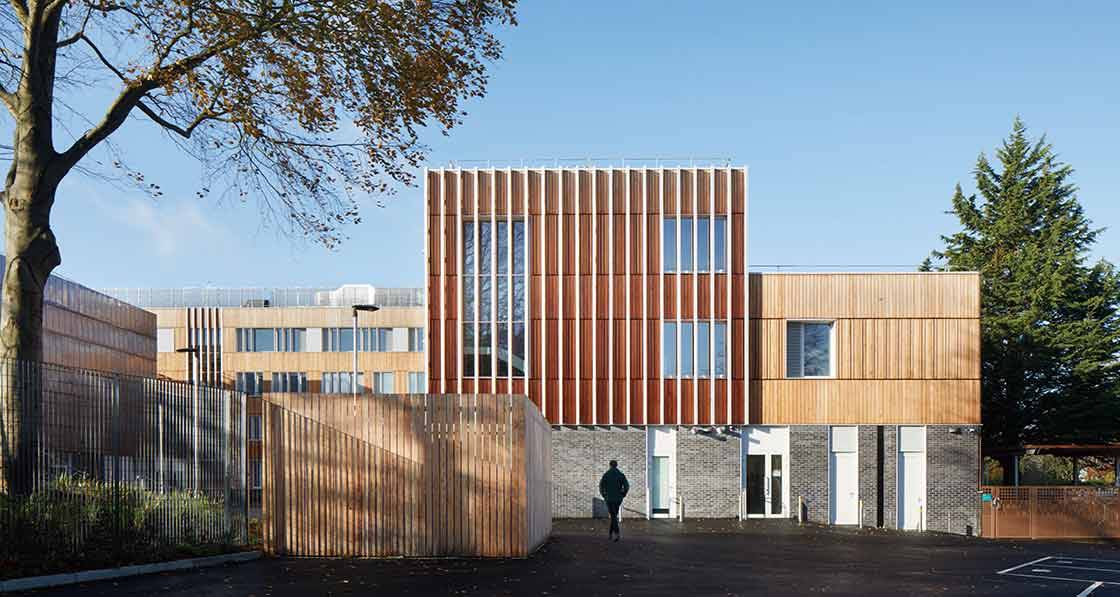
- Feature
- Posted
Inside the UK’s largest passive school
With a decade of experience designing primary schools to the passive house standard under their belt, Architype have now designed the UK’s first passive secondary school — and all of the evidence suggests there is no better way to ensure a healthy, comfortable environment that is supremely conducive to learning.
Click here for project specs and suppliers
Building: 8,952 m2 secondary school
Build method: Cross-laminated timber with concrete ground floor
Site & location: Sutton, South London
Standard: Passive house certification pending
Several of the most forward-thinking local authorities in the UK have been adventurous enough to build passive standard primary schools in recent years. But no authority boasted a passive secondary school until Sutton Council opened the £40 million Harris Academy Sutton, in South London, last summer.
Not only is it the UK’s largest passive school, but it appears to be the largest school project anywhere in Europe to achieve the standard. The four-storey building covers more than 10,000 m2 and will house 1,275 pupils and 95 staff . It won Building Magazine’s ‘Building Performance Award’ for 2020.
The hope is that the project’s success will break down barriers and that it will serve as a template for more passive secondary schools. There has already been intense interest from local authorities all over the UK, and architects Architype are now working on several new secondary schools to the passive house standard.
“Risk has been an inhibiting factor for local councils. Until Sutton Council took the leap, they all hesitated to be the first to build a secondary school passive house,” said Architype project architect Christian Dimbleby.
“But we’ve proved it’s possible to design large high performing buildings with low carbon and great aesthetics. There can be a little bit of extra cost — between 4 per cent and 8 per cent — but it comes back in the long-term running costs and improvements.”
This article was originally published in issue 36 of Passive House Plus magazine. Want immediate access to all back issues and exclusive extra content? Click here to subscribe for as little as €10, or click here to receive the next issue free of charge
Sutton Council’s pioneering approach emerged out of its long commitment to high environmental standards for public buildings. The council created the much-praised BedZED ‘eco-village’ housing project and it drew up ambitious sustainability targets as the first ‘One Planet Living’ council in 2009. Those plans were recently updated with even tougher targets.
Sutton Council has put in place stringent requirements, too, for public buildings of more than 1,000 m2. Most London authorities settle for BREEAM Very Good, but Sutton Council has mandated BREEAM Excellent. In recent years, however, the council has become somewhat disillusioned with BREEAM.
