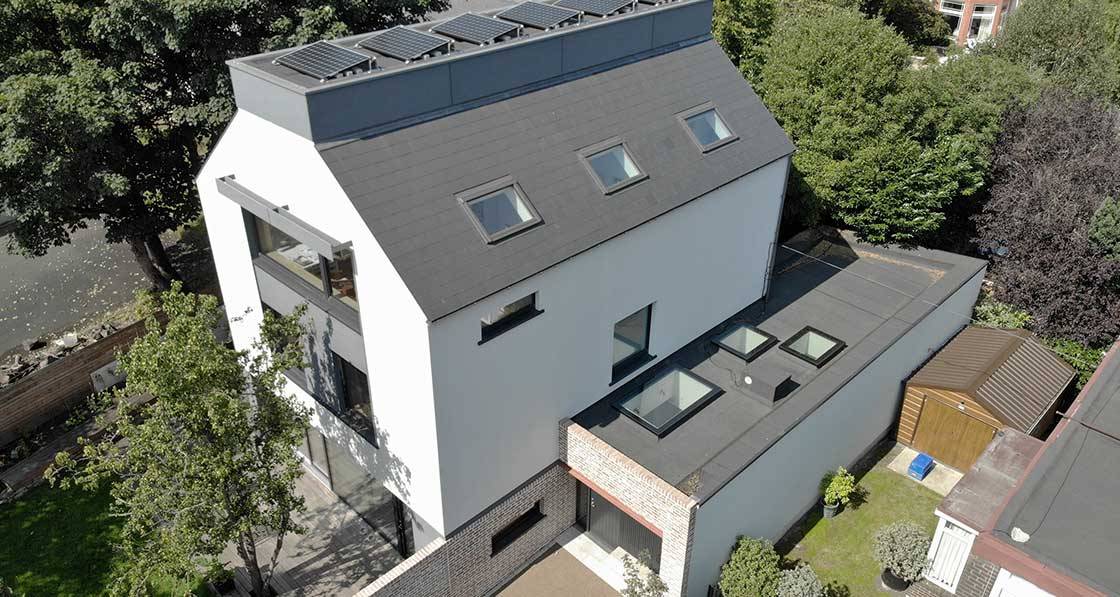
- Upgrade
- Posted
Onwards and upwards
This Enerphit project in the suburbs of South Dublin has dramatically transformed and extended a dated 1970s dwelling by adding an extra storey, radically reducing its energy consumption and creating a smartly-designed, light filled family home and office.
Click here for project specs and suppliers
Building: 251 m2 detached home & office
Method: External insulation on blockwork
Location: Dartry, Dublin
Standard: Enerphit (passive house retrofit, certification pending)
BER: A3
Heating & hot water bill: €47 per month (to run the compact heat pump for space heating, hot water & ventilation, for a family of six and two home offices. See ‘In detail’ for more)
When architect Peter Nickels took on the The Willows project, he was working for the most demanding of clients: himself. This deep retrofit involved partially demolishing a dated 1970s dwelling and replacing it with a modern, energy efficient, and taller building.
The Willows was not Nickels’ first refurbishment, but it was an opportunity to put his interest in passive design into practice.
“I had refurbished my own home before and I sort of realised fairly soon afterward, within five or six years, that I could have done things differently. In the last ten to 15 years things have changed tremendously in terms of what we’re trying to achieve,” he says.
In 2013 Nickels and his wife Edelle O’Doherty bought the house — a two-storey flat-roofed structure in Dartry, Dublin 6 — with the aim of undertaking an extensive renovation.
When finished, it would have to serve not only as a home to their family of six, but also as an office for both (Edelle works as a nutritional therapist and functional medicine practitioner). “I thought ‘this is an opportunity to do things properly,” Nickels says.
The couple, both widowed and each with two teenage children, had decided to bring their two families together. Buying a house to raise the blended family was a huge stepping stone, Nickels says. They had been renting nearby and had seen the house come up for sale, although at first sight it did not appear to be an obvious choice.
Nickels was working for the most demanding of clients: himself.
“It was one of a pair of identical infill houses which had been built in the side garden of a large Victorian redbrick villa. These houses were completely out of scale and character with their surrounding context – to one side was Sunbury Gardens, a Victorian architectural set piece, comprising three-storey redbrick villas, all protected structures, arranged around a formal landscaped garden. To the other side was a 1990s development of three-storey townhouses.”
The positive thing about this was the existing house had neither aesthetic nor historical value. “I felt pretty free in the design, because of the age of the building,” Nickels says. “There was nothing precious about it, even though we were right next to these protected structures. Whatever we did was going to make it perform better, function better, and look better.”
