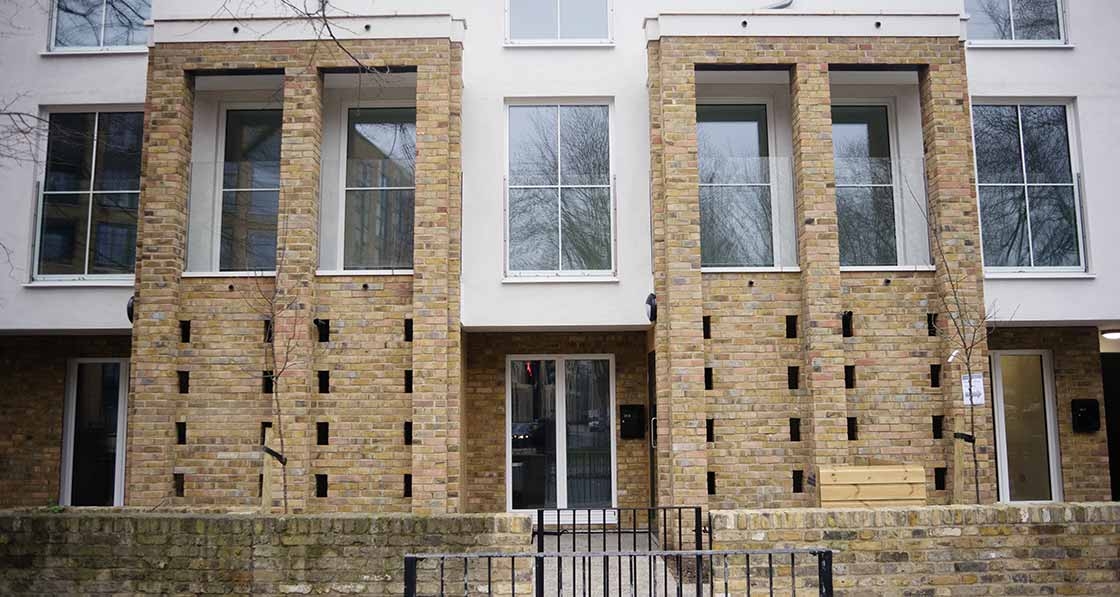
- New build
- Posted
South London scheme delivers better health for residents
A sensitive development of social housing in Lambeth combines three new passive houses with six low energy flats delicately constructed inside an old Victorian terrace — and with the emphasis on good indoor air quality, residents are already reporting improvements in health & well-being since moving from their old accommodation.
Click here for project specs and suppliers
£99 (new build) & £78 - £200 (retrofit) per year for space heating only.
Buildings: Three new four-bedroom terraced passive houses & six low energy flats retrofitted into a Victorian terrace
Standard: Certified passive new build & low energy fabric-first retrofit
Location: Akerman Road, Lambeth, London
Completed: December 2016
Total budget: £2m
Build method: Timber frame new build / deep retrofit with internal insulation to Victorian terrace.
Back in the spring, nine households received the keys to their new social rented homes from Lambeth Borough Council. Three of these are new four-bedroom terraced houses, built to the passive house standard, and the first new social housing built by Lambeth council for ten years. The other six are low energy flats, carefully retrofitted into the two Victorian houses next door.
This development, on Akerman Road in the heart of the borough, is something of a mini shop window for Lambeth’s much wider plan to redevelop its existing estates and build 1,000 new homes to tackle the acute housing shortage in the area.
But this was not the easiest site to develop. Sitting in a conservation area, one of the existing houses has a local listing. The Victorian houses also had to be completely reconfigured from their previous use as temporary hostel accommodation, while preserving the original façades.
The new dwellings, which re-connect the existing houses to their neighbours across a vacant bombsite, also had to meet strict visual criteria. And at the same time, the development needed to be completed within a realistic local authority budget, and be robust, easy to occupy and maintain. It also had keep the occupants safe, warm and free from large fuel bills.
The design was led by Anne Thorne Architects, who had worked with Lambeth on other redevelopments. But the project was a long time in gestation, Anne Thorne partner Fran Bradshaw explains: “The redevelopment was originally planned before the 2010 election, when the government was still spending on housing.”
Even though there was only a small passive house movement in the UK at the time, the terraced form dictated by the site would enjoy a good form factor, which encouraged the architects to design to the standard.
