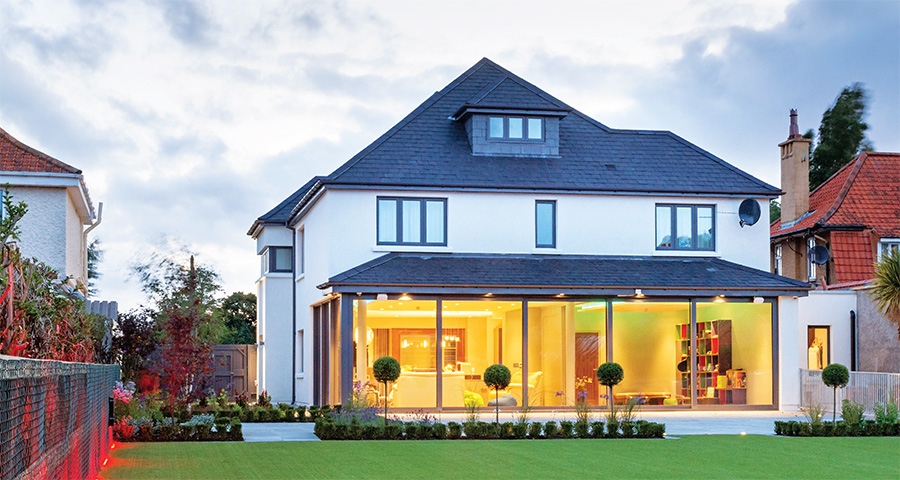
- Upgrade
- Posted
Enerphit upgrade breathes new life into Dublin home
This ambitious and complicated project — a partial upgrade, partial rebuild of an old detached property in south Dublin — is on course to achieve the onerous Enerphit standard for retrofit.
This retrofit project in south Dublin proved complex, but despite the challenges it ultimately appears to have met the onerous Enerphit standard for low energy retrofit.
The client, who wishes to remain private, had been living in Rathgar, Dublin with his family. With two young children the family wanted more space, but were eager to remain locally. Because the area has been well developed for over a century, buying an old house and renovating was the obvious way forward.
The client spent a few years looking for a suitable property, before buying a 300 square metre early 20th century detached house. Unlike other homes on the street, it was not a protected structure. This made it possible to externally insulate the pebbledash building, thus driving U-values as low as possible and eliminating thermal bridging. But the client was also eager that the retrofit remain sympathetic to the local architectural style.
“Our intent really was to keep the style of the house, keep the shape of the house and everything that actually can be seen from the road — so all of that remained the same, and we just added insulation to the outside,” he says. “We were very sympathetic to the original design. It was a modern take on how it looked.”
The client, an engineer himself, was intimately involved in the design and build. “At the start we were quite hands on with the level of details,” he says. “With any job, if it’s passive or not, if you want to influence the outcome you need to be.”
He says that minimising the environmental impact of the house was always going to be high on the agenda. “I’m in the business for 25 years, sustainability is a large part of that. We wanted to do something that’s true to what we actually do for clients day-to-day. We were never going to do anything that wouldn’t be sustainable. We wanted to take it as far down that route as we could.”
But he insists: “To get something that is low energy and environmentally friendly, I don’t think you should suffer on comfort —in fact I think your comfort should be enhanced.”
Ralph Bingham of Mola Architecture produced the drawings for the planning permission (and later took on the role of project architect during the build). Another architect and passive house designer, Natalie Walsh, was also appointed and produced the working construction drawings, including 16 details related to cold bridging and airtightness. She also found passive house building firm Pat Doran Construction Ltd — run by father and son team Pat and Paul Doran — through Passive House Plus magazine.
The client had originally looked at the possibility of meeting the Enerphit standard for retrofit, but thought it would be too expensive, though they still planned to adopt passive house design principles. But when Pat Doran Construction was appointed, they pushed the passive house agenda. “We said it might be possible to do Enerphit without it costing more,” says Paul Doran.
