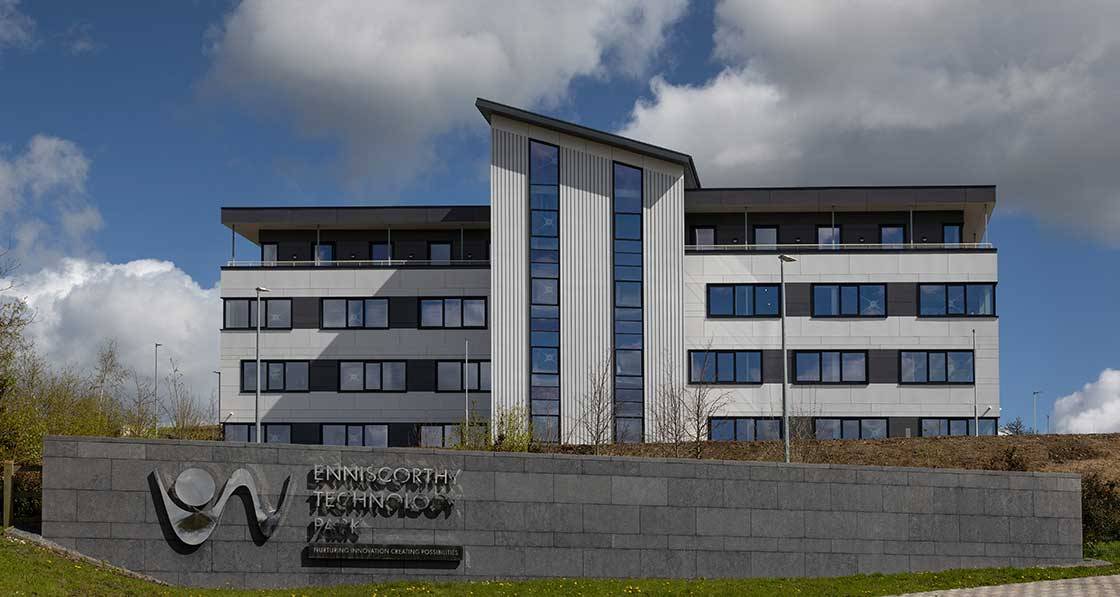
- New build
- Posted
Seal of office
While the passive house standard has had a lasting impact on the design and construction of new homes in Ireland, progress has been slower in commercial property. With the business world under increasing pressure to take meaningful climate action while providing better working conditions for staff, one new office building in the southeast may be a sign of things to come – and a beacon for a UN-affiliated project.
Click here for project specs and suppliers
Building type: Four-storey, 4,710 m2 office building
Method: Steel frame with celluloseinsulated timber panels
Location: Enniscorthy, Co. Wexford
Standard: Passive house classic
Embodied carbon: Meets RIAI 2030 Climate Challenge target
A landmark development on a prominent site just outside Enniscorthy in Co. Wexford has become Ireland’s first passive house certified office building. Built by longstanding passive house contractor Michael Bennett Group under a design and build contract, Senan House was designed by passive house architects MosArt.
With that combination of expertise behind it, this building was always going to be exceptionally high performing. It also represents an early benchmark in respect of embodied carbon for Irish office buildings.
“Ever climbed Croagh Patrick?”, architectural technologist Stephen Donoghue asks in response to a query about the challenges posed by the site. Enniscorthy is a hilly town.
Its new technology park – of which Senan House is the lead building – is cut into the side of a steep hill that runs down to the Wexford road and the river Slaney, which run parallel to each other for about five kilometers outside the town. During the early stages of the project, preparing a sloping site and getting levels right was very challenging, not least because of the unstable wet marl that comprises so much of the land in this part of the country. The payoff comes in a striking building with fantastic views. Senan House runs on a slightly cranked north-south axis, with views of the river valley to the west. You can see the town with its spires against the backdrop of the Blackstairs Mountains to the north while St. Senan’s Hospital – a distinctive Victorian building now converted into apartments – can be seen through the southern windows.
Art McCormack of MosArt explains that the reference building for this project was a successful tech incubation space called The Hatch Lab down the road in Gorey. Once brought on board by Michael Bennett, MosArt created a masterplan for the site, which included the construction of a sister building alongside Senan House. Wexford County Council, who plan a pedestrian and cycle bridge linking the town centre and the technology park, owned the site and supported the development through all its phases.
A variety of design options – including the possibility of creating a construction training centre – were explored before the team settled on a rational, flexible office building. The first plan ended at the third storey, but following input from Wexford County Council, it was decided to add a fourth, recessed, penthouse-style storey facing west to the river.
