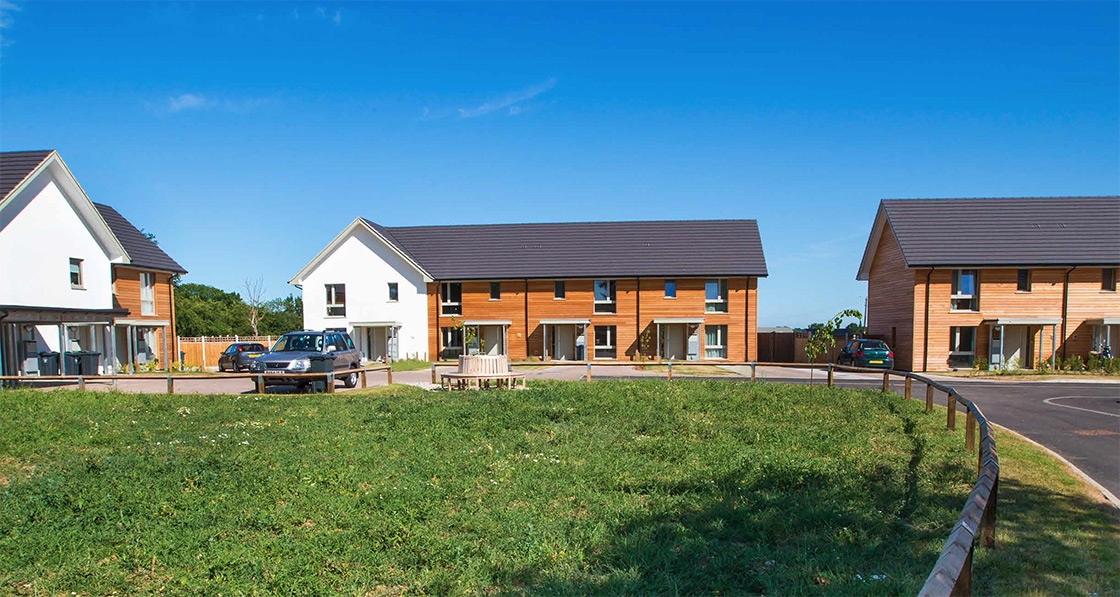
- New build
- Posted
Hastoe Scheme adds to passive affordable housing trend
With a number of trailblazing housing associations and councils building social and affordable housing schemes repeatedly to passive standards, the notion that the world’s leading low energy building standard is the preserve of the well-off doesn’t stand up to scrutiny, as Hastoe’s latest Essex passive house scheme demonstrates.
Click here for project specs and suppliers
This article was originally published in issue 15 of Passive House Plus magazine. Want immediate access to all back issues and exclusive extra content? Click here to subscribe for as little as €10, or click here to receive the next issue free of charge
This new development of 14 units in Essex marks the latest in a long line of passive house projects for Hastoe Housing Association, now one of the UK’s most prolific passive house developers.
The project at Hatfield Heath features 11 units that are certified to the passive house standard, and is the latest in a long line of passive house projects by Hastoe and architects Parsons + Whittley.
Having carried out a local housing needs survey, Hatfield Heath Parish Council then invited local housing association the Hastoe Group to act as a developer for a new affordable housing scheme.
The team found a rural exception site — a plot where private housing is not allowed, but affordable or social housing can apply for planning — on the edge of the village, and brought on board leading Norfolk-based passive house architects Parsons + Whittley. “The Parish Council was very supportive [of passive house],” says Ulrike Maccariello, development manager with the Hastoe Group.
“They really appreciate the high sustainability level.” She adds: “The scheme also facilitates some allotment spaces — that was really important for the parish.”
Parsons + Whittley have history with Hastoe now — the firm has designed about 50 passive house projects for the association across various schemes.
Hastoe currently builds 20% of its new housing units to the passive house standard, and has built 105 passive units so far, with 58 more on the way, making it one of the UK’s leading passive house developers.
