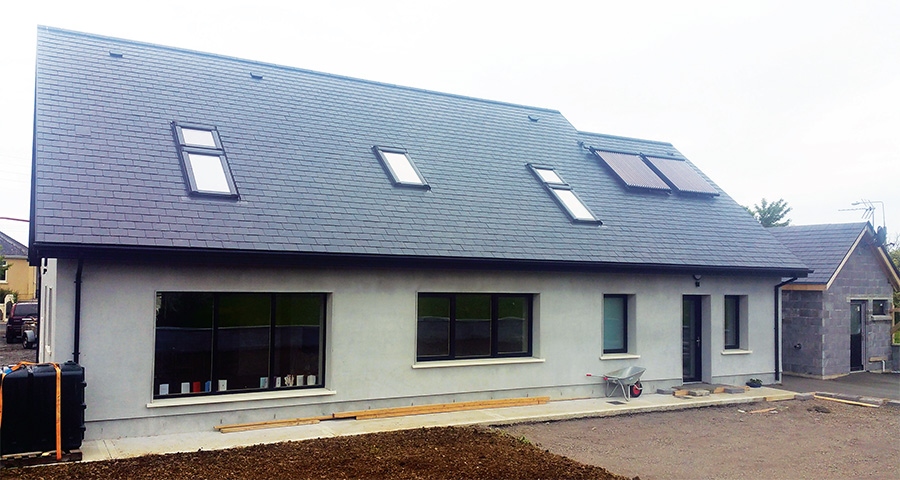
- New build
- Posted
Ecological passive house built on tight budget
Despite some setbacks, this passive house in Roscommon managed to meet the passive house standard for fairly standard costs — all while emphasising natural materials like untreated timber, cellulose and sheep’s wool.
Art Timmins had been thinking about changing his living space for years, and had explored a range of refurbishment possibilities before deciding to start again with a new-build passive house. “We were living on the side of a mountain in a 150-year old three-room cottage with an extension,” he says, “I’m after going from one extreme to the other.”
He moved into his new passive house in March, so he hasn’t yet had a full heating season to compare old with new. The old cottage, however, was swallowing €3,500 worth of heating oil every year, so at the very least, the savings should be dramatic. Art had known Roman Szypura of Clíoma House from an insulation project Roman had carried out for Art years before. Because that experience had been so positive, Art approached Roman when he needed to build a new house from scratch.
Raft foundation with Quinn Lite blocks
“He had a really tight budget,” Roman explains, “so he got into contact with me and asked if it would be possible to build a passive house for €200,000. This was a 218 square metre house – so 200K is a tight budget. But I said it could be done.”
Airtightness membrane preinstalled around the webbed ceiling joists
Keeping within that budget then became the central challenge of the build. At first glance, the site that Art had chosen appeared to be almost perfect, with a full, unobstructed southern aspect at the back. Even better, the architect Art used to provide planning drawings had delivered a layout and a glazing plan that worked perfectly, even though permission had been sought before the decision to go passive.
Timber frame being erected
“The house is basically rectangular with the long side facing north to the road and south to the back, so it’s perfectly lined up,” says Roman. “The main living areas and most of the glazing was on the south, with bedroom, bathroom and utility to the north.” Because the orientation and layout were so good, and the house itself had a simple, compact footprint, going from conventional to passive design was relatively straightforward.
That, however, was where the good news ended. It turned out that the site needed extensive groundworks, and had to be raised by nearly three feet. This unforeseen eventuality blew a hole in the budget. As the project progressed, an unusual pattern began to emerge. Because Roman had so much experience at passive building, the typical passive house challenges hardly cost him a second thought.
Walls are filled with 330mm Dämmstatt cellulose insulation
Take airtightness. The house achieved a rating of 0.23 ACH at 50 Pa, an exceptional result that exceeds the passive house standard of 0.6 ACH by a very generous margin. Roman’s main expertise is airtightness, and during this stage of the project, he used his own team of installers, all of whom were passive house certified tradespeople. “My main guy Gary Waters has been with me now for four years and is absolutely second to none as an airtightness installer,” Roman says. “He’s as good as me, only faster. That’s why airtightness wasn’t really a challenge.”
