Capital L
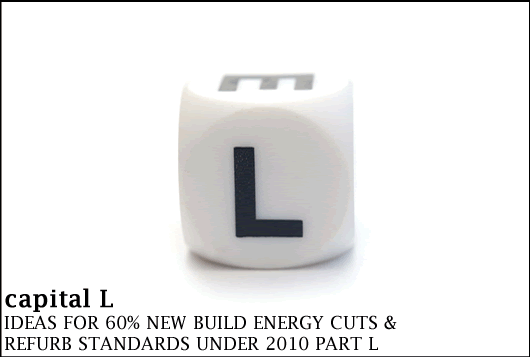
With the goal of achieving zero carbon standards for new homes by as soon as 2013, environment minister John Gormley has committed to introducing 60 per cent energy and carbon reductions under changes to part L of the building regulations next year. John Hearne spoke to leading industry figures to find out how the revised regulation could raise standards for both new and existing homes
Policy makers sit down to draft the latest draft of part L against a very different backdrop to that of the last conclave in 2007. House completions have dropped through the floor and the broader construction industry is on its knees. Yet statements from the government indicate a continued focus on transformational change in building standards.
“We’re in an extraordinary time,” says leading green architect Joseph Little. “To drive forward global action on climate change the EU has committed to a 20 per cent increase in efficiency, a 20 per cent increase in renewables and 20 per cent reduction in carbon emissions. If other non-EU countries join with us this target could even be increased to 30 per cent. The National Energy Efficiency Action Plan for 2007 to 2020 sets out how the Irish government plans to meet this 20-20-20 target across all sectors. Government officials have told me that it’s very flexible; as situations change they will change its emphasis and revise targets. Given how much oil and gas we import this is not just about climate change but about security and the economy too. The action plan is intended to tie policy together across all sectors of society to achieve these crucial over-arching targets.” Little goes on to say that currently 53 per cent of the energy reduction target needs to be met by the residential sector. It is in working back from this position, he believes, that should drive our approach to what changes we make in the 2010 regs.
Little believes that our approach to the 2010 regs should be informed by working backwards from these targets. Recently appointed chair of the building regulations advisory body (BRAB), Jay Stuart of sustainability consultants DW EcoCo agrees. “What we need is a roadmap to get us from here to 2013 part L, and the stated target of carbon neutral building…It’s all good and useful to have these incremental changes, but I think now we’ve run out of time for that sort of stuff. Given the targets that the EU has set, that the UK has set and that the government here has set, we need to jump to the end game and the end game is that all new buildings from now on should be built so that they don’t have heating systems if they’re residential, and that they generate as much renewable energy as possible and provide as much of the domestic hot water as can be provided.”
REFURBISHMENT
AIB expects housing completions to fall from 51,000 in 2008 to around 25,000 this year, a figure which is now beginning to look optimistic, and remains in stark contrast to the 93,400 completed in 2006. Given the glut of empty and unsold residential units in the country, it seems highly unlikely that any recovery, when it comes, will return us to anything like these activity levels. Against this backdrop, more exacting energy standards for new build houses will have a limited impact on national energy targets. Many in the industry now believe we need to switch emphasis to refurbishment. “The Home Energy Saving scheme and Warmer Homes scheme are the prime tools being used by the government to meet the residential targets in the National Energy Efficiency Action Plan,” says Little. “As housing completions have plummeted most of the 53 per cent reduction will have to be met by energy-focused refurbishment. It may be argued that refurbishing your home has become the key national response to climate change. That link has now been made clear: seemingly modest, localised actions like lagging your cylinder, improving heating controls and insulating attics, when carried out on a large scale, have a national impact and will help slow climate change.”

