- Case Studies
- Posted
Out of the Woods
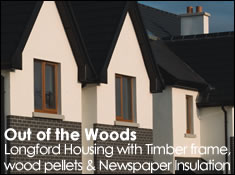
Many of the opportunities that trees offer for sustainable building are harnessed by a housing development in Ballymahon, Co. Longford which combines timber frame construction with recycled newspaper insulation and wood pellet heating. Adding in solar panels and attention to detail for airtightness, these low energy, low carbon homes reveal a developer who sees a bright future in going green. John Hearne visited the site to find out more.
At Ballymahon in Co. Longford, developers Bespoke Construction are on the point of completing the last of the 36 houses in their Section 23 development, Auburn Village, on the banks of the Inny River. Built to a high energy spec, there’s little external sign of the range of sustainable technologies incorporated in the build save for the solar panels on every roof.
Now almost completely sold out, Bespoke’s managing director Ronan Meeley says he’s witnessed a dramatic change in the house buying public’s attitude to energy-aware building. At the beginning of the boom, before the surge in oil prices, no one wanted to know about solar panels or wood pellet boilers. Now they do. Funded under SEI’s House of Tomorrow programme, the most widely known scheme for promoting greener practises within the building trade, grant aid of up to €8,000 per unit is available per house for housing developments of 10 to 50 units where heat energy usage and associated CO2 emissions are reduced by at least 40% relative to building regulations. Having studied renewable energy construction in college in the UK, Meeley has long been interested in putting together a housing development which would improve the standard building spec. “These are Section 23 houses and there’s quite a number