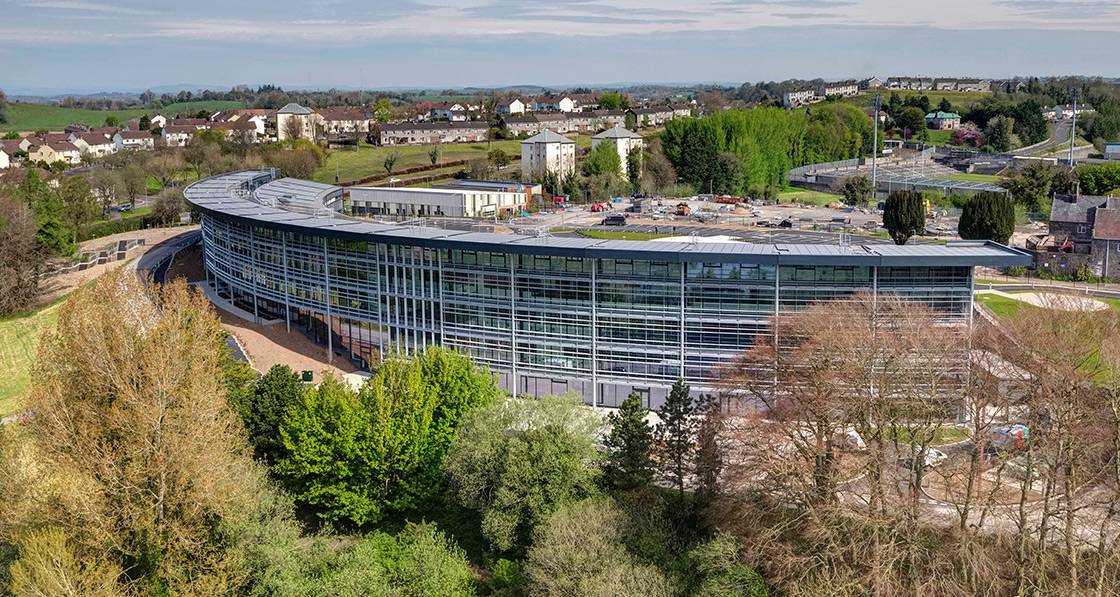
- Feature
- Posted
Learning curves
Since Erne Campus opened its doors in September, students of South West College in Enniskillen can now experience one of the world’s most environmentally advanced higher education buildings, and the largest building in the world so far certified to the passive house premium standard, in recognition of both its highly efficient building fabric and the large amount of solar energy it generates.
Click here for project specs and suppliers
Building: 7,950 m² four-storey educational building
Method: Steel frame with timber frame & masonry infill
Location: Enniskillen, Co Fermanagh
Standard: Passive house premium
On the banks of the River Erne, in the heart of Enniskillen, Northern Ireland, a brand-new passive house campus is pushing the boundaries of sustainable design and energy efficient building.
In a series of record-breaking achievements, the newly completed Erne Campus, part of South West College, is both the largest building and the first educational building in the world to achieve passive house premium certification.
It is also the first building in the UK to achieve both passive house premium and BREEAM Outstanding accreditations.
Passive house premium is awarded to buildings that not only meet the passive house standard for fabric efficiency and ventilation, but that also generate a significant amount of renewable energy on site.
Erne Campus, designed and constructed with meticulous attention to the building fabric, features nearly 1,600 photovoltaic panels on the roof, capable of generating 116 kWh per square metre of floor area, with excess energy stored in Tesvolt batteries.
The £30 million project (including £19.4 million in direct construction costs for the building) was funded by the Department for the Economy in Northern Ireland.
It recently opened its doors to students, offering 85 part-time and full-time courses ranging from accounting to creative media, cyber security, and visual media. Erne campus, which replaces the existing campus building at Fairview in Enniskillen, will accommodate more than 800 full-time students, 2,000 part-time students and 120 staff.
“It feels like a once-in-a-lifetime opportunity to be involved in a project like this and everyone involved feels a huge sense of pride,” says Eimear Grugan, project sponsor in South West College. “The college has always had a great interest in sustainability and has been a provider of passive house courses for the past number of years,” she says.
