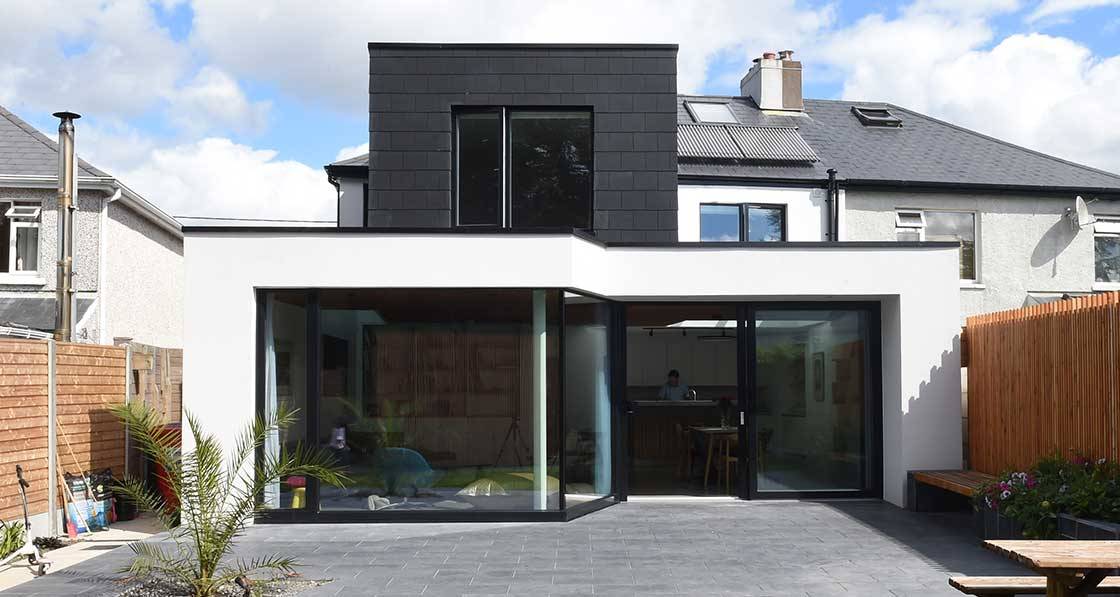
- Upgrade
- Posted
Cork retrofit blitzes new build NZEB standard
The retrofit and extension of a run-down semi in Cork shows just how radically a typical Irish home can be transformed with a skilful retrofit — and why, if your budget is limited, upgrading the building fabric should be your first priority.
Click here for project specs and suppliers
Completed: February 2018
Budget: €280,000
Standard: Nearly zero energy
building (NZEB)
€40 per month gas bill
If you’re a passive house advocate in a position to do a deep retrofit but your budget is tight enough that you might have to make some fundamental compromises, what should they be?
Such compromises might come down to spending less on the heating system and other technological solutions and more on the fabric of your home – or vice versa.
Architect Loic Dehaye knew exactly what his priorities were when he finally got the keys to a three-bed semi in Ballinlough, on the southside of Cork city.
The finished result is beautiful, inside and out.
He’d had his eye on this 1930s-built house for two years and even missed an opportunity to buy it at one stage, but with a sale having fallen through no less than three times, he managed to snap it up on his second attempt.
It’s easy to see why he persevered. Its location, mere minutes away from both schools and work, would limit the family’s daily commuting times and help to reduce CO2 emissions. Its south-facing rear aspect, suitable for large sections of glazing, would ensure a bright open-plan living space that could open out to the garden and maximize solar gain.
And being a semi-detached house, enough space was available to extend out sideways yet still retain side access for bins and bikes etc. “I knew it had great potential,” says Dehaye.
“It also was derelict, giving me a good opportunity to go for a deep retrofit.”
As well as a deep retrofit, the €280,000 budget incorporated the building of a two-storey side and rear extension that would make the house into a four-bed with an open-plan kitchen and living area, a guest toilet, a storage room, a utility room and a converted attic space/play room.
Achieving airtightness in the existing structure was a challenge.
These two goals — retrofit and extend — were so closely intermeshed that Dehaye admits not being able to separate out what proportion of the budget went on the retrofit and what was eaten up by the extension. But having worked on several Enerphit projects for clients over the past number of years, a fabric-first approach to the whole project seemed appropriate.