Before and during shots of the construction
He continues: “From our experience and knowledge we were able to say that the budget was sufficient, that the house had a good orientation and form factor for passive house. I'd done a preliminary PHPP [calculation] that showed it met Enerphit requirements and suggested getting Darren O'Gorman [of passive house consultancy Target Zero] involved who confirmed my findings that the house was an excellent candidate for Enerphit.”
Paul Doran says that while many builders don’t like working in Dublin because of the traffic and lack of space, this house made for a nice change, with its spacious site providing ample room for a site office and small canteen. “It was a brilliant location,” he says.
Being a big, old building with lots of different junctions, meeting the Enerphit standards for airtightness and thermal bridging was always going to be the biggest challenge. “There were numerous junction details, and all of them were potentially problems in getting the envelope cold bridge free. On top of that you had all of the services,” Paul says.
Steel column with Compacfoam thermal break
The house features a wide array of services including automated LED lighting, a security system and audiovisual systems — all of which can be controlled remotely by smartphone app. All mechanical and electrical services including the heating and cooling setup were designed by Ethos Engineering. Ethos spoke to some of their clients who had built near passive buildings, and they reported overheating to be the biggest issue1 — particularly the length of time it took to cool their dwellings down after returning from time away in summer.
Xtratherm used to insulated upstands
The client points out that while PHPP, the passive house design software, allows homes to go above the overheating threshold of 25C ten per cent of the time, this still equates to about one month a year of overheating. Thus he was keen to have an active cooling system in the house. An outdoor Panasonic air source heat pump provides cooling via a refrigerant delivered to fan coil units in each bedroom (completely separate to the ventilation system). There is a thermostat in each of the bedrooms to control this system, which can also provide heating if necessary.
Partial fill board at boundary wall; Quinn Lite thermal blocks at eaves to reduce cold bridging
Separately, a high efficiency condensing gas boiler provides heat to Polytherm underfloor heating pipes downstairs and towel rails upstairs. There’s also a solar thermal system to help meet the family’s hot water demand. The gas heating and hot water is all regulated by Heat Miser controls, with a touchscreen in the plant room, and can be controlled by smartphone too. And given the size of the house, there are two Zehnder ComfoAir MVHR systems providing fresh, pre-heated air through the house.
“We spent a week figuring out how to get the ventilation system inside the airtight envelope,” Paul Doran says. “We did manage it in the end.” The semi-rigid ducting used for the manifold, he adds, would have been a nightmare to seal with tapes and membranes otherwise.
The use of a continuous cavity inside the airtight layer helped to contain the services, but there were still lots of penetrations of the airtightness layer at the attic level, because it was more practical to keep the membrane towards the inside of the build-up rather than the outside. “After 100 penetrations I stopped counting,” says Paul Doran. “The important thing was not how many there were, just that we caught all of them.”
25mm Xtratherm PIR sandwiched behind timber to provide continuous insulation from lower roof to external insulation at rear of house
The builders took a number of key steps to make sure the airtight layer remained intact: this included direct site supervision from Paul’s father Pat, giving ‘toolbox talks’ to tradespeople on site, and putting up signs warning people on site to inform the builders if the airtight layer was breached, whether intentionally or by accident. “The worst thing someone could do was drill a hole and not tell us about it,” Paul says.
The team removed the chimney stacks completely, cutting out a major cold bridge and source of air infiltration in one swoop. Meanwhile Compac Foam mats supplied by Galway-based company Partel cut out thermal bridging between the seven structural steel beams and the foundations.
While the house is essentially a retrofit, with external EPS insulation to the original brick walls, large sections were rebuilt with concrete blockwork and insulated in the same manner. The footprint of the original building was also extended by about 100 square metres with a single-storey side and rear extension. The roof was also a mixture of new and original parts, all insulated heavily with Isover Metac glasswool.
The old suspended timber floor was removed, and a new concrete poured and insulated with PIR board and finished with polished concrete. There’s also thermally broken triple-glazing throughout – in the form of windows and doors from Rationel Vinduer Ltd, Reynaers curtain walling, and Fakro roof windows.
