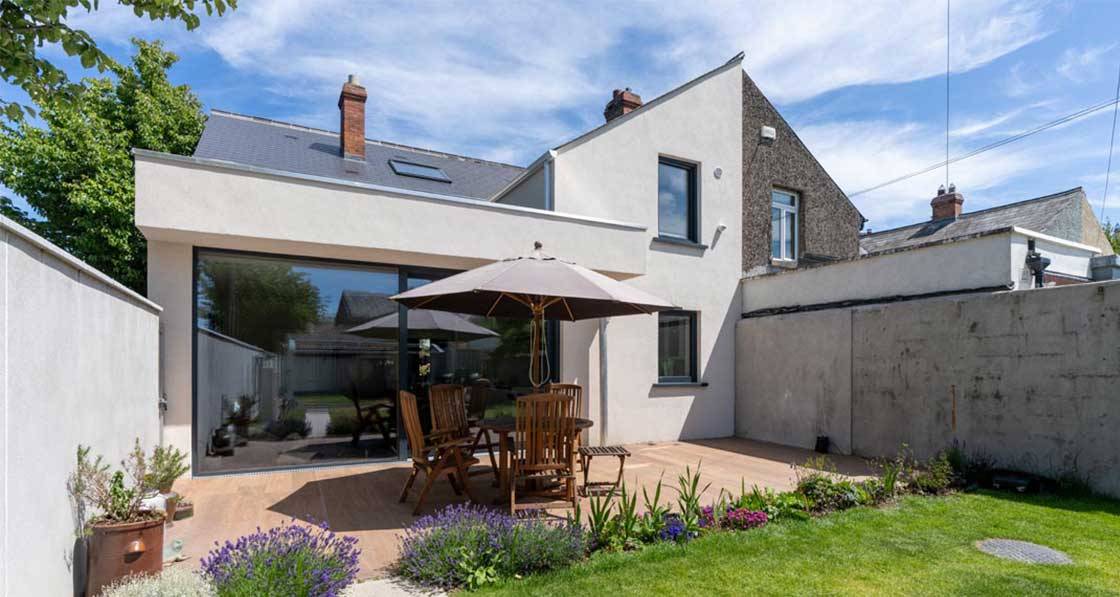
- Upgrade
- Posted
Breath of life
The skilful deep retrofit of a red-brick semi on the south side of Dublin has brought an old property into the 21st century in terms of energy performance and living space, while carefully upgrading its century-old façade with breathable materials.
Click here for project specs and suppliers
Building: Deep retrofit & extension of 1920s semi-d
Method: External insulation, breathable internal insulation, single leaf thermal block extension
Location: Rathgar, Dublin
Standard: Enerphit (certification pending)
Heating cost: €24/month*
*Space heating use only, modelled based on measured energy use. See ‘In detail’ panel for more information.
A year after their house in South County Dublin had been retrofitted to the Enerphit standard, owners Brendan and Geraldine decided to apply for certification to the Passive House Institute. But to be certified as having met the Enerphit standard, new airtightness tests would have to be done.
“Going back to do airtightness tests a year after completion isn’t ideal,” says architect and passive house designer, Mel Reynolds. “Normally you’d try and do your final test as close to when you complete as possible because buildings settle, doors warp, seals come loose... There was one sliding door that was in constant use. I was sure that there would be problems there.”
It’s a measure of just how well executed the project was that the blower-door test registered 0.9 air changes per hour – inside the Enerphit standard of 1.0 – on the first go. Neville Road in Rathgar is a 1920s development of red-brick semi-detached homes, and this is the last house in the row. Brendan grew up in the house, and was now returning to live there with his own family.
Prior to the refurb, there had been a dilapidated single-storey lean-to extension to the side. This was set to be demolished and replaced with a single-storey rear extension and a two-storey side extension. Though it had been lived in continually, by the time the project began in 2020, the house felt a little unloved. Both wiring and plumbing needed extensive work, and the windows and doors were in need of replacement, while the layout of the rooms belonged to another time.
“It was always going to be a deep retrofit,” says Reynolds. He notes too that the initial design specified a larger extension, but that before finalising the layout, he and the clients took a closer look at the family’s space requirements. “I’d recommend that anyone considering an extension, first look at the space that you use every day.”
It can be a very revealing exercise because it invariably uncovers areas that are either being under used or not used at all. “A lot of us think, ‘I don’t have enough space, I need to extend the house,’ but hang on for a minute. Are you using all the space you’ve got well? Are there any spaces that you don’t use? Maximise what you have before looking at extending.” The family wanted to retain as many of the old features of the house as possible, while at the same time creating spaces more attuned to how we live today: open plan living areas, additional bathrooms and bedrooms upstairs. The brief also included a self-contained studio apartment/office space, to cater for the needs of family members as they change.
