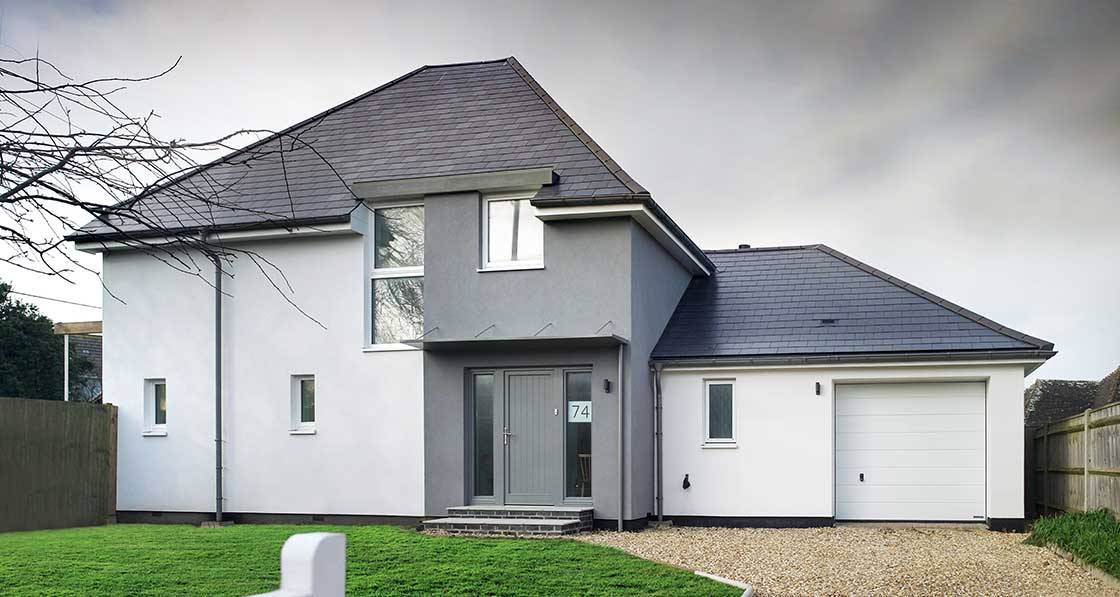
- Upgrade
- Posted
Witness the Phitness
The deep retrofit of this 1930s dwelling on the Hampshire coast provides a pitch-perfect example of how to transform old dwellings while preserving their original structure and minimising embodied carbon, utterly transforming the living space without the need for an extension, and creating a cosy home that uses two-thirds less energy than before.
Click here for project specs and suppliers
Building: Deep retrofit to 144 m2 detached home
Method: External insulation on cavity brick wall
Location: Barton-on-Sea, Hampshire
Standard: Enerphit (certified)
Space heating cost: £36 per month (see ‘In detail’ for more)
David Dacombe and Julie Botham spent the best part of three decades living in a cold and damp four-bedroom 1930s detached house, in Hampshire. Passionate environmentalists, they set out to insulate the 144 square metre brick property a few years ago. But somewhere along the way, their ambitions soared and a new goal emerged to achieve the Enerphit (passive house) standard for retrofits.
The project ended up costing 50 per cent more than they initially envisaged, but their “new” home achieved Enerphit and has transformed their living experience.
“We spent a scary amount of money in the end, but we’re very pleased with the house and definitely glad we did it. We’ve ended up with almost a brand-new home,” says David, a retired engineer (the project was not fully costed until the contracting stage, and bids from builders came back higher than anticipated). “We get lovely comments from visitors and passers-by about the outside. The tiles have been replaced with slates which together with white and grey render gives a contemporary appearance outside. Inside, the main advantage is the comfort all-year round as it used to be cold, draughty and damp in winter.”
Before consulting an architect in 2016, the couple spent a long time thinking through their options. One ambitious plan was to knock down their existing house and build three townhouses in its place, then sell them and use the profit to build a passive house. “But we couldn’t find a suitable plot anywhere in the local area, and we felt it wasn’t a green thing to do because of all the embodied energy,” says David. Neither did they want to tear themselves away from the local area, where they have lived since 1994.
The house is 500 metres from a beautiful stretch of coastline, near Bournemouth, and close to the border of the New Forest National Park.
This article was originally published in issue 39 of Passive House Plus magazine. Want immediate access to all back issues and exclusive extra content? Click here to subscribe for as little as €10, or click here to receive the next issue free of charge
Another option was to attempt a DIY approach to insulation. David read up on how to do this and started by stripping off the plaster in two rooms. But the reality proved more complex than the manuals had suggested.