“It doesn’t dictate the design approach and we were not always satisfied projects were performing as well as they should in practice,” said Adam Whiteley, senior project manager for Sutton Council. “We felt it would be easier to monitor a passive house building’s performance and we expected a higher standard.”
Flexibility is there for future styles of teaching to change and develop.
There was another important motivation behind the decision to go down the passive route. Harris Academy Sutton was the first building to be constructed on the £350 million London Cancer Hub development, which will have 280,000 m2 of medical buildings and research centres.
The Cancer Hub will house more than 275 scientists who are developing new drugs and treatments. Sutton Council is the landowner of the site and has a regeneration partnership with the Institute of Cancer Research.
The Harris Academy Sutton places a strong emphasis on the sciences and there are many opportunities to collaborate with cancer researchers.
“Because our school is a gateway project for the London Cancer Hub, we wanted the architecture to make a real statement. It had to represent much more than the average building by virtue of its high energy performance, building physics and aesthetic appearance,” said Adam Whiteley.
Sutton Council’s partnership with Architype is built on their shared commitment to sustainability. Architype have designed passive certified schools in Wolverhampton and Wales, and Sutton Council had already appointed them in 2014 to design the smaller Hackbridge Primary to the passive house plus standard. In January 2016, Sutton asked Architype to carry out a feasibility study for a large secondary school. At the end of the year, Architype submitted a planning application.
But there were concerns about the impact of an imposing four-storey building on adjacent low-rise homes and the Architype team was asked to redesign some elements. “We had to accept the east-west classroom arrangements needed some adjustments as they created overshadowing of school courtyards and residential housing,” said Dimbleby.
“We designed three iterations to deal with their concerns and finally got planning permission following consultations, revisions and public meetings, on 31 August 2017. The completed building steps down in scale to two storeys on the north side as it gets closer to the houses. It’s much less imposing now. And we’ve designed terraces with green planting that step the roof back and camouflages the main building.”
Four months later, in December 2017, work began on site to bring Architype’s designs to life. A few months later, however, more modifications had to be made to the design after the government selected Harris Academy to run the school. The academy requested clearer views into the classrooms. “They wanted the head teacher to be able to walk around and see into the classrooms from the corridors. The idea was to encourage ‘mature’ attitudes to learning,” Dimbleby said.
Harris Academy also expressed a desire for Architype to create flexible classroom spaces with removable internal walls. “If the worst came to the worst and we had constant Covid-19 for years, we could take away some walls to double the size of spaces and allow more social distancing. That flexibility is there for future styles of teaching to change and develop,” Dimbleby said.
The school, he says, is designed rather like a modern campus. Pupils are given freedom to move around and the cross laminated timber walls are very exposed. “It looks like we’re inviting pupils to graffiti them, but the head wants the students to learn to respect the loveliness of the environment rather than worrying about the consequences. It’s about assuming the best in people,” Dimbleby said.
An overarching goal of the design, he says, was to maximize the amount of light reaching the courtyards and buildings. To increase solar gain without a risk of overheating, Architype placed most classroom spaces in the north-south orientation. For east-west classrooms, they used vertical aluminium to provide as much shading as possible.
Douglas fir fins with aluminium cladding project past the buildings, and the 350 mm deep windows are set back. Meanwhile, Lamilux roof lights allow daylight to flood into the corridors and gymnasium.
The school has a concrete ground floor, but Architype used 50 per cent GGBS, a low embodied carbon cement substitute, made from a steel industry by-product.
-
Laying the XPS insulation under the ground floor Laying the XPS insulation under the ground floor
-
Cross-laminated timber walls on the upper floors Cross-laminated timber walls on the upper floors
-
Installing the exposed timber roof beams for the sports hall Installing the exposed timber roof beams for the sports hall
-
Low thermal conductivity Ancon TeploTies visible here protruding through foam insulation before installation of brick cladding Low thermal conductivity Ancon TeploTies visible here protruding through foam insulation before installation of brick cladding
-
JJI joists installed to upper floor wall over pro clima Solitex Fronta Quattro vapour control membrane, before being finished with a rendered board JJI joists installed to upper floor wall over pro clima Solitex Fronta Quattro vapour control membrane, before being finished with a rendered board
-
JJI joists installed to upper floor wall over pro clima Solitex Fronta Quattro vapour control membrane, before being finished with a rendered board JJI joists installed to upper floor wall over pro clima Solitex Fronta Quattro vapour control membrane, before being finished with a rendered board
https://passivehouseplus.ie/magazine/feature/inside-the-uk-s-largest-passive-school-harris-academy-sutton-delivers-top-class-comfort-superb-air-quality-for-pupils#sigProId71c129a611
A concrete ground floor was needed because the level of the site changes from one end of the building to the other by a height of one storey. The concrete ground floor serves partly as a retaining wall, and together with the first-floor slab it provides a platform on which to construct the cross laminated timber (CLT) structure above.