For the new-build infill, the conservation authorities wanted to convey the height and grandeur of an adjoining 19th century house, and were initially unhappy about the look of the new designs with their level access, which was required for the Lifetime Homes standard. So Anne Thorne Architects added two-storey brick porches to echo the flights of steps to the Victorian entrances. These did add expense and complication, but look right in the location and helped to win planning permission.
The retrofit also prioritised energy performance. As Huw Jones, housing development manager at Lambeth Borough Council, puts it: “We particularly like the fabric-first approach because of its simplicity. It avoids relying on expensive technologies that require long term maintenance and replacement, which can add to tenant service charges.”
However, having finally agreed a design with the planners and secured permission, progress stalled, and it was not until the planning permission was at risk of expiring that there was a window of opportunity to fund the build and proceed – so long as the team could get on site within four months. In the intervening years the UK’s passive house movement had expanded dramatically and Anne Thorne Architects had teamed up with a small group of design practices to form the 15:40 Collective, focusing on low energy fabric-first design to passive house and AECB building performance standards.
Anne Thorne Architects therefore enlisted the help of their colleagues in 15:40 to work up the design drawings to the highest performance standards while meeting the tight deadline. Everyone had to move fast. “With the very short time to get on to site, it was really good to have the 15:40 structure in place, to take on the construction designs for the retrofit and new build sides respectively,” Fran Bradshaw says.
This article was originally published in issue 22 of Passive House Plus magazine. Want immediate access to all back issues and exclusive extra content? Click here to subscribe for as little as €10, or click here to receive the next issue free of charge
Anne Thorne Architects kept the reins overall. Meanwhile Prewett Bizley Architects took on the detailed design of the retrofit, and CTT Sustainable Architecture (since superseded by Passivhaus Homes Ltd) worked up Anne Thorne’s designs into a fast-to-erect, passive house standard construction, using their own PH15 timber frame system.
New build
As Janet Cotterell of Passivhaus Homes explains, there was a pre-designed set of details, worked out carefully for minimal thermal bridging and ease of airtightness installation, so much of the design work had already been done. “We had all the details ready, they did not all have to be designed afresh for passive house, which would have been impossible in the time,” she says.
“Having the pre-designed details de-risks the project and saves a huge amount of time and people’s money. For me this is the really valuable thing about this construction system. It is such a waste of energy re-inventing the wheel each time.”
“Especially for the trickier elements, we were very careful about communicating the way the airtightness membranes were sequenced into the construction, and even sent some pre-cut and pre-taped corners for the carpenters to use,” Cotterell adds. The strategy worked, and the fabric of the new houses passed the airtightness test comfortably at 0.4 air changes per hour at 50 Pascals.
She believes carpenters are particularly well suited to passive house construction “because they are all about precision”.
The Passivhaus Homes PH15 timber frame system is hygroscopic and vapour-open, increasingly so towards the outside of the build-up, where it is finished with a very open lime render. The nature of hygroscopic natural materials means a certain amount of moisture can be bound to the fibres in the materials in the solid phase – the material holds moisture but is not wet. This is different from the behaviour of impermeable materials, which might suffer condensation under the same conditions, and which might not disperse moisture so readily either.
“I think it is unwise to assume water will never get into a structure,” Cotterell says, pointing out that no construction is perfect, and as the years go by, all buildings suffer damage and ageing. “The construction process may also allow some water in from the weather, and this needs to escape.”
“We worry that impermeable construction solutions, coupled with timber frame, may be setting up a future problem down the line, and give timber building an undeserved bad reputation.”
The retrofit
The detailed design of the retrofit was taken on by Anna Carton of Prewett Bizley. The two existing buildings had been in council possession for a long time, but had not undergone major works carried out since the 1980s. Described by the council as “generally habitable” the buildings were very ‘tired’ (or in council terminology, they had “significant asset liabilities”). And while some of the issues were already known, some only became apparent once work began. “The fabric was not in great condition: brickwork needed repair, there were roof leaks and damp in the basement, single glazed windows with rotten woodwork in the sashes and cills,” Anna Carton recalls.
Despite the challenges imposed not only by the old and slightly ropey fabric, but also the conservation status of the buildings, the client wanted to carry as many of the benefits of passive house design as possible through to the retrofit. This meant using high levels of insulation, high-performance windows and doors, careful design to minimise thermal bridging, and the installation of heat recovery ventilation.
As Huw Jones of Lambeth council puts it: “Passive house design allows people to live their lives. They can dry laundry indoors without worrying about cold draughts, they won’t suffer big energy bills.”
