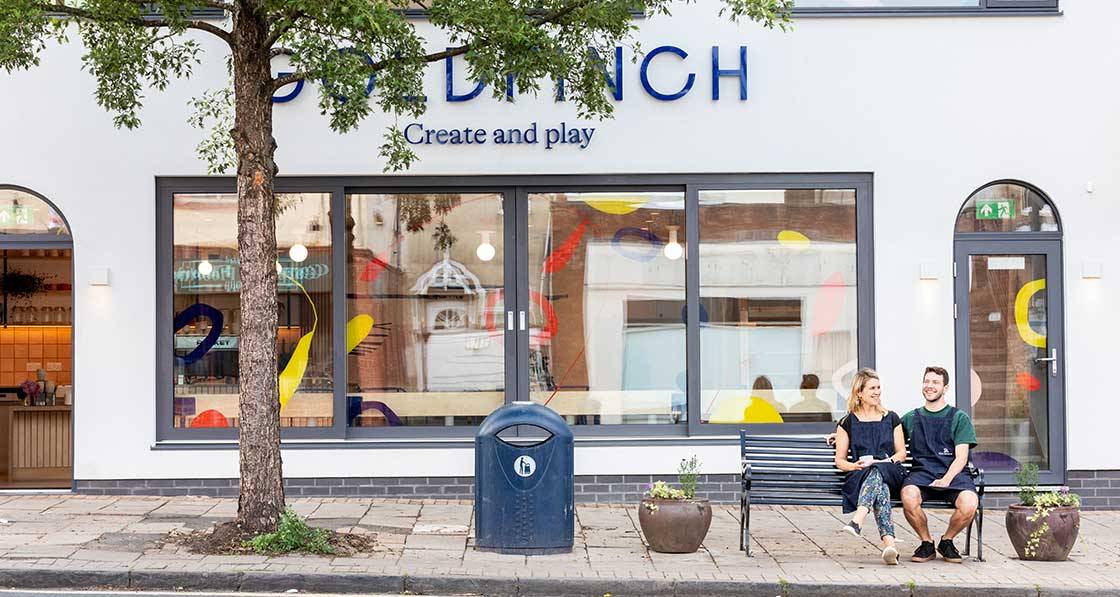
- Feature
- Posted
Play to win
Click here for project specs and suppliers
Building type: 150 m2 mid terrace café and art studio
Method: Timber frame, insulated foundations, cellulose, heat pump, PV
Location: Bristol
Standard: Passive house classic (pending)
Embodied carbon: £75 / month*
* Calculated total energy costs, including standing charges and feed-in tariff income. See ‘In detail’ panel for more information.
When Nicole Strong and Mark Finney arrived in Bristol they were seeking a change. They got one, and a challenge, too.
Coming from Cape Town, the couple, both of whom are architectural professionals, relocated to England, Finney’s home, and set to work. Arriving in the city, Strong, who had been a senior landscape architect for the city of Cape Town, decided to turn a problem into an opportunity: having young children, she found that the city, despite its reputation as one of England’s most vibrant, was missing something. But using her background as the foundation, she set about building it.
“My background is in architecture, urban design and city planning, and I am interested in the social side of buildings and the built environment,” she said.
So what was missing? Strong parlayed her experience to create a new space that offered families somewhere to be that was neither home nor an unsuitable commercial space.
“The coffee shops are very dark and dingy, and there are not many healthy options in terms of food. There are play centres but they can be a little bit overwhelming [both] for parents and children,” she said.
The walls were collapsing and covered in algae and mould, so we had to demolish and start again
The end result is Goldfinch, a welcoming community space designed to give families the freedom to imagine, create and connect, beyond the confines of the traditional café or classroom.
“We wanted to create a space where children could be, where adults could be, where they could connect in a really beautiful space. So we found a building,” she said. The building was far from suitable, however.
The 80 m2 site, located in the Bristol suburb of Westbury-On-Trym, was home to a one-storey building in extremely bad condition that had previously housed a print shop.
Nevertheless, despite this and the bad luck of beginning the process just as the Covid-19 pandemic and its attendant lockdown shut down construction, Strong and Finney proceeded.