This article was originally published in issue 42 of Passive House Plus magazine. Want immediate access to all back issues and exclusive extra content? Click here to subscribe for as little as €15, or click here to receive the next issue free of charge
“The extension is almost invisible from the outside,” says Reynolds, “the front façade is very low impact, very understated, but when you walk in the front door to the central area, all of a sudden you have a double height, cathedral space with an overhead walkway linking with the master bedroom.” Downstairs, the open plan kitchen/living room connects directly to the garden via a large sliding door. “In going from the master bedroom to the kitchen, you experience seventy per cent of your house; you’re not simply being threaded through it, while the double height brings the whole lot together.”
The story of the Neville Road deep retrofit really begins with an earlier Mel Reynolds project, the country’s first passive house ‘plus’ project, which was Reynolds’s own house at Cove Mews in Sandycove, a project featured in issue 35 of Passive House Plus. While working on this project, Reynolds was struck by how well several of the building solutions he implemented there would work on a refurb.
Airtightness is always a challenge when you’re retrofitting, but two things served to make the process surprisingly smooth on Neville Road. The first was that the builder on Cove Mews – Sean Regan – also won the tender here, and so was equally familiar with the solutions deployed in the earlier project.
Maximise what you have before looking at extending.
The second was one of those solutions: Blowerproof liquid airtight membrane. This is a BBA certified product with Class C fire rating which has been used in Europe for some time. It’s a paint-on product.
In the new parts of the house, there was no need to batten out the walls or attach a screw-fixed plasterboard. Instead, the build team used dot and dab plasterboard, while in the older part of the house, the liquid membrane was simply applied to the existing plasterwork.
“It didn’t take Sean any more than a week to get to a preliminary airtightness level of 0.9. Because he had done Cove Mews, airtightness here was a doddle. No need for all the tapes and things we used to use in junctions and in floors, which were really laborious. With this, you’re simply spraying it on. It’s perfect... The lesson for any contractor with these onerous, difficult-to-achieve standards is that when you’ve done it once, that’s it, it’s easy.”
While existing plasterwork was retained inside the house, the design team decided to replace the suspended timber floor with an insulated concrete slab featuring 50 per cent Ecocem GGBS. Walls are externally insulated where possible. The red-brick front façade was of course retained, and faced internally with a 60 mm Calsitherm board. Calsitherm is a breathable calcium silicate board, made from a mix of lime and sand, which is capable of regulating dampness in walls by absorbing it and then allowing it to evaporate and dry out. The design team conducted condensation risk analysis to determine the optimum thickness of the interior board.
“When you have a protected façade or brick – as in this case – you insulate as much as you safely can and then compensate on other areas. That’s what we did here. In the end, our provisional rating was A1. Brendan mentioned that a scheme of very expensive new houses had just been launched not too far away from this one, and they were A2 rated. So, this 1920s build was delivering a better performance than those lavish new homes.”
The original house relied on infiltration and opening windows for ventilation. The refurbished house uses Lunos decentralised heat recovery ventilation units from Partel, a technology which Reynolds came across before but hadn’t found the right opportunity to deploy.
Brendan grew up in the house, and was now returning to live there with his own family.
“Centralised mechanical heat recovery ventilation is great, you have ducts, you have a single unit and your efficiency is very high, but in existing buildings, fitting a centralised system is a real challenge because you don’t have the space for ducts, you don’t have the voids, plus you might have to retain ceiling details like cornicing.”
By contrast, Reynolds says decentralised systems are ideal in retrofits. You install vents, bring power to them and each is commissioned individually.
“All they need is power, you don’t have any interruption to your ceilings or floors and the cost to run them comes to a total – across the whole house – of between €10 and €12 per year. It’s a brilliant concept for existing buildings, particularly when you want to get your airtightness down to passive levels.”