But first the plans had to get the go-ahead. “Everyone in this area understands how challenging it is to work with conservation officers,” Anna Carton says. “Getting agreement on the windows for example took about six months of going back and forth with different possible windows, and there were a number of objections, such as the thickness of the midrail, the drip details, etc. The Vrogrum sliding sash windows were finally accepted because they had the right curved heads.” “However just as important were the client’s requirements for the windows to be lockable, easy to operate and easy to keep clean, and not exorbitantly expensive.”
Meanwhile, new timber frame extensions to the rear for bathrooms and kitchens were insulated externally with Pavadry wood fibre insulation, but the front required internal insulation to preserve the street façade. Carton elaborates: “Timbers had been incorporated into the masonry by the Victorian builders, and as a couple of these at least were affected by dry rot, we removed them and repaired the bricks. We also cut away all the joist ends, parged the wall and then hung the joists away from the brickwork so they were out of capillary contact with the wall, which will be cooler and potentially damper after internal insulation.”
Dampness in the basement appeared to be coming from groundwater, so the team lowered the ground level externally to the front and rear. This was not possible at the north façade, so a studded drainage membrane and French drain were installed here. Inside, the bottom 1.2m of the lower ground floor walls were lined with waterproof render and closed cell insulation. Above this, the insulation was breathable Pavadry wood fibre boards. The team taped all joints in the internal insulation to keep the warm indoor air away from the masonry – especially important as social housing can be quite densely occupied, with high moisture production.
To minimise thermal bridges, the insulation under the slab was turned up to meet the internal wall insulation, and the internal insulation was also returned inwards along party walls and up the basement partition walls to isolate the rooms from the ground. Retrofitting a centralised mechanical ventilation with heat recovery (MVHR) system in an old building is tricky enough, but here, no duct terminals were permitted in the front façade, so some fiddly ductwork runs were needed that required false ceilings and ducts passing above staircases. Despite these difficulties, the team went ahead — the client wanted to share the benefits of good indoor air quality in all the dwellings. The MVHR will potentially save energy too, and the “cool recovery” function (when outdoor temperatures rise above indoor temperatures) should help with summer comfort.
Performance
Airtightness tends to be the biggest performance challenge when retrofitting an old building, and the finished retrofit here is less airtight than had been hoped — closer to 6.0 air changes per hour than the targeted 3.0.
“We suspect the issue may be at the interface between old and new structure at the back, which was quite tricky topologically. With all the parging and taping, we think the airtightness elsewhere was not too bad,” Anna Carton says.
Different flats ended up with different energy consumption figures because form factors and solar gains vary. The aim was to get to around 40-45 kWh/m²/yr of space heating demand, but with the missed airtightness target the team couldn’t get that low in all the units — the average is about 65 kWh/m²/yr.
Planning constraints potentially affected the performance of the new houses too, because of the requirement for tall façade windows in line with the neighbours.“With all the glass on the front façade, we had to work hard to get the overheating down,” Janet Cotterell explains. “With a combination of strategies like improved g-values and alterations to the window openings to enable more night ventilation, we managed to hold the overheating down to a figure 1.9% of hours above 25C in PHPP — allowable under passive house, but higher than we would ideally have liked.”
The design and build style of the contract (common to social housing procurement in the UK) meant that not all the final details of the construction could be nailed down by the design team as closely as with a conventional contract.
Thus Prewett Bizley were not involved with the air-testing of the retrofit, so they weren’t able to locate the weak points in the fabric. And a miscommunication about safety barriers meant that the purge ventilation openings on some windows in the retrofit are smaller than intended, though this is due to be resolved.
These kind of issues crop up quite frequently in design and build contracts, and 15:40 have now distilled their collective wisdom into procurement advice to social housing clients intending to build high quality, high performance homes.
They advise clients to ensure there is independent (from the main contractor) post-tender quality control on site, delivered by someone with good energy-efficiency knowledge, who reports directly to the client.
Handover
Occupants were taken through the ins and outs of their new homes at the time of moving in. Anne Thorne Architects is now working with a PhD student from University College London on a two-year post occupancy study, looking at energy use and bills, indoor air quality (CO2, humidity) and the perceptions of both residents and landlord. The post occupancy evaluation team found on the first visit, three months after occupants had moved in, that things still needed some explaining and adjusting.