The same goes for cold bridges. “We chose a build-up that is relatively simple,” says Roman, “and that naturally has no cold bridges. To be honest I wasn’t scratching my head for even ten minutes about it.”
Extenders on structural rafters to enable installation of 50mm EPS thermal breaks
By contrast, it was the conventional stuff that ended up causing problems. In addition to the need to raise the site, a retaining wall was required around the perimeter. There were also headaches in relation to connecting the house with mains services and opening up the site to the road, together with a range of scheduling issues that had nothing to do with the passive spec.
Airtightness detailing including gromit around ductwork
A battened service cavity inside the airtight layer
The roof’s timber sheeting layer
“Meeting the passive house standard wasn’t a challenge at all,” Roman explains. “That was almost the smallest part. The big problems were the things I wasn’t really used to... There was a lot of frustration around lining up contractors, around the wrong materials being delivered or else not being delivered on time.”
Similarly, the team was able to deliver passive house materials and techniques within the budget, but it was the ancillary issues that drove costs higher — despite the fact that Roman went to great lengths to ensure the quality of those materials.
An airtightness strip detail in the attic with EPS thermal break installed on rafter
“We were eager to use as few glues and toxins as possible,” says Roman, “and create a healthy living environment by using as much natural timber as possible.”
Roman is keen to emphasise one innovation which he and his team implemented on the build. The initial plan had included a truss roof, but shortly before work began, he realised that this approach would require huge amounts of additional airtightness work – upwards of 900 individual seals.
Installed Roto Designo roof windows
“Instead, we invented a new way of building a traditional cut roof that allows you to preinstall the airtightness membrane around the ceiling joists.” It’s a solution, Roman believes, that would make it much easier for builders to achieve passive airtightness results with traditional style roofs. “It’s one of the things I was most excited about on the build. We found a really smart solution there.”
In the end the house itself ended up costing about €215,000, excluding the groundworks and site works. Still, this put the price of the house itself at about €91 per square foot well within conventional boundaries.
The roof begins to take shape
Art Timmins is very positive about the whole experience. He says when you’re looking for someone to build your house, they have to fulfil two – and only two — conditions. “The key really is that you need someone who knows what they’re doing and you need to be able to trust them. That was Roman. He knew what he was about and he was totally trustworthy.”
Selected project details
Client: Art Timmins
Architectural design, planning:
O’Rourke Design & Planning
Passive house design, project management,
main contractor & airtightness: Clíoma House
Timber frame:Clíoma House/RC Building Consultancy
MVHR design: Digren
Civil & structural engineering:
O’Rourke Design & Planning/CST Group
PHPP & passive house certification: Target Zero
BER: Energy Rating & Planning Services
MVHR system design, supply & installation:
A+ Ventilation Supplies
Plumbing: Brian McCann Plumbing & Heating Contractor
Electrical contractor: Aidan Hackett Electrical
Airtightness testing: ABuild
Natural insulation & airtightness products:
Ecological Building Systems
EPS insulation: Kingspan Aerobord
Windows & entrance doors: Munster Joinery
Roof windows: Roto Roof & Solar Technology
Screeds: McLaughlin Concrete Flooring
Heating system supplier:Joe Simon Building Supplies
Roofing: J Long & Son Ltd
The house is rendered externally with a Nap plaster finish
Additional info
Building type: 219 square metre detached timber frame dwelling
