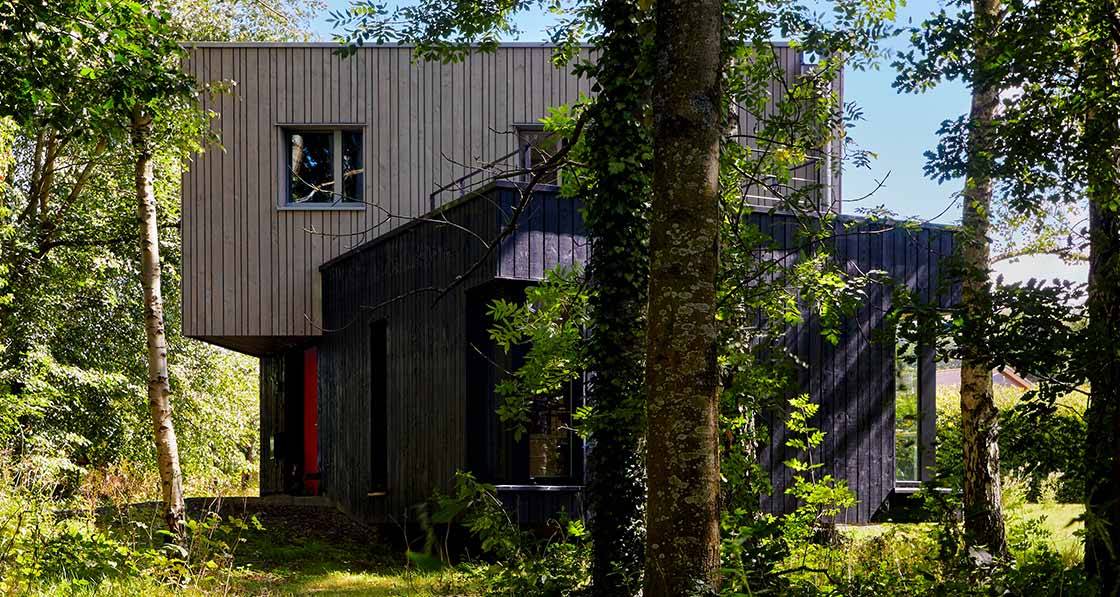
- New build
- Posted
Woodland wonder
Hiding in woodland in an area of outstanding natural beauty, the Fishleys passive house manages to be both strikingly contemporary yet deeply sensitive to its rural setting. It also boasts a masterfully crafted timber frame structure with one of the best airtightness results this magazine has ever published.
Click here for project specs and suppliers
Building: 190sqm timber frame passive house
Location: Colwall, Malvern, Worcestershire
Completed: November 2016
Standard: Passive house certified
£34 per month for all heating & electricity
Despite its modern appearance, the three-bedroom Fishleys passive house won planning permission on the rural Herefordshire-Worcestershire border largely for its sustainable credentials and sensitive design.
From the outset, the design embraced the site’s concealed position nestled in woodland in the village of Colwall, located within the Malvern Hills area of outstanding natural beauty.
“The owners wanted it to feel like a retreat in the woods as they both love woodland very much, so it has no relationship with the road. We tested views from all around the site and it was well-sheltered by the woods,” says architect Matt Hayes of leading passive house design firm Architype.
“But we also designed it to capture the stunning views across to British Camp, an iron age hill fort that is one of the highest points in the Malvern Hills. One other important design element was to make the most of the solar gain from the south.”
This article was originally published in issue 29 of Passive House Plus magazine. Want immediate access to all back issues and exclusive extra content? Click here to subscribe for as little as €10, or click here to receive the next issue free of charge
To make sure the house blended in with the woodland, the architects tested different cladding materials before settling on Douglas fir. Matt says the “vertical feel” of the cladding blends in well with the birch, ash and oak trees in the woodland.
Meanwhile the small ‘retreat’ section of the house has a much smaller mass that cantilevers into the woods so “it feels like it’s tucked into this cluster of silver birches”.
Hayes continues: “The house is seamlessly bedded into the woods and the route through the woods from the road is impressive, I think. As you get closer to the house, you see the striking red door set against the green of the woods. The timber cladding has had a natural oil stain that gives it a grey-silver hue that will eventually wear off as all the timber is silvered uniformly.”
Alongside the woodland niche and the spectacular views, the owners Liz and Mike Hill enjoy the quality of life inside their passive house. “We’re very happy here. Last summer, when the temperatures were so high, we had a nice comfortable working temperature all day,” says Mike.
Last summer, when the temperatures were so high, we had a nice comfortable working temperature all day.
“It never exceeded the temperature outside until around 10pm in the evening. We’re also passionate about ecology, growing our own food and taking care of the environment, so the passive-house lifestyle suits us.”
The couple’s plan, hatched back in 2015, was to dismantle a large barn on their four acres of land, auction it on eBay, then replace it with a passive house. They also knocked the old 1960s house they had been living in on the site.
They then approached local passive house specialist Architype and were given a series of design options to choose from for the house. They ended up surprising themselves by going with a flat roof design rather than a more traditional style. “Although we stipulated that we didn’t want a boxy, flat roof, the more we looked at it the more we liked it,” says Mike.