This is far from unusual —on moving day new occupants are usually preoccupied, and people tend not to absorb everything in one go anyway. Quite often the first visit in a post-occupancy evaluation or ‘soft landings’ process ends up being an extension of the handover.
Arguably, landlords and developers should accept this as routine.
“Lambeth have been very good about this, they appreciate the importance of improving the handover process, particularly for explaining the importance of the ventilation and how to use it,” Fran Bradshaw reports. All nine of the households have now been interviewed and asked about their experience. Comments are generally very positive — occupants like the warmth, the space, and the garden with its mature trees and room to grow vegetables.
Residents were also asked specifically about their health, and whether anyone in the household suffered respiratory problems. In four households, at least one occupant suffered from asthma or other lung problems. Remarkably, all of these households reported that symptoms had improved. There was less need for medication, they reported, and one household reported that a child’s asthma had not been problematic at all since the move.
One mother commented: “My baby daughter had patches on her lung ... You could hear the raspiness in her cough, and a constantly runny nose. She doesn’t suffer from that anymore — since we’ve been here, she doesn’t cough in the night.”
While this is a very small sample, it gives a tantalising glimpse of just what might be achieved if we built and renovated our housing stock explicitly around everyone’s need for a healthy home. Lambeth Council are certainly keeping an eye on the findings with interest.
“Health is not a specific factor on our housing needs register, but we are responsible for public health as a borough, so it makes sense that this is something we can do long-term for health,” says Huw Jones.
“There is anecdotally a link here to good health. It would be nice to be more scientific about this — we are hoping that the post occupancy evaluation information and monitoring we are collecting will help us.”
Will Lambeth go passive again?
Council members are very enthusiastic about the new homes and the benefits they bring, Jones says. “They are really keen to drive this quality across our wider programme to help address important issues such as fuel poverty, high bills, indoor air quality and health.
“However there are challenges in delivering larger projects to the [passive house] standard, including cost, building form, and contractor experience, so we are taking a methodical approach to ensure appropriate solutions across our programme.
“We have written a design guide with a set of principles that includes some targets, including indoor air quality. The post occupancy study on the Akerman scheme will hopefully help us to inform future work.”
Despite achieving passive house with the new build, these houses didn’t break the budget – mainly, Jones believes, because they designed in high performance from the outset.
This echoes the advice from Anne Thorne Architects, who have been helping Lambeth with their strategy for the 1,000 new homes they want to deliver in the borough. “We have been encouraging Lambeth to go for it and build to passive house — but we have stressed that they really do need to be clear that is the goal, and ensure everyone is signed up, right from the start of any project,” Fran Bradshaw says.
Meanwhile, Huw Jones certainly wants to share the benefits they have achieved at Akerman Road across all of their new housing stock. “I think social landlords are the ideal organisations to take up this method of building and prioritise it,” he says.“We’ve got a long-term interest in the stock, and a responsibility for everyone’s well-being.”
Selected project details
Client: London Borough of Lambeth Council
Architect (pre-planning): Anne Thorne Architects
Architect (post-planning) & passive house design: 15-40 Collective
M&E engineer: Alan Clarke
Civil & structural engineer: Ellis & Moore
Passive house certification: Warm
Project management: Artelia UK
Main contractor & mechanical contractor: Sandwood
Quantity surveyors: Peter W Gittins & Associates
Electrical contractor: PA Electrical
Airtightness tester: Encraft
Timber frame system & MVHR: Passivhaus Homes
Airtightness products: Green Building Store
Windows & doors (new build): Passivhaus Store
Double glazed sliding sash windows: Vrogum
Flooring: Hillingdon Flooring Planting: Acacia Gardens
Drainage / paving: Connellys
Wood fibre insulation (retrofit): Natural Building Technologies
In detail
Building type: Three 136.5 square metre three-storey timber frame terrace houses.
Passive house certification: Certified January 2017
Space heating demand (PHPP): 15 kWhm2/yr
Heat load (PHPP): 9 W/m2
Primary energy demand (PHPP): 103 kWh/m2/yr
Heat loss form factor (PHPP): 1.8
Airtightness (at 50 Pascals): 0.34, 0.39, 0.4 ACH
Overheating (PHPP): 1.9 % (of time above 25C). No opportunity for Brise Soleil in this London location with sensitive planning issues. Overheating study carried out and as a result lower g-value glass added to the front elevation, increased top window frame thickness (so night cooling could be enhanced in tilt position), and added demand control on the MVHR systems.