The ground floor is insulated with 400mm of Dow Floormate XPS
Hastoe builds the other 80% of its units to Code for Sustainable Homes level four, but with the demise of the code, the association is currently looking to adopt a new standard for the majority of its new build.
Parsons + Whittley has also designed units for Hastoe to the AECB Silver standard. Architect Chris Parsons praises Hastoe for the association’s “genuine attempts to lower energy use and preserve comfort”.
At Hatfield Heath, the walls of the 14 units are of simple lightweight aircrew block construction with external insulation, with internal wet plaster forming the airtightness layer.
“We decided that we would go for masonry again. I quite like the thermal mass, and I think it’s a cost-effective method of delving the thermal performance we need,” says architect Chris Parsons.
“It’s skills that are available locally, materials that are available locally, and a technique that we used before that worked.”
The ground floor is a raft foundation insulated with 400mm of Dow Floormate XPS, while the roof is insulated on the flat with 500mm of Knauf Earthwool. Windows are triple-glazed passive house Internorm timber-aluminium units, supplied and fitted by passive housespecialists Ecohaus Internorm. Perhaps not surprisingly considering the experience the team has in building to the passive house standard, the build went fairly smoothly.
The walls are of simple lightweight Airtec block construction and are externally insulated with Lambdatherm graphiteenhanced EPS
“It went pretty much to plan if I’m honest,” Parsons says. “We had a little bit of a struggle with some airtightness, but we went back and sorted it out.”
It was Hastoe and Parsons + Whittley’s second time working with contractor DCH Construction too.
”They’re really very conscientious contractors who were keen to learn, keen to understand,” says Parsons.
The houses are ventilated by Zehnder MVHR units, and Parsons says there was some discussion among the team about whether to install rigid or flexible ducting, with Chris Parsons favouring rigid Lindab ducting, even though it required a more careful design and construction process.
“I just feel that if you’re burying ducts in the structure of the building, you should probably use the best product you can,” he says. “That’s not to say plastic flexible ducting is necessarily a bad thing.”
Specifying rigid ducting posed a design challenge though, Parsons says. “How do you design your space joists so you can feed rigid ducting in, and when do you install it during the construction process?”
Ultimately the team put all the long ducting runs into the joists during construction, then came back at the end of the project to connect all the ducts up.
The houses are all heated by Baxi combi gas boilers delivering to, in most instances, single radiators downstairs and towel rails upstairs in the passive house units.
“We just decided it would be very good to keep things, especially the M&E, very simple,” said Maccariello. “In the summer you turn it down, and in the winter you turn it up to a temperature that you’re comfortable with, and then you just leave it.”
“People are quite used to having gas central heating, even though we only have two or three radiators in the house — it’s easy.”
On a previous scheme Hastoe had specified a more complicated gas heating set up, with all heat delivered through the MVHR, and found it more difficult to find local engineers who could service the system.
Chris Parsons specified, he says, the simplest thermostat he could find. “All I wanted was something that goes from 0C to 30C and lets people turn the dial.”
Four of the houses are being monitored for temperature, relative humidity, CO2 and energy consumption, but the data had yet to be processed at the time of writing.
Parsons says: “This is probably the first scheme in which we did some detailed induction or handover for tenants.”
This involved spending 45 minutes to an hour with each tenant to explain the principles of a passive house, the ventilation, the heating system and so on.
“A lot of them have no prior knowledge of passive house, or any form of sustainable housing,” Maccariello says. “It’s basically to give them the knowledge to get the best out of their new home.”
Tenants moved into the houses about a year ago. Maccariello says feedback from has been very positive so far. “At Hatfield Heath they have sort of just gone through their first winter. It hasn’t been a particularly harsh winter, but there wasn’t any negative [feedback].The residents are generally very happy in their homes.”
One thankful and unintentional by-product of building to the passive house standard is that, even though the house sits right under a major flight path for Stansted Airport, it’s still quiet inside.