“Cold bridges were a big issue. If you don’t get rid of them, you end up introducing even bigger ones,” David says [editor’s note: when you insulate internally, any remaining cold bridges — uninsulated paths that cut through the insulation layer — are exacerbated and potential points for condensation].
At this stage, they opted to seek the help of a professional architect.
RIBA recommended three local architects and the couple were impressed with Ruth Butler, who also lives in Hampshire. She had previously built four passive houses, including her own home, previously featured in Passive House Plus issue 33.
When David and Julie met her in 2016, their intention was simply to improve the insulation. But it was obvious that significant internal changes would in any event be essential to upgrade the airtightness. The couple had become familiar with the Enerphit standard and decided to go for it.
Ruth worked with the couple to develop options in 2017 and showed them three reconfigurations using 3D models. David and Julie wanted an open-plan design and agreed to get rid of a conservatory. Ruth convinced them to give up plans for an extension in favour of spending more money on the existing structure. The original roof structure was kept too, and all-in-all the house provides a first-class example of how to undertake a deep retrofit while preserving as much of the existing building as possible, in order to reduce the embodied carbon of the build. An analysis in PHribbon calculated the embodied carbon of the retrofit at 111.7 kgCO2e per square metre, for building life cycle stages A (product stage) through to C (end of life). For comparison, this smashes even the older, more stringent RIBA 2030 target for new build homes of 300 kgCO2e, emphasising the importance of preserving existing structures.
There was no opposition from New Forest District Council to the application for planning. But finding the right builder proved far more challenging. When David and Julie’s initial choice pulled out just as the project was about to get underway in mid 2018, they nearly gave up.
“It was very frustrating and we were on the verge of quitting,” David says. “There were a few builders with passive house experience in other parts of the south, but no one was prepared to travel for a small job.”
Ruth persuaded them to change their strategy and give it another shot. Instead of looking for a specialist, they put out a tender for skilled local builders and hoped to train them up in passive house methods. There were two bids and Ruth advised them to go with Tuakana Construction, who are based nearby. “I thought they’d be a good fit for an Enerphit project as they’d worked on a lot of historic buildings,” Ruth says. “I think there’s a synergy with the attention to detail you need for passive house projects.”
The builders began work in February 2019 while the couple rented a property for eight months. Tuakana’s operations manager Neil Woodley says the company likes to be stretched by new challenges, but admits to a few nerves at the outset. “We were a bit daunted at first because we weren’t sure what would happen if we didn’t meet the Enerphit criteria. We even joked that if we don’t get passive house accreditation, do we not get paid? But when you break it down, if you follow all the necessary details, you reap the rewards,” he says.
Construction in progress
https://passivehouseplus.ie/magazine/upgrade/witness-the-phitness#sigProIdf9269c0950
The key to success was to get the experienced team of builders thinking a little bit differently. “The foreman in charge had been doing things in a certain way for 30 years,” Neil says. “Suddenly he was asked to do things differently, the standard methods and processes he had been adopting for years were suddenly not permitted, basic things like the running of electrical and plumbing services were carried out in a completely different way. The few times we slipped up were where we did things out of habit that we have always considered good practice in a standard build, but you have to think differently in passive house. It comes down to understanding the reason behind the different ways of doing things. If you realise why all the little details are important, it becomes a much much more logical process.”
To challenge their pre-existing habits, all the builders in the team received half a day’s hands-on airtightness training from Bill Butcher, director of Green Building Store. That proved invaluable: the project went on to achieve an airtightness of 0.48 air changes per hour, beating not just the Enerphit standard of 1.0 but also the passive house new build standard of 0.6. “The success was in many ways down to the training. The building team really related to Bill as a fellow builder. It meant that they all started off on the project with the same language and understanding,” says Ruth.
Naturally, one of the main difficulties of achieving Enerphit was working around the original structure. “You’re stuck with all the thermal bridges, and it can be complicated to get the airtightness line around the existing pieces of construction,” Ruth says. “It’s a nice challenge to have and you have to get your brain working in how to resolve issues in the simplest, most practical way possible. We chose to use plaster parge on the walls [as the airtightness line] and put membranes over the existing floor and ceiling.”
The experience of living in the house is radically different now.
To create an open-plan space the team removed a number of walls. The builders knocked through the old entrance lobby and pulled down the wall between the kitchen and dining room. The kitchen was re-modelled entirely. “Opening up the living and dining areas and having the stairs as part of the house makes it feel like a much bigger house. We’ve taken away a rather ratty old conservatory on the south-facing side which was preventing direct access to the garden. They’re keen gardeners so that was important for them,” she says.