-
Architect Loic Dehaye had his eye on this 1930s-built house for two years and even missed an opportunity to buy it at one stage, but managed to snap it up on his second attempt; Architect Loic Dehaye had his eye on this 1930s-built house for two years and even missed an opportunity to buy it at one stage, but managed to snap it up on his second attempt;
-
As well as a deep retrofit, the €280,000 budget incorporated the building of a two-storey side and rear extension, a steel and timber frame structure built on site As well as a deep retrofit, the €280,000 budget incorporated the building of a two-storey side and rear extension, a steel and timber frame structure built on site
-
As well as a deep retrofit, the €280,000 budget incorporated the building of a two-storey side and rear extension, a steel and timber frame structure built on site As well as a deep retrofit, the €280,000 budget incorporated the building of a two-storey side and rear extension, a steel and timber frame structure built on site
-
Airtightness taping and membrane at joist ends Airtightness taping and membrane at joist ends
-
The new timber frame walls were pump-filled with cellulose insulation from Cork manufacturer Ecocel through holes in the internal OSB layer The new timber frame walls were pump-filled with cellulose insulation from Cork manufacturer Ecocel through holes in the internal OSB layer
-
Thermally efficient, lightweight & insulated window sill from Youghal-based Passive Sills, certified by the Passive House Institute. Thermally efficient, lightweight & insulated window sill from Youghal-based Passive Sills, certified by the Passive House Institute.
https://passivehouseplus.ie/magazine/upgrade/cork-retrofit-blitzes-new-build-nzeb-standard#sigProIdd8a0a1e62c
“We decided to put the capital into the building structure by having all the elements and construction details to passive standard, and keep the mechanical to a simple, cost-effective, well-proven and low maintenance system,” he says.
Specifically, he opted for a condensing gas boiler (to an existing gas supply connection), a solar thermal hot water system, solar PV panels and an Aereco demand control ventilation system.
Although Dehaye is mindful of the environmental impact of opting for a fossil-fuel burning set-up, the system has been designed to be able to switch to a heat pump in future when budget allows.
Indeed, the decision to hold off on investing in a heat pump was made easier by some modelling Dehaye did with the DEAP software to compare the carbon emissions of an air-to-water system with the gas boiler and solar thermal, which found that the emissions were similar given the extent to which electricity production in Ireland still relies on fossil fuels.
“It means electricity production needs to continue to be cleaner and self-produced where possible to maximise the benefit of a heat pump,” he says.
So, the bulk of the budget went towards the fabric, including external insulation over the concrete blocks of the original dwelling, while the extension is a steel and timber frame structure built on site and insulated with cellulose insulation from Cork manufacturer Ecocel. Irish-sourced larch timber cladding was used for the front, and triple glazed alu-clad windows were fitted all round, with openable rooflights over the landing and kitchen.
This article was originally published in issue 30 of Passive House Plus magazine. Want immediate access to all back issues and exclusive extra content? Click here to subscribe for as little as €15, or click here to receive the next issue free of charge
Achieving airtightness in the existing structure was a challenge, however. “We were targeting one air change per hour but could not achieve it. For budget reasons and sustainability, we tried to keep as much partition and structure in place, which made it harder. We did achieve 1.9, which is very good for an existing structure but not enough to qualify the house for Enerphit.”
Dehaye also says that the installation of an Isover metal-stud acoustic insulation system to the party wall has been a big success.
“We completely forget we are living next to a family with three young kids in a semi-detached house,” he says.
The finished result is beautiful, inside and out, but the idea of delaying investment in heat pump technology might give some pause for thought. Indeed, this choice is not unlike the ones being made by many motorists interested in buying a new electric car but who have chosen to hold off until battery technology and ranges improve (and prices fall), and until further progress is made in greening electricity generation. This is especially true when considering the carbon intensity of grid electricity has dropped by over a third since 2010, that considerable further drops are inevitable within the lifespan of heat pumps installed today, and the potential of using heat pumps to help mop up wind energy generation at times when demand is otherwise low.
But as Dehaye puts it, the enhanced fabric in this now NZEB-compliant dwelling is there now for the next 40 or 50 years, while the heating system will have a likely lifespan of 15 years or so.