From the start, Mike and Liz were closely involved in the entire process. They had a number of requirements that Architype had to incorporate into the design. Both are software specialists who sometimes work from home, so they needed two study rooms, but these rooms had to be easy to convert into double bedrooms for when their two adult children, or elderly relatives, visit.
Another requirement was that they have no intention of moving out of the area, and the house had to be easy to manage in old age. One final stipulation from Liz was to avoid the trend for open-plan living. She wanted the kitchen to be separate from the living space, ensuring noise, smells and mess were hidden away.
1 The Isoquick EPS foundation system wraps the entire raft foundation in insulation to eliminate any thermal bridges; 2 laying the 250mm reinforced concrete slab; 3 installing I-beams for the stick-built timber frame system; 4 Green Building Store Progression windows installed into the timber frame system; 5 airtightness detailing around windows; 6 external wall build-up includes a Siga Majvest façade membrane, a 50mm ventilation zone, and 2x20mm Douglas fir cladding.
“We made it as efficient and flexible as possible,” says Matt. “Both studies double up as guest bedrooms and one of the study areas is on the ground floor. It’s next to a wet room that is designed with concealed knockout doors, so it’s easily transformed into a ground-floor accessible bathroom. It means the ground floor has the potential to be turned into a bedsit with everything they need.”
And though the house has no attic for storage, the architects designed deep cupboards along the corridor on the first floor, as well as a walk-through library on the way to the study.
Herefordshire is fortunate to be the home base for some of the UK’s most experienced practitioners of passive-house development. Hereford-based Architype has won three CIBSE building performance awards for passive house schemes and become renowned as leaders in designing buildings of all types to the standard, and many of the firm’s most high-profile projects have featured in the pages of this magazine.
After a decade of building passive houses, they now make up 70% of Architype’s current projects, including the UK’s first passive house-certified secondary school for the London Borough of Sutton.
Meanwhile, the builder for Fishleys was another Herefordshire-based passive house specialist, Mike Whitfield. In 2005, Whitfield was the main contractor for the Duchy of Cornwall on the conversion of two barns into Architype’s office, a project that won the 2007 RIBA sustainability award. He has completed around 15 passive houses over the last decade and is now working on a low energy building to mark Prince Charles’ 70th birthday.
On the Fishleys development, Whitfield took charge of the build on site after Architype had completed the plans. He liaised with the engineer and spoke almost every day with Liz, who was working from home. Whitfield suggested all kinds of small details, such as an oak door with oak latches, which added to the beauty of the home, although in other matters, the couple preferred to find their own more cost-effective options.
The Fishleys house proved quite complex as it consists of two interlocking cubes.
Groundworks lasted from summer 2015 until the end of the year and then building work began in January 2016. Whitfield’s team had the whole wooden frame watertight using I-beams in March despite torrential downpours and high winds at the beginning of February. The house was waterproof after eight weeks and the couple were able to move in by November 2016.
All the framework was built on site as Whitfield prefers not to use prefabricated panels. “It’s more expensive to use prefabricated as long as you have the expertise to do it efficiently yourself. But if you have inexperienced carpenters on their first passive house, a factory product might be easier,” he says.
“Another reason we prefer to build it ourselves is it gives us greater flexibility to start and finish when we want. In the time we were waiting for factory frames to arrive we might have built half of the structure. Having said that, as our workload has increased, I’m considering using more prefabricated parts so we can work on more than one at once.”
1 SMARTPLY PROPASSIV panels fitted to the walls and roof deliver outstanding levels of airtightness; 2 Checking the Freedom Pet Pass dog door for air leaks with a smoke pencil; 3 the dog door installed in the external breather membrane; 4 roof build-up includes a breather membrane, with a 150mm ventilation zone, and 24mm WBP Plywood above; 5 this is followed by a Resitrix EPDM waterproofing roof membrane; 6 builder Mike Whitfield after others members of the team told him there was a “big leak” in one particularly difficult corner of the build.
The Fishleys house proved quite complex as it consists of two interlocking cubes and it required a lot of additional engineering to cantilever all the corners and the front door using dragon beams. “But it was a fun house to do with two different foundation systems,” Whitfield says.
All the way through the process, Liz and Mike kept a detailed blog with pictures (www.blog.fishleys.co.uk). It started out as a way of keeping family in touch with their progress, but soon attracted a wide audience of people interested in passive houses. For example, they described how they had planted an orchard to make amends for the loss of the trees cut down to make room for the passive house.
The blog detailed the results of the airtightness tests, which initially gave a reading of 0.2 air changes per hour (ACH). Normally, passive house standards require less than 0.6, but the team had assumed 0.3 as a design target given the extensive passive house experience of those involved. A second test came back with the even better figure of 0.13 ACH, the lowest figure ever achieved by Mike Whitfield and his team, and one of the best results ever published by this magazine — especially impressive given the complex shape of the house.
Whitfield credits the collaborative nature of the project for its success and says that getting an experienced passive house builder on board early in the process is key to delivering the passive house standard as smoothly as possible.