Ruth’s plans for the retrofit included a new thermal jacket for the house. This involved installing a rendered external insulation system on the outside of the cavity brick walls, raising the timber flooring to add insulation and installing a Brink mechanical ventilation with heat recovery unit (MVHR). All the old heating pipework was stripped out, leaving just one 1.5 kW fitted electric radiator, and one portable 1.5 kW radiator that is now used in the lounge (separate to the open-plan area). This ultra-minimal heating setup is testament to David, Julie and Ruth’s confidence that the house will perform as it is designed to (of course, the mild climate on the south coast of England also made it easier to achieve the Enerphit standard).
The house had recently had most of its old windows replaced with triple glazed units from Green Building Store. But during the retrofit these had to be re-positioned to accommodate the external wall insulation, and some windows were moved too. Thankfully, this this was reasonably easy to accomplish as straps had been used to fit the windows. They were moved 200 mm out into the insulation zone, and deeper extension sills were fitted.
There were not as many structural changes to the four bedrooms upstairs. But the design enlarged the bathroom, allowing both a shower and bath to be fitted. The builders also reconfigured the roof slopes and removed a dormer with two windows, so the bedrooms became less constrained.
To be awarded an Enerphit certificate, retrofitted homes must achieve a maximum space heating demand of 25 kWh/m2/yr. PHPP, the passive house design software, showed that the remodeled house’s space heating demand was 19 kWh/m2/yr, and it was certified in 2020. It was a finalist in the 2021 UK Passivhaus Awards in the small projects category.
David and Julie have monitored the house’s energy consumption over the past two years and they are using approximately one third of what they were pre-retrofit, although this has only resulted in marginally lower energy bills – likely due to comfort-taking and the switch from comparatively inexpensive gas to direct electric for heating and hot water. (see ‘In detail’ for more). In summer, they generate a small amount of electricity from their 12 m2 solar PV array and never switch the heating on. David says the lounge can sometimes get too warm, but that they manage this with an internal blind and by opening the bi-fold doors. In winter, the fitted electric radiator in the open place space provides whole house heating; the portable radiator in the lounge is only used on very cold winter days. The experience of living in the house, David says, is radically different now.
For Ruth Butler, the New Forest Enerphit project proved equally as life-changing. Although passionate about passive house new build, she points out that retrofitting old houses is more critical to the climate crisis.
“When they said they were interested in a deep retrofit I jumped at the chance. It turned out to be a landmark project in my career as an architect. It helped me to realise that deep retrofitting was my primary concern as an architect.”
The New Forest Enerphit turned out to be her final design for her own company, Ruth Butler Architects. In February 2020, she took a new job with Pritchard Architecture, in Portsmouth. The company carries out a lot of conservation and conversion work and Ruth’s role is to work on low energy refits. Her current projects include retrofitting a home in Prinsted, near Chichester and converting a barn into offices for Seven Sisters Country Park.
Embodied carbon
An embodied carbon analysis by PHribbon author Tim Martel and sustainable building consultant John Butler revealed high and low estimates for cradle to grave totals, with the difference in results depending on the assumptions made about component lifespans and consequent replacement. The high estimate was based on using the default values on expected lifespans from the RICS document, ‘Whole life carbon assessment for the built environment’. This assumed a lifespan of 30 years for windows, external doors and renders, and a 20 year lifespan for the ventilation system and ductwork. The low estimate – which was informed by the results of a destructive monitoring study on the first passive house 25 years after it was completed, assumed a 60 year lifespan for the windows, doors and renders and ventilation ductwork, with one replacement of the ventilation system. In both cases, it was assumed the PV array would last for 30 years.
The high estimate resulted in a total of 20.9 tonnes, 136.1 kg CO2e/m2 – less than a quarter of the 625 kg total set for dwellings in the RIBA 2030 Climate Challenge. The low estimate total was 16.9 tonnes of CO2e, or 110.1 kg CO2e/ m2 – less than a fifth of the RIBA 2030 target. In either case, the result confirms the importance of focusing on retrofit over new build in terms of reducing embodied CO2. The analysis included the external envelope, including new roof, along with the ventilation system and ductwork. The ventilation system calculations were based on a draft Product Environmental Passport for the Brink Flair unit, which hasn’t yet been independently verified, and calculations for the ductworks provided by ventilation supplier CVC systems, in accordance with CIBSE’s TM65 methodology. Any changes to the internal layout and finishes were not included, nor was the building’s single electric panel heater.