“With the triple-glazed windows, you can’t really hear the airplanes inside the houses,” Maccariello says.
This was by accident more than design though, she says. “Nobody thought about it. We did a time lapse film, and when we did some of the interviews on site, we had to stop filming every few minutes because another airplane came over. That’s when we realised it’s right under the flight path.”
Hastoe now has extensive experience building to passive and other green building standards, but Maccariello says it’s difficult to tease out how much more passive costs compared to the mediocre energy efficiency demands of English building regulations.
“We haven’t done a cost comparison exercise for some time. I would think it’s probably around 10% [extra] or below, but we haven’t done a proper analysis.”
She says the thing Hastoe likes about passive house, because of the certification process, is certainty of performance. With the Code for Sustainable Homes, you can put extra resources in and not be sure what the exact benefits to residents are. But with passive, he says: “You have lower energy bills, but you’re just comfortable.”
“The main driver for us to deliver passive house is fuel property in rural areas,” she says. “It’s really important to us that our residents can afford to live comfortably.”
Selected project details
Client: Hastoe Housing Association
Architect: Parsons + Whittley Architects
Contractor: DCH Construction
M&E engineer: Engineering Services Consultancy
Civil engineer: Donald Hall Associates
Structural engineer: Ken Rush Associates
Quantity surveyor: AECOM
Mechanical contractor: Bentley Mechanical Services
Electrical contractor: Kim Daplyn Electrical Services
Passive house certifier: MEAD Energy & Architectural Design
Airtightness tester: Anglia Air Testing
Wall insulation: SPS Envirowall
Additional wall insulation: Dow
Thermal breaks: Ejot
Roof insulation: Knauf
Floor insulation: Dow
Airtightness products: Ecological Building Systems
Windows: Ecohaus Internorm
Gas boiler: Baxi
Radiators: Stelrad
MVHR: Zehnder
Additional info
Building type: 14 affordable housing units across three terraces in rural Essex, 11 of which are built to the passive house standard
Location: Broomfields, Hatfield Heath, Bishop’s Stortford, Essex
Completion date: February 2015
Budget: £1.94m
Passive house certification: 11 units certified
Other environmental certification: Code for Sustainable Homes Level 4
Space heating demand (PHPP): 14kWH/m2/yr
Heat load (PHPP): 9 W/m2
Primary energy demand (PHPP): 93 kWh/m2/yr
Airtightness (at 50 Pascals): All units achieved 0.6 air changes per hour
Energy performance certificate (EPC): B (87)
Ground floor: 300mm concrete raft with 400mm XPS structural insulation and sub-base. U-value: 0.085 W/m2K
Walls: Envirowall silicone render system or Siberian Larch cladding on 285mm Lambdatherm 70 graphite-enchanced EPS insulation (thermal conductivity 0.032W/ m²K), on Thomas Armstrong AirTec ‘Standard’ Wall Block (thermal conductivity 0.11W/m²K), with gypsum based two-coat plasterwork internally for airtightness. U-value: 0.106 W/m2K
Roof: Concrete interlocking tiles on battens on vapour permeable underlay on timber roof trusses, with 500mm Knauf Earthwool Loft Roll on the flat. 15mm Gyproc plasterboard to internal ceilings, with two-coat lightweight plaster system for airtightness. U-value: 0.91 W/m2K
Windows: Internorm HomePure HF310 triple-glazed timber-aluminum composite windows and doors. g-value: 61%, Overall U-value: 0.87.
Heating system: Baxi Duo-Tec Combi Boiler GA 20KW natural/mains gas boiler, with one radiator downstairs and one towel rail upstairs to passive house units. Radiators sized for low temperature operation.
Ventilation: Zehnder ComfoAir CA200 mechanical ventilation system with heat recovery, Passive house Institute certified to have an efficiency of 92%.
Image gallery
Passive House Plus digital subscribers can view an exclusive image gallery for this article. Click here to view