- Case Studies
- Posted
Sustainability in store
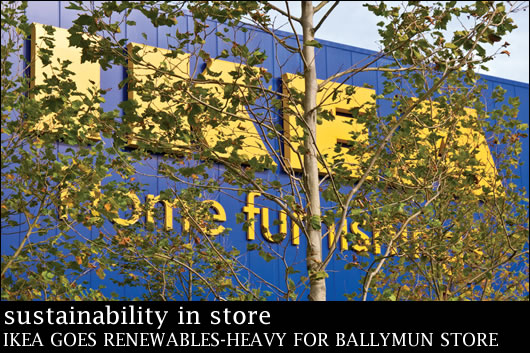
Little did we know when campaigning for the Fingal energy standard in 2005-06 that Construct Ireland would have a direct impact on Ikea’s first Irish store. Driven by a combination of Fingal’s requirements and their own renewable energy policy, the Swedish retail giant has invested in the largest ground source heat pump installation in Ireland and the UK, along with a well-thought biomass system fed by an onsite waste stream and a host of other green measures, as John Hearne reports
Ikea Dublin finally opened in July after an extremely long and extremely complicated gestation period. To facilitate the construction of the Swedish retailer’s 301st store, there were legislative changes, a torturous planning process and major public infrastructural works that are still not complete. A two storey steel frame structure over a partially enclosed ground level parking area on a 12.6 hectare site, Ikea Dublin has a total floor area of 30,598 square meters. It is as popular as it is vast. On the Sunday prior to Construct Ireland’s visit, more than 5,100 people glided up the travelator into its huge blue and yellow bulk.
Everything about this development is big. The site incorporates the biggest ground source heat pump installation in Ireland or the UK. This looks after the bulk of the building’s space heating requirement, and the entire cooling load. Within the first month of opening, the store achieved recycling rates of 90 per cent thanks primarily to a biomass boiler fuelled exclusively from onsite timber waste. This boiler takes care of all of the store’s hot water needs, as well as providing space heating to those parts not taken care of by the heat pumps. A building energy management system controls these systems, the low energy lighting, together with an occupancy driven ventilation system. Up on the roof, a third of the rainwater is harvested and used in public toilets and for irrigation on landscaping around the site.
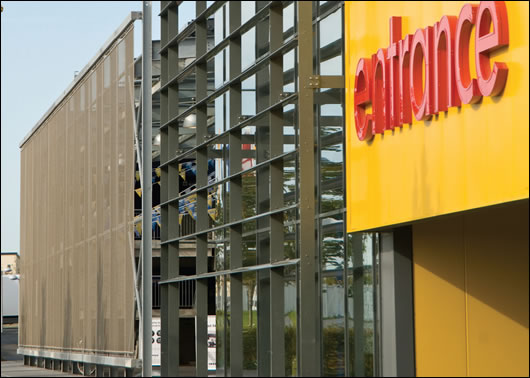
The entrance to Ikea’s first Irish store in Ballymun
“Frugalness in the use of resources has been part of our DNA from the very start.” says Charlie Browne, Ikea UK’s environment manager. “But when we sawed the legs off the first table in the 1950s, it wasn’t necessarily about environmental improvement, it was about the flat-pack concept; getting more tables to the marketplace with less cost…but then with the economies of scale, you’d get less trucks on the road, less emissions, less resources used.” With that frugality as a guiding principal, three years ago, the company developed an ‘IGR directive’ standing for Ikea goes renewable. This aims for 100 per cent renewable energy for electricity and heating/cooling, and is to be achieved by increased building energy efficiency measures, use of low/zero carbon systems alongside the purchase of green electricity. Cost reduction and resource efficiency usually pull in the same direction. However, to achieve the energy reductions sought in that directive, the company had to alter its investment protocols. “Normally, in putting capital expenditure together, most companies look at a three to five year payback. Ikea extended that to a nine year payback on renewables, specifically because they knew that the costs were high at the moment but we wanted to make that over-investment.” Browne points out that this decision would probably not have been possible if the company wasn’t in private hands. Shareholders don’t like long payback periods.