Construction in progress
-
Construction underway of the two-storey side extension constructed of Mannok Aircrete blocks Construction underway of the two-storey side extension constructed of Mannok Aircrete blocks
-
Delivery of the large glass patio door with pre-fitted brackets for the new rear extension Delivery of the large glass patio door with pre-fitted brackets for the new rear extension
-
Internorm triple glazed aluminium-clad oak units sitting proud of the blockwork to keep continuity with the external insulation layer Internorm triple glazed aluminium-clad oak units sitting proud of the blockwork to keep continuity with the external insulation layer
-
Carefully applied Siga airtight tape seals the joist ends and stud walls to the Mannok blocks Carefully applied Siga airtight tape seals the joist ends and stud walls to the Mannok blocks
-
Wetroom tanking to wall of master bedroom ensuite at first floor level, pre tiling Wetroom tanking to wall of master bedroom ensuite at first floor level, pre tiling
-
Blowerproof to inner surface of Mannok block walls with surface-mounted slimline boxes and conduits – no chasing required before dab and slab applied as internal finish Blowerproof to inner surface of Mannok block walls with surface-mounted slimline boxes and conduits – no chasing required before dab and slab applied as internal finish
-
60mm Calsitherm board applied to existing solid brick front bay wall with Blowerproof repairs behind (airtight layer on inner surface of existing wall) and Calsitherm applied to reveals 60mm Calsitherm board applied to existing solid brick front bay wall with Blowerproof repairs behind (airtight layer on inner surface of existing wall) and Calsitherm applied to reveals
-
Siga Majpall airtight membrane to double height ceiling Siga Majpall airtight membrane to double height ceiling
https://passivehouseplus.ie/magazine/upgrade/breath-of-life?highlight=WyJ3ZWxscyIsIndlbGwiLCJ3ZWxsZSIsIndlbGxuZXNzIiwid2VsbGluZyIsIid3ZWxsIiwid2VsbCciLCJ3YXRlciIsIndhdGVycyIsIndhdGVyJ3MiLCJ3YXRlcmluZyIsIndhdGVyZWQiLCJiaWxsIiwiYmlsbHMiLCJiaWxsaW5nIiwiYmlsbGVkIiwiYmlsbCdzIiwiYmlsbCciLCJiaWxsaW5ncyIsImJ5IiwiYmlsbCBieSJd#sigProId13196c3507
He continues: “The back elevation of the house has a unified, modern look, without fascia boards, so that internal roof insulation meets external wall insulation in one continuous layer, thereby eliminating thermal bridges. It’s a very elegant detail architecturally but it also has the added benefit of delivering high performance.”
In the year up to the beginning of the project, the house had been occupied by two people – Brendan & Geraldine’s son and partner. When the retrofit was completed in late 2020, Brendan, Geraldine and their adult son Thomas moved in, with the occupancy doubling the following summer, when Brendan and Geraldine’s son John moved in with his partner and their baby.
During the two-person occupancy pre-retrofit, total energy used over a twelve-month period came in at 3,151 kWh of electricity and 11,103 kWh of gas. From May 2021 to May 2022 – a period including six occupants from June to January – total energy use came to 8,551 kWh. But how would the house fare with half the number of occupants, as current? Cue energy modelling expert Tim Cooper, who devised a way to deduct the impact of increased occupancy, and account for the house drying out and the homeowners learning to use the new systems in the house – factors which substantially affected the building’s energy use.
Cooper developed an energy performance model for the house, taking account of the extra demand placed on the house for showering, space heating, cooking, refrigeration, washing and other appliance use – and taking account of the rated power use of the actual appliances in the house. The usage assumptions were corroborated by Brendan.
Space heating increases were assumed from the house drying out and the occupants learning how to use the new heating system. The net result: total energy use reduced from an unadjusted total of 8,551 to 6,290 kWh/yr. Of this, 1,452 kWh was attributed to space heating demand, at a cost of less than €24 per month based on current electricity prices.
With the risk of rocketing electricity prices obscuring some of the energy savings accruing from the refurb, the clients decided to install PV panels after the project had been completed. Planning permission was granted for panels on the back of the house, but analysis by Tim Cooper - who is also arguably Ireland’s leading expert on PV – revealed that chimney overshadowing would be an issue. So instead, the design team created a carport with a butterfly roof, and eight panels are due to be installed in the coming weeks.
Going back to do airtightness tests a year after completion isn’t ideal.
Cooper predicts that once the PV array is in place - and using a dynamic model to project the output of the array on a granular level throughout the year, against his granular model of the building’s energy use – the array will reduce grid energy use to 4,181 kWh/yr. This is based on the planned installation of an eight panel (2.96 kWp) PV array. Cooper’s projections – based on the measured output of a similar array on a local project – to be 2,447 kWh/yr, including 1,427 kWh of useful energy, and 1,021 kWh to be exported to the grid. Cooper projects that the useful energy generated by the array will knock over €330 off the house’s electricity bill.
Like so many houses of its vintage, Neville Road was draughty and hard to heat, which is part of the reason why the clients specified underfloor heating throughout the refurb. When the team ran the design through the Passive House Planning Package (PHPP) software however, it suggested that underfloor heating was surplus to requirements. It was retained – just in case – but two winters in, it’s hardly been used.