Jay Stuart of sustainability consultants DW EcoCo, Durkan Ecofix and recently appointed chair of the building regulations advisory body
Part L as it pertains to refurbishment and renovation has not changed significantly since 1997. Joseph Little points to a massive gulf that has emerged between energy standards for new build houses and those that apply to renovations. The maximum permissible U-value for a new build wall currently stands at 0.27 W/m2K, up from 0.45 W/m2K in the 1997 regs. By contrast, you can still refurbish an existing wall to a U-value of 0.6 W/m2/K – the same as twelve years ago. Moreover, confusion in the industry about how the current regulations work has hidden the true extent of the levels of energy efficiency required to comply. The technical guidance documents for 2008 part L takes the reference house specification details from the 2005 regs, with essentially the same U-values, a standard efficiency boiler and a weak air-tightness target. The designer then must take those details along with the form, lay out and orientation of the proposed dwelling and input it into the DEAP software. This leads to a BER figure, typically somewhere around 150 kWh/m2/a. Crucially, they must then multiply that BER figure by 0.6 to get the 40 per cent lower figure of circa 90kWh/m2/a that they’ll have to hit to comply. Most smart designers have realised that some of the most cost-effective and sensible ways to claw towards that target include improving the building envelope, which means better air-tightness, better U-values, and therefore a greater disparity between standards for new build and renovation standards than the prescribed U-values would initially suggest.
Insulation in older buildings can be a thorny subject, says Paraic Davis of MCO Projects. He says that while conservation architects often advise against the use of insulation in older buildings, he believes that ways can be found to improve the thermal performance of most buildings without compromising their integrity. Guidance is however lacking. “I think the new part L should categorise buildings by age and description…and also guide on whether or not a building needs breathable insulation. Buildings prior to the damp proof course era do. If we’re going to move forward with our existing buildings, I think the regulations should start giving that more detailed guidance rather than simply referring you, as they do at the moment, to documents written by very conservative conservation architects and which will essentially recommend no insulation.”
U-VALUES
Opinions vary over whether or not the new regs should become more prescriptive. Under the new approach introduced in 2008, compliance cannot be met simply by copying the reference house values. Using DEAP, the primary energy consumption figure of the proposed building is calculated, then divided by that of the reference house, to give the energy performance coefficient (EPC). To demonstrate that an acceptable primary energy consumption rate has been achieved, the calculated EPC of the dwelling being assessed should be no greater than the maximum permitted energy performance coefficient (MPEPC). The MPEPC is 0.6. This approach is expected to be retained this year. The 2005 reference house will remain as before, and only the MPEPC will change – falling to 0.4, thereby giving designers a free hand in deciding how to meet the targets.
“I think this sends out the wrong message,” says Tomás O’Leary of MosArt, Ireland’s first accredited passive house certifier. “It’s implicit that you have to do better than those U-values in order to achieve compliance with the building regulations…But I just think the focus should be on the building fabric first of all and thereafter on renewable energy technologies.” He points out that by allowing designers complete flexibility in specifying how energy reduction targets are met, there’s ample scope to meet those targets in sub-optimal ways. “You could leave U-values as they are and cover your whole roof with PV panels, but I would say that’s the wrong approach.”
Peter Keavney of Galway Energy Agency is concerned that the depressed housing market will lead policy makers to row back on planned improvements to building standards. “I feel that the next building regulations upgrade will only be tweaked a little bit,” he says. He points out too that with the market stagnant, substantially upgrading new build will create a huge gulf in energy performance between new houses and those built under earlier regimes. This, he fears, will make the existing housing stock even less attractive than it is at present. He believes therefore that the current flexibility in the regulations should be maintained. “I think the main thing we need to do with building regulations is to change the energy performance coefficient…If a house built in 2010 is 60 per cent better than one built under the 2005 building regulations, it will be harder to sell that [older] house.” Keavney argues that by leaving that flexibility in the regs, it will be possible to use renewable technologies to upgrade the existing housing stock, thereby bridging the gulf in the energy profiles of old and new houses. This view assumes, of course, that the house-buying public is considerably more motivated by energy concerns than it has been in the past. “The regulations should be drafted in sympathy with the market, and not put a huge burden on the sector,” he says, “but at the same time promote best practise in air-tightness, thermal bridging and of course the renewable energies.”