“We tried to eliminate concrete as far as possible, but we needed it there and round the staircases for fire purposes, especially since we were designing in the aftermath of the Grenfell Tower fire,” Dimbleby said.
The CLT made the building much lighter though, enabling Architype to reduce the depth of the foundations. “We were able to get rid of pile foundations and just use mass footings on a concrete raft with occasional foundation strips. Reducing the load by using CLT also helped with airtightness and thermal insulation detailing on the ground as we didn’t need to go through the pile foundations,” he said.
Architype’s own analysis revealed that the switch from concrete to timber for the upper floors reduced the embodied carbon from 863 kgCO2e/m2 to 698 kgCO2e/m2, which is a 20 per cent decrease. Dimbleby said this was “very significant” and the final figure is close to the RIBA 2025 target of less than 650 kgCO2e/m2.
The contractor Wilmott Dixon had previously delivered one of the UK’s largest passive house projects, the George Davies Centre at the University of Leicester. But none of the workers from its supply chains had prior experience of passive house construction. Wilmott Dixon sent all the sub-contractors on a two-day passive house introductory course while its own site managers did certified passive house tradesperson training.
Even the Wilmott Dixon project lead Graham Thompson knew little about the passive house standard when he joined the project four months into the build. Nevertheless, Thompson has a passion for green building, and had spent a lot of time studying low carbon and energy standards. It turned out Wilmott Dixon made a shrewd choice. Despite his previous inexperience with passive buildings, Thompson’s work on the Harris Academy Sutton earned him a nomination for the Chartered Institute of Building’s 2019 construction manager of the year for schools. He was praised for his “pragmatic, disciplined and strategic” approach.
“My first impression was that passive house can’t be that difficult. I thought it must be just another building standard like BREEAM. Within 48 hours, I realised it was like nothing else I’d done before,” said Thompson.
“It’s not rocket science. But it’s different to BREEAM, which I see as a box-ticking exercise. It’s more about designing the core of the building as green and high performing. Having done one passive [building], I’m passionate about them. I think it’s the best method available for anyone serious about the climate. If we made it mandatory for every public building it would have a huge impact, but our industry is slow to react.”
Thompson’s perfectionist approach to construction was evident in his decisionmaking. For example, he wanted the timber cladding to be manufactured on site because checks could be done on the spot and it was easier to guarantee precise measurements.
There’s been a lot of poor quality school construction over the past two decades.
Then, he instructed his team to build a full-size mock-up of a section of the building, including two large classrooms. This allowed rigorous testing to be carried out to reduce the risk of errors and formulate quality standards.
The mock-up contained all the important elements, including windows, cladding junctions, waterproof seals and walls. It was airtightness tested, and produced a result of 0.3 air changes per hour, which ended up being the same value as the final building too (the airtight layer was toward the outside of the construction, for example being provided by the breather membrane for the CLT walls).
Sutton Council used a design-and-build contract, which can be notoriously tricky for quality control if there’s an absence of dialogue between parties. But Thompson instigated a “no blame” culture of open communication. Whenever anyone encountered a problem, they were encouraged to walk into the large site cabin office and ask for a meeting with all key decision-makers.
“With D&B contracts you sometimes never see the client again, but Sutton Council were present at all the meetings. And Wilmott Dixon wanted the architects involved every step of the way. So, although we switched from a partnering agreement with Sutton to a D&B contract, everyone was still working as if it was a partnering agreement,” said Dimbleby.
The final building has been open since September 2019 and Adam Whiteley and his team have been closely watching its performance. “We’ve tweaked a few things with the on-site teams, but we’re delighted with the performance. As well as the energy and carbon being saved, we’ve had a lot of feedback about how comfortable the school is,” he said.
“That was important to us because there’s been a lot of poor-quality school construction over the past two decades. Many school buildings are so poorly designed that they’re either overheating, or too cold. It has a negative impact on children’s education, whereas we think the comfort of passive house will benefit them.”
Chryssa Thoua, an architect and researcher at Architype, is studying for a PhD on how schools perform, including the influence of the environment on learning outcomes.
Dimbleby said that her analysis of data from four primary schools shows that passive house is the only construction method that achieves the CO2 concentration levels required by BB-101 (Building Bulletin-101), which provides guidance on air quality for schools.