But while the organisation may have been moving towards a more sustainable energy profile on their own, Fingal County Council sought even more exacting standards, spurred on by the combined efforts of Green Party councillors David Healy and Joe Corr, and Construct Ireland editor Jeff Colley. The development had to reduce carbon emissions by 60 per cent below TGD L, and generate 30 per cent of onsite renewable energy.
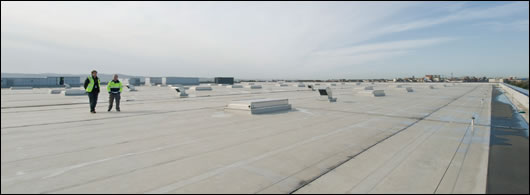
The vast expanse of roof space gives a sense of the sheer size of the building
Frank Doyle of OMS Architects and OMS Green explains that designing an Ikea store is all about negotiating within a range of inflexible parameters. “While this is what Ikea would call a standard store, each individual set of circumstances has to be addressed on the site, and Ikea have very prescribed areas.” The Ikea retail experience is based on a carefully plotted journey through the building. You do not wander freely, but are lead from entrance to showroom to market hall to warehouse to checkout. This format is central to the concept, and the design has to respond to that. Similarly, many of the materials used are uniform across all three hundred other stores, are sourced within a long-established procurement process and cannot be designed away. “We didn’t analyse the cladding other than its thickness and its U-values, because it is the corporate image of Ikea,” says Doyle. “These are full height panels, 11m high, all pre-manufactured and lifted into position; row after row.” While the design team did boost the insulation in the panels, thereby achieving 6 per cent of the 60 per cent energy reduction sought by Fingal, they could not tamper with the panels themselves, or the windows. “We incorporated brise soleil on the south elevation to minimise heat gain,” says Doyle, “but we did not deviate from the window specification so the introduction of brise soleil offered a more efficient solution.”
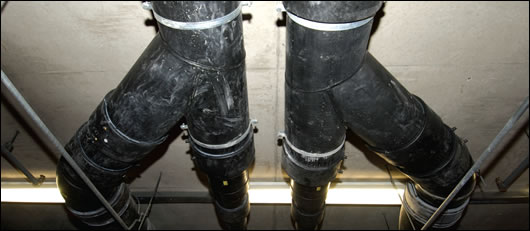
Symphonic pipes give the rainwater harvesting system more capacity because the water flows under a vacuum. When the rain fills to a particular level, the pipe runs full
A long blue box on stilts, this is an unprepossessing building. “Scandinavian design is at the core of the Ikea concept – that is good quality, good design, functional and inexpensive. The Ikea store model has developed to reflect this ethos. The cost of the building has a direct relationship with the cost of the product in the store,” says Brian McClinton of OMS. “They may be a design-led company, but when it comes to capital expenditure, bare-bones functionality trumps beauty. The only place they’ve really spent money – because it’s a big blue box – is on the front areas at the entrance and restaurant area. Stair cores are draped in banners to animate the elevation and promote different events and seasons.” McClinton points out too that this kind of utilitarianism is a valid aesthetic. “Show it naked if that’s what it needs to do,” he says. “So yes, it has an industrial feel to it, but that’s all it needs to have. Ikea express it as they see it.” This is no frills construction. “Behind the scenes,” says Charlie Browne, “it’s just grey breeze block walls and no ceiling spaces because that’s all frippery. It’s functional enough as a grey breeze block wall and it actually looks ok…We put in ceiling grids which are then used to hang displays and lights and banners and those kinds of things, and by allowing our engineers and decorators access to that roof space we can move things about easily. That kind of frugalness is inherent in our business model, in everything we do. Everyone travels economy class, no matter who they are. We always look at the best economic option, not the cheapest option, but whatever gives us value for money.”