Selected project details
Clients: David Dacombe & Julie Botham
Architect: Ruth Butler Architects
Main contractor: Tuakana Construction
M&E engineer: Cundall
Civil & structural engineer: Andrew Waring Associates
Energy consultant: Cundall
Passive house consultant: Green Building Store
Passive house certifier: Mead Consulting
Electrical contractor: LSB Electrical, Plumbing & Heating
Airtightness tester: BRE
External wall insulation system: Permarock, via Specialist Rendering Services
Airtightness products: pro clima, via Green Building Store
Windows & doors: Green Building Store
Electric radiator: Zehnder
Ventilation: Brink MVHR, via CVC Direct
Passive fire safe door: James Latham
In detail
Building type: Deep retrofit to 144.4 m2 (treated floor area) detached 1930s house
Location and site: Village site, Barton-on-Sea, New Forest
Completion date: September 2020 (practical completion & handover September 2019)
Space heating demand (PHPP): 19 kWh/m2/yr
Heat load (PHPP): 13 W/m2
Heat loss form factor (PHPP): 2.86
Overheating (PHPP): 0 per cent of year above 25C
Number of occupants (PHPP): 2.9
Primary energy renewable (PHPP): 72 kWh/m2/yr
MEASURED ENERGY CONSUMPTION:
Before: 147 kWh/m2/yr (20,061 kWh total, 17,730 kWh of gas & 2,331 kWh electric, for 2018)
After: 45.74 kWh/m2 (or 6,605 kWh total, 12 months from Sept 2020 to Sept 2021)
Energy bills (estimated): Based on measured energy use (electricity + gas) prior to retrofit, and based on Energy Saving Trust figures from June 2021 on average tariffs, the calculated pre-retrofit combined electricity and gas bill for this property of £1,302 per year, including VAT and standing charges. Based on post-retrofit metered electricity consumption, the cost drops slightly to £1,168. This is due to the higher price of electricity (based on an average tariff of 16.36p per kWh versus 4.17p per kWh of gas) in spite of the house’s energy use dropping by two-thirds. This is an indicative figure and we give it for illustrative purpose only. In reality the homeowners say their total annual bill has reduced from approximately £1,490 per year to £1,040, as estimated on their latest bill, including all charges. Given that the gas bill pre-retrofit may have included hot water use and cooking, we haven’t attempted to estimate heating costs pre retrofit. Based on PHPP figures for space heating, and the EST electricity tariffs, the post retrofit heating use is estimated at £437 per year, or £36.42 per month.
Airtightness (at 50 Pascals): 0.48 air changes per hour
GROUND FLOOR
Before: Mix of uninsulated concrete floor and uninsulated suspended timber floor
After: Concrete slab insulated with 50 mm PUR insulation. U-value: 0.257 W/m2K. Suspended timber floor with air tightness membrane (Contega Solido) and 80 mm PUR insulation beneath. U-value: 0.166 W/m2K
WALLS
Before: Render, brick cavity walls
After: Permarock external insulation render system comprising render on 100 mm graphite EPS, on existing 100 mm brick cavity walls, 100 mm blown bead insulation into existing cavity, brick inner leaf, plaster parge as airtightness layer. U-value: 0.27 W/m2K
ROOF
Before: Concrete roof tiles followed beneath by felt, sarking boards, plasterboard ceiling internally. Loft mineral wool insulation.
After: Fibre cement slates externally, followed inside by battens/county-battens, existing roof structure and sarking board, 400 mm loft mineral wool insulation between and over ceiling joists and continuous with cavity wall insulation, highly vapour permeable membrane to underside of mineral wool (pro clima Solitex Plus), plasterboard ceiling with skim finish. U-value: 0.09 W/m2K
WINDOW AND DOORS
Ultra triple glazed timber windows by Green Building Store. Overall reference U-value of 0.75 W/m2K (the existing GBS windows were repositioned and some new ones installed). Two Lacuna UK and Ireland Ltd bi-folding doors installed (each including three glazed sections 2.52 m high x 2.2 m wide). Heat treated beech frames, with breathable off-white paint. Ug value: 0.72 W/m2K, Uw 0.90 W/m2K. New Moralt Ferror Passiv Fire Safe door added between utility room and garage (By James Latham).
HEATING SYSTEM
Before: Gas boiler & radiators throughout entire building
After: 1.5 kW Zehnder Road electric panel
radiator to open plan living area; one plug-in 1.5 kW radiator in lounge
VENTILATION
Before: No ventilation system. Reliant on infiltration, chimney and opening of windows for air changes
After: Brink Flair 325 heat recovery ventilation system, Passive House Institute certified to have heat recovery rate of 91 per cent.
Green materials & features: FSC certified timber, re-use of existing kitchen units in utility room, re-use of some existing sanitaryware, cork flooring in bedrooms, low flow water fixtures, rainwater butts to garden.
Electricity: 12.7 m2 solar photovoltaic array.
Image gallery
https://passivehouseplus.ie/magazine/upgrade/witness-the-phitness#sigProId62986a2633