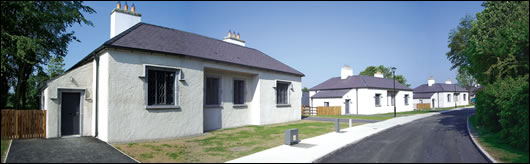
Architectural conservation guidelines can prevent the application of insulation to existing walls, as was the case when the 18th Century Belvedere Orphanage (above) was renovated. Engineer Paraic Davis achieved some thermal improvements by the use of a lime plaster on both sides of the existing rubble wall
AIR-TIGHTNESS
Both Keavney and Tomás O’Leary in MosArt believe we need to build on the introduction of air-tightness requirements in 2008 and lower the air permeability rate from 10m3/hr/m2 under pressure test conditions of 50Pa. “I don’t think the current rate of air-tightness is particularly challenging,” says O’Leary. “Ok, we’re heading for carbon neutral in 2013 gradually, but if they don’t bring about a reduction in U-values and an improvement in air-tightness this year, it’s going to leave an awful lot of work to do in the final run up to carbon neutral.” Peter Keavney would like to see the air permeability rate fall to 4m3/hr/m2. “That’s not that good either, but at least we have the tool there, let’s change it. It took a lot of hard work by a lot of good people to get it in there. Now that it’s there we can adjust it.”
BER assessor Brian Rochford of Colin Galavan & Associates does however have concerns around enshrining a higher level of air-tightness in regulations. The predominant means of addressing ventilation within an air-tight building envelope is mechanical ventilation with heat recovery. Rochford has several concerns around MVHR solutions if they are to be applied across the board. “I think MVHR is being installed by an industry that doesn’t fully understand what it’s doing. I don’t think the fire risks are understood, or if they’re understood, they’re being disregarded.” He points out that for MVHR systems to work safely, filters have to be changed regularly. He questions whether this happens in installations where the client is not a motivated self builder, although some MVHR suppliers on the market address this through a combination of after-sales service and client education. In multi-unit developments, bulky MVHR units are often installed in inaccessible, infrequently visited spaces like attics, making filter changing even more unlikely. According to a report in Building magazine published earlier this year, the UK government is to issue guidance regarding mechanical ventilation systems after a draft BRE study found widespread failure to maintain filters. “I think we’re saving up terrific health problems by air-tightening our houses and not having a competent industry,” says Rochford. Technology can answer some of these concerns. By placing system controls in utility areas, and by facilitating external access to filters by building maintenance personnel, it will be possible to address human behaviour issues. It should also be said that designed passive and demand based ventilation solutions do offer an alternative to filtered MVHR systems.
RENEWABLES
Under TGD L 2007, all new dwellings must provide a proportion of their heating or power from onsite renewable energy sources – a minimum of 10kWh/m2/a by utilizing solar thermal panels, heat pumps or either biomass boilers or stoves, or alternatively a minimum of 4kWh/m2/a from solar photovoltaic or wind turbines. It is expected that these figures will be raised in 2010 part L, but by how much we don’t yet know.
Problems emerge with this particular stipulation in some low energy settings. Last year, Galway-based energy efficiency specialists Energy Matters conducted a study into Lars Pettersson’s passive house in Moycullen. This is a large, 289m2 building, and because it requires little or no space heating, the only scope for renewable energy applications is in hot water generation, and indeed, the house does have 6m2 of solar thermal panels and a 300L tank. Yet to comply with TGD L 2007, the house would need 14m2 of panels and a 750L hot water tank. “The regulations as they currently exist,” says Ronan Rogers of Energy Matters, “may encourage passive house builders to install non-required renewable heating systems to passive houses to ensure their dwelling will meet the new requirement. For example, systems such as oversized DHW solar systems, solar space heating systems, or even dedicated space heating heat pumps or pellet boilers/stoves may be installed, which are essentially excess to the requirements of the dwelling.” If we continue the current flat target approach to renewables as houses become more efficient, issues like this are likely to multiply. Expressing the target as both a kWh/m2/a and roughly equivalent percentage of overall energy demand would sidestep this problem.