Nickels received planning permission for the refurb in 2016, but at first the aim wasn’t to go passive. It was only after this that he became an avid reader of Passive House Plus, and subsequently decided to undertake training to become a certified passive house designer.
This article was originally published in issue 39 of Passive House Plus magazine. Want immediate access to all back issues and exclusive extra content? Click here to subscribe for as little as €10, or click here to receive the next issue free of charge
“I designed the scheme and obtained planning permission before undergoing passive house training – so although originally it did embody many of the principles of passive house, the scheme needed to be reviewed and the details re-visited before tendering.”
He says this magazine was a big help in finding the right materials and suppliers. “I was looking for passive house performance window systems and external insulation systems, and originally was considering timber frame on the top floor as a lightweight way to extend over the existing structure.”
Technical challenges
Angelo Babos, owner of main contractor Leopardstown Construction, says that working for an architect building his own house only had a positive effect on the project.
“The only thing I could see different from other jobs in terms of the client being an architect was that he was able to make changes in the layout, finish and location of [things like] electricals,” he says.
1 The southern side of the house prior to renovation; 2-5 much of the external wall on the south elevation at ground floor level was removed and replaced with full height glazing, and the relocated kitchen now feels like part of the garden; 6-8 the masonry walls were insulated externally with graphite enhanced EPS with silicon render finish.
Airtightness works included 1 use of blowerproof liquid airtight paint, seen here at the wall-to-floor junction; 2 & 3 use of airtightness membrane behind joist ends and partition walls; 4 Partel Izoperm membrane behind service cavity battens to the roof; and 5 Partel Conexo tape around window frames; meanwhile thermal bridging measures included 6 Schoeck Isokorb thermal breaks; 7 & 8 and Partel Alma Vert structural insulation (seen here in green).
This does not mean the job was easy, though. In fact, soon into the build major problems requiring remedial work made themselves apparent. “We had to dig out some of the old lobby and found the middle wall and back were not strong enough to put another floor on.”
At this point, total demolition was considered. But Nickels says that by now, the importance of limiting the embodied carbon of the build was high on his mind. This guided a lot of the big decisions, such as preserving as much of the existing structure as possible, in spite of the technical challenges.
Some of the original walls had have to be rebuilt for structural purposes, and while Nickels originally wanted to specify timber for the second floor, he ended up using lightweight thermal blocks from Mannok due to concerns over the compatibility of different render systems applied over timber frame and block, and the associated detailing issues.
Thankfully, Angelo Babos and his team were not entirely new to passive house construction.
“I have done other passive house standard building, a lot of upgrading, especially heat recovery ventilation and Part L compliance,” Babos says.
“Because of the changes in regulations over the last few years, architects are keeping an eye on airtightness and upgrading the U-values of walls.”
Although retrofitting is increasingly seen as the only way Ireland can, at least in terms of its housing stock, meet its climate targets, Babos says the sheer amount of skilled labour required should not be underestimated.
“When you have a retrofit it’s much harder than building from scratch,” he says. “It was very hard to go around and make it airtight, you have weak spots to deal with. That made my life and my lads’ life very hard; we had to put a lot of work in to make it right.”
The main airtightness layer was formed by internal plaster on the new walls and existing plaster on old walls, which needed to be re-done in places. Airtightness tapes from Partel were used to seal junctions, while Blowerproof liquid airtight membrane was applied along door thresholds and where the external walls met the concrete slab (below where plaster could be applied).
Babos says that while the job was challenging, the positive side of this is that it was a learning experience, and a better one than you can get in the classroom or workshop.
“Next time will be easier as we learned a lot. When I did a course, back in 2013, we brought techniques from the workshop, but that was a workshop not reality. And when you go outside into the world you have to do a lot of research,” he says.
Nickels says part of his reasoning in choosing Leopardstown Construction was the need for confidence. “We tendered to builders who had passive house experience and passive house training. Angelo came at it with a very rigorous approach, he was thinking things through, methodologies and so on.”
Design for life
1 The roof features three Fakro quadruple glazed timber aluclad roof lights, while the new roof finishes include 2 fibre cement slates to the pitched sections; and 3 bituminous membrane on the flat.
Clues as to how to extend the dwelling lay in the original design: the house had a central staircase and hall, running east-west, dividing the plan into two equal halves, and the roof was flat.
Nickels says: “The obvious design solution was to go up – forming a new stair over the existing straight stair flight, a new second floor comprising a master bedroom to the north, and a spacious home office on the southern side with views out to the trees and the Dublin mountains. This solution provided the space required, without extending the footprint any closer to surrounding boundaries – and brought the house into scale with the three-storey Victorian houses and the 1990s townhouses.”