Further proof of the support of the local authority comes in the fact that it took just five weeks to get through planning.
“The steep site was one of the main design problems,” says Art McCormack. “So, we used the higher ground to the east to create a bridge and enter the building at the first floor level.”
In the original plan, the central bay which projects towards the river housed a multi-height atrium. The site was subsequently sold to a private company however, and, as McCormack puts it “they added insight into how the offices might be optimised.” Rentable floor space was expanded, and the atrium took on more modest dimensions.
McCormack explains the north-south alignment follows the contours of the site and makes sense in terms of road layout and how the building would be accessed via that aforementioned bridge linking the car park with the first floor.
The detailed design stage coincided with the pandemic and everything that went with it. A subcontractor was commissioned to provide the timber wall panels that the design team had settled on. Covid-related issues forced that contractor out of the project in mid 2020 however, and finding a replacement proved challenging. During this period, the design team almost decided on a cross laminated timber (CLT) construction. This is the process of using bonded layers of solid wood panels for floor, roof and wall elements, thereby achieving carbon savings that are vastly superior to concrete and steel.
In the end however, the financials didn’t add up, and PYC Construction stepped into the breach with their I-beam system. They built and supplied the factory-fabricated timber panel I-joist system that was used on the build – a low embodied carbon system designed to be airtight, breathable and windtight. The 240 mm wide panels comprise Propassiv boards on the inside taped at edges, I-beams fully filled with close to roughly 67 kg/m3 of Warmcel cellulose, Meditevent board and Pro Clima Fronta Wa, taped for wind tightness. While the panels came pre-taped, they were taped together for airtightness, and taped to the concrete slab and roof.
This article was originally published in issue 45 of Passive House Plus magazine. Want immediate access to all back issues and exclusive extra content? Click here to subscribe for as little as €15, or click here to receive the next issue free of charge
Stephen Donoghue lists the advantages of this build approach. “There’s less mess, it’s cleaner and safer, and the panels go up faster, plus you get better quality. And you don’t need scaffolding. There was no scaffolding erected on this building.”
In order to avoid thermal bridging where the external walls meet the structure, the panels were hung from the steel beams. This was one of several strategies deployed to ensure an unbroken thermal envelope. Though the bridge at the main entrance looks as though it’s connected to the building, it is structurally separate, and actually ends 5 mm from the wall. On the top floor, a 10 mm load-bearing insulation was used to separate the steel base plate which supports the roof canopy from the insulation below, and rainwater downpipes were wrapped with foil-backed insulation from roof to ground floor.
Windows, curtain walling and external doors are Passive House Institute certified. The windows have thermally broken aluminium frames, which were manufactured locally by Reynaers Aluminium. Unusually in an office space, all units are triple glazed, and glazing covers 23 per cent of the structure. At 1.34, the building has an excellent heat loss form factor.
According to the PHPP, there is zero risk that the air temperature will exceed 25 degrees over the course of the year. In the absence of brise soleil, overheating risks are mitigated by glass with three separate G values, ranging from 42.7 per cent down to 27.8 per cent.
Art McCormack notes that there was a particular overheating risk in an office high in the central bay, which projects east but also has exposure to the southern sun. Again, that risk was dealt with using glazing with a very low G value.
Doubts about the airtightness strategy planned for the raised mono-pitch steel panel roof prompted the build team to construct a mock-up onsite, and test its airtightness, just to see if it would work. It didn’t. The dovetailed system failed, so all the panel joints and roof-to-wall junctions were taped by airtightness contractor Aerzeal Ltd, with input from Joe Fitzgerald from Ecological Building Systems and Roman Sypura from Clioma House. The subsequent test confirmed an excellent score of 0.15 ACH at 50 Pa.
There is no oil or gas onsite – the office is fully electric. Integrated units from Nilan – two per floor – look after heating, cooling and ventilation. These units are connected to the Nilan Cloud system, a cloud-based management system which allows the facilities manager to remotely control the system as they wish, rather than going to individual control panels, and which enables remote servicing and maintenance. A large PV array supplements the power load. At one point, the plan was to mount the panels on the pitched roof, but the change to the roof spec as a result of airtightness issues prompted a rethink, and the panels – 119 in all – were relocated to the flat roofs.
The system was actually installed by the building’s first tenant – Pinergy Solar Electric. CEO Ronan Power explains the system generates an annual average power of just over 44,000 kWh, with peak power of just over 48,000 kWh.
“The install here was quite similar to those we’ve done with other corporate customers. Because this was a building still under construction rather than a retrofit, however, it was quite a complex lift and build, with a number of health and safety issues. So far, the generation appears to be excellent.”
