- Retrofit
- Posted
Carlow A1 upgrade
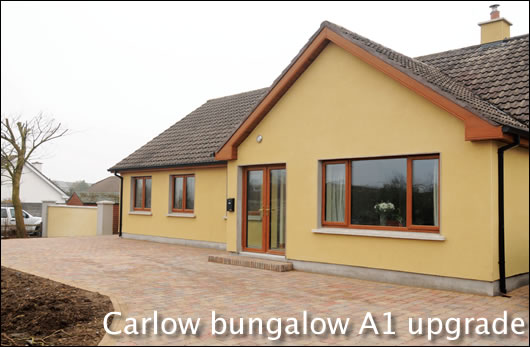
Is it possible to ditch fossil fuels and run a 1970s Irish bungalow on solar energy? Norman McMillan’s renovated A1-rated bungalow in Carlow proves it is.
Norman McMillan can make an impressive boast: not only does he have one of the few A1 rated renovations in the country, he appears to be the first person to achieve the rating without solar photovoltaic (PV) panels. He did ultimately install PV, but it wasn’t included in the BER calculation.
McMillan — Mac for short — wasn’t necessarily aiming for an A1 rating, just for the best job possible. “We just decided we’d do a proper job. We specified the best building we could,” he says.
Mac and his wife Trixie bought the house new in 1970. But it deteriorated over the years, and dampness and mould were affecting some rooms. Mac had insulated the attic and fitted double-glazing inside the existing single panes.
“[My mother] used to say ‘when I’m gone, you should do your house up,’” he says. So he did: work on the refurb began last March and finished in November. Local builder Kevin Doyle of Doyson Construction oversaw the revamp.
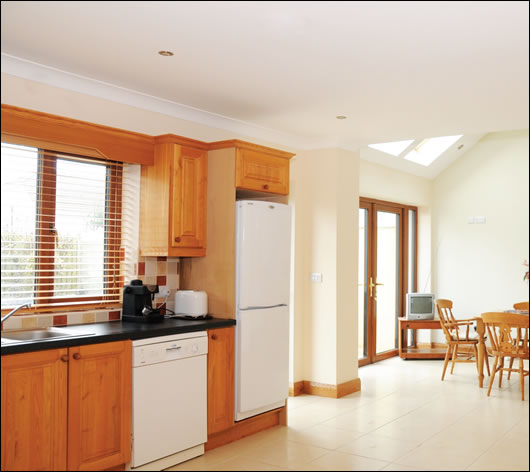
The kitchen was internally insulated and features an electric Velux roof window powered by a small solar PV panel
Solar heat & power
The house’s solar energy systems are its pride and joy. Twenty square metres of rooftop solar thermal collectors heat a 1,000 litre buffer tank that supplies space heating, backed up by a Dimplex Lab 11 air-to-water heat pump. A 12m2 array of solar PV panels powers the heat pump.
“We won’t need to get oil or anything, and we can back up the electricity with PV and be self sufficient,” Mac says. “It makes life easier doesn’t it?”
The house’s underfloor heating needs to run at about 30C to keep the house warm when space heating is needed. So when the solar collectors alone can’t provide this and the temperature in the middle of the buffer tank drops below 35C, the heat pump — powered by the PV — switches on.
The PV array has an average annual output of 2kW — about what’s needed to power the whole house, including the heat pump, in the coldest weather. For comparison, Mac points out that a single bar of an old electric fire has an output of about 1kW. He monitored the house’s energy use before putting in the PV system to make sure it was properly sized. “Given a bit of testing you can be sure that you are going to cover the energy demand for the year,” he says.
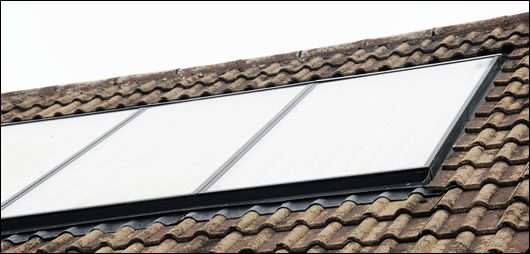
The 20 square metre array of Solar Focus collectors is designed to provide most of the house’s heating needs
The roof’s 37 degree angle means the solar thermal collectors work best in winter — when most space heating is needed — capturing energy from the low winter sun. Considering how poorly Mac says the house was built, he reckons it’s a coincidence the roof’s angle is just right. “He’s a really crap builder, the guy who built it,” he laughs. “He had no idea and the roof’s just perfect.”