The decision to build up rather than out also provided another embodied carbon win: it improved the building’s form factor, the surface area from which heat can escape, to such an extent that the house could meet Enerphit, the passive retrofit standard, even without digging up the floor slab. This is despite the fact that there was only 50 mm of insulation underneath.
“This is where the use of the PHPP software really came into its own,” Nickels says, “to analyse and inform important and costly decisions like this.” (Some of the slab did ultimately have to be replaced to allow for underpinning of walls.)
At first floor level, the simple arrangement of the original house meant that the layout could be re-configured to provide four equally sized bedrooms, which were large enough for double beds and work desks, something that will have proved its value in recent months.
“This was the perfect democratic solution for four teenagers studying from home and meant that none of the children had to settle for a tiny ‘box room’ – which is a typical issue in many existing house types,” Nickels says.
At ground floor, the existing plan again made it very simple to swap the kitchen and living room, with the kitchen relocated to the southern side of the house where it has views out to the garden, whilst the living room was moved to the north side, with a large west-facing window, where it is bright in the evening.
Much of the external wall on the south elevation at ground floor level was removed and replaced with full height glazing, so the kitchen feels like part of the garden, and the movement of the sun around the house throughout the day can be fully experienced.
He became an avid reader of Passive House Plus.
With the addition of the extra floor and steeply pitched roof, the house is now much more visible from the street. But the increased scale and massing fits much better alongside the Victorian villas that inspired the house’s design. Their influence is reflected in features such as the prominent street-facing gable and the grouping of windows at first and second floor level (with brise soleil for shading). An existing mature pear tree was also retained to provide summer shading to the south elevation.
The merging of passive principles, aesthetics and meeting the needs of a modern family — all things missing from many mass-produced houses — should be the logical outcome of the reality of construction, Nickels says: it should all be right.
“There’s so much money invested in construction that you have to succeed on all fronts. Reducing embodied and operational energy is obviously critical to all building projects now, but as an architect the challenge is not just to incorporate these requirements but to use them to inform and help generate a contemporary design aesthetic.”
Though it seems unlikely that he would settle for a standard house, Nickels said the pressure created by the surrounding context helped. “There was a real challenge, being surrounded by historic red brick houses, to make a low energy, contemporary design work.”
Thermal comfort at the Willows
Temperature and humidity monitors were fitted in several rooms in the house, as the project was part of the SEAI Deep Energy Retrofit scheme. In the first year post-retrofit, the overall indoor air temperature (as measured by the return air on the Nilan unit) did not rise above the 25 C threshold for overheating specified by PHPP, the passive house design software. The top floor office was prone to localised higher temperatures, as it has a large south-facing window (with shading) and two rooflights (without shading). In practice, this was not a particular problem, as it is a large house and temperature differentials can be eased by leaving internal doors open. In addition, the rooflights can be opened to allow cross ventilation on the top floor. Conversely, the den at ground floor, which is located to the north of the house and has three external walls and a flat roof, does not benefit from solar gain during the day, and has intermittent occupancy. It is therefore regularly cooler than other rooms. This was anticipated at the design stage, and an electrical point was provided here so that an electric convector heater could be added later.
A huge change in air quality
During construction, extensive mould growth inside the stud partitions in the kitchen was discovered as a result of water leakage. One family member, who suffers with rhinitis and has a sensitivity to mould, had difficulty with the air quality in this room. But it had not been known that that the issue was within the fabric of the building. The clean filtered air supplied by the Nilan ventilation unit has now resulted in a huge change in indoor air quality for him and for the whole family. In addition to the improvement in air quality, Edelle was particularly keen to avoid the introduction of toxins into the interior of the house. Specifications therefore included Keim mineral paints – which are solvent and chemical free, non-allergenic, odourless and breathable — and Keracoll Cementoflex cement- based resin floor topping, a seamless thin finish with very low volatile organic compound (VOC) emissions that was applied over the floor slabs.