Speed was also a vital element of the construction. “This store was built in thirty-four weeks,” says Frank Doyle of OMS. “To build something this size in little over thirty weeks is some achievement. They’re very focused, very driven, very cost conscious.” The construction process was very different to anything OMS had worked on before. Individual elements of the build are broken down and subcontracted out, often to firms already looking after that same element on another Ikea project elsewhere in Europe. “The panelling comes from a particular supplier because he’s also supplying all of the cladding panels for all Ikea stores all over Europe…If he performs, he’s kept and if he doesn’t, they put it out to tender again, and it’s the same with the windows, the same with the travelators, so there really isn’t a main contractor, just a series of sub contractors.”
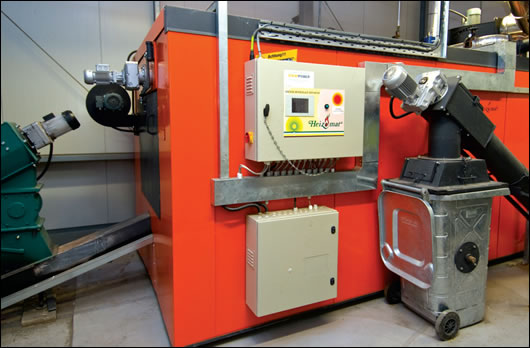
The Heizomat woodchip boiler caters for all hot water needs as well as space heating in warehouse areas
Given this standardisation, the design team were faced with particular challenges when trying to introduce additional insulation measures, or design out cold bridging. The insulation spec introduced runs as follows: The walls incorporate 120mm thick Rockwool wall panels, while the roof includes 100mm of TR26 rigid insulation board. On the ground floor and in enclosed building service areas including entrance lobbies, there’s 50mm of Kingspan Floormate. On the first floor, there’s 100mm of rigid board foil faced insulation fixed to soffits. That standardisation also makes it difficult to introduce natural light into the building. Glazing is restricted to the entrance lobby. The architects did however find a way of working in a little more sunlight. Fire regulations require facilities for dumping smoke in the case of fire. “In certain zones,” Frank Doyle explains, “we use glass-finned vents so that we could have more natural daylight, particularly over the warehouse area. We also included glazed roof lights over the foyer area and offices to optimise daylight and minimise the amount of electrical light required.”
When it came to establishing the right mix of renewable technologies, the design team thermally modelled a range of solutions. Using biomass in isolation would have resulted in a 24 per cent carbon reduction alongside an 8.8 per cent on-site renewable. A biomass/solar thermal mix would have given 29 per cent carbon reduction with a 10.5 per cent on-site renewable. Ground source was however the only solution that came close to meeting Fingal’s requirements, delivering a 65 per cent carbon reduction with 44 per cent on-site renewable. “We targeted the biggest energy user,” Darren Penson of building services and environmental engineers GDM explains, “which is the heating and cooling of the space. By using the ground source, that tackled all of the heating and cooling within the store.” The heat pump provides space heating of 884,018 kWh/yr (27.6 kWh/m2/yr), and, taking free cooling into account, provides cooling of 207,194 kWh/yr (6.5 kWh/m2/yr).