The dedication to a highly airtight, continuous thermal envelope posed a threat to the family dogs – as a dog door would have created a significant thermal weak spot. The solution was an automated pet door from Austrian manufacturer Petwalk, which combines access for pets, burglar-proof security and a highly airtight, highly insulated, thermal bridge-free design.
The project involved much more than energy efficiency work though. All internal walls were knocked, and the team completely reconfigured the layout inside, turning the ground floor into a much more open plan, light-filled space. “We were looking for something that flows well, something that was open plan, that suited our way of living,” says the client.
Installation of the Kore EPS external insulation
His family had only moved into the house nine days before Passive House Plus spoke to him, so it was much too early to ask about the house’s performance. But he said: “It’s been very pleasant. Other than the usual building problems of living with painters and plumbers and electricians doing the final bits and pieces.”
“There’s a nice fresh feel in the house,” he says. The natural lighting strategy has worked well, with the coloured LEDs — designed to change the mood of the living space — only coming on late in the evening.
Paul’s father Pat Doran is happy the team managed to overcome the numerous challenges on site. The project, he says, would have been difficult enough without having to make it airtight. “There was a lot of detail on the roof, and then we had to knock down more than half of the existing building,” he says. “It was the most difficult [job] I’ve done with regards to airtightness and cold bridging.”
100mm Quinntherm PIR insulation at eaves
He adds: “All I can really say is that it was difficult, but we got the result we wanted, and I was happy with it.”
Meanwhile Darren O’Gorman of Target Zero says the final airtightness result of 0.99 air changes per hour is impressive for such a complicated project. “It was a very difficult feat to achieve, particularly with airtightness.”
Isover Metac insulation over the wall plate to help cut thermal bridging
Paul Doran also says that it was the toughest project he’s ever worked on from an energy efficiency point of view: “Enerphit is special forces training for passive house builders, and this one was particularly tough.”
The project was awaiting Enerphit certification at the time of going to press.
1– ed. This appears to be a problem for new homes in general, rather than for passive houses per se. While passive houses are designed to meet maximum average temperature targets, there are no such requirements in Irish or UK building regulations – meaning many highly insulated new homes are being built without regard to whether orientation, form, layout and/or lack of shading will run the risk of causing unacceptably high or low internal temperatures. Similarly, it’s possible to use site-specific weather data for passive houses, while the software tools used for Part L compliance for dwellings in Ireland and the UK respectively use data from Dublin Airport and UK average weather data, leading to additional risk of overheating, underheating or higher than anticipated energy use.
Airtight boxes for down lights
Selected project details
Architect (planning drawings & project supervision):
Mola Architecture
Architect (working drawings & passive house
details): Natalie Walsh
Contractor: Pat Doran Construction
M&E engineer: Ethos Engineering
Structural engineer: Garland Consultancy
Passive house consultants:
Integrated Energy, Target Zero
Passive house certification: Mead Consulting
BER: Rate My Home
Quantity surveyor (client): KMCS
Quantity surveyor (contractor): RTC Surveying
Electrical contractor: Jones Engineering Group
Plumbing: Prospect Plumbing & Heating
Underfloor heating contractor: Base Engineering
Underfloor heating system: Polytherm
MVHR: Flynn Heat Recovery
Air-to-air heat pump: Panasonic
Fan coil units: Tech Refrigeration
Solar thermal: Alternative Energy Ireland
Airtightness testing: Greenbuild
EPS insulation: Airpacks
External render: Neotherm
External insulation contractor:
Enda Linnane Construction
Mineral wool insulation: Isover Ireland
Airtightness products: Siga
Breather membranes: Ecological Building Systems
Floor insulation: Xtratherm
Thermal breaks: Partel
Low thermal conductivity blocks: Quinnlite
Roof insulation & airtightness contractor:Baker & Co
Windows & doors: Rationel
Curtain walling: Lakeside Windows
Roof windows: Tradecraft
Pet door: Petwalk
Polished concrete floor: Renobuild
Roofing: Christy McMahon Carpentry
Additional info
Building type: 400 square metre two-storey detached house from 1926. Enerphit refurbishment with single-storey side and rear extension
Location: Rathgar, Dublin
Completion date: July 2015
Enerphit certification: pending
BER
Before: D1 (251 kWh/m2/yr)
After: A2 BER (43.05 kWh/m2/yr)
Space heating demand (PHPP): 22 kWh/m2/yr
Heat load (PHPP): 13 W/m2
Primary energy demand (PHPP): 78 kWh/m2/yr
Airtightness (at 50 Pascals): 0.99 ACH
Walls
Before: 215mm solid brick walls with no insulation. U-value: 3 W/m2K
After: 200mm silver aged KORE EPS insulation and acrylic render finish externally, 215mm brickwork, 50mm uninsulated service cavity inside. U-value: 0.15 W/m2K
Extension walls: 200mm silver aged KORE EPS insulation and acrylic render finish externally, 215mm block wall, 50mm uninsulated service cavity. Two courses of Quinn Lite blocks at floor to wall
junction. U-value: 0.15 W/m2K
Extension boundary wall (adjacent to neighbouring house): 215mm block on flat internally followed outside by 80mm Xtratherm insulation, 20mm ventilated void, and then 100mm block externally.