“There’s an established link between CO2 and fatigue. The BB-101 requirement is 1,500 parts per million and, in winter, passive houses hover around 700 to 1,200, whereas naturally ventilated normal buildings range up to 5,000 parts per million. At that level, you get issues with concentration and it can be a health hazard,” Dimbleby said.
Throughout the year, mechanical ventilation with heat recovery provides fresh air, and there are CO2 sensors in all rooms at Harris Academy Sutton. In the winter, the system delivers fresh warm air. This combination of CO2 sensors to measure air quality, and warm fresh air, is also likely to be a good way to mitigate spread of Covid-19 (see our schools and ventilation feature for more).
Classrooms never get stuffy and there are no uncomfortable draughts or cold spots. “Unfortunately, public buildings are rarely assessed in terms of energy performance, let alone suitability for learning. But we’re providing bigger and bigger catalogues of evidence showing the benefits of the passive house standard for school buildings,” Dimbleby said.
Selected project details
Client: London Borough of Sutton
Architect: Architype
Main contractor: Willmott Dixon
Structural engineer: Price & Myers & KLH with Rambol
M&E consultant: BDP
MEP sub-contractors: Jones King & CMB Engineering
Electrical contractor: Jones King & DES Group
Airtightness testing & consultancy: Etude
& WARM Low Energy Building Practice
Passive house certifier: WARM Low Energy Building Practice
Landscape architect: Churchman Thornhill Finch
Quantity surveyor: Synergy Construction and Property Consultants
CAD software: Revit
Educational consultants: Lloyd Wilson Partnership
Planning consultant: Lichfields
Wall insulation: Warmcel, via CIUR
Additional wall insulation: Kingspan
Roof insulation: Soprema
Floor insulation: Kingspan
Airtightness products: Ecological Building Systems
Thermal breaks (under slab): Foamglas
Thermal breaks (external walls): Puren
Glazing & shading: Lang Fenster
Cladding: NH Ethridge
Screeds: Flowcrete
Fit-out: DMC Ash
Roofing: Soprema UK
Cross-laminated timber: KLH
CLT structural engineer: Rambol
Main space heating: Ideal, via CMB Engineering
Ventilation: Swegon, Lennox & Airflow Developments
MVHR units, via CMB Engineering
Solar PV: Spirit Solar
In detail
Building type: 8,952 m2 (treated floor area) four-storey secondary school (10,625 m2 gross internal floor area)
Location: Chiltern Road, Sutton
Completion date: August 2019
Budget: £40million / £2,764m2
Passive house certification: Pending
Space heating demand (PHPP): 12.65 kWh/m2/yr
Heat load (PHPP): 8.91 W/m2
Primary energy demand (PHPP): 133 kWh/m2/yr
Heat loss form factor (PHPP): 1.8
Overheating (PHPP): 0 per cent
Number of occupants: 1,275 students plus school staff
Environmental assessment method: BREEAM – compliance with all mandatory credits required to achieve an ‘Excellent’ rating
Airtightness (at 50 Pascals): 0.30 ACH @ 50 Pa
Energy performance certificate (EPC): A 22
Thermal bridging: Bespoke details developed to avoid thermal bridges across the external envelope based upon Architype’s experience of delivering passive schools. Where not possible to omit, thermal bridge calculations were done using Psi-Therm & Psi-Therm 3D, e.g. chi-value calculation was done for metal fi xings required for large vertical fins. Thermal bridge & temperature checks done for window details & critical ground details.
Measured energy consumption: According to its gas meter, over 12 months between November 2019 and October 2020 inclusive, the school used 18,477 m3 of gas. This converts to 204,444 kWh of gas, using conversion calculation provided by Gazprom, or 23 kWh/ m2 of delivered heat energy. While this was mostly for space heating, some domestic hot water is provided by gas heaters too and use of this may have been above average during 2020 due to increased handwashing. The building may also need extra gas heating in its first few years as it is only partially occupied, and thus has less internal heat gains from occupants. During the same time period the school used 84,480 kWh of imported grid electricity.
Energy bills (estimated): Using the school’s Gazprom tariff of 1.172p per kWh and the gas consumption figures above, we estimate an annual gas consumption bill of £2,396, exclusive of VAT & standing charges, or about £200 per month. Note this includes some domestic hot water as well as space heating. Also standing charges can potentially be large – in the one sample bill we viewed from Harris Academy Sutton (June 2020), the standing charge for the month was £328, while the monthly gas usage charge was £117.
