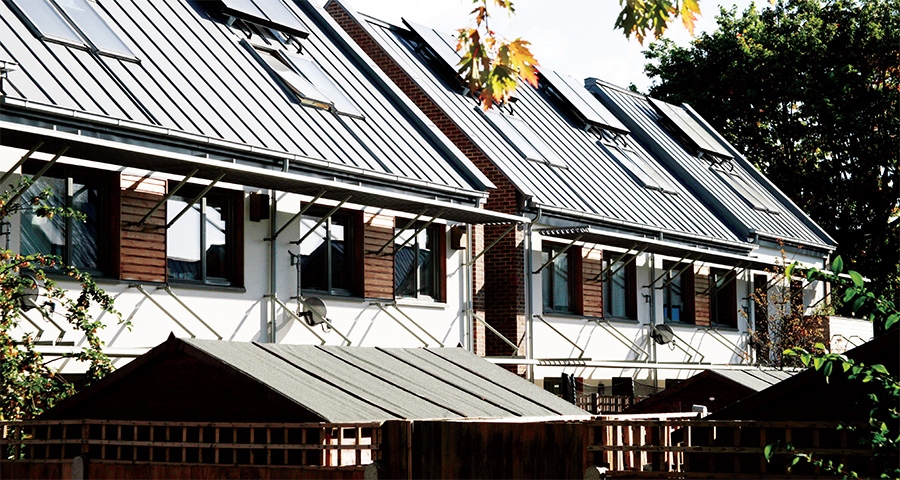
- New build
- Posted
Sussex social scheme pits passive against the code
In the absence of strong energy requirements under building regulations, much of the UK’s new build innovation has been driven by the Code for Sustainable Homes. Amid growing concern that the code’s attention to energy efficiency falls some way short of passive house, monitoring results from one social housing scheme offer a rare opportunity for direct comparison.
A development by Horsham housing association,Saxon Weald, breaks new ground by delivering passive housing to social tenants. Standings Court is a home development of 17 houses and 21 flats, 12 of which are passive, while the remaining 26 meet level 5 of the Code for Sustainable Homes.
Marie Riordan of Saxon Weald explains that an earlier housing project the association developed in Billingshurst was the first in the UK to achieve code 5. It was the success of that experience that prompted the association to see if an even better result was possible. “My concern with code was that you can borrow credits from different areas,” says Riordan, “so you don’t necessarily have to build a particularly good home, you can just whack on a load of technology to achieve the standard, whereas passive house was all about the building envelope, the insulation and airtightness. It just seemed to make more sense in terms of building sustainably.”
Standings Court, as one of the first passive social housing developments in the UK, provided a rich training ground for everyone involved. Neither architect MH Architects nor the contractor, Osborne, had built passive before. Energy consultant Warm ran the PHPP calculations and assisted in the design and specification of the build to ensure it made the standard. The company ran workshops with the architects during the feasibility stage, and throughout the design process, architect and energy consultant remained in constant contact.
The site itself lies close to Horsham town centre. The necessity both to retain existing access routes and achieve the right orientation for passive in a terrace form was one of the initial challenges faced by the design team. In addition, there were two existing mature trees which were the subject of tree preservation orders. Architect Nathanael King-Smith says that as it turned out, these constraints didn’t actually conflict with each other. “We wanted green areas and we wanted to integrate the two routes into town with the new scheme, together with the orientation for passive house. It all fell into place and worked quite nicely. It could have been a lot harder on a different site.”
The development includes passiveand code 5 dwellings
Getting around these physical constraints was one thing, actually achieving a pleasing design was another. “We wanted to design something that wasn’t just a box,” says King-Smith. “The design needed to be interesting, and interesting to live in. That was the challenge.”
Compromises were inevitable. The original design sought bay-windows, but the window profiles were so ‘chunky’ that they could not achieve the effect that the architect had hoped for, and so the bay windows were dropped. To avoid a flat and featureless façade, terraces were introduced to the northern elevations of the passive block while the bathrooms of these units protrude at ground floor level. These features required very careful detailing in order to ensure they didn’t compromise the thermal performance of the building envelope.
Mark Wellbelove of contractors Osborne says that the company had well established processesfor conventional building projects. But Standings Court required a reinvention of those processes.“Our close communication with Warm throughout the design period meant that we learned along the way...Understanding the passivehouse was one of the biggest hurdles.”