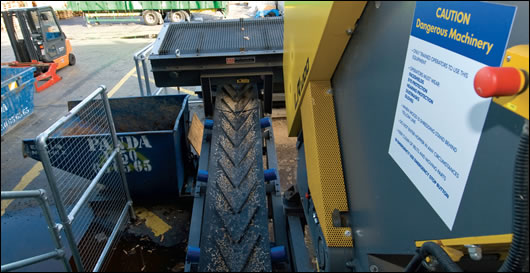
All waste wood is fed in to a wood chipper located at the rear of the building, enabling fuel for the woodchip boiler to be generated onsite
The geothermal bore field lies under one of the car parks adjoining the main building, and contains fully 158 individual boreholes. The water to water heat pumps, selected to suit the AHU heating/cooling loads and supplied by Aermec, were installed within the AHU casings on the roof. “The principle,” Darren Penson explains, “was that the closed loop bore field pipe-work was distributed within the building to serve a number of water to water heat pumps dedicated to AHU’s serving various parts of the building – the showroom, market hall, restaurant, kitchen and checkouts. This circuit also serves a number of Mitsubishi WR2 water to refrigerant heat pumps that serve the VRF systems within the office and staff areas of the building.” Ventilation is occupancy driven. CO2 sensors monitor air quality and control fresh air volumes depending on numbers within the store. In addition, the AHUs have variable speed drives to control supply and extract air volumes and match requirements to room temperature and occupancy. The AHUs also provide a certain amount of free cooling. In summer and whenever the external temperature is lower than the internal supply, the units will maximise the fresh air volume in order to provide free cooling. The roof-mounted AHUs are sited to deliver heat exactly where it’s required, thereby minimising service runs and duct lengths. “There’s a full opening underneath each one,” Frank Doyle explains. “Rooftop plant is designed in this way to feed directly into the building, thereby reducing problematic surface duct runs and losses and also minimizing the height of the units to reduce the visual impact of rooftop plant”.
The Heizomat woodchip boiler, provided by Clearpower who also provided a wood shredder and fuel store infrastructure, takes care of all hot water needs on the site, as well as providing space heating for the loading bay and warehouse areas. This, together with the ground source heat pumps, shoulders the project’s entire heating load. There is no fossil fuel backup. The biomass heating system, Darren Penson of GDM explains, was conceived primarily as a way of dealing with the waste wood generated by the business. “We suggested that the biomass drive all the domestic hot water within the building. And that’s used up their waste wood. There was a concern with the planning authorities that it would be considered a waste burner, although when we sat down with the planners and talked it through, they were swung round to it.” All told, the biomass boiler takes care of a total space heating load of 371,909 kWh/yr (11.6 kWh/m2/yr), as well as domestic hot water of 845,356 kWh/yr (26.4 kWh/m2/yr). Total carbon emissions as a result of space heating, cooling and hot water come out at 22.5 kg CO2/m2/yr.
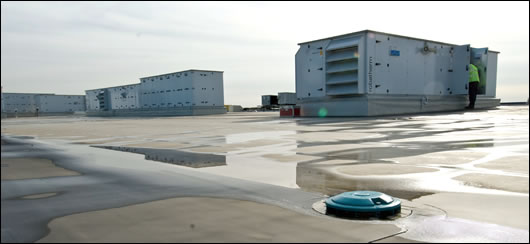
Inlets for the rainwater harvesting system with air handling units in the background. Rainwater is harvested, chlorinated and used in public toilets and to irrigate the landscape
The boiler is housed next to the loading bay/recycling centre to the rear of the building. Here, all waste wood, from pallets and damaged furniture are manually fed into a chipper. The woodchip produced is then conveyed via belts to a holding silo. From there, it’s augured into the boiler as required. All woodchip for the boiler is generated onsite, with no additional need for pellets or chips. In the recycling centre, all waste from the store is conveyed and separated into bins and compactors. Within the first four months of opening, the store has reached a recycling rate of 90 per cent. Charlie Browne of Ikea believes that the recycling equipment at the Dublin store will pay for itself within twelve months. “That’s assuming we did nothing and sent everything to landfill.”
“When we started recycling, we used to have a sealed compactor, which would crush the cardboard, then it would then be taken away and put it into another baling machine. We said hold on a minute, we’re doing the hard work by loading it into the bin and sorting it, why don’t we put the mill-size balers on our own sites and so instead of getting a cardboard bin which was a free uplift and someone else got the revenue, we baled it ourselves and loaded that straight into a curtain-side or a container. That goes to the mill and we get £25 a bale for it. In Dublin, that revenue will come to between e20,000 and e30,000 a year.”