Like many designers before him, Reynolds pays tribute to PHPP as a design tool. On a different project, the software suggested that the radiators that had been specified were unnecessary upstairs.
“Again, just in case, we put in flow and return for the rads, but left the rads themselves out. That saved the clients about €3,000. If they wanted them later, they could put them in easily… And last year, we had supply chain problems, but if one insulation is unavailable, you can put the spec of a potential replacement into the software and it will tell you if it’s going to work or not.”
Hidden beneath the back garden of the Neville Road Enerphit, there’s a 5,000-litre rainwater harvesting tank which is plumbed to the WCs. This makes the house a lot more self-sufficient, and guards against the impact of water charges if and when they return.
And as Reynolds points out, the cost of installing rainwater harvesting during refurb is far cheaper than doing so after the fact.
Rainwater harvesting should be in all retrofits and new builds.
“I think rainwater harvesting is something that should be in all retrofits and all new builds, and should be incentivised. It just makes no sense to use potable water that we have already treated to flush toilets. So don’t buy an expensive sofa. Get one in Ikea and install a rainwater harvesting system instead.”
Selected project details
Architect & passive house design: Mel Reynolds
Main contractor: Sean Regan Ltd
Quantity surveyor: Damian Bowers & Associates
Services engineer: Mike Kelly & Associates
Structural engineer: Carraig Consultants
Health & safety: Safety Solutions
Passive house certification & thermal bridge analysis: Earth Cycle Technologies
Renewable energy consultant: Tim Cooper Conservation Engineering Consultant
Roofing: KD Roofing
Mechanical contractor: Mountain Lodge
Mechanical Services Electrical contractor: Thomas Kenny & Co
Heat pump: Heat Merchants
Decentralised MVHR: Partel
Ironmongery: Ecco Architectural Hardware
Solar PV consultant: Tim Cooper Conservation Engineering Consultant
Underfloor heating: Unipipe
Windows & doors: Internorm, via Eco Window Concepts
Rooflights: Velux, via Tradecraft
Blockwork: Mannok
Rigid insulations: Kingspan
Mineral wool: Isover
Calcium silicate board: Ecological Building Systems
External render: Baumit
Airtightness tapes/membranes: SIGA
Liquid airtight membrane: Blowerproof Ireland
Flat roofing: Moy Materials
Thermal breaks: Compacfoam, via Partel
Concrete containing 50 per cent Ecocem GGBS: Kilsaran
FSC certified timber: Glennons
BER: SC Airtightness & Ventilation
Rainwater harvesting: Wastewater Solutions
Metal fabrication: Dunfab Engineering
Sanitaryware: Bath House
Kitchens: Timbercraft
In detail
Building type: 167.4 m2 semi-detached house from 1928. Works included 46.7 m2 part demolition of existing building and single-storey lean-to side garage, Enerphit refurbishment with new single-storey rear extension and two-storey side extension of 67.9 m2. Total completed net floor area 188.6 m2.
Location: Rathgar, Dublin 6
Budget: N/A
Completion date: October 2020
Enerphit certification: Pending
BER (before): F
BER (after): A1 (provisional)
Heat load: 13 W/m2
Primary energy demand (PHPP): 45 kWh/m2/yr
Primary energy renewable (PHPP): 25 kWh/m2/yr
Heat loss form factor (PHPP): 2.79
Overheating (PHPP): 1 per cent (of hours above 25 C)
Number of occupants: 3
Measured energy consumption
Before: 3,151 kWh (electricity) and 11,103 kWh (gas) over 12 months pre-retrofit, with two occupants in the house. Total: 14,254 kWh
After: (May 2021-May 2022) 8,551 kWh total consumption (all-electric) over one year post-retrofit, but with three occupants for four months, and six occupants for eight months. An energy model from Tim Cooper produced an adjusted figure for three occupants, allowing for the house drying out and homeowner learning to use the building, of 6,290 kWh/yr. This includes 1,452 kWh for space heating. Passive House Plus took the cheapest tariff available on Bonkers. i.e., as of 3 July 2022 of 19.69c (based on smart meter, urban connection, without night meter), meaning the portion of energy use for space heating comes in at €286/yr, or under €24 per month. Standing charges were excluded from this calculation, as they are incurred at the same rate merely by having an electricity connection. In fact, the decision to switch from gas to electricity for heating avoided incurring a second standing charge - ranging from €104 to €187/year, depending on the supplier. This reduction was not factored into these calculations. Airtightness (at 50 Pascals): 0.9 air changes per hour.