Paraic Davis at MCO Projects points to a legislative anomaly in the section of TGD L 2007 which deals with shared onsite electricity generation such as CHP in a multi-occupancy building. Despite the provisions of this section, sharing a private power supply is illegal in Ireland. “If a developer puts a combined heat and power unit into an apartment building, that will generate heat and electricity much more efficiently than Moneypoint, but it’s also illegal,” he points out. Providing for shared supply featured originally in the 1997 electricity directive, but was subsequently lost in its transposition into Irish law. Davis believes greater use of CHP could assist enormously in the reduction of emissions in Ireland. ”I estimate that we could save between 10m and 15m tonnes of CO2 per year if we made widespread use of CHP. Obviously you’d have to start small, but that small start would be to change the legislation, then that part of the building regulations would become feasible.”
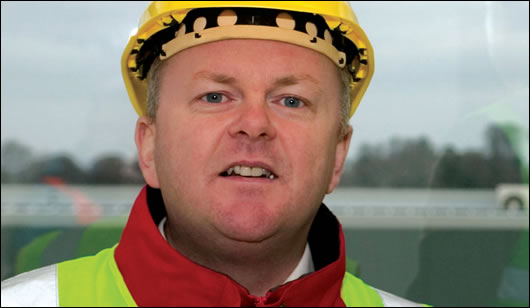
Tomás O’Leary of MosArt, Ireland’s first accredited passive house certifier
ACCEPTABLE CONSTRUCTION DETAILS
Little’s concerns in this area relate primarily to a lack of guidance in relation to refurbishment and renovation. In the forthcoming January edition of Construct Ireland he concludes a series of articles on appropriate upgrades of single leaf walls, and the health and condensation issues associated with ill-conceived approaches. “I’m half expecting that in four or five years’ time, there’s going to be a rash of stories about how asthma levels have increased, about how mould has been discovered in all sorts of conditions behind drylining approved under the Home Energy Saving scheme, that there’s going to be a lot of bad press about energy saving because there wasn’t enough technical guidance on insulating different types of walls.
“One thing we need to do in reshaping the building regulations is give refurbishment standards a huge kick,” says Little. “I would suggest that they need to improve by 60 percent immediately from where they were. Because houses tend to be significantly refurbished only once in every 30-40 years we need to increase the standard in one jump thereby ensuring that as many refurbishments as possible contribute to the national target. But we also need to support the new regs with a big increase in advisory documents. The [Department of the Environment’s guidelines on] acceptable construction details and the Homebond manual, for instance only relate to new-build.”
Dealing with thermal bridging is also a huge issue, in both new build and refurb contexts. “Increasing elemental U-values across doors, walls, roofs - great, but how those elements are connected is of great concern,” says Brian Rochford. “We’ve got accredited details and UK enhanced details and so on, but what’s lacking in terms of education for designers and builders is calculating Psi-values and avoiding condensation risk.”
Appendix D in the current part L provides a table of good practice Psi-values for each construction junction (at sills, eaves and so on) which, taken together, provide a whole house Y-value of 0.08 W/mK. “That’s a good value and should remain on as the new default standard for new-builds (replacing 0.15 W/mK)” says Little, “but we now need to raise the bar for acceptable construction details to 0.04 W/mK.” The regulations are also confused and ambiguous in relation to thermal bridging in refurbishment as Little’s third Breaking the Mould article in Issue 8, Volume 4 points out. “I can see a need for three tables in appendix D: 0.15 W/mK and 0.08 W/mK for refurbishment, and 0.08 W/mK again and 0.04 W/mK for new builds. In support of these the acceptable construction details guidelines needs to be revised for new build and a whole new series commissioned for refurbishment. Otherwise people will assume they can use new-build methods and materials where they are not appropriate.” He further added that the air-tightness value of 10 m3/m2hr in new-builds which was introduced in the current regs is very poor. “The Irish report for the Avash study, for instance, showed that even uninsulated, wet-plastered blockwork houses with rattling windows built in the 50s can exceed this level of air-tightness. The value for new-builds needs to jump to a standard of 3m3/m2hr alongside some really good regulations on safe, robust whole-house ventilation. Air-tightness and ventilation standards also need to be created for refurbishment.”