Additional words by Peter Nickels
Selected project details
Clients: Peter Nickels & Edelle O’Doherty
Architect: Peter Nickels Architects
Main contractor: Leopardstown Construction
Structural engineer: Niamh O’Reilly Structural Engineering
Heating & ventilation: Nilan Ireland
Passive house consultant: Earth Cycle Technologies
Quantity surveyors: FMMP
Electrical contractor: John Bombu Electrical
Airtightness tester: Building Envelope Technologies
External wall insulation system: Atlas Aval
EPS insulation: Thermotech
Thermal breaks: Partel
Thermal blocks: Mannok
Low thermal conductivity structural fixings: Schoeck, via Contech Accessories
Roof insulation: Saint-Gobain
Additional roof insulation: Gutex, via Ecological Building Systems
Floor insulation: Xtratherm
Airtightness tapes: Partel
Liquid airtight membrane: Blowerproof Ireland
Windows & doors: Viking, via Prestige Aluclad
Roof lights: Fakro
Cement fibre cladding: Cembrit Ireland
Resign floor topping: Keracoll Cementoflex, via Stone Seal
Roof slates: Tegral
Warm roof system: Moy Materials
Solar PV: Sunpower
Ventilation installation: Allied Air Conditioning
Eco paints: Keim, via McConnell Coatings
Embodied carbon
The building’s embodied CO2e emissions were calculated by John Butler using PHribbon, resulting in a cradle to grave figure of 79.1t CO2e, or 282 kg CO2e /m2 GIA when calculated in accordance with the RIBA 2030 Climate Challenge. The biggest element of this total was the external walls – including new and retrofitted walls (22.6t CO2e), followed by the solar PV array (15.4t), a new roof system (8.6t), building services (6.1t), windows, doors and roof windows (6.1t), the steel frame (6t), and demolition (5.8t). Sixty-year lifespans were assumed for all building fabric, excluding the flat roof system, where 30 years was assumed, and 40 years for the render system, based on the Atlas Aval NSAI Agrément certificate.
The PV array and compact heat pump were assumed to have 30-year and 20-year lifespans respectively, with the ductwork assumed to last for 60 years. Where Environmental Product Declarations (EPD) were not available for the exact product, data from equivalent products was used (e.g., from the closest matched Product Environmental Passports for a heat pump and EPD for a different EWI system), or emissions are based on emissions for the component materials (e.g., window frames and ventilation ducting). In all 69 per cent of materials mass and 82 per cent of lifecycle stage A-C material emissions are accounted for by EPD data and 18 per cent by reference values (mainly from the ICE database).
In detail
Building type: Detached 251 m2 (TFA) home, created from the retrofit of 179 m2 1970s dwelling.
Site & location: Urban site, Dartry, Dublin 6
Budget: Not disclosed
Completion date: September 2020
Passive house certification: Pre-submission for Enerphit certification
Number of occupants: 6
BER
Before: D2 (295.2 kWh/m2/yr)
After: A3 BER (54.16 kWh/m2/yr)
PHPP
Space heating demand: 24.6 kWh/m2/yr
Heat load: 13 W/m2
Primary energy demand: 94 kWh/m2/yr
Heat loss form factor: 1.16
Overheating: 2 per cent of hours above 25C
Energy performance coefficient (EPC): 0.431
Carbon performance coefficient (CPC): 0.401
MEASURED ENERGY CONSUMPTION
Before: 132 kWh/m2/yr (January to December 2018 inclusive, all energy use, gas & electricity)
After: 33.76 kWh/m2/yr (September 2020
to August 2021 inclusive, all energy use, all electricity)
ENERGY BILLS
Before: €2,500 on gas and electricity for all of 2018.
After: €1,294 on electricity (September 2020 to August 2021 inclusive). Includes all energy use. This period included lockdowns when the house was fully occupied with six people working/ studying from home. The measured energy consumption for the Nilan Compact P heating & ventilation unit between September 2020 and January 2021 inclusive (1,811 kWh total), which we have estimated (and likely overestimated) to increase to a total of 3,644 kWh over 12 months. Bonkers.ie suggests a cheapest available bill of €567/year or €47 per month to run the heat pump for space heating, hot water and ventilation – for a family of six and two home offices, and with higher-than-normal occupancy due to the pandemic. The heat pump energy use figures include VAT but exclude standing charges & PSO levy, as these charges apply for any dwelling with an electricity connection. This also assumes no contribution from the PV array to power the heat pump. Summer heat pump data was not available due to IT issues.