“It was a dilapidated building that needed to be completely rebuilt. Covid slowed things down, but we got the planning [permission],” she said.
Planning was approved for a two-storey – 75 m2 per storey – building to house the new venture.
Strong’s husband Finney, a partner in Seb + Fin Architects, took up duties as architect on the project and, despite the site’s suitability, it soon became clear that an entirely new building would need to be designed and built.
While Finney says he prefers to preserve building fabric when it is possible, his description of the existing building on the site makes it clear why the couple did not go down that road.
“We did look at a retrofit. It was a single storey, but increasingly dilapidated building and half of the site was a yard. Part of it had a corrugated tin roof, which was collapsing, the walls were collapsing and were covered in algae and mould, so we had to demolish and start again,” he said.
“The previous tenant moved out because the building was so dysfunctional. It was heated with electric bar heaters [and] frankly, it was getting dangerous”.
Sustainability consultants Ecospheric, who provided energy and life cycle assessment consultancy on the project, did attempt to see if a retrofit was possible, but the results were not positive.
“We looked at viability, but it was too restrictive,” said Kit Knowles, Ecospheric’s managing director. “First, as an infill site it was tight, as they always are, but the building was not really salvageable. It was a case of too structurally compromised, too much function required and too little space”.
Skills on site
This article was originally published in issue 46 of Passive House Plus magazine. Want immediate access to all back issues and exclusive extra content? Click here to subscribe for as little as €15, or click here to receive the next issue free of charge
If the existing building was an inauspicious start the site at least afforded the opportunity for a new beginning. As Seb + Fin Architects, a specialist in residential architecture, is enthusiastic about the passive house and Enerphit standards, building the new building to passive standard was the obvious choice.
Finney designed the building with the ground floor resting on a concrete raft foundation with a 25 mm thick concrete slab, housed in an Isoquick insulated foundation system. The walls are made with timber I-joists with cellulose fibre insulation and an external render. “Internally, on the walls, we get good airtightness,” said Finney.
Ecospheric, in its consulting role, took major steps to ensure that the building would meet passive house standards despite the difficulty doing so given its use as a café. Knowles and his colleagues did a feasibility study to establish how the passive house standard could be met for a building with this intended use, given the specific kinds of loads a café would bring.
According to Knowles, other similar UK projects were thin on the ground at best. “There are cafés inside a university and a student accommodation unit, but those are much bigger, commercial buildings. So, this is the first time that’s been done in the UK.” This points to a general truism: while residential buildings tend to have very similar energy use profiles, non-domestic buildings are far more varied, given the broad ranges of uses they encompass, and the consequent divergence in terms of impact on energy use. For a building where the main function is a café, a substantial amount of appliance use in a relatively small building pushes up the plug loads, and therefore makes it more challenging to meet the primary energy targets for passive house.
“We did our modelling and consulted with the passive house certifiers [PH Certification],” said Knowles. “The conclusion is that it would be possible if we drew up a new profile with the Passive House Institute.”
Ecospheric also performed a whole life carbon analysis, a process analysis and engaged with the design of the mechanical and electrical systems.
“Carbon analysis was done with the creation of an ‘optioneering’ engine, looking at the viability and impact on a whole life basis, of both the active and passive elements. Once we’ve got through that we know all of the different materials and methodologies we’re using and all the mechanical and electrical elements. After that, we need to know how it is going to fit together: it’s the nitty gritty that gets it right,” Knowles said.
“Next, we used our detailing methodology process, called the ‘thirteen hats’. It’s an analysis where you put on a different hat and use that to guide our detailing process. Finally, we did the mechanical and electrical, getting involved with designing that,” he said. Construction was contracted to Earthwise Construction, a Bristol-based specialist in passive house construction and heat recovery ventilation.
Both Strong and Finney complimented Earthwise’s work, noting that few contractors have the right skills and experience – and some of the few that do only work on massive projects.
We had already done all of the joinery and then the Russian invasion of Ukraine meant birch ply became much harder to get
According to Strong, working with Earthwise was particularly reassuring because previous experiences with other builders had not always been ideal.