Quinn Lite blocks at top of boundary wall to eliminate thermal bridges. U-value: 0.22 W/m2K
Roof
Before: Roof slates to sloped areas and torch on felt to flat roof areas externally. No Insulation.
After: (sloped ceiling areas): Blue Bangor slates externally, on counterbattens, on pro clima Solitex breathable membrane with 220mm Metac between rafters, on Siga Majpell airtight membrane stapled to underside of rafters, counterbattens to create a 500 service cavity inside insulated with Metac. U-value: 0.15 W/m2K
After (flat ceiling areas): Blue Bangor slates on counterbattens, on pro clima Solitex breathable membrane with 400mm Isover Metac above the ceiling joists and 200mm between. Siga Majpell airtight membrane stapled to underside of rafters, counterbattened to create a 25mm uninsulated service cavity. U-value: 0.08 W/m2K
Existing ground floor: Uninsulated suspended timber floor
Upgraded ground floor and extension floor: Poured concrete onto existing concrete subfloor (brought level with extension floor), 150mm Xtratherm PIR insulation above. Underfloor heating pipes in concrete screed, polished concrete floor finish. U-value: 0.13 W/m2K
Windows & doors
Before: single-glazed, timber windows and doors. Overall approximate U-value: 3.50 W/m2K
New triple-glazed windows: Rationel Aura Plus triple-glazed aluclad windows and doors with argon fill and warm-edge spacers: Overall U-value of 0.93 W/m2K
Sliding doors & curtain walling: CareyGlass 52mm triple-glazing with A-rated warm edged spacer bars. Ug value: 0.7 W/m2K. Reynaers frames for sliding door & curtain walling with respective U-values of 2.6 & 2.3 W/m2K. Overall U-values for sliding doors & curtain walling respectively of 1.1 & 0.90 W/m2K.
Roof windows: 9 x Fakro FTT U6 thermally broken triple-glazed roof windows with thermally broken timber frames. Overall U-value: 0.80 W/m2K
Pet door: highly insulated & airtight Petwalk automated door, with frame and door insulated with rigid polyurethane. U-value: 0.5 W/m2K
Heating
Before: 20 year old oil boiler & radiators throughout entire building
After: Remeha modulating condensing gas boiler, 40 Kingspan solar tubes, underfloor heating to ground floor, and six fan coil units providing cooling to upper floors supplied by a Panasonic heating & refrigeration air source heat pump. Polytherm underfloor heating system with Heat Miser controls. Heat Miser control system regulates underfloor heating system downstairs and towel rail circuit upstairs, with a thermostat in every room, while also controlling the hot water. Also controllable via a touchscreen interface in the plant room.
Ventilation
Before: no ventilation system. Reliant on infiltration, chimney and opening of windows for air changes.
After: 2 x Zehnder ComfoAir 550 MVHR units — Passive House Institute certified to have heat recovery rate of 84%
Image gallery
Passive House Plus digital subscribers can view an exclusive image gallery for this article. Click here to view