Having developed the CREST (Centre for Renewable Energy and Sustainable Technologies) Pavilion to passive house and BREEAM Excellent standards in 2016, South West College was ready to take its sustainability journey one step further with the Erne Campus project, which went to tender in 2017.
Incoming fresh air is delivered through an earth pipe system.
The college and integrated consultancy teams decided to aim for passive house premium and BREEAM Outstanding before the project went to tender, explains Grugan. “We felt we were doing something new and ground-breaking, and there’s an excitement in that, but the flip side is the risk, because it was unchartered territory for all of us,” she says.
“The college had tremendous aspirations for the building,” says Karl Pedersen, a partner in Mullarkey Pedersen Architects and project architect for the Tracey Brothers design and build team. Although it was a “huge challenge,” he says, “teamwork was one of the key elements in achieving those aspirations.”
“That everyone buys in is so crucial, because you’re only as strong as your weakest link,” he says. Pedersen recalls the “constant pressure” and intensity of work that accompanied the design, assessments and calculations, both pre-construction and once on site. “There were a few sleepless nights!” he jokes, but “we are delighted to have achieved passive house premium,” he says.
Located on the former site of a hospital, the campus has a large, multi-storey atrium all along one side, and is built in an elongated crescent shape that is 20 metres high, with a south-facing, triple-glazed façade designed to capture passive solar gain. The rear of the building has a timber framed structure, which is externally clad in brickwork and panels, and there was an emphasis on minimising thermal bridging throughout the design.
Technical details aside, says Pedersen, “we always come back to those fundamental issues” of how to heat and cool the building, how to get fresh air into it, and how to retain heat. “Those are key environmental issues that humans have been struggling with for thousands and thousands of years.
With a treated floor area of 7,167 m2, a length of 200 m, and four storeys of elevation, the size and shape of the building were one of the many hurdles the project team had to overcome. One easy way to monitor and record the construction process on a site as large as the Erne Campus was to use photographic evidence, says Pedersen.
Airtightness, on a building of that scale, was a huge, huge challenge.
“A lot of passive house [teachings] are geared towards the domestic market and traditional house building,” says Donal McGloin of Tracey Brothers. “Airtightness, on a building of that scale, was a huge, huge challenge,” he says.
The main frame of the building is made of steel, combined with timber framed wall elements and solid concrete flooring across all levels. The removal of cold bridging in the structural steel frame was a primary concern for the project team, particularly where the steel frame connects to the foundation or floor, and the external shell of the building. “We had to design and model all details to ensure we overcame that challenge,” says McGloin.
Thermal 3D modelling was crucial in allowing the team to “identify exactly where cold passages were happening,” says Pedersen “and we used this to modify our design details to eliminate the cold bridge(s).”
A number of trial airtightness tests were carried out on site during construction, to test design and workmanship at various interfaces, and these provided positive results.
The building ultimately achieved an overall airtightness test result of 0.36 air changes per hour (ACH), comfortably inside the passive house standard of 0.6 ACH (never mind the building control requirement of 10 m3/h/ m2).
Overheating was a concern for the team from early on. At the design stage, 3D modelling using a Sketch Up helped to avoid excess summer heat, says Pedersen. In addition, key features of the building that help to prevent summer overheating include the selection of glass, the shading provided by brise soleil on the external walls, a five-metre roof overhang and the presence of maintenance walkways, which provide shading, as well as automatic opening vents in the façade for cooling. Exposed concrete soffits internally also help to absorb temperature peaks.
It feels like a once-in-alifetime opportunity to be involved in a project like this.
“Since the façade was completed, we have worked through winter and through summer,” McGloin says, adding that it was “a very comfortable environment to work in temperature-wise.”
The south-facing atrium also acts as a thermal buffer to the low north-facing teaching spaces. Heat can either be mechanically dumped into the atrium from the teaching spaces, or taken from the atrium by the teaching spaces, to heat and cool them. The heat in the atrium space, meanwhile, can be purged in the summer by stack ventilation, with automatically opening windows at low level and roof level within the atrium.
The site-based control by Tracey Brothers also helped to ensure that the entire construction team bought into the concept of passive house design, says Pedersen. “If you’ve got a couple of hundred men on site, each one of them has to buy in to the project, because they could be opening up airtightness issues that no one actually would know about.”
