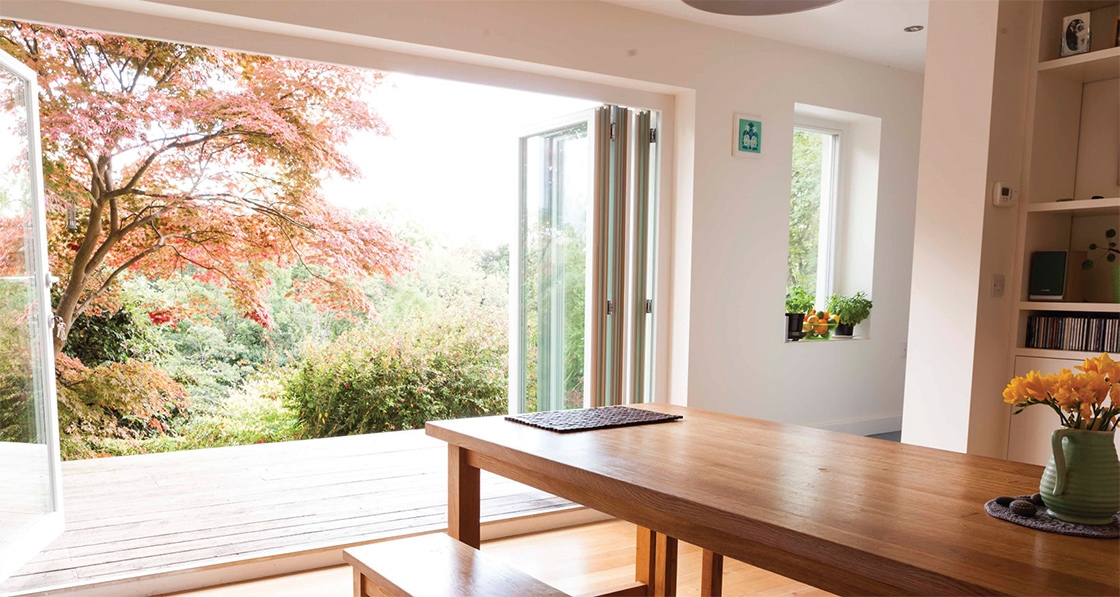
- Upgrade
- Posted
Bristol deep retrofit proves worth with monitoring
This unique energy retrofit in Bristol walked a fine line between ambition and pragmatism to deliver a healthy, comfortable and ultra-low energy home
Click here for project specs and suppliers
This article was originally published in issue 14 of Passive House Plus magazine. Want immediate access to all back issues and exclusive extra content? Click here to subscribe for as little as €10, or click here to receive the next issue free of charge
Deep retrofits can sometimes go so far that they’re effectively new builds in everything but name. Others tinker at the edges of the thermal envelope without really tackling the building’s fundamental problems. This Bristol retrofit and extension is different. Here, the design and build team expertly walked the line between the possible and the practical, to deliver high comfort, low energy living.
Ian Mawditt — owner and designer of the project — is an independent building performance researcher. As such, he could hardly be better placed to embrace the challenges of retrofitting this 1962 detached two-and-a-half storey home, on the fringes of Blaise Castle Estate in Bristol.
Before moving to Bristol from Oxford, Mawditt and his wife Corinne had been thinking in terms of retrofit, if the right property came along. But when they pulled up outside the nondescript 1960s house they had arranged to see with the estate agent, they took one look and decided that it wasn’t for them.
“Both myself and my wife have a preference for older buildings, for things that have a bit of character about them. And this was lacking much external character.”
When they got inside however, they discovered that the house had been built into a hill, and that the back garden fell away steeply, putting the ground floor at tree-top level.
“It’s a bit strange,” says Mawditt. “You all of a sudden feel as if you’re in a rainforest out the back...The location was so fantastic that it made us look at the house differently. I looked around and thought, you know what? There’s something you could do here.”
In addition to recasting the building’s thermal and comfort profile, the project also involved converting a storage space on the lower ground floor into a kitchen/diner, and adding a side extension. The project also set out to address the house’s nondescript facade, and give it a more engaging aesthetic.
The key challenge on the build was apparent to Mawditt almost as soon as he pulled up to the house that first day. Like so many buildings of this era, concrete elements were everywhere, from the gutters to the steps to the balcony at the back. Great for stability, but not so good for thermal bridges. Everywhere he looked, he could see clear evidence that any attempt to upgrade the building envelope would be futile without tackling those thermal bridges.