Foundations: Ground bearing pads and strip footings, thermally separated from the slabs using high compressive strength insulation (100 mm Foamglas).
Ground floor: Concrete blinding followed above by 2 x 50 mm XPS insulation (Kingspan Styrozone® N300), 200 mm reinforced concrete slab with edge thickening, liquid applied DPM, carpet/vinyl/lino/timber fi nish above. U-value: 0.34 W/m2K (typical).
Typical ground floor wall: Brick cladding with Ancon TeploTie wall ties or copper sheet on 22 mm plywood backing fixed on Nvelope helping hand bracket on thermal break; followed inside by 50-80 mm ventilated cavity, 100 mm Kingspan phenolic foam board made up of two layers of 50 mm with staggered joints, pro clima DA vapour check and airtightness membrane, concrete columns with timber frame infill (MGO board on 250 mm timber studs with internal 18 mm Medite SmartPly OSB3), 38 mm service cavity insulated with Rockwool RWA45, gypsum board wall lining. U-value: 0.19 W/m2K
Typical upper floor wall: 21 mm thick vertical Douglas Fir timber rainscreen cladding, treated with PTG Sentrin FRX, followed inside by insect guard mesh, softwood 50x50 mm battens, pro clima Solitex Fronta Quattro vapour control membrane, 195 mm framed JJI-joist structure filled with blown insulation (Warmcel), pro clima DA vapour and airtight membrane, VersalinerTM magnesium oxide sheathing board, CLT columns with timber frame infill (timber studs with internal 18 mm Medite SmartPly OSB3), 38 mm service cavity insulated with Rockwool RWA45, gypsum board wall lining. U-value: 0.17 W/m2K
Roof: Soprema reinforced bitumen membrane warm roof covering system (front wings have green roof) with tapered (PIR) & 180 mm uniform (EPS) insulation roof boards underneath, followed below by vapour control layer on 300 mm cross laminated timber exposed structural deck. U-value: 0.11 W/m2K (average tapered & uniform insulation).
Windows & external doors: Lang-Fenster composite (timber and aluminium) triple glazed argon-filled glazing, windows & external doors. Average overall window U-value of 0.96 W/ m2K (installed). Wicona aluminium glazed doors used for Primary Entrances.
Roof windows: 10 x Lamilux CI System glass architecture with PR60 energysave roof lights.
Glazing: toughened outer and laminated safety glass inner with low emissivity coatings, gas filled cavities and spacers. Anti-glare obscured glass specifi ed for sports hall. U-value: 1.10 W/m2K
Space heating system: 2 x Ideal EvoMax 150 kW condensing gas boilers (one back-up). Radiators in teaching and office areas. Thermostatic valves with remote wall mounted room temperature sensors.
Domestic hot water: 26 x localised electric water heaters (various). 2 x domestic hot water calorifiers (Ormandy Rycroft Evoplate CP-B25 + 257 L Buff er Vessel). 2 x gas fired DHW heaters (Andrews Water Heaters - Ecoflo EC230/600).
Ventilation: 5 x Swegon Gold RX mechanical ventilation with heat recovery systems in various models, ranging in heat recovery effi ciency from 75 per cent to 82 per cent. 1 x Airflow Duplexvent Multi Eco-N DV4500 MVHR. 1 x Lennox LX0412.
Kitchen: Dedicated extract system consists of an extract & supply hood connected to volume control dampers.
Water: All wash hand basins, classroom sinks, and showers have flow regulators to limit water use. Water wastage from sinks/shower and hand basins is limited by flow control regulator valves on the inlet. BMS system is programmed to monitor the flows on the incoming revenue meter.
Electricity: 17 kWp roof-mounted PV array, generating an estimated 10 per cent of the school’s energy needs.
Green materials: KLH PEFC-certified cross laminated timber, Douglas Fir cladding all from FSC certified sources, concrete with 60 per cent GGBS content, long-life copper cladding with recycled content, cellulose insulation from recycled newspaper, green roof system, magnesium oxide boards, Tarkett DESSO loose lay carpet tiles, OSMO Polyx Oil.
Image gallery
-
Landscape labels Landscape labels
-
Sectioned spine labels Sectioned spine labels
-
Typical parapet detail Typical parapet detail
-
South elevation South elevation
-
All plans All plans
-
Ground floor Ground floor
-
Roof plan Roof plan
-
Window - brickwork Window - brickwork
-
Brick corner plan details Brick corner plan details
-
Typical Parapet - Main roof east Typical Parapet - Main roof east