Early planning and coordination were vital ingredients to the success of the project, according to McGloin. “Early involvement in the design, before getting to the site, was absolutely essential in achieving the airtightness result that we got,” he says.
Three members of the design and construction team were qualified passive house designers, and training in passive house principles was provided to everyone on site.
A workshop delivered by the passive house certifier at the pre-construction stage ensured everyone was aware of what was being fed through the passive house software, PHPP.
“Everybody knew what we had to achieve and how difficult it was going to be, but the training and the workshops all paid dividend for us,” McGloin says.
“As we did come up against issues, we were able to resolve those through design recalculation,” says Pedersen, also noting that “the treated floor area calculation was critical” to the overall achievements. When it came to design calculations, other key factors for balancing heat gains and losses included the overall volume of the building, the number of students that would use the building, and the amount of electronic equipment they would use. Installing the correct amount of glazing was another important consideration in avoiding overheating and achieving the required U-values, says McGloin.
The two renewable energy systems in place for the building are: solar powered battery storage, provided by the nearly 1,600 photovoltaic panels on the roof of the building, and a combined heat and power (CHP) biofuel unit. Gas boilers in the building are intended to act as back-up.
This article was originally published in issue 40 of Passive House Plus magazine. Want immediate access to all back issues and exclusive extra content? Click here to subscribe for as little as €10, or click here to receive the next issue free of charge
The solar panels provide energy to the mechanical heat recovery units that circulate air around the building, explains McGloin.
Incoming fresh air is first drawn through an earth pipe system, whereby three ground pipes temper the air from outside – boosting its temperature in winter, and reducing it in the summer, before being delivered to the mechanical ventilation systems, allowing them to operate more efficiently. In addition, a small number of windows can be opened in the building to provide natural ventilation.
For Pedersen, one take-away from this project is to “try to use as many passive house certified products as possible,” as the alternative is to get uncertified products tested and proven compliant, which takes time.
An enormous amount of time was spent on supply chains to deal with the specification of the materials, says Pedersen. It is important that “buildings are treated holistically,” he comments. “Sustainability isn’t its own little chapter, or its own little element. It has to be seen in combination with everything else that’s going on in the building. We’re working with the materials and the people that are available around us.”
Overall, the project demonstrates that “in a rural town in the northwest of Ireland, you can create a world class, environmental building. And that’s through the application of knowledge of how you go about detailing things, but also the diligence of the locally based contractor’s team and their willingness to rise to the challenge. I found that very satisfying throughout the whole project,” says Pedersen.
-
Erection of the steel frame Erection of the steel frame
-
Pipework for the earth pipe system, which tempers fresh air that is delivered to the building Pipework for the earth pipe system, which tempers fresh air that is delivered to the building
-
Laying the 250 mm hollowcore concrete slabs Laying the 250 mm hollowcore concrete slabs
-
OSB infill panels to the steel frame OSB infill panels to the steel frame
-
The top floor of the building during construction with timber frame elements and sub floor visible, housing various services The top floor of the building during construction with timber frame elements and sub floor visible, housing various services
-
Installation of Xtratherm Thin-R insulation to floor Installation of Xtratherm Thin-R insulation to floor
-
Underfloor heating pipes and 75 mm screed above this Underfloor heating pipes and 75 mm screed above this
-
Middle floor during construction showing ventilation pipework, and with floating floor in place Middle floor during construction showing ventilation pipework, and with floating floor in place
-
Service corridor outside the building with ducting for earth tube system visible Service corridor outside the building with ducting for earth tube system visible
https://passivehouseplus.ie/magazine/feature/learning-curves#sigProId4ad0ff1bbc
The uncertainty brought about by the Covid-19 pandemic presented additional challenges, notes Grugan. The site had to close for several weeks, moving the completion date back from spring 2020 to April 2021, she recalls.
Now that college staff have moved into the new campus, everyone is still learning how the building works, especially during this summer’s heatwave, and evaluation is ongoing, but feedback has been very positive, says Grugan.
“People talk about the feel of the building, the light, the freshness of the air,” she says. “I think that’s a huge testament to the design, because something that can evoke a feeling, an emotional reaction, means that you’ve touched somebody.
Not only have you fulfilled the functional aspect, but you’ve also transcended beyond that,” she says.