AIRTIGHTNESS (AT 50 PASCALS)
Before: 11.32 (m3/hr)/m2
After: 0.98 (m3/hr)/m2
GROUND FLOOR
Original floor (before): Generally, 150 mm concrete floor slab on 50 mm PIR insulation. U-value: 0.488 W/m2K. Original extension floor: 150 mm concrete floor slab on 25 mm EPS insulation. U-value: 1.078 W/m2K
Original floor (after): Existing floor build up retained generally. Approx 25 per cent of slab replaced where required by underpinning works. Upgraded floor build up: 150 mm concrete slab on 100 mm PIR insulation U-value: 0.261 W/m2K New extension ground floor: 150 mm concrete slab on 150 mm PIR insulation. U-value: 0.141 W/m2K
WALLS
Original walls (before): 103 mm brick outer leaf followed inside by 100 mm cavity filled with EPS blown bead, 100 mm concrete block inner leaf, 13 mm plaster. U-value: 0.335 W/m2K
Original walls (after): 120 mm or 140 mm graphite enhanced EPS insulation with silicon render finish externally, over existing cavity wall build up as above. U-value: 0.146 W/m2K or 0.133 W/m2K
New extension walls: 200 mm or 220 mm (depending on location) graphite enhanced EPS insulation with silicon render finish, over 200 mm Quinn Lite (Mannok) standard blocks laid on flat, 13 mm plaster internal finish to form airtightness layer. U-value: 0.138 W/m2K or 0.128 W/m2K
ROOF
Original roof (before): Flat roof, bituminous roofing felt on 18 mm plywood, followed underneath by timber firring pieces, and timber joists with approx 175 mm mineral wool insulation between joists, 13 mm plasterboard internal ceiling finish. U-value: 0.190 W/m2K
New flat roof over den (retaining original roof structure): Bituminous roof membrane on 200 mm Xtratherm PIR insulation, on 18 mm OSB3 deck laid to falls, over timber firring pieces and 175 mm deep existing timber joists; Isover Metac mineral fibre insulation between joists (average depth 325 mm), on Partel Izoperm airtightness/ VCL membrane below joists, 50 mm battens to form service cavity below joists, 13 mm plasterboard internal ceiling finish. U-value: 0.071 W/m2K
Extension pitched roof: Fibre cement roof slates, on 50 mm counter battens, 50 mm battens to form ventilated air space and breather membrane; on 35 mm Gutex Multiplex Top wood fibre board insulation laid over 200 mm deep timber rafters; Isover Metac mineral fibre insulation between rafters, on Partel Izoperm airtightness/VCL membrane below rafters, on 50 mm battens to form service cavity below rafter with 50 mm mineral fibre insulation within cavity, on 13 mm plasterboard internal ceiling finish. U-value: 0.145 W/m2K
Extension flat roof (over utility room): Bituminous roof membrane on 200 mm Xtratherm PIR insulation, on 18 mm OSB3 deck laid to falls, Partel Izoperm airtightness/ VCL membrane above joists, over timber firring pieces and 175 mm deep timber joists, 13 mm plasterboard internal ceiling finish. U-value: 0.113 W/m2K
WINDOWS & DOORS
Before: Mixture of double glazed PVC, aluminium and timber windows, solid timber front door. Overall approximate U-value: 3.50 W/m2K New windows: Viking DK88 triple glazed windows. Timber frames at first & second floor, timber aluclad at ground floor. Argon-filled, with two low-E glasses (Planitherm One) and SGG Swisspacer Ultimate warm edge solution. Average whole house U-value 0.80 W/m2K
New pitched roof windows: Fakro FTT U8 Thermo quadruple glazed timber aluclad roof light. Overall window U-value 0.58 W/m2K New flat roof windows: Fakro DXF DU6 non-opening triple glazed roof light with multi chamber PVC kerb profile. Overall window U-value 0.70 W/m2K
HEATING & VENTILATION
Before: Gas fired back boiler with low temperature hot water radiators and 2 x gas fires. Natural ventilation through hit & miss wall vents. No mechanical ventilation to kitchen or bathrooms.
After: Warm air distribution from the Nilan Compact P XL combined heating & ventilation unit. Passive House Institute certified to have heat recovery efficiency rate of 80 per cent. The Compact P unit uses the return air heat exchanger to pre-heat supply air being distributed to the house, and for hot water with its integral DHW tank. Space heating supplemented by three Dimplex Girona electric panel convector heaters, located in circulation areas. The electric heaters are controlled by the Nilan unit and only switched on when the return air temperature for the whole house falls below the temperature designated by the user on the Nilan unit. In addition, a supplementary buffer hot water tank is pre-heated (when excess solar PV production allows) and raises the water temperature to the Nilan unit to reduce energy consumption.
Green materials & measures: Keim EcoSil mineral paint (solvent free, non-allergenic, odourless and breathable); Partel Alma Vert thermal break (made from recycled PET material); Keracoll Cementoflex cement-based resin floor topping.
Electricity: 10 square metre Sunpower solar photovoltaic array with average annual output of 2.34kWh. Surplus electricity generated is diverted to the hot water buffer tank. Point provided for future electric vehicle charger.
Image gallery
https://passivehouseplus.ie/magazine/upgrade/onwards-and-upwards#sigProIdfc9c24023f