“Because of our specialist contractor it went as smoothly as it possibly could. When we first tried out [passive house techniques] at our home, with different contactors, there were some problems, Earthwise knew what they were doing,” said Strong.
Finney says he was glad to work with Earthwise because there are few enough contractors in the area with the right expertise.
“In Bristol, you’ve got a little group of about three people who can do this. One of them, I don’t think they touch things under half a million and are looking for more than a million: high-end houses, basically,” he said.
-
The existing building was in extremely bad condition and structurally compromised The existing building was in extremely bad condition and structurally compromised
-
Intello Plus membrane and ductwork for MVHR systems Intello Plus membrane and ductwork for MVHR systems
-
Velux roof windows help to bring in more natural light Velux roof windows help to bring in more natural light
-
Installation of two 12.5 mm layers of British Gypsum FireLine board on timber battens. Installation of two 12.5 mm layers of British Gypsum FireLine board on timber battens.
-
The existing building was in extremely bad condition and structurally compromised The existing building was in extremely bad condition and structurally compromised
-
The existing building was in extremely bad condition and structurally compromised The existing building was in extremely bad condition and structurally compromised
-
Work underway demolishing the building as it had to be completely rebuilt Work underway demolishing the building as it had to be completely rebuilt
-
Ground floor build-up features a 250 mm deep concrete raft slab with Isoquick 100 mm perimeter insulation upstand Ground floor build-up features a 250 mm deep concrete raft slab with Isoquick 100 mm perimeter insulation upstand
-
Ground floor build-up features a 250 mm deep concrete raft slab with Isoquick 100 mm perimeter insulation upstand Ground floor build-up features a 250 mm deep concrete raft slab with Isoquick 100 mm perimeter insulation upstand
-
Arrival of windows for installation Arrival of windows for installation
-
Timber frame structure progressing Timber frame structure progressing
-
Smartply Propassiv OSB, seams fully taped with Pro Clima Tescon Vana Smartply Propassiv OSB, seams fully taped with Pro Clima Tescon Vana
Earthwise was also able to make suggestions during the design and build, including how to meet requirements around heating and ventilation.
“We were very nervous about meeting building regulations requirements, but the contractor suggested using two residential MVHR units,” said Finney.
“We were incredibly pleased with the contractor because they were very experienced. They were good at what they do, and so there was no need for hand-holding,” he said.
This was also important because one of the core dreams was for a healthy building for the families visiting for classes and social space at Goldfinch.
“Apart from sustainability, we wanted a healthy environment with good air circulation,” Strong said.
In addition to construction and ventilation, Earthwise also did all of the internal joinery. “That was quite novel, [and was possible] because they are joiners,” said Finney.
As it is not a residential building, however, there were additional challenges. As a result, the fact that a new build was required had some significant design benefits.
“Due to the high occupancy, the ventilation rate has got to be really high and that’s quite challenging to address, but the envelope is new so it was easier to achieve. Working around things in Enerphit is tricky: you always have cold bridges to address, whereas we just designed them out of it,” said Finney.
A Stiebel Eltron air source heat pump – selected by Ecospheric to ensure a low global warming potential refrigerant as part of the performance spec – provides heating and cooling, while photovoltaic panels feed electricity to a battery for storage and later use.
Geopolitical events also had an impact, primarily on cost: both the post-pandemic supply chain crunch and the Russian invasion of Ukraine were felt.
“We were quite fortunate because the plot was purchased and was going through the legal side during lockdown. What we did suffer from was price inflation. We were relying on a lot of timber products, which all went up by 50 per cent. That has now levelled off but not come down,” said Finney.
“We had already done all of the joinery specifications and design and then the Russian invasion of Ukraine meant birch ply became much harder to get,” he said. Nevertheless, the project was completed and signs of success are visible.
“Because it’s tight and well-insulated we were able to do all of the hot water, heating and cooling from an air source heat pump on the roof and that’s distributed by the ventilation system. The heat demand should be pretty low – it’s designed to minimise the demand,” he said.