There are further issues here that the current regulations remain completely blind to. “Suppose somebody is trying to build to a low energy standard, and brings the U-value in their wall down from 0.27 W/m2/K to an impressive 0.15 W/m2/K or lower. They might think they can refer to the current acceptable construction details document and appendix D, select the relevant Psi-value listed for each junction, and go from there to feed in the 0.08 Y-value into the DEAP software: they’re allowed to but the fact is they shouldn’t be, because the Y-value would be wrong and the thermal bridges would be far worse. The acceptable construction details really only relate to somebody building to a standard of efficiency that is close to the minimum standard in the building regulations. As you improve the U-value of the window, wall, roof etc, the impact of thermal bridges that haven’t been equally improved grows significantly. The result, after all that money is spent, could be greater heat loss at those junctions than through the rest of the building fabric. Nowhere in the guidance documents does it tell you this... It’s clear to me that we’ve a lot of work to do in making this next jump.”
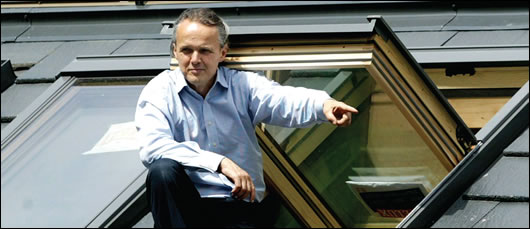
Lars Pettersson at his passive house in Moycullen. It boasts 6m2 of solar thermal panels and a 300L tank, which is sufficient for hot water generation. However to comply with TGD L 2007, the house would need 14m2 of panels and a 750L tank, which vastly exceeds the houses’ requirements
BUILDING CONTROL
The industry speaks with one voice on this issue. What’s the point in driving standards higher when they will not be enforced? Jay Stuart points to the policy breakdown implicit in rolling out the Home Energy Saving scheme to houses built only three years ago. Peter Keavney in Galway cites the fact that the SEI’s monthly report on BERs awarded to new build houses invariably lists a substantial number of D, E, F and G rated houses, when the reference house under the 2005 regs is a C2. How, he asks, can one government body certify the energy performance of a house that does not comply with energy legislation? “I worked for ten years in the UK,” says Brian Rochford, “and even the most modest 10ft by 10ft flat roof kitchen extension would get at least one visit from a building control officer. A one-off house would be visited four or five times, and when the building control officer arrives onsite and he says jump, it was how high? [This applied to] everyone – the architect, the client, the builder – because they had real power. I returned to Ireland in 1995 and I had one announced site visit from a building control officer, because a neighbour complained about noise on the building site. When the guy turned up he was more afraid of me than I was of him and he went away as quickly as he arrived.”
- Articles
- part l
- building regulations
- Capital L
- zero carbon
- emissions
- gormley
- joseph little
- housing completions
- home energy saving scheme
Related items
-
Scotland to accept passive house as regs compliant
-
Much ado about nothing
-
Embodied carbon & zero emission targets adopted in new EPBD
-
Scotland committed to continuing passive house journey
-
Scotland to mandate passive house for new homes
-
Decarbonising buildings “most important issue” – Climate Change Committee
-
Roadmap targets embodied and operational carbon
-
Techrete aims for net zero carbon by 2030
-
Disappointment at new building energy standards
-
Grant launches online learning academy
-
LETI: 33,000 net zero carbon homes planned
-
Scrap EPCs to unlock deep retrofit market, MPs argue