The building offers many different learning spaces and experiences for students, says Grugan, including the large atrium, socialisation and breakout spaces, and staff rooms. “You’re struck by the calmness of the building,” says McGloin. “Because of the high level of airtightness and insulation, acoustically, you’re in a very quiet space. You also have a comfortable building temperature-wise.”
The inception of the CREST Pavilion back in 2015 was the start of a journey that has led to the college becoming an international passive house hub, says the college’s active head of business development, Barry McCarron, who is also the current chairperson of the Passive House Association of Ireland.
Not only have you fulfilled the functional aspect, but you’ve transcended beyond that.
“We have in that time supported industry with 70 research and development projects in sustainable construction to the value of one million euro and directly trained over 250 construction professionals in both passive house designer and trades courses,” he says. The college has also been invited to become a United Nations Centre for Excellence for High Performance Buildings, and recently hosted a workshop at COP26 on how buildings can mitigate climate change.
Students will now have another a real, cutting- edge passive-certified building to learn from. Karl Pedersen says: “I think having the opportunity to learn in a building which is what they’re learning about is going to be a great benefit. […] Hopefully they will realize that the world is your oyster, and whatever decisions you make fashion how the world is going to change, and everyone can do that.”
“It’s wonderful for students to have this facility on their doorstep,” says Grugan, adding that the new campus “should give them a huge sense of pride in their surroundings, and confidence in the courses that are being offered to them. Hopefully that leads to greater confidence and self-belief in the students themselves, so they can feel they can compete with anybody and go out into the world and make their mark, and know that the building and their education prepared them for life. What more could you ask for?”
Selected project details
Client: South West College
Main contractor (design & build): Tracey Brothers Ltd
Design stage architects: Hamilton Architects
Construction stage architects & passive house design: Mullarkey Pedersen Architects
Client-side quantity surveyors: ESC Construction Consultants Ltd
Design stage structural engineers & BREEAM assessors: Tetra Tech
Contractor’s structural engineers: Albert Fry Associates
Design stage M&E consultants: Bennett Freehill
Contractor’s M&E consultants: Semple McKillop
Post construction BREEAM assessors: Tracey Brothers Ltd
Passive house certification: Passive House Academy
M&E contactors: AEM Ltd
Curtain walling & window installers: D & K Architectural Systems
Curtain walling system: Metal Technology
Primary insulation supplier: Xtratherm
Airtightness products: Glidevale Protect
CHP units: Fleetsolve
Earth pipe: Rehau
Radiators: Versatile
Heat recovery ventilation systems: GDL
Air conditioning: Zircon
Boilers: Elf Combustion
Underfloor heating: Alternative Heat
Rainwater harvesting: Rainwater Harvesting Ireland
Solar PV: Solmatix
In detail
Building type: 7,950 m² four-storey steel frame third-level educational building
Location: Enniskillen, Co Fermanagh
Completion date: April 2021
Budget: £19.4 million direct construction costs Passive house certification: Certified passive house premium
Space heating demand (PHPP): 8 kWh/m²/yr
Heat load (PHPP): 9 W/m²
Primary energy demand (PHPP): 41 kWh/m²/yr
Primary energy renewable demand (PER demand): 27 kWh/m²/yr
Renewable energy generation: 116 kWh/m²/yr
Heat loss form factor (PHPP): 1.65
Overheating (PHPP): Frequency of overheating less than 5 per cent over 25 C. This will mostly be during the height of the summer, when the college is in low use.