Open for around three months at the time of publication, the next step for Goldfinch is to see if the building performs as expected. “What we are keen to do is see how it works down the road,” said Finney.
“What we often tell clients is that if you did passive house modelling it should be pretty accurate – but we want to see just how accurate,” he said.
Of particular interest to Finney is understanding the impact of materials such as concrete and expanded polystyrene, choices forced on the design by the site.
“We’re very keen on embodied carbon analysis. We were keen to use as much timber and [as many] natural materials as possible, but in this case we had to use EPS and concrete and [petrochemical-based] roof insulation. We would have avoided that on a greenfield site. Also, there was zero information on the steel and that means we have to assume the worst case scenario and that could knock us out of the top bracket,” he said.
The experience, largely positive but not without the unexpected problem of inflation in the price of materials, has only confirmed Finney’s view that all construction projects should be sustainable.
“The government needs to come to the party and incentivise good building practice. It should always be the case that choosing the green option is cheaper,” he said.
Selected project details
Client: Goldfinch Create and Play
Architect: Seb + Fin Architects
Civil / structural engineer: Build Collective
Energy consultant and life cycle assessment consultant: Ecospheric
Main contractor: Earthwise Construction
Electrical contractor: Electrotech SW Ltd
Airtightness tester/consultant: Building Analysis and Testing Ltd
Passive house certifier: Zero Energy
Build system supplier: Pasquill
Cellulose insulation: Warmcel, via PYC
Wood fibre insulation: Pavatex, via Soprema
Floor insulation: Isoquick
Airtight OSB: Medite Smartply
Airtight membrane and tapes: Pro Clima
via Ecological Building Systems
Windows and doors: Viking
Roof lights: Velux
Entrance doors: Velfac
Flooring: Forbo
Roofing: Alwitra Evalon
Rainwater systems: Lindab
Heat pump: Stiebel Eltron, via Green Flare
Mechanical ventilation system: Zehnder, via Earthwise Construction
Photovoltaic supplier: JA Solar array and Pylontech battery, via Green Flare
Sanitaryware: Ideal Standard
Embodied carbon
Ecospheric’s carbon analysis included a life cycle assessment on the building calculated using OneClickLCA. The building was assessed against the RIBA 2030 Climate Challenge, and compared against the RIBA 2030 target for schools, as the closest building use category to the play cafe. The building met the RIBA 2030 target of 540 kg CO2e/m2 GIA, covering the RICS life cycle stages A1 through C5, but excluding operational energy and water use (B6 & B7).
The reality however may be better still. One problem Ecospheric encountered was the absence of Environmental Product Declarations for big ticket items such as the steel, concrete and rebar. “We have assumed average UK figures, to be conservative,” said Knowles.
Life cycle assessments cover up to four modules: A, B, C and D. Module A covers the carbon emitted in manufacturing the building’s materials and technologies, in transporting them to site, and in the construction process itself. B covers emissions during the expected lifespan of the building – in the UK a reference life of 60 years is typically taken - including maintaining, repairing or replacing materials, and operational energy and water use. C covers the building’s end of life, including emissions released by the building being knocked down (or hopefully taken apart), including material disposal. D focuses on potential future uses of materials from the building in other applications. Module D emissions typically aren’t included in embodied carbon targets, but it’s encouraged to report them separately. Frankly, once a life cycle assessment moves beyond module A, the figures start to become heavily reliant on assumptions – about how long a component will last, about how a building will be maintained, about how polluting the manufacture of replacement components will be, and about how much care will be taken in deconstructing rather than just demolishing a building. While it is important to look at a building on a cradle-to-grave basis – and to think about designing the building in such a way as to minimise emissions down the line – Knowles makes the point that a particular focus on upfront emissions is key.
“We feel it is important to list the A1- A5 figures separately as the next eight years are crucial for climate change,” he says, “and trying to predict what the embodied carbon of replacement materials in 30 years time or the end of life carbon in 60 years is pretty difficult.”