Structurally insulated panels (SIPs) were chosen as the build method. These were manufactured by a sister company of Osborne’s, Innovaré. On a field trip prior to his involvement in Standings Court, Wellbelove had seen OSB panels used as an airtight layer in a passive build. Because OSB panels were also being used in the SIPs under construction at Innovaré, it seemed a natural fit. Innovaré went on to develop a product specific to the passive house building envelope requirements.
Throughout the project, a system of checks, controls and sign-offs ensured compliance with all of the client’s requirements. During the build itself, the contractors produced a monthly validation report, complete with photographs and commentary, where any problems were highlighted, along with any remedial measures taken.
Knowing airtightness was going to be a big issue, the design and build teams went to great lengths to ensure that the passive units met the targets. Marie Riordan explains that the contractors ran ‘toolbox talks’ on site, in which the importance of the airtight layer was emphasised.“They explained, this is what you have to do, this is why you have to do it...If you do puncture through, tell somebody straight away.It was all about reinforcing those principles all the way through, a top down, bottom up approach.”
In some instances, problems did arise however when repeated tests failed to get the air leakage rate below one air change per hour, well short of the passive house requirement of 0.6. In particular, anxiety began to centre on the use of OSB as an airtight layer. “Some units passed with an OSB airtightness layer,” says Mark Wellbelove, “but with others we ended up having to put membranes onto the wall before we plasterboarded.” Ultimately, that attention to detail paid off and all of the units passed at or below the passive house threshold. “Once two or three guys were assigned to air leakage,”says Wellbelove, “they took on board the importance of it and why we’re doing it – they became quite passionate about it. That was great to see.”
One issue that has tended to arise with social housing tenants - and indeed any people occupying sustainable buildings by chance rather than design - is a failure to engage with the building's M&E systems. Marie Riordan says that at Saxon Weald’s code 5 development in Billingshurst, induction sessions were provided to help tenants familiarise them with the underfloor heating and ground source heat pump that were installed in the project. “What we found was that wasn’t enough for most people...So what Osborne and the project manager for Standings Court did was put together a DVD, and uploaded a video about the home to YouTube.”
This, she says, has yielded mixed results. Some tenants have had particular trouble grasping the concept of mechanical heat recovery ventilation and the necessity to run it constantly.“Even when you try to demonstrate how little it costs, there’s still some anxiety because it’s new and they haven’t had to deal with it before. Similarly with the requirement to clean the filters. It’s no different to cleaning out the filters in your cooker hood, but not everyone does that.”
Immediately after construction, two of the passivehouses together with a selection of the code 5 units were fitted with a range of monitoring equipment designed to assess their performance. Once a year’s worth of data had been collected, consultants SRE Ltd produced a report which contained a number of surprising results.
The two passive house units monitored used respectively 27% and 38% of the gas for hot water and space heating that had been predicted by PHPP. In addition, taken on a per-occupant basis, the passive house units used respectively 68.9% and 77% less gas over the year than the code 5 units. While the design team was gratified by the performance, it begs the question why the software was so inaccurate in its predictions.
The other key finding is that summer overheating is occurring on a regular basis in the passive units. In the two units monitored, the daily internal temperature exceeded 25C for 13.7% and 14.8% of the year respectively. One unit experienced a 15 hour period during which internal temperatures exceeded 30C.
John Trinick at Warm says that the reason for both the low gas consumption and the overheating is likely to be occupancy. “The biggest thing we are learning from monitoring social housing passive units is that the occupancy and the amount of time people are there doesn’t exactly match the passive house assumptions.The reality is that you have much higher internal gains. Instead of having 15 kWh/m2/yr of heating like we predict, you have almost zero, and you have a bit more overheating than you would have predicted.”
Trinick is careful not to overstate the overheating issue. “We’re finding overheating issues with passive house but it’s not necessarily because they’re passive house. A lot of it is because we’re looking. My house gets to 28C on hot days and it’s not a passive house, in fact it’s got almost no insulation whatsoever. But it’s badly designed. Overheating is a design issue...If you design a house without regard to overheating, you’ll cook, that’s true. It’s not a specific passive house issue.”
He says that the passive house community in the UK needs to look at designing for all kinds of different occupancies. Warm’s subsequent passive projects have built on the experience of Standings Court, adapting passive house modelling to take account of these lessons, particularly in a social housing context.