Number of occupants: 480 (PHPP)
Environmental assessment method: BREEAM Outstanding
Airtightness (at 50 Pascals): 0.36 ACH
Energy performance certificate (EPC): B 86
Measured energy consumption & costs: Not available yet
Thermal bridging: Thermally broken window frames centred on wall insulation layer, insulated reveals. Bespoke details that were confirmed by thermal calculations. Steel frame within thermal envelope as far as possible. Insulated timber framed walls to north, east and west elevations: externally hung off steel structure, then brickwork facing. In the curtain walling elevation on south façade, balcony supports penetrating envelope reduced to minimum, and thermally stopped. First course of Mannok blocks. Y-value (based on ACDs and numerical simulations): 0.08 W/mK
Ground floor: 150 mm compacted base followed above by 25 mm sand blinding, 250 mm thick hollow core slabs, 1 mm DPM, 90 mm Xtratherm XT/ UF insulation, 75 mm screed, floor finishes (mix of tiled flooring, sprung timber floor, vinyl flooring). U-value: 0.11 W/m²K
Walls: Brick outer skin followed inside by 50 mm air gap, then breather membrane/wind barrier on 9 mm OSB board sheathing, on 150 mm Xtratherm Xtroliner XO/FB insulation between timber studwork; then airtightness barrier on 100 x 38 mm battens (service zone) with 100 mm Xtratherm Xtroliner XO/FB insulation (0.021 W/mK) between timber studwork. Finished internally with 13 mm plasterboard. U-value: 0.13 W/m²K
Roof: Single Ply Sika-Trocal membrane roof on 140 mm insulation (Xtratherm FR- ALU) with thermal conductivity of 0.022 W/mK, on vapour control layer (S-VAP 5000E SA), on profiled metal deck. U-value: 0.15 W/m²K
Glazing: Metal Technology triple glazed powder coated aluminium windows, with argon filling and a project U-value of 0.7 W/m²K
Heating: The ground floor auditorium and atrium spaces are heated via underfloor heating from an air source heat pump. The remainder of the building is heated via low water content radiators served with hot water from a Fleetsolve bio fuelled CHP plant which feeds a 3,000-litre buffer vessel. Gas boilers are for back up only in case of CHP failure. Water is distributed through multi-layer composite pipework insulated with phenolic foam. The only active cooling is in the fitness suite which has a 14 kW fan coil powered by the solar PV.
Hot water: Generated via indirect cylinders with a coil served from the CHP buffer vessel and also large 6 kW immersion to avail of electricity generated by the solar PV array. Water distributed through multi-layer composite pipework that is insulated with phenolic foam.
Lighting: The entire building’s lighting system is comprised of high efficiency LED light fittings. Automatic lighting controls are incorporated to switch off lighting in areas that are not in use. In many of the teaching/office spaces, the light fittings can be dimmed to allow for prevailing daylight conditions.
Ventilation & cooling: Mixed mode ventilation employing both mechanical and natural systems. The mechanical ventilation design strategy includes a low-carbon displacement ventilation system in open plan spaces such as auditoria and classrooms as an alternative to conventional air conditioning. This delivers air at low velocity at 19-21 C directly to the occupied zone and air warmed by occupation of the space rises through buoyancy to the return air points at high level. But before entering the building, incoming air is first drawn through an earth pipe system, which consists of large tubes placed in the earth approx 1.5 metres deep. At this depth the ground temperature will range between 7-13 C throughout the year. This system can cool the air by up to 14 K in the summer and heat it by 9 K in the winter. The atrium also employs an automatic stack effect natural ventilation system using opening rooflights. At a design rate of approximately 30 m3/h per person the ventilation will ensure good indoor air quality (approximately 1,000 ppm/CO2).
Building management system: The building energy management system (BEMS) is set up to control airflow throughout the occupied spaces via monitoring of the CO2 levels within these areas, thus ensuring optimum power usage of the air handling, heat recovery and variable refrigerant volume (gym only) units to ventilate these spaces efficiently. There are a large number of sub-meters throughout the building. These are linked to the site wide BEMS system, which allows the energy usage of each of the sub systems that are metered to be monitored.
Electricity: 2,667 m2 of solar PV, generating 380,782 kWh/yr. Approx peak generation of 520 kWp (kilowatts at peak generation). A Tesvolt battery storage system has also been designed to capture some of the peak PV generated electricity during the day and prolong its use into the evening times when the college is still running. The Tesvolt battery storage system has an instantaneous rating of 180 kWp and battery storage capacity of 460 kWh. The building also benefits from the inclusion of the CHP unit which provides 65 kilowatts electrical generation during operation. These two complementary systems are expected to generate 800,000 kWh of renewable electricity per annum between them, with the biofuel CHP also generating circa 560,000 kWh of high-grade heat for space heating and hot water generation.
Green materials: Products have generally been selected that are A-rated in the BRE Green Guide. AAA rated white goods specified.
Image gallery
https://passivehouseplus.ie/magazine/feature/learning-curves#sigProId0e8a1ff8c6