In this building, Ecospheric calculated a module A total of 353 kg CO2e/m2 GIA. If the CO2 stored in biogenic materials such as timber, wood products and cellulose is factored in, that total drops to 190 kg CO2e/m2 though LCA experts tend to counsel against netting off in this case, preferring instead to say that the upfront total is 353 kg CO2e/m2, with a further 163 kg CO2e/m2 stored in the biogenic materials in the building.
In detail
Building type: 150 m2, mid-terrace two-storey timber frame café and art studio.
Site type & location: Suburban high street, Westbury-on-Trym, Bristol
Completion date: July 2023
Budget: Construction cost including fit out and furnishings of £670,000 (excluding site purchase and professional fees).
Passive house certification: Passive house classic (certification pending)
Space heating demand: 3.0 kWh/m2/yr
Heat load: 6.7 W/m2
Primary energy non-renewable: 195.1 kWh/m2/yr
Primary energy renewable: 77.5 kWh/m2/yr
Heat loss form factor: 2.9
Overheating: 0.0 per cent of year above 25 C, assessed in PHPP
Number of occupants:
Ground floor max: 26 people (20 seated, 2 staff, 4 people queuing for take away).
First floor max: 26 people (12 children, 12 accompanying adults, 2 staff). A realistic average occupancy would be 20-40 people during daytime.
Airtightness (at 50 Pascals): 0.43 m3/hr/m2 at 50 Pa / 0.40 air changes per hour
Embodied carbon: 540 kg CO2e/m2 GIA for RICS life cycle stages A1 through C5, but excluding operational energy and water use (B6 & B7). Calculated using OneClickLCA.
A1-A5 (cradle to practical completion) = 353 kg CO2e/m2 GIA excluding biogenic storage.
A1-A5 (cradle to practical completion) = 190 kg CO2e/m2 GIA including biogenic storage.
Measured energy consumption: Not available
Thermal bridging: Continuous tongue and groove wood fibre to each façade; Isoquick below slab insulation with insulated upstands; Insulated reveal liners (wood fibre for main windows, spacetherm for roof light windows); Warm roof deck extending close to the perimeter, with insulated timber ladder structure to form perimeter edge. Building Y-value: 0.005 w/m2K, based on calculated thermal bridges.
Energy bills (measured or estimated): Estimate based on PHPP data and assumed levels of occupancy is £900/yr electricity based on current typical business energy costs of 30p/kWh and assuming 80 per cent self-consumption of energy generated by PV on roof, plus a standing charge of £200/yr. Export of the remaining 20 per cent is estimated to generate £200 in income at 15p/kWh.
Ground floor: (Top to bottom) Marmoleum Cocoa - Earl Grey Chocolate finish; latex self-levelling compound; 250 mm deep concrete raft slab to structural engineer’s spec and detail; Isoquick 100 mm perimeter insulation upstand (vertically around perimeter of the slab), with the top of the insulation level with the top of the floor screed; Isoquick 150 mm grade EPS300; Visqueen Radon R400 membrane with fully taped seams; non-shrinkable compacted fill; ground. U-value: 0.207 W/m2K.
Walls: (Inside to out) Paint; two 12.5 mm layers of British Gypsum FireLine board and 3 mm skim coat plaster finish with all joints taped with scrim tape; 25x50 mm treated FSC certified pine battens, running vertically at 400 mm centres to form services void; 12.5 mm layer of Smartply airtight board with fully taped seams with Pro Clima Tescon Vana; 300x90 mm JJ I-joist construction fully filled with Warmcel cellulose fibre insulation; 40 mm Pavatex Isolair wood fibre insulation board mechanically fixed to the timber frame; Baumit render system including 2 mm Baumit SilikonTop finish render, Baumit premium Primer, 6 mm Baumit MC55 lime contact mortar, incorporating Baumit StarTex mesh. Colour Baumit W1208 ceramic white. U-Value: 0.115 W/m2K.