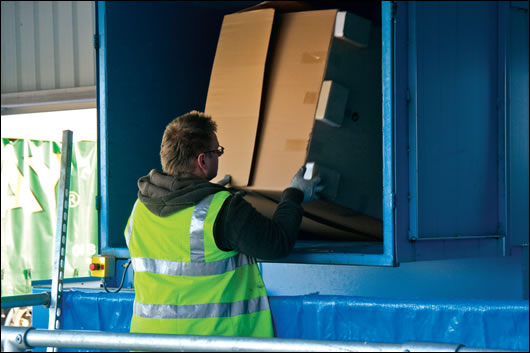
All waste from the store is separated and recycled where possible

All lighting is low energy, with PIRs installed in office and toilet areas. The building energy management system optimises the energy mix throughout the store. Different zones within the building have very different heating and cooling requirements. The loading bay area is necessarily exposed to the elements for long periods, generating a large heating requirement, which is looked after by the biomass boiler via high level heating cartridges. In the market hall, extensive lighting displays and high occupancy generate a substantial cooling load, while in the warehouse, where customers push trolleys and load up their own flat-packs, there’s a lesser heating load due to the nature of the activity – temperatures are generally maintained between 17 and 19 degrees.
Rainwater is harvested from the roof area, chlorinated and used in all public toilets and to irrigate the landscape. It’s a symphonic rainwater system, Frank Doyle explains. “A symphonic system has far more capacity because it flows under a vacuum. When the rain fills to a particular level, the pipe runs full,” he says. Because air isn’t allowed in, the entire pipe volume is used, so you can reduce pipe diameters dramatically. “If you had a conventional system, you would need a huge amount of rainwater outlets for a building of this scale.” Once the water is collected, the pipes split off, with a third harvested for greywater recycling and two thirds going into the attenuation tank. “This system minimises lots of things, including pipe sizes, but also roof penetrations and maintenance.”
With 1,527 car parking spaces, the whole concept is of course hugely dependent on the private car. There are however bike parking facilities, coach parking for 12 coaches, and a bus route running through the site. If Metro North goes ahead, there will be a Ballymun stop. And, as a planning condition, Fingal required that Ikea provide subsidised home delivery for those who use public transport to come to the store.
This was an unusually complex project says Brian McClinton of OMS. While Fingal was the planning authority, the land was owned by Ballymun Regeneration Ltd. Working through the raft of design, environmental, drainage and planning issues on a development of this scale with two separate agencies took a great deal of time, effort and diplomacy, however both local authorities were very supportive. McClinton sees the project as central to the ongoing regeneration of Ballymun. “Ikea has helped to place Ballymun on the map in a very positive way,” he says. “Sustainable design is not just about the technology in the building; it is a much broader concept and should benefit the wider community now and into the future. Ikea ticks a lot of the boxes. When you look around Ballymun, there are lots of fantastic projects large and small jigsawing together. I think the whole piece will come together very well over the next few years.”
Selected project details
Client: Ikea
Architects: OMS Green
M&E engineers: GDM
Main contractor: RG Group
Biomass heating system: Clearpower
Heat pump design and installation: TCS Group
Heat pump suppliers: Aermec /Mitsubishi Electric Ireland
- Articles
- Case Studies
- Sustainability in store
- Ikea
- Finglas
- Ballymun
- renewable
- heat pump
- ground source
- biomass
- onsite waste stream
- OMS Green
- Clearpower
Related items
-
It's a lovely house to live in now
-
State-of-the-art heating test lab opens at GMIT
-
Woodland wonder
-
The stunning low energy seaside home that's built from clay
-
Mayo passive house makes you forget the weather
-
Life in an air-heated passive house - Five years on
-
Affordable homes scheme reflects rise of Norwich as a passive hub
-
Larch-clad passive house inspired by a venn diagram.
-
389 sqm home, €200 measured annual heating
-
‘3D textbook building’ opens in Ballymun
-
19th century barn gets 21st century fabric upgrade
-
Passive architect walks walk with Carlow home