The HVAC units have yet to operate. So far, things are really comfortable.
He expects the system to offset in the order of 20 per cent of the building’s total power demand. There is also an export connection under ESB Networks’ mini-generation connection process which effectively compensates users for any unused electricity that is exported to the grid.
Power says that he and his colleagues moved in last February. “We’ve our feet under the table at this point, and it’s great, we love it here. Senan is very aligned to our core values, in terms of sustainability, and it’s nice knowing we’re in a passive building.”
Though the company has not yet seen a full heating and cooling season, first impressions are very good.
“The building seems to be performing very well. Bear in mind, mine is a corner office, with two external windows. We’re monitoring humidity and CO2, and everything is staying within normal levels. There’s just ourselves – twenty-four people – and one other tenant so far. That’s not a huge load, and the HVAC units have yet to operate. So far however, things are really comfortable.”
And there’s no comparison with the company’s last office, he says, which was old, with all an old building’s flaws. It’s currently being retrofitted.
“Ours is a growing business, so this is ideal for us. We’ve got space to expand, and we signed a ten-year lease because we want to continue to stimulate employment here.”
-
The steel frame structure; the thermal envelope takes shape with PYC Construction’s cellulose insulated, airtight panels and windows and steel battens and counter battens The steel frame structure; the thermal envelope takes shape with PYC Construction’s cellulose insulated, airtight panels and windows and steel battens and counter battens
-
Heating comprises air-based heat distribution via two Nilan VPM 360 MVHR units per floor Heating comprises air-based heat distribution via two Nilan VPM 360 MVHR units per floor
-
The steel frame structure; the thermal envelope takes shape with PYC Construction’s cellulose insulated, airtight panels and windows and steel battens and counter battens The steel frame structure; the thermal envelope takes shape with PYC Construction’s cellulose insulated, airtight panels and windows and steel battens and counter battens
-
The steel frame structure; the thermal envelope takes shape with PYC Construction’s cellulose insulated, airtight panels and windows and steel battens and counter battens The steel frame structure; the thermal envelope takes shape with PYC Construction’s cellulose insulated, airtight panels and windows and steel battens and counter battens
-
Airtightness tests were conducted on a mock-up of the roof system to catch and address leakage issues Airtightness tests were conducted on a mock-up of the roof system to catch and address leakage issues
-
To obviate thermal bridging where the external walls meet the primary steel structure, the wall panels were hung by steel lugs from the steel beams To obviate thermal bridging where the external walls meet the primary steel structure, the wall panels were hung by steel lugs from the steel beams
-
To obviate thermal bridging where the external walls meet the primary steel structure, the wall panels were hung by steel lugs from the steel beams To obviate thermal bridging where the external walls meet the primary steel structure, the wall panels were hung by steel lugs from the steel beams
-
The windows have thermally broken aluminium frames, which were manufactured locally by Reynaers Aluminium The windows have thermally broken aluminium frames, which were manufactured locally by Reynaers Aluminium
-
A 10mm thick Farrat TBK structural load-bearing insulation was used to separate the steel base plate from the insulation within the structure A 10mm thick Farrat TBK structural load-bearing insulation was used to separate the steel base plate from the insulation within the structure
-
Precaution was taken to wrap rainwater down pipes with foil-backed insulation from roof to ground floor; Precaution was taken to wrap rainwater down pipes with foil-backed insulation from roof to ground floor;
Embodied carbon
A cradle-to-grave embodied carbon calculation was done by Ciaran Flanagan of MosArt using One Click LCA.
The scope included all the big ticket items within the building itself - the foundations, superstructure, thermal envelope, PV array and heat pump and ventilation system – but did not include the external works, including the car parking area, which would likely have added a significant amount. The building fit out was excluded, as were the ducts, pipes and cables for buildings services.
In many cases punitive default data from One Click was used, in the absence of Environmental Product Declarations, most notably in the case of the three largest sources of the building’s embodied carbon: the structural steel frame, concrete, and PV array, which respectively contributed 1,200 tonnes, 371 tonnes and 180 tonnes of CO2e to the building’s cradle-to-grave total of 2,357 tonnes – or 484 kg CO2e/m2 of gross internal area, comfortably inside the RIAI 2030 Climate Challenge target for offices of 750 kg CO2e/m2, albeit with omissions from the scope including a potentially large total for external works.
UN connection
One thing the project team could not have anticipated is the building becoming emblematic of a UN-backed high performance building initiative, but that is what has happened.
