulated upstands for flat roofs. Passive House Institute certified (phA component). One of the two units is Passive House Institute certified (the other, which provides roof access, is not). Average U-Value: 0.96 W/m2K.
Space heating: Direct electric heating provided by 3 x 800 W and 1 x 500 W infrared heating panels, spread throughout ground floor, all thermostatically controlled using Salus controls. Backup 2 kW post heater on MVHR system thermostatically controlled using Nest thermostat on first floor.
Hot Water: 4 m2 Solfex CPC 12 OEM evacuated tube solar thermal panels on ballasted frame on flat roof connected to 300 litre Gledhill solar hot water cylinder with back up 3 kW electric immersion heater.
Ventilation: Paul Novus 300 heat recovery ventilation system; certified efficiency in this dwelling of 91.2% (PHPP). Supply ducts insulated due to installation of post heater.
Water: Recoup Pipe +HE waste water heat recovery unit to master bedroom shower. 54% dynamic efficiency of system calculated in PHPP. Low flow fixtures and fittings throughout in accordance with section seven of the Scottish building standards technical handbook (sustainability water use efficiency). Sedum roof attenuates approximately 40 per cent of rainfall to roof with remainder carried to purpose-built raingarden with final discharge to burn on site.
Electricity: 9.9 m2 Solarworld solar photovoltaic array (6 x 250 W panels) on ballasted frame on flat roof with total installed capacity of 1.5 kW.
Green materials: All timber from PEFC / FSC-certified sources, untreated timber cladding and decking, sedum roof covering for biodiversity & water saving, wood fibre insulation throughout all walls (including internal partitions), recycled damp proof membrane, Fermacell board throughout internal partitions and ground floor ceilings, Marloleum & reclaimed parquet flooring for upper floor coverings.
Landscaping: recycled slate salvaged from neighbour’s build chipped on site for landscaping, stones from excavations on site utilised in landscaping, salvaged local sandstone from architect’s other projects used in landscaping to create rockery / feature borders, upcycled brick from previous veterinary surgery on site used upcycled to create gabion retaining wall and seating.
Green measures: Waste tightly controlled during construction: no soil / excavated material taken off site, no skips used for duration of build. All packaging recycled, all waste non-treated timber provided to family member for use as fuel. Design for future deconstruction.
Embodied carbon explained
Words by Jeff Colley
The embodied carbon score of Ostro passive house varies depending on how you assess it.
For this article the as built-house was compared to the same spec with one difference: substitution of the timber frame external walls with a cavity wall build-up to achieve the same thermal performance.
The as-built house scored a cradle-tograve embodied carbon figure of 437 kg CO2e/m2 of the treated floor area, falling well short of the RIBA 2030 Climate Challenge’s embodied carbon target for dwellings of 300 kg, but surpassing the 2020 (600 kg) and 2025 (450 kg) targets.
One obvious target for further reductions is stage B, the emissions associated with projected component replacements during the building’s assumed 60 year life. The stage B figures assume that elements like the roof, windows, roof window and floor covering will each be replaced once within the building’s life. In the case of well-detailed, high quality windows and roof windows – both of which are aluminium-clad – a considerably longer lifespan may be possible.
As Wolfgang Feist and colleagues found in a monitoring study of the first passive house scheme 25 years after its completion, the original triple glazed windows were found to have less than a 5 per cent loss in insulating value (U-value), and the frames were expected to last at least another 25 years. Their report noted advances in glazing technology in the intervening decades, and referenced a functional service life for glazing in excess of 40 years.
Conceivably, the windows at Ostro may not need to be replaced within 60 years. If some of the main assumptions around replacements during the building’s projected lifespan were altered – assuming no replacements of windows or roof windows, and one rather than two replacements of the solar PV array – the cradle to grave embodied CO2e score would drop to 383 kg CO2e.
Additional savings from the concrete foundations are limited by the fact that the as built insulated foundation system had already significantly reduced cement use compared to strip foundations, but substituting 70 per cent of the Portland cement in the concrete foundations with GGBS would lower the total to 338 kg CO2e.
Some savings come from just having independently verified data. A case in point is the Forbo Marmoleum flooring, which had an Environmental Product Declaration (EPD) confirming that the product’s embodied carbon emissions were just 23 per cent of the total for linoleoum from the Inventory of Carbon and Energy – a reflection of the kinds of improvements progressive manufacturers can make in some product areas.
Other areas to target may include reducing the 42 kg CO2e to transport materials to site – perhaps a reasonable target even without localising supply chains given progress in EVs – and the estimated 29 kg CO2e related to the construction process itself – a figure which may be much lower in this case, given the amount of direct labour involved. If all of these changes were made, it’s possible the building would beat the 2030 Climate Challenge target of 300 kg CO2e m2 TFA.
The analysis also looked at the building’s external walls in isolation, and compared them to cavity wall construction (assuming 100 mm concrete blocks internally and externally) to achieve the same energy performance.
In this case, if we compare the cradle to factory gate emissions for materials only, it tells a very different story – in spite of the fact that the cavity wall comparison ignores the extra concrete that may be required in the foundations in this case.
The upfront CO2e emissions for the as built timber frame walls come in at 8.43 tonnes of CO2e, whereas the cavity wall version would be 15.25 tonnes of CO2e. Meanwhile, the as-built walls also include 33.8 tonnes of CO2e sequestered in the timber and wood fibre insulation, compared to 5 tonnes of stored CO2e in the cavity wall – a benefit that arises from the assumption of timber cladding being used in that case.
Life cycle assessment rules state that while sequestered CO2 can be considered in cradle- to-grave analyses, the end of life must be factored in too. To an extent it’s a moot point: the applicable standard for EPDs, 15804+A2, specifies that even if CO2 sequestering materials are recycled at the building’s end of life, the sequestered CO2 is passed on to this future use and thus ‘lost’ from the building’s embodied carbon score – a fact which may actively discourage consideration of deconstruction and disassembly in the design process.
But the fact remains: the house as built includes 299 kg CO2e/m2 stored in timber and timber-based products for as long as they remain in the building, whereas the same house built with typical cavity wall construction would store 128 kg CO2e/m2 (certain timber use is common to both approaches, including the timber cladding, timber floors, etc).
And with an extraordinary house like this – due to the combination of architectural quality and robust detailing – the CO2 emissions sucked out of the atmosphere and stored in those timber products must stand a strong chance of staying out of the atmosphere far beyond the assumed 60 years, buying humanity vital time in the great climate fight.
Image gallery
https://passivehouseplus.ie/magazine/new-build/boxing-clever?highlight=WyJ3ZWxscyIsIndlbGwiLCJ3ZWxsZSIsIndlbGxuZXNzIiwid2VsbGluZyIsIid3ZWxsIiwid2VsbCciLCJ3YXRlciIsIndhdGVycyIsIndhdGVyJ3MiLCJ3YXRlcmluZyIsIndhdGVyZWQiLCJiaWxsIiwiYmlsbHMiLCJiaWxsaW5nIiwiYmlsbGVkIiwiYmlsbCdzIiwiYmlsbCciLCJiaWxsaW5ncyIsImJ5IiwiYmlsbCBieSJd#sigProId79bfb30761