Likewise, the rest of the design and build team has capitalised on their experience in Horsham. “What we’re concentrating on doing now,” says Mark Wellbelove of Osborne, “is taking as many of those lessons we learned through Standings Court, taking them onto other schemes and applying that little bit of information to improve the quality of the build.”
Selected project details
Client: Saxon Weald Housing
Architect: MH Architects
M & E engineer: Derek Durant Associates
Civil / structural engineer:GEMMA Building and Design Services
Energy consultant: Brooks Devlin & Warm
Main contractor: Geoffrey Osborne Ltd
Quantity surveyors: Phillip Pank Partnership
Mechanical contractor: Nuaire Limited
Build system supplier: Innovaré Systems
Floor insulation: Cellecta
Windows and doors: NorDan UK Ltd
Roof lights: Fakro GB Ltd
Heat recovery ventilation systems: Zehnder
Condesing boilers: Vaillant
Photovoltaic supplier: Ecolution
Flooring: Charcon Flooring
Roofing: Boss Metals
Additional info
Development type: 38 home development - 17 houses and 21 flats, 6 designed for people with learning difficulties. Ranging from 87 sqm 3-bed two-storey houses to 112 sqm 4-bed three-storey houses,
with flats sized between 49 to 69 sqm. The code 5 houses are constructed using SIPs and timber frames, the passive houses are 3 and 4-bed homes between 101 and 111 sqm constructed using SIPs.
Location: Standings Court, Horsham, Sussex
Completion date: April 2012
Budget: £4.5 Million
Passive house certification: certified
Space heating demand (PHPP): 15 kWh/m2/yr
Heat load (PHPP): 10 W/m2
Primary energy demand (PHPP): 111 kWh/m2/yr
Environmental assessment method: Code for Sustainable Homes – level 4 for passive houses and level 5 for flats and remaining 5 houses
Airtightness (at 50 Pascals): 0.6 ACH or better
Energy performance certificate (EPC): B: 89
Measured energy consumption: 60.3 kWh/m2/yr (Sep 2012-Sep 2013) average across two passive homes monitored.
Thermal bridging: A logical approach was taken to designing and detailing each component to minimise heat loss. At each stage of the design process thermal modelling was performed by the consultants, Warm Associates, to identify problem areas and further iterations of the detailed design performed until acceptable results were obtained. Key examples include:
The structural frame within the SIPs panels
The standard SIPs panel uses solid timber frames, relying on the relatively good thermal properties of timber. When modelled these solid timber elements were completely unsuitable for use in passive construction and the frames were redesigned using smaller sections of timber and plywood webs forming a box section filled with insulation.
Fastenings connecting the SIPs panels
Usually connected using long ‘spikes’ driven from outside into the adjacent component. These provide a thermal bridge which would be unacceptable in passive construction. An alternative solution was devised using nails secured to a specially fabricated mandrel which was removed once the nail was in place. The resultant counter-bore was filled with insulation.
Also thermally broken window frames and insulated reveals, additional insulation on the internal side of the SIPS panel.
Ground floor: strip foundations with 175mm insulation between and under Tetris Eco Block floor system and 150mm insulation and 65mm screed over. U-Value 0.10
Walls: Brick course, 50mm cavity, breather membrane, factory-built 297mm SIPs panel, 25mm insulated service cavity, and 15mm plasterboard internally. U-value: 0.10
Roof: Falzonal zinc standing seam roofing on breather membrane on 18mm plywood decking with 50mm ventilation void, followed by 297mm thick SIPs panel on VCL and 100mm internal insulation then 25mm insulated services cavity , 15mm plasterboard ceiling. U-value: 0.08
Windows: NorDan Ntech Passive triple-glazed composite windows with argon filling and an overall U-Value of 0.7. Fakro FTT Thermo triple-glazed roof lights 0.94
Heating system: Vaillant Ecotec Plus 824 (89.4%) gas boiler supplying radiators to all rooms, plus solar hot water panels supplying separate domestic hot water tank
Ventilation: Zehnder Comfosystems CA200 with 92% efficient heat recovery
Electricity: N/A to the passive house units
Green materials: Offsite manufacuter of SIPs allows optimum amounts of material to be used, with all wood FSC certified. All principal elements achieved an A+ rating in the Green Guide to Specification, with the exception of the triple-glazed windows which feature PEFC certified timber and were given a bespoke rating of B by the BRE.
Image gallery
Passive House Plus digital subscribers can view an exclusive image gallery for this article. Click here to view