Energy performance certificate (EPC): B (88 or 89) for all three units (Note: the architects stress these figures are unlikely to reflect the true energy performance due to use of various assumptions / defaults).
Thermal bridging: Houses are built using the PH15 passive house suitable timber frame system from Passivhaus Homes. PH15 details for all principle junctions: wall to slab detail 0.004 W/mK, intermediate floor to wall thermal bridge free, eaves detail 0.003 W/ mK, roof ridge detail -0.006 W/mK.
Energy bills (measured or estimated): Estimate of £99 per year for space heating only (based on PHPP data & gas price of 4.3p per kWh).
Ground floor: Ground bearing slab of 150mm thick reinforced concrete on 1200 gaugepolythene Radon membrane, on 200mm Celotex GA4000 (Lambda value of 0.022 W/mK), on sand blinded and compacted hardcore. Power floated finish to slab, target +/- 3mm level tolerance to take pre-cut timber frame. U-value: 0.109 W/m2K. Substructure blockwork walls with 150mm cavity, fully filled with insulation, thermal break using two courses of Foamglas Perinsul blocks in inner leaf.
Walls: 360mm Steico I-joists at 400mm centres with 360mm wide timber floor plate. Wall void fully filled with Thermofloc cellulose insulation. Sole plate screwed to concrete slab and outer leaf blockwork on DPC. Timber lintels generally C24 softwood. 12mm Spanotec Durelis Vapour board to inner face of all walls with 4mm expansion gap at edges. All joints taped with pro clima Tescon Vana to form combined racking, vapour check and airtightness layer. All service penetrations fitted with pro clima Kaflex or Roflex airtightness grommets. 40mm of Steico Protect wood fibre insulation to outer face of timber frame (Lambda value of 0.049 W/mK) using Ejot thermally broken insulation fixings. Finished externally with Lime Green Warmshell render system. Overall U-value of 0.112W/m²K.
Roof: 360mm deep Steico I-joists at max 400mm centres with a maximum span 5890mm. Roof void fully filled with Thermofloc cellulose insulation. Roof joists fixed to load bearing I-joist walls using 18mm plywood gussets, fixed to webs (gussets also used at roof ridges). Lintels to rear elevation using bespoke timber box lintels supplied as part of PH15 System. Roof ridge beam Ultralam R LVL beams. Intello Plus vapour control and airtightness membrane on underside of roof fully taped at all joints with Tescon Vana airtightness tape and taped to Spanotech wall airtightness layer. 40mm of Steico Special Dry wood fibre insulation to outer side of roof (Lambda value of 0.041W/ mK) using Ejot thermally broken fixings. Solitex Plus roofing membrane with taped joints. Reconstituted slate roof externally. U-value: 0.108 W/m2K.
Party wall: Plasterboard skim externally followed inside by 25mm service void if needed, 12mm Spanotec Durelis board (airtight / vapour block), 18mm Fermacell board, 97x47mm studs + 60mm gap + 97x47mm studs (all fully filled with mineral wool insulation to 254mm), 18mm Fermacell board, 12mm Spanotec Durelis board (airtight / vapour block), 25mm service void if needed, plasterboard and skim.1 hour fire rating. U-value: 0.137 W/m2K.
Windows, external doors and patio doors: All windows and doors Katzbeck Massiva, all wood stained / painted and triple glazed. Tescon Profil airtightness tape. Windows minimum overall U-value of 0.8 W/m²K and class 4 airtightness rating.
Heating system: Vaillant Ecotec Plus 837 gas combi boiler, SEDBUK (2009) 89.3%. Controls: Vaillant time switch 150 to control heating, Vaillant VRT room thermostat in living room.
Radiators: Stelrad concord slim column radiator in living room with lockshield valves, heated towel rails in bathrooms with TRV control. Ventilation: Brink Renovent Excellent 400MVHR, PHI certified heat recovery rate of 84%, with radial ducting system (ie. supply or extract ducts direct to each space from a distribution box). Semi-rigid circular ducts (diameter 75mm) generally running within Eco-Joist floor voids to wall mounted outlets. Main unit located within second floor cupboard off landing.
Water: Water butts in gardens.
Green materials: Cellulose insulation and all timber from PEFC certified sources. PH15 is a low embodied energy construction solution, and is both breathable and vapour permeable.
Image gallery
https://passivehouseplus.ie/magazine/new-build/south-london-scheme-delivers-better-health-for-residents#sigProId3e12b40766