Mac — an optical engineer — estimated the output of the solar thermal collectors based on local climatic data before the system was installed, and he’s been monitoring it closely since. “They’re pumping better in the winter than they are in the summer, because of the angle. We were getting massive charging in January and February…so the panels are working a treat,” he says. “They seem to be doing what I predicted.”
Wicklow-based Renewable Energy Systems (RES) installed both solar systems. The thermal collectors are Solar Focus ‘hybrid’ panels — a mix of evacuated tube and flat plate panels. “The semi-evacuated construction with inbuilt parabolic reflector improves performance,” says RES’s Joe Corrigan. “It’s a completely sealed panel therefore eliminating condensation issues. The result is a higher prolonged output over the day to day than a standard collector.” RES have also installed meters that allow Mac to monitor their exact performance.
The house will need little space heating from May to October, and according to his calculations Mac expects the solar thermal collectors to meet 60% of his space and water heating demand in November, 20% in December, 30% in January and 40% in February.
The house is divided into seven different heating zones — essentially one for each room — with a Heatmiser thermostat in each. “Every zone is an individual room, so each zone can be set at its own temperature,” says Thomas Vaughan of Geothermal Solar, who supplied the heat pump, underfloor heating system and the buffer tank.
“The underfloor heating was designed to operate at lower temperatures than normal so we can maximise the efficiency of the solar panels,” Vaughan says. Pipes were laid closer together — and in shorter runs — to maximise the heat given off in any one area.
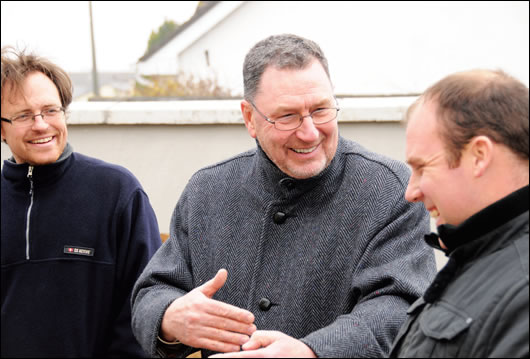
Homeowner Norman McMillan, centre, chatting with his son Doug, left, and builder Kevin Doyle of Doyson Construction
Insulated, airtight building envelope
But the house is only suited to a low temperature, solar heating system because it needs so little heat, having been heavily insulated as part of the renovation. Doyson Construction installed 60mm of high performance rigid Xtratherm insulation. The wall cavities had previously been pump-filled with Rockwool.
Small cavity wall extensions were added to each end of the house — one for the kitchen, the other for a utility room. The wall cavities feature 60mm of partial fill rigid Xtratherm insulation, with a further 60mm of Xtratherm internally.
Insulating internally can be risky – doing so to onerous U-values creates a sudden drop in temperature between the insulation and the cold surface of the original wall behind it. This ‘dew point’ is an ideal place for condensation — and potentially mould growth — to occur. But because the cavities at Mac's house are insulated too, he’s confident the inner leaf of the walls should remain sufficiently warm.
The team paid detailed attention to thermal bridging. Martin O'Neill, director of the BSc course in quantity surveying at IT Carlow, oversaw much of the detailing. “It was evident there were going to be problems with thermal bridging," he says.
O’Neill mentions some of the most prominent thermal bridges, including cavity closers, window sills and a large concrete lintel running across the front of the house. “All the sills had to be removed,” O'Neill says. “There were new sills put in and we put insulation in behind them.”