Early in the project, builder Michael Bennett organized a visit to the site by a delegation that included Scott Foster, then director of sustainable energy at the United Nations in Geneva. During his decade-long tenure at the UN, Foster worked with experts to develop the UN’s Framework Guidelines for Energy Efficiency Standards in Buildings that were at the heart of the high performance buildings initiative. The guidelines were endorsed by the Committee on Sustainable Energy in 2017 and then by the UN Economic and Social Council in 2018.
Foster credits Tomas O’Leary as a catalyst for the discussions that led to the creation of the guidelines.
Foster and Washington DC-based consultant Robert Cavey supported establishment of an entity in Enniscorthy, the Enniscorthy Forum, to support the UN’s sustainable development agenda. The remit for the forum includes not only buildings and the built environment, but also energy, diplomacy, health and education. In the process of the forum’s institution they worked with Michael Bennett, who championed Enniscorthy for the new organization and sits on the forum’s board.
Under the stewardship of CEO Barbara- Anne Murphy, the forum now has launched the Buildings Action Coalition, a global collaboration comprising partners from industry, communities, academia, NGOs, governments – all stakeholders in the built environment. “Our partners are dedicated to making real and rapid differences in the built environment around the world to enhance quality of life globally while meeting the climate challenge,” said Foster.
The coalition convened an international summit in Enniscorthy in June to celebrate the recent signing of a memorandum of understanding with the UN Environment Programme. The memorandum of understanding sets out a broad collaboration between the Enniscorthy Forum and the UN to advance the buildings breakthrough target proposed under the Glasgow Breakthrough Agenda. The target calls for near-zero emission and resilient buildings to be the new normal by 2030. Foster notes how helpful it is to have a landmark building in Enniscorthy that demonstrates how high performance can be achieved, “The forum’s logo represents the castle of yesterday, the building of tomorrow, and the bridge of transformation”.
Selected project details
Client: Moyne Point Ltd
Main contractor: Michael Bennett & Sons
Architects/passive house designers/ landscape architects: MosArt Ltd
Mechanical engineers: Arkman
Mechanical designers: Colman Reynolds Associates
Civil/structural engineer: John Quigley & Associates
Energy consultant: JOT Energy / IES
Quantity surveyors: Nolan Construction Consultants
Mechanical contractor: Ollie McPhilips Ltd
Ventilation contractor: AirCon Mech
Electrical contractor: Bunclody Engineering
Fire alarm & access control: Bluerock Networks
Airtightness tester/consultant: Greenbuild
Structural steel: Wall Steel
Structural thermal breaks: Farrat
Insulated wall panels: PYC Construction
Thermal building blocks: Mannok
Roof insulation: New Century Roofing
Floor insulation and screeds: Niall Barry and Co. Ltd
Airtightness contractor: AerZeal Ltd
Windows, doors and curtain walling: Reynaers, via Curran Aluminium
Cladding supplier: Cembrit, via New Century Roofing
Flooring and carpets: Matt Kilroy
Heating, cooling and ventilation: Nilan Ireland
Primary hot water system: Ollie McPhilips Ltd
Photovoltaic supplier: Pinergy Solar Electric
In detail
This building, Senan House, is the first in a series of buildings in the Enniscorthy Technology Park (ETP) that are intended to stimulate economic growth and development in Enniscorthy Town and its surrounds, as well as augmenting a sense of purpose and pride. The site, positioned on a slope that overlooks the river Slaney and its gentle flood plain, is highly visible from the town. A new pedestrian and cyclist bridge is planned to cross the river Slaney, linking the town centre and the ETP, thus ensuring greater sustainability. It has been commented that this building makes a 21st century contribution to the form and profile of the town that is noteworthy for landmark structures from bygone years, including the Anglo-Norman Castle and two elegant Victorian church spires.
Building type: Senan House comprises a four-storey detached office building of 4,710 m2 with the top-most floor set back as a gallery balcony to provide penthouse offices. Construction comprises factory-produced timber wall panels with Warmcel cellulose insulation that hangs on a steel primary structure.
Site type & location: The building is the first in the Enniscorthy Technology Park on a site owned by Wexford County Council and zoned for Business and Technology Park. It is a peri-urban site northeast of Enniscorthy Town, Co. Wexford looking onto the N11 linking to Wexford Town and over the river Slaney and its flood plain.
Completion date: February 2023
Budget: €6.5 million for construction and €8 million including site development and external works, but not including site purchase and professional fees.
Passive house certification: Passive House Classic (certification in process)
Space heating demand: 18 kWh/ m2/yr
Space cooling demand: 1 kWh/ m2/yr
Heat load: 10 W/m2
Space cooling load: 6 W/m2
Primary energy: 149 kWh/m2/yr
Heat loss form factor: 1.34 (Total thermal envelope of 5,708.32 m2 / TFA of 4,238 m2) Overheating: PHPP): 0 per cent of year above 25 C.