Meanwhile Caplor Energy installed 4kW of solar PV panels on the roof — these are invisible from outside because they are hidden by the roof parapet. That system has a Powerflow energy box that diverts excess electricity to heat water. Rainwater is collected from both the greenhouse and garage to be used for gardening. The couple will now turn their sights to three new passive houses which they are hoping to build on the site of their old house. There have been no public objections to their plans and they now await the council’s green light. Architype and Mike Whitfield will renew their partnership for the build. But the three new passive houses will be quite different in design to Fishleys. As they will have a close relationship with the road and be far more visible, the plan is to use a conventional pitchedroof design rather than flat roofs. Each will be put on the market with a decent-sized garden attached.
Selected project details
Clients: Liz Taylor & Mike Hill
Architect: Architype
Contractor: Mike Whitfield Construction
Passive house consultancy: Architype, Elemental Solutions & Alan Clarke
M&E engineer: Alan Clarke
Structural engineer: Allan Pearce
Energy rating assessment: Energy Surveys
External insulation: Steico
Blown cellulose insulation: Warmcel, via PYC
Insulated foundation system: Isoquick
Windows & doors: Green Building Store
Airtightness tapes: Ecological Building Systems
Systems, via Green Building Store
Wind-tight membrane: SIGA
Airtight OSB board: Medite SmartPly
Plasterboard: Gyproc
Sarking board: Panelvent
I-beams: Pasquill
Flooring: Mandarin Stone
Clay-based paints: Keim
Plaster: Tadelakt, via Mike Wye Ltd & Associates
Oils & stains: OSMO
EPDM membrane: Carlisle Construction Materials
Solar PV system: Caplor Energy
Heat recovery ventilation: Paul, via Green Building Store
In detail
Building type: 190sqm detached two-storey timber frame passive house
Location: Malvern, Worcestershire
Completion date: November 2016
Passive house certification: Certified
Space heating demand (PHPP): 13 kWh/(m2a)
Heat load (PHPP): 9 W/m2
Primary energy demand (PHPP): 93 kWh/(m2a)
Heat loss form factor (PHPP): 3.10
Number of occupants: 2
Overheating (PHPP): 3.9%
Airtightness (at 50 Pascals): 0.13 ACH
Energy performance certificate (EPC): B 90
Measured energy consumption: 1,905 kWh electricity consumed during 2017. 5 x 47kg LPG gas bottles consumed for heating in same year.
Energy bills (measured or estimated): £260 spent on 5 x gas bottles in 2017 and £375 spent on electricity in same year, including VAT & standing charges. £225 received in renewable energy feed-in tariff in 2017, making for a net energy spend of £410 that year.
Thermal bridging: Thermally broken insulated raft slab and TGI balloon timber frame, thermally broken window frames with insulation over frames and Compacfoam at thresholds.
Ground floor: Thermally broken insulated raft slab to the main portion of the house: 150mm compacted base followed above by 25mm sand blinding, 250mm Isoquick EPS foundation system, 250mm reinforced concrete. U-value: 0.14 W/m2K. The ground floor study features a cantilevered timber frame detailed with dragon beams offset from the small-scale pile foundation.
Walls: 15mm Gyproc Fireline with 25mm service zone internally, followed outside by 15mm SMARTPLY PROPASSIV panels with joints taped, 350mm TGI joist fully filled with Warmcel insulation, 18mm Steico Universal board, Siga Majvest façade membrane; 50mm ventilation zone, 2x20mm hit & miss Douglas fir cladding. U-value: 0.10 W/m2K
Roof: Resitrix EPDM roof membrane externally over 24mm WBP Plywood, followed inside by 150mm ventilation zone, breather membrane over 18mm Panelvent, 400mm TGI joist roof rafters, pumped full of Warmcel insulation. On the underside, 15mm SMARTPLY PROPASSIV panels as airtight layer. Service void with 25mm battens. Gyproc Fireline plasterboard finishes to ceilings. U-value: 0.09 W/m2K
Windows & external doors: Green Building Store Progression windows & doors high quality laminated finger-jointed Spruce Thermowood windows with cork insert. Argon fill. G value 36%. Passive House certified. Overall standard whole window U-value 0.68 W/m2K.
Heating system: Worcester Bosch Greenstar 12i System (LPG) with Solar PV (Powerflow Energy recovery) to be supplied to the hot water immersion heater when there is a surplus of PV power. Heating emitted via Stelrad radiators.
Ventilation: Paul Novus 300 MVHR system. Passive house certified heat recovery efficiency of 94.4%.
Water: All cold-water outlets from mains, showers and bathroom cold water supply from after hot water cylinder pressure reducing valve. Conventional pipework arrangement with 22mm main pipe and 15mm to outlets. Rainwater harvesting for gardening water supply.
Shading: External solar shading blinds to selected windows.
Green materials: Tadelakt plaster, clay-based Keim Ecosil paint, cellulose insulation, Douglas fir cladding & internal linings, OSMO oil & stain, low water toilets, Oak & Travertine flooring.
Image gallery
https://passivehouseplus.ie/magazine/new-build/woodland-wonder#sigProIdcbfe0cfa18