Location: Boyle, Co Roscommon
Completion date: March, 2015 (excluding site-works & landscaping)
Final cost: €215,000 approximately (excluding site-works & landscaping)
Passive house certification: pre-submission
Space heating demand (PHPP): 12 kWh/m2/yr (based on preliminary airtightness results)
Heat load (PHPP): 7 W/m2 (based on preliminary airtightness results)
Primary energy demand (PHPP): 83 kWh/m2/yr
Airtightness: 0.23 ACH at 50 Pa
Energy performance coefficient (EPC): 0.313
Carbon performance coefficient (CPC): 0.346
BER: A2 (49.52 kWh/m2/yr)
Thermal bridging: Raft foundation with first three course of Quinn Lite aerated concrete blocks, timber frame / Larsen truss walls and roof structure, timber / aluclad windows located in accordance with PH recommended window details, insulated reveals and cills. Y-value (based on ACDs and numerical simulations): 0.08 W/mK
Ground floor: 75mm screed on 260mm EPS100, on Monarflex RMB350 radon membrane, on 150mm reinforced concrete raft to engineer's specification. U-Value: 0.13W/m2K
First floor (inside the thermal envelope): Laminate floor on soundproofing layer, on two layers of 12mm plywood, on 405mm top hung Easi-Joists, (filled with 405mm Dämmstatt cellulose insulation), on pro clima WA membrane, on 35/48mm counter batten, on 12.5mm gypsum board. U-Value: 0.093 W/m2K
Walls: 20mm Nap plaster finish, on 100mm blockwork rain screen, on 50mm ventilated cavity, on pro clima Solitex Fronta Humida wall membrane, on 125 x 25mm untreated diagonal racking, on timber frame / larsen truss wall constructed with untreated 89 x 38mm outer non-loadbearing stud, with untreated 139 x 38mm internal loadbearing stud both at 600 Crs, with 12mm 300 x 375mm gusset plates at 1200mm Crs (filled with 330mm Dämmstatt cellulose insulation), on untreated 125 x 25mm untreated diagonal racking, on pro clima Intello Plus airtightness membrane, on untreated 50 x 50mm battens at 400 Crs forming service cavity with 50mm Thermafleece sheep wool batts, on 12.5mm Gypsum plasterboard. U-value: 0.10 W/m2K.
Roof: Natural slate on 44 x 38mm slating batten, on 44 x 38mm ventilation battens (running same direction as the rafter on top of the rafter), on pro clima Solitex Plus breathable membrane with pro clima Naidec nail sealing tape, on 22mm natural timber sheeting, on a Larsen truss roof / rafter system made up of 125 x 44mm rafters on 50mm EPS rigid insulation, on 225 x 44mm rafters with 12mm 300 x 375mm gusset plates at 1200mm Crs. (filled with 400mm Dämmstatt cellulose), on pro clima Intello Plus airtightness membrane, on untreated 50 x 50mm battens at 400 Crs forming service cavity with 50mm Thermafleece sheepwool batts, on 12.5mm Gypsum plasterboard. U-value: 0.093 W/m2K.
Ceiling / roof (to cold attic): 530mm Dämmstatt cellulose, on 150 mm collar ties, on pro clima Intello Plus airtightness membrane, on 48/48mm counter batten, on 12.5mm gypsum board. U-value: 0.075W/mK
Windows: Munster Joinery passive house certified EcoClad timber-aluclad triple-glazed windows with argon filling and a U-value of 0.7 W/m2K for the glazing, and overall U-values of between 0.99
W/m²K and 0.79 W/m2K installed (including frames).
Roof windows: Roto Designo roof windows with R8 BlueTec Plus glazing 9P (compliant with passive house) with prefitted insulation collar against heat loss, and vapour barrier for optimal airtightness.
Overall U-value: 0.84 W/m2K
Heating system: 92% efficient Grant Vortex condensing oil boiler supplying three radiators and 300 litre two-coil Joule stainless steel cylinder, plus 40-tube Joule Acapella solar thermal array.
Ventilation: Zehnder ComfoAir 550 MVHR system, Passive House Institute certified to have heat recovery rate of 84%, EN 308 certified efficiency of 92.7%.
Green materials: cellulose insulation, sheep wool insulation, untreated timbers.
Image gallery
Passive House Plus digital subscribers can view an exclusive image gallery for this article. Click here to view