The house featured a concrete finlock guttering system, but unlike the standard guttering systems we’re familiar with today, the finlock system is actually a structural element. “These gutters act as a gutter first,” says Mawditt, “but they also span all the way through to act as the wall plate, so they take the roof trusses, the rafters and the full roof load. In an ideal world, we would take the roof off completely, get rid of the gutters and put in a completely new, thermal bridge-free roof onto the building.”
New extension constructed from H+H Celcon high strength AAC masonry, which was insulated with 120mm of Kingspan Insulation UK Kooltherm
When he examined the roof more closely however, Mawditt saw that despite the fact that it was more than fifty years old, it was still in good condition. But he says that while the ideal solution would have been to install a completely new roof, doing so would have blown his budget.
“I realised that I couldn’t justify skipping the whole roof and […] putting in a new one just to deal with thermal bridges. There had to be a more economic way of doing this.”
While Mawditt himself worked on the overall design, he brought in Ruairi Kay of Taylor Kay Architects to work up the detailed drawings that would guide the work and allow them to go to tender.
Kay had amassed significant retrofit experience working on the Retrofit for the Future programme run by the Technology Strategy Board (now Innovate UK), and had encountered houses of similar style and vintage to Mawditt’s.
Insulá thermal breaks used to prevent cold bridging at a steel column
Kay explains that he worked on eight separate solutions to the guttering problem, ranging from taking off the roof to leaving the gutter untouched and using internal insulation to mitigate the thermal bridge. The former, as Mawditt pointed out, was impractical, wasteful and expensive. The latter wouldn’t have gone far enough.
In the end, Kay explains, it was decided to cut the gutters flush with the existing walls, then bring up the external wall insulation as far as possible. “We extended the existing rafters and created a new eaves line,” he says, “plus we managed to get 60mm of Kingspan insulation across the top of the gutters. That was enough to bring the thermal bridges down to an acceptable level.”
Then there was the balcony. This was an extension of the ground floor slab that extended into the external space. Left as it was, it would conduct any heat energy directly into the outside. Mawditt and Kay decided to shear it off, again, flush with the existing building, and replace it with a wooden balcony. As with the gutter, this doesn’t eliminate the thermal bridge but it does reduce the problem to an acceptable level.
The Green Building Store Eco Contract triple-glazed timber frame windows were installed outside the existing brickwork, designed to sit flush with the new Kooltherm external insulation
Pragmatic solutions were also applied to some of the more endemic issues on the house. “Certain concrete elements are there to anchor the house into the hill,” Mawditt explains. “These created thermal bridges that were simply too difficult to deal with. On the south side, where the original concrete steps are cast against the house, all we could do was install some internal insulation on the other side to minimise, but not eliminate, the thermal bridges.”
Ruairi Kay says that the challenges posed by the project are typical of retrofits on houses of this era. Dealing with them, he says, requires a subtle blend of expertise and compromise. “It’s definitely a major problem. All these fifties and sixties properties tend to have a lot of concrete detailing, but it’s a balance between finding a practical solution that’s also thermally effective without pulling the whole thing down.”
Once the thermal bridges were dealt with, upgrading the thermal envelope was the next priority. Mawditt relied upon external wall insulation, together with passive standard, timber framed, triple-glazed windows.
There were also challenges to getting the insulation strategy right. Mawditt explains that he removed and lowered the original slab in the new dining area on the lower ground floor to increase headroom and to provide the opportunity to insulate the floor. That however was an expense he couldn’t justify in the existing utility room on the same level. “This meant that our options for insulating the existing floor slab were limited because we didn’t want to further reduce the low floor-to-ceiling height [at 2.1m] much further. Even 100mm of insulation was out of the question.”
The compromise here was a 20mm layer of Spacetherm, which uses Aerogel insulation. This is an ultra-high performance — and consequently expensive — insulant that’s bonded to chipboard, which was laid directly over the original floor. You don’t get the same thermal standard as the rest of the house, but that 20mm has cut heat loss through the utility floor by almost 60%, reducing the U-value from 0.59 to 0.25.
With an eye to what might be learned from the experience, Mawditt deployed a range of sensors and data loggers about the house, both before and after the build. He’s now been through two heating seasons since the work was completed, and the results make for fascinating reading.
Take overheating for example. Mawditt points out that a misconception has grown in the last few years that low energy houses are somehow more prone to overheating than ‘traditional’ houses. He notes too that as the pressure for space grows, it’s become increasingly common to put bedrooms into roof areas that used to be ventilated loft space.