Selected project details
Client: Loic Dehaye
Architect: Loic Dehaye Architects
Civil & structural engineers: EIRENG Consulting Engineers
Main contractor: Garry McCarthy
Mechanical contractor: Trevor O’Mahony Heating & Plumbing
Electrical contractor: CMI Electrical
Airtightness tester: Clean Energy Ireland
Cellulose insulation: Ecocel
Wood fibre insulation: Gutex, via Ecological Building Systems
Insulated window sills: Passive Sills
Thermal blocks: Foamglas / Quinn Building Products
Roof & wall insulation: Isover
Additional roof insulation: Kingspan Insulation
Floor insulation: Kore
Airtightness products: Siga, Gerband
Windows & doors: Viking, via West Building Products
Roof slates: Tegral
Solar thermal system: Kingspan
Demand controlled ventilation: Aereco
Solar PV supply: Garo
Solar PV installer: Paul Sweeney Electrical
In detail
Building type: Deep retrofit to 95 sqm semi-detached house from 1938, plus two-storey side and rear extension & attic conversion. Finished floor area: 197.65 sqm
Location: Ballinlough, Cork
Completion date: February 2018
Budget: €280,000 (all works excluding fittings)
Before: E2 (381.62 kWh/m2/yr) After: A2 BER (40.72 kWh/m2/yr)
Energy performance co-efficient (EPC): 0.293
Carbon performance co-efficient (CPC): 0.241
MEASURED ENERGY CONSUMPTION
(gas + electricity): Before: 381 kWh/m2/yr (estimate)
After: 43.14 kWh/m2/yr (Feb 2018 to Feb 2019)
Energy bills (after): €532 on electricity incl. all charges & vat Feb 2018 to Feb 2019. €485 gas bill, incl. all charges & vat, in same period. Gas bill includes non-solar portion of hot water generation. Total: €1,058
Thermal bridging: Quinnlite blocks at base of extension walls, Foamglas blocks to all window & door thresholds, insulated window sill on external wall insulation system.
Airtightness (after, at 50 Pascals): 1.9 air changes per hour
GROUND FLOOR
Before: Uninsulated concrete floor
After: 150mm Concrete slab with 250mm
silver EPS insulation. Polished concrete finish to some parts. U-value: 0.1 W/m2K
WALLS (ORIGINAL)
Before: Concrete block-on-flat walls.
After: 150mm Platinum EPS insulation and silicone-based render finish externally to existing walls, 32.5mm insulated drylining internally. U-value: 0.15 W/m2K
Extension walls: Stick-built timber frame walls. External cladding (Knauf Aquapanel, Thrutone slate or Irish larch) followed inside by battens, breathable rain screen, 22mm Gutex wood fibre board, 200mm studs filled with cellulose insulation, 11mm OSB, 50mm Metac insulation to service cavity, vapour membrane & plasterboard. U-value: 0.15 W/m2K.
ROOF (ORIGINAL)
Before: Existing roof insulated on flat with 100mm mineral wool.
After: Side attic insulated with 350-400mm cellulose on the flat. U-value: 0.11 W/m2K. Attic room insulated with 100mm Metac between rafters, with airtight membrane & 90mm Kingspan insulated board beneath. U-value: 0.14 W/m2K
Side extension roof: Tegral fibre cement slates on battens/counter battens, followed underneath by breathable roofing underlay, 350-400mm cellulose insulation. U-value: 0.11 W/m2K
Rear extension flat roof: PVC roof followed beneath by 18mm Smartply OSB, ventilated battening, breathable roof membrane, counter joists, joists insulated with 300mm cellulose, airtight membrane, battened service cavity, plasterboard. U-value: 0.14W/m2K
WINDOWS & DOORS
Before: Double glazed aluminium windows. New triple glazed windows: Viking passive certified timber-aluclad windows & doors. Average U-value of 0.82 W/m2K
Roof windows: Flushglaze triple glazed flat roof window to sitting room. Overall U-value: 0.8W/m2K. Velux modular skylight system (2 x fixed & 1 x motorized) to kitchen. U-value: 1.20W/m2K. 3 x further motorized Velux thermally broken triple glazed roof windows to 1st floor landing, 1st floor bathroom & attic space. U-value: 1.20 W/m2K.
HEATING SYSTEM
Before: 20-year-old gas boiler & radiators; open fireplace.
After: Logic System s30ie gas boiler. 4 heating zones with time & temperature control, radiators with thermostatic valves. Solid fuel Termofoc C-130 stove. Kingspan Thermomax HP400 solar thermal system + 300 litre dual coil Telford Tempest solar cylinder. Hot water produced by solar thermal + gas.
VENTILATION
Before: No ventilation system. Reliant on infiltration, chimney and opening of windows for air changes.
After: Aereco demand controlled central acoustic fan for up to six wet rooms. 250m3/h. Passive stack ventilation via motorised roof windows.
Green materials: Cellulose insulation, timber frame extension, Irish larch cladding. 100% wool carpet, Irish limestone for patio finish. As much of the existing structure as possible retained. Electricity: 7 x solar photovoltaic panels. Avg. annual output of 1.6kW.
Image gallery
https://passivehouseplus.ie/magazine/upgrade/cork-retrofit-blitzes-new-build-nzeb-standard#sigProId53d0288ac7