Floor
Before: Uninsulated timber ventilated floor in main section of house with solid concrete uninsulated slab to original side garage. U-value: 1.85-3.48 W/m2K
After: 150 mm thick 50 per cent GGBS RC slab insulated with 270 mm Kingspan K3 insulation. U-value: 0.073 W/m2K
Walls
Before: 300 mm solid masonry walls. U-value: 0.65-0.80 W/m2K
After (generally): Acrylic external render on 140 mm Kingspan EWB insulation, on 300 mm existing masonry wall with 15 mm existing render, with Blowerproof airtightness paint (as required), with 12.5 mm plaster on 15 mm dabs internally. U-value: 0.12 W/m2K
After (brickwork front elevation): Existing brick-faced 300 mm masonry wall with 15 mm existing render, with Blowerproof airtightness paint (as required), with 60 mm Calsitherm board skimmed internally. U-value: 0.585 W/m2K
Roof
Before: Sloped with mineral wool insulation. Roof slates to sloped areas and torch-on-felt to flat roof areas externally. 75 mm mineral wool insulation on the flat between roof joists and a combination of suspended ceiling tiles or plasterboard ceiling internally. U-value: 0.47 W/m2K
After: Min 50 mm ventilated space retained between underside of existing slates and top of 100 mm Kingspan K7 Thermaroof insulation friction-fitted between rafters with counter-battens, and 100 mm Kingspan Thermaroof insulation to underside (200 mm total), with Siga vapour membrane and 13 mm plasterboard finish internally. U-value: 0.134 W/m2K
Extension new walls: Acrylic external render to 140 mm Kingspan EWB insulation, to 215 mm Quinn Lite B5 blocks, Blowerproof liquid airtight membrane, 12.5 mm plaster on 15 mm dabs internally. U-value: 0.12 W/m2K
Extension flat roof: Paralon NT4 2-ply roofing membrane on 120 mm Paratorch insulated board, on 18 mm OSB on timber joists, with 210 mm infill Kingspan K7 insulation and 15-90 mm Isover Metac insulation, on 15 mm OSB board underside, with 25 mm service cavity and 12.5 mm plasterboard internally. U-value: 0.10 W/m2K
Windows & doors
Before: Single glazed timber windows and doors. Overall approximate U-value: 3.50 W/m2K
After: Internorm triple glazed aluminium-clad oak windows, with argon filling and an overall U-value of 0.73 W/m2K; G value 0.6
Roof windows: Velux triple glazed window No 68. Centre pivot, electrically operated pine finish internally. Overall U-value: 1.1 W/m2K
Attic hatch: Wellhöfer Passive House Institute certified airtight hatch
Heating system
Before: 20-year old gas boiler & radiators throughout.
After: Panasonic Aquarea air source heat pump with Harp database registered COP of 4.74, delivering to underfloor heating throughout, fitted with integral hot water cylinder.
Ventilation
Before: No ventilation system. Reliant on infiltration, chimney and opening of windows for air changes.
After: Lunos decentralised E260 and Ego ventilation units. E260 has maximum efficiency of 96 per cent and 88 per cent to EN13141-8. PHI adjusted efficiency for this project is 75 per cent, with specific power consumption = 0.11 W/m3/h. E260 is the only decentralised fan with S1 wind class protection, and costs from €10 to €20 per annum to operate the system including filters.
Water: FLine Diver 5,000 litre rainwater harvesting tank supplying all irrigation and WCs. All sanitary fittings are low-flow 9 litres per min.
Green materials: A 50 per cent GGBS cement used in all in situ-concrete, aerated blockwork throughout with FSC certified timber in all areas. All ground surfaces are permeable.
Electricity: Yet to be installed. Plan is for 8 x 340 W peak PV modules, prioritised over heat pump for generating hot water.
Image gallery
https://passivehouseplus.ie/magazine/upgrade/breath-of-life?highlight=WyJ3ZWxscyIsIndlbGwiLCJ3ZWxsZSIsIndlbGxuZXNzIiwid2VsbGluZyIsIid3ZWxsIiwid2VsbCciLCJ3YXRlciIsIndhdGVycyIsIndhdGVyJ3MiLCJ3YXRlcmluZyIsIndhdGVyZWQiLCJiaWxsIiwiYmlsbHMiLCJiaWxsaW5nIiwiYmlsbGVkIiwiYmlsbCdzIiwiYmlsbCciLCJiaWxsaW5ncyIsImJ5IiwiYmlsbCBieSJd#sigProId6932df5a69