“When you start building into the roof, if you don’t deal with the overheating potential, and try to dilute some of the solar radiation, you’re going to have an overheating issue, particularly in that room, and that will transfer down to the lower rooms.”
Before the retrofit, the summer temperature in the bedrooms reached an unbearable 35C. Since the project was completed however, the data loggers have recorded maximum summer temperatures of 26C in the bedrooms.
In part this is thanks to the external placement of the insulation. During the winter, it keeps the heat from escaping from the house, but during the summer, it keeps it from getting in. In addition, the render layer on the outside is deliberately light in colour, so that it radiates away solar energy rather than absorbing it. Additionally, the new windows have much better solar control.
Based on monitoring data, overall energy use in the house has been reduced by 73%, while the energy required for heating alone is down 90%. In the year before the works were completed, the total gas bill came to £1200. In the first year after completion, gas costs for both space and water heating came to £225.
Mawditt had anticipated that total space heating demand would just about meet the Enerphit standard of 25 kWh/m2/yr. In the first year, however, it didn’t get above 14 kWh/m2/yr, and following further tweaks to the system, it’s now down to 12 kWh/m2/yr.
He notes too that he inherited a relatively new boiler from the previous owner that is grossly oversized for the house’s heating needs, but he plans to replace it in future.
One other interesting finding is that the total energy costs for the MVHR system amount to £37 a year (plus £50 a year for filters), which again shatters the misconception that running two fans constantly requires a lot of energy. “Thirty seven pounds,” says Mawditt, “is a small price to pay for comfort and good indoor air quality.”
His monitors also tracked relative humidity (RH) and CO2 concentrations. RH should lie between 40% and 60%. Much lower than 40% can lead to a feeling of dryness and discomfort; much higher than 60% can lead to condensation and mould growth.
Average relative humidity in the main bedroom came in at 57% in the first year post-renovation, within the comfort band, but slightly high due to the recent re-plastering of the room and the associated moisture content. The average relative humidity on this floor has since fallen to 48%.
Mean CO2 levels should ideally be within 1500ppm. The ventilation system air flows have been commissioned to ensure this threshold is not exceeded, which has been confirmed by the logged data.
“The logged data shows that it’s a very stable environment from a temperature and humidity point of view.” says Mawditt. “The MVHR system is fine-tuned to keep CO2 levels under control. The comfort is quite remarkable compared to its pre retrofit state, between winter under-heating and summer overheating. And comfort is something that should be emphasised as much as energy.”
For more information about this project visit: fourwalls-uk.com/blog. Ian Mawditt, owner and designer of the project, is an independent building performance researcher. Originally an M&E engineer, he returned to university some years ago to complete a masters in sustainable architecture. Since establishing his own business, his key professional activities include field-based building research in new and existing buildings, evaluating energy performance and targets, and occupant comfort. Much of this research has been used to support various revisions to the building regulations and related approved documents for Part L and Part F. He is also an expert advisor to the Technology Strategy Board (now Innovate UK) on both their Building Performance Evaluation and Retrofit for the Future Programmes.
Selected project details
Clients: Ian Mawditt & Corinne Welch
Design: Ian Mawditt & Taylor Kay Architects
Energy rating assessment: Ian Mawditt
M&E engineer: Ian Mawditt
Main contractor: Greenheart Sustainable Construction
Heating engineer: Bent Copper Plumbing
Electrical engineer: Kilo Electrical
Extension roof and sedum layer: Poole Single Ply
External wall insulation: Kingspan
Internal Wall Insulation: Natural Building Technologies
Cavity wall insulation: Ecobead
Blown cellulose insulation: Warmcel
Windows, doors & heat recovery ventilation: Green Building Store
Roof windows: Velux
Airtightness products: Ecological Building Systems
Magnesium silicate boards: Resistant Building Products
Rainwater harvesting: Rainwater Harvesting Ltd
Thermal breaks: Insulá
Existing floor insulation: Spacetherm, via the Passivhaus Store
AAC blocks: H+H
Additional info
Building type: 1960s two-and-a-half storey detached cavity wall house with new extension. Floor area of 188 sq m.