Where the external wall runs along the external maintenance access, the render system is replaced as follows to allow for pre-fabrication of wall panels: 40 mm Pavatex Isolair wood fibre insulation board mechanically fixed to the timber frame; Pro Clima Solitex Frontra WA breather membrane, with fully taped seams using Tescon Vana; treated 44x44 mm pine battens running vertically at 400 mm centres (and doubled up at junctions of boards) with Tenmat FF102/50 ventilated cavity barrier; 3050x1200x8 mm RockPanel. Panels screwed into battens with stainless steel screws. The top of the panels are weatherproofed with a PPC aluminium sill (colour matched to windows external colour) fixed to the I-joist beyond. The underside of the panels includes a stainless steel insect mesh to form a continuous barrier to vermin and insects.
The wall plinth (dense blockwork upstand with Isoquick insulated upstand externally) clad with 15 mm Wetherby Brick Slip Cladding System in ‘Staffordshire Blue’ colour. U-value: 0.115 W/m2K.
New party walls: (Inside to outside) Paint; two 12.5 mm layers of British Gypsum FireLine board and 3 mm skim coat plaster finish with all joints taped with scrim tape; 25x50 mm treated pine battens, FSC certified, running vertically at 400 mm centres to form services void; 12.5 mm layer of Smartply airtight board with fully taped seams; 300x90 mm JJ I-joist construction to structural engineer’s spec fully filled with Warmcel cellulose insulation; egg crate tanking system: Delta MS500 (8 mm cavity drain membrane) with fully taped seams and plugs to manufacturers spec. Minimum embedment of plugs in party wall to manufacturers spec. subject to party wall agreement; Koster Polysil TG500 (anti lime coating) applied to existing wall; existing masonry party wall; neighbouring building. U-value: 0.121 W/m2K
Roof: (Outside to inside) Warm roofing system including Alwitra Evalon in slate grey (RAL 7015) with colour matched 75 mm drip trims; 200 mm (100+100 mm) PIR with staggered board application, secured using manufacturer approved, thermally broken fasteners; InStar Elotene DSN self-adhesive total vapour barrier; 18 mm OSB3 T&G board fixed to timber structure below; firring timbers: ex 47x225 mm C24 timber at 400 mm centres at minimum 1:60 falls. Timbers trimmed to a minimum of 70 mm; 300x90 mm JJ I-joist construction to structural engineer’s specification / specialist sub-consultants design to form a level ceiling; timber battens to form service void and allow ceiling to extend into window reveal; two 12.5 mm layers of British Gypsum FireLine board and 3 mm skim coat plaster finish with all joints taped with scrim tape; paint; acoustic panels. U-Value: 0.105 W/m2K
Windows & external doors: Main entrance door: Velfac Ribo door and top light window triple glazed aluminium clad timber framed window and door, with Argon filling and overall Uw value of 0.89 W/m2K installed.
Windows and fire escape door: Viking triple glazed aluminium clad timber framed windows, with Argon filling and overall Uw value range between 0.74 and 1.4 W/m2K. The lower Uw value is due to fire-rated glass requirement.
Service access door: Moralt Ferro Passiv Firesafe FD30 Exterior MDF faced door with laminated pine frame (no glazing). Ud value of 1.0 W/m2K. PHI certified.
Roof windows: Two Velux UK08 triple glazed ‘Extra Heat’ roof lights with Velux UK08. U-value: 1.01 W/m2K installed.
Heating system: Stiebel Eltron WPL-A 07 HK Premium Pack consisting of an air-to-water heat pump with cooling capacity, integral hot water cylinder with a nominal capacity of 168 L, and a 100 L buffer cylinder. The heat pump refrigerant R454C, has a global warming potential of 146. Heating and cooling distributed via two Zehnder ComfoPost air-to-water heat exchangers (one per floor).
Ventilation: Two Zehnder Comfoair Q600 MVHR systems (one per floor). PHI certified. Heat recovery rate of 87 per cent thermal efficiency according to EPN standard 97.6 per cent.
Water: Low flush WCs and microbore hot water pipes.
Electricity: PV: 21 x JA solar panels JAM60S21-370/MR 370 Watts
Inverter: S5-GR3P8K SOLIS - Ningbo Ginlong Technologies 8.000 kW
Battery: PylonTech FORCE H2 7.1 kWh
Sustainable materials: Timber frame using FSC certified timber and I-joists, cellulose insulation, wood fibre insulation and marmoleum floor finish.