Number of occupants: 377
Energy performance coefficient (EPC): 0.52.
Carbon performance coefficient (CPC): 0.53.
BER (SBEM/NEAP): A2 (52 kWh/m2/yr)
Embodied carbon: 484 kg CO2e/m2 TFA, calculated using One Click LCA (cradle-to-grave, excluding operational energy and water). See article for detailed description.
Measured energy consumption: N/A – would require a minimum year’s occupation and use.
Airtightness: 0.15 ACH at 50 Pa or 0.540 m3/m2/ hr at 50 Pa.
Thermal bridging: Point thermal bridge where steel posts supporting projecting roof canopy at top floor meet the gallery. A 10 mm thick Farrat TBK structural load-bearing insulation (0.187 W/ mK thermal conductivity) was used to separate the steel base plate from the insulation within the structure. Thermal modelling was carried out at the plinth, particularly regarding the penetration of floor insulation by steel stanchions. Likewise, the plinth was modelled to see whether the thermal block used as a thermal break could be reduced. It was, thus, established that a reduction was feasible. Precaution was taken to wrap rainwater down pipes with foil-backed insulation from roof to ground floor, and ventilation ducts were isolated with insulation from the external walls. Main access via a steel and concrete bridge that remained structurally independent of the building. To obviate thermal bridging where the external walls meet the primary steel structure, the wall panels were hung by steel lugs from the steel beams.
Ground floor: 150 mm reinforced concrete slab reinforced with fiberglass thread on 125 mm PIR insulation (thermal conductivity 0.022 W/mK), on Visqueen EcoMembrane loose-laid polyethylene DPM, U-Value: 0.169W/m2K.
Walls: 8 mm Cembrit fibre cement rainscreen board, on treated and planed timber battens and counter battens faced with EPDM and profile ribs, on factory-fabricated s.w. wall panels from PYC Construction comprising Pro Clima Solitex Fronta WA membrane, on 12 mm Smartply Medite Vent Board (vapour-open), 240 mm deep I-sections @ 600 mm centres filled with blown Warmcel cellulose 0.15 W/mK thermal conductivity), on 12.5 mm Smartply ProPassiv airtight board on 12.5 mm plasterboard. U-value: 0.152 W/m2K
Roof: Single-ply membrane with standing seam on pitched roofs on RK Roofliner with 10 mm insulation. U-value: 0.12 W/m2K This insulation abuts directly to the perimeter parapet balustrade and to high-density Rockwool insulation beneath the recessed glazing forming part of the wall for the top floor in order to minimise thermal bridging.
Fenestration: Passive House Institute certified windows, curtain walling and external doors. Aluminium thermally broken frames with argon-filled triple glazing. Whole-window and curtain walling U-value installed: 0.63-0.90 W/ m2K, depending on orientation. Average U-value installed: 0.71 W/m2K.
North-facing glazing: U-value of 0.6 W/m2K and a g-value of 42.7 per cent.
East, south and west-facing glazing: U-value of 0.5 W/m2K and a g-value of 36.7 per cent. Modelling with SBEM established that a single office located above the main entrance and with east and south exposure could suffer from more critical over-heating and, thus, comprises a U-value of 0.5 W/m2K and a g-value of 27.8 per cent.
Doors: Installed U-values of 0.93-1.3 W/m2K, depending on orientation. Typical Psi-values for fitted windows are 0.060 W/mK at heads, 0.047W/mK at cills and 0.058 W/ mK at jambs.
Heating, cooling and ventilation system: Air-based heat and cooling distribution via the 2 x Nilan VPM 360 heat recovery ventilation units per floor. Each unit has a 3,600 m3/h capacity, combining passive and active heat recovery as well as heating and cooling to all office spaces. The building is completed to a shell and core standard with fit-out by future tenants. Individual split units to meet localized heating and cooling needs if necessary for each office area are, therefore, to be selected as tenants assume occupancy.
Electricity generation: Vertex S solar photovoltaic array with an average annual output of 44,386 kWh and 48,196 kW peak power. The majority of the electricity thus produced is used on site, with the excess exported to the grid. Four car parking EV chargers fitted and there is a provision in 20 per cent of car parking spaces for future EV charging.
Sustainable materials: Timber frame panels using FSC certified timber; cellulose insulation, glass fibre reinforcement in (above ground floor) concrete floor slabs instead of more conventional steel reinforcement bars, locally produced high performance windows and curtain walls.
Image gallery