Location: Bristol, England
Project budget: £155,000
Space heating demand (SAP 2009):
Before: 170 kWh/m2/yr
After: 17 kWh/m2/yr
Primary energy demand (SAP 2009):
Before: 361 kWh/m2/yr
After: 58 kWh/m2/yr
Energy performance certificate (EPC):
Before: E 46
After: B 89
Measured space heating consumption:
Before: 140 kWh/m2/yr (Oct 2010 to Sep 2011)
After: 12 kWh/m2/yr (Oct 2014 to Sep 2015)
Gas consumption (heating and hot water):
Before: 158 kWh/m2/yr (Oct 2010 to Sep 2011)
After: 26 kWh/m2/yr (Oct 2014 to Sep 2015)
Electricity
Before: 27 kWh/m2/yr (Oct 2010 to Sep 2011)
After: 15 kWh/m2/yr (Oct 2014 to Sep 2015)
Total measured energy consumption (gas and electricity):
Before: 185 kWh/m2/yr (Oct 2010 to Sep 2011)
After: 41 kWh/m2/yr (Oct 2014 to Sep 2015)
Gas bills
Before: £1230 (Oct 2010 to Sep 2011)
After: £225 (Oct 2014 to Sep 2015)
Airtightness (at 50 Pascals)
Before: 18.6 m3/hr/m2 at 50 Pa
After: 1.4 m3/hr/m2 at 50 Pa
Walls
Before: Existing masonry cavity wall
(60mm cavity unfi lled). U-value: 1.4 W/ m2K
After: Existing masonry cavity wall infilled with Ecobead+ (nominal 60mm depth). Cavities edge-sealed at top. External wall insulation applied using 2 x 60mm layers of Kingspan Kooltherm K5 over a sand/ cement slurry coat (air barrier). Finished in render or ventilated timber cladding. U-value: 0.12 W/m2K
Internal wall insulation applied in some areas where special restrictions limited the ability to continue external insulation (e.g. south wall section on lower ground fl oor). Internal wall insulation used instead, limited to 100mm + cavity wall insulated with Ecobead. U-value: 0.17 W/2mK
Extension walls: H+H Celcon high strength AAC masonry – 190mm 7.3N/ sqmm blocks. Insulation/air barrier/ fi nishes as per existing walls. U-value: 0.14 W/m2K
Timber infill section walls: Timber ladder frame infilled with 145mm Kooltherm K5 + 120mm external wall insulation (265mm insulation total). U-value: 0.10 W/m2K
Existing roof
Before: original roof, cold loft, timber with concrete tiles. 50mm nominal insulation with vermiculite, poorly laid, causing condensation in winter. U-value (nominal): 0.75 W/m2K
After: Existing roof insulated using Warmcel blown in to a depth of 300mm, with a further 300mm on top/around MVHR ducting. Area-weighted U-value: 0.1 W/m2K
New roof to extension: Flat, warm roof construction made up from 20mm marine ply taped with Tescon No.1 tape, with Alutrix 600 vapour control layer and 150mm Kingspan Thermaroof TR26 laid on top. Cefi l single ply membrane laid over insulation, topped with sedum layer dressing. U-value: 0.14 W/m2K
Windows & doors
Before: Mixture of single-glazed, timber windows and doors, and double-glazed uPVC windows. Overall approximate U-value range: 2.4 to 3.2 W/m2K
After: New triple-glazed timber frame windows with double low-e coating (4/16/4/16/4) and argon fill. All as per Green Building Store Eco Contract range. Overall U-value of 0.90 W/m2K
Roof windows: Three Velux triple-glazed units on fl at roof. Overall U-value: 0.85 W/ m2K
Heating system
Before: New A-rated (SEDBUK 89.2% eff) gas boiler installed by previous owner, but connected to the original single pipe, conventional open vent system, utilising skirting radiators throughout entire building.
After: Boiler retained, but connected to a new sealed twin pipe system. Radiators are small panel type, between 300 and 500 watts depending upon room size. Minor efficiency issue – boiler is now grossly over-sized (size for a big ineffi cient building), meaning that it runs less effi ciently. It was felt wasteful to discard such a new boiler, but it will eventually be replaced with a smaller unit.
Ventilation
Before: No ventilation system. Reliant on infiltration, chimney and opening of windows for air changes.
After: Paul Novus 300 heat recovery ventilation system. EN 308 certifi ed effi ciency of 94.4%. All ducting is Lindab SAFE galvanised steel – double sealed, airtight installation.
Green materials: Cellulose (loft) and wood fibre (IWI) insulation materials used. Sedum extensive roof layer dressing to extension roof.
Image gallery
https://passivehouseplus.ie/magazine/upgrade/bristol-deep-retrofit-proves-worth-with-monitoring#sigProId8f2569dcc4