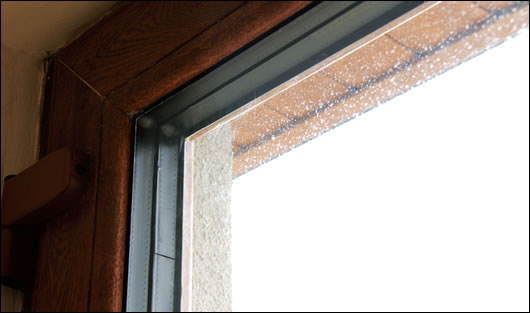
The house’s windows are triple-glazed, argon-filled and feature low-e glass and warm-edged spacer bars; they were supplied by Munster Joinery
To eliminate cold bridging through the concrete lintel, Doyson externally insulated the front of the house with 30mm of rigid Kingspan phenolic insulation. Mac considered external insulation for the whole house, but that would have meant extending the roof, which he didn’t think was a good idea. The floors had to be taken up anyway, so he reasoned that choosing external wouldn’t have saved much disruption inside either.
Doyson Construction also insulated under the ceiling with 60mm of Xtratherm, installing a Pro Clima Intello ‘intelligent’ vapour membrane here too. There were already six inches of fibreglass in the attic. Doyson took up all the original floors, putting 280mm of Xtratherm beneath the underfloor heating pipes. “It is important with underfloor to really overdo the underpipe insulation,” Mac says, “if you put in energy it can either go up or go down.”
Munster Joinery supplied the house’s windows. The triple-glazed PVC-coated Future Proof units are insulated with argon gas. They also feature low emissivity coatings to reflect heating back into the house, and warm-edged spacer bars to prevent cold bridging between the sheets of glass. The core of the frame is pumped with an insulating foam. Munster Joinery told Construct Ireland that the Future Proof range is currently waiting certification from the Passive House Institute, and that quadruple-glazed and krypton-filled versions are also available.
The kitchen features an electric, remote-operated operated Velux roof window that’s powered by a small solar PV panel. The Velux window itself has an overall U-value of 1.0 W/m2K, and is filled with krypton gas.
Doyson paid particular attention to airtightness, sealing with Pro Clima tapes and membranes from Ecological Building Systems throughout the build. The airtightness test performed by Gavin O Se of Greenbuild produced a result of 2.35 air changes per hour — a great result for a 1970s bungalow. Nonetheless, contractor Kevin Doyle was a bit disappointed. “We’re happy enough but we thought for the effort we put in we might have done slightly better,” he says.
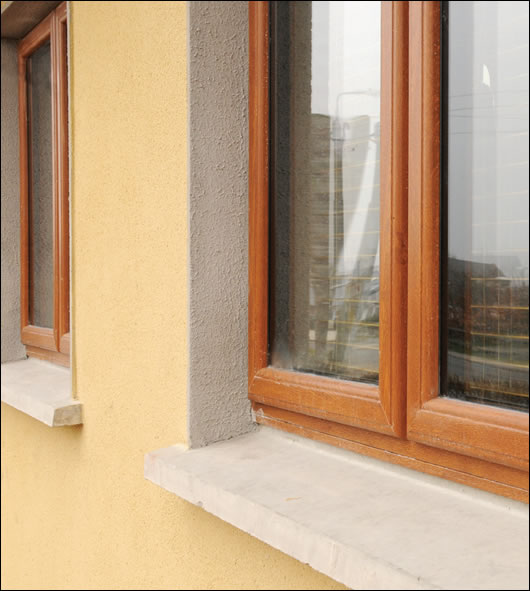
The house’s original concrete sills were removed and new ones installed, with insulation behind them to prevent cold bridging
An Xpelair Xcell 150 heat recovery ventilation unit — supplied by Geothermal Solar — extracts warm, moist air from ‘wet’ rooms such as kitchens and bathrooms and uses it to pre-heat incoming fresh air that’s supplied to sitting rooms and bedrooms. It has a heat exchange efficiency of up to 90% according to the independent Sap Appendix Q database.
Rainwater for washing, cleaning and drinking
Rain will provide practically all the house’s water — even for drinking. Rainwater harvesting systems often just provide water for toilets and gardening — or if they have UV filters installed, for washing too. But Mac’s comfortable enough to drink it. His system features an inline filter to catch dirt and debris and UV treatment to kill bacteria. “And as a double safeguard we have supplied another bacterial filter at the kitchen sink, an ultra filter,” says Stuart Smith of Watershop, who supplied the filters. This final filter catches anything over 0.2 microns in size.
Smith says the only added risk with drinking treated rainwater is that it’s often stored for longer periods, meaning there’s more time for bacteria to develop. But systems are available that keep the harvested rainwater circulating, so it’s constantly passing through the filters. Sturdy Products supplied the 10,000 litre rainwater tank that’s buried under Mac’s garden — if it ever dries up, mains water kicks in.
Mac and his wife Trixie have been back in the house since November. Trixie says the house was quite damp before. “There’s so much of a better feel to the place now,” she says.
But she admits it took her a little while to get used to the contemporary feel of the renovated house. “I’m definitely bonded with it now,” she says. “It took a while. It’s all very modern. But I love it now.”
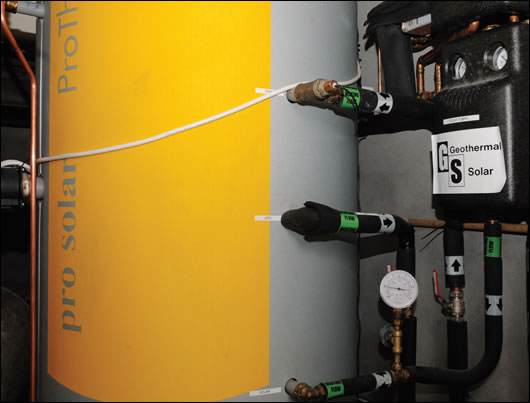
The 1,000 litre buffer tank is heated primarily by the Solar Focus collectors, but when the temperature in the middle of the tank drops below 35C the heat pump kicks on
Selected project details
Contractor: Doyson Construction
Client: Norman & Trixie McMillan
Solar thermal & PV: Renewable Energy Systems
Air-to-water heat pump, heat recovery ventilation & underfloor heating: Geothermal Solar
Rainwater harvesting system: Sturdy Products
Rainwater filters: The Watershop
Airtightness testing: Greenbuild
Insulation: Xtratherm , Kingspan , Rockwool
Project overview:
Location: Carlow Town
Building: 130m2 1970s cavity-wall bungalow
BER: A1 (7.18 kWh/m2/yr)
Carbon dioxide emissions rating: 1.71 KgCO2/m2/yr
Airtightness: 2.35 air changes per hour
Walls: Concrete cavity wall, fully-filled with Rockwool insulation in the original dwelling and 60mm Xtratherm rigid partial fill in the new gable extensions. Internally insulated throughout with 60mm Xtratherm insulation. U-Values: 0.18 W/m2K. Front facade also externally insulated with 30mm rigid Kingspan phenolic insulation.
Roof: Six inches of fibreglass in the attic. From the ceiling down: Pro Clima Intello membrane, 60mm rigid Xtratherm insulation, timber battening, plasterboard.
Ground floor: Insulated with 280mm of Xtratherm rigid insulation. U-value: 0.15 W/m2K
Windows: Triple-glazed, argon-filled Munster Joinery Future Proof windows, with an insulated core, warm edge spacers and low e glass. U-value: 0.8 W/m2K.
Heating: 20m2 solar thermal array, optimised for winter. Dimplex Lab 11 air-to-water heat pump, with COP of 316% according to SEAI’s Harp database
Electricity: 12m2 solar photovoltaic array, average annual output of 2kW
Ventilation: An Xpelair Xcell 150 heat recovery ventilation system with heat exchange efficiency of up to 90% (Sap Appendix Q)
Related items
-
Derelict to dream home
-
Traditional homes retrofit grant pilot launched
-
Dr. Barry Mc Carron appointed MD of KORE Retrofit
-
Bungalow Bills
-
New scheme offers up to €75,000 retrofit loans at low cost
-
Phit the bill
-
Mainstreaming retrofit – a massive missed opportunity
-
It's a lovely house to live in now
-
Is it okay to retrofit heat pumps before building fabric?
-
New Licence Plus scheme undermines retrofit standards, experts say
-
Government supported almost 27,200 home energy upgrades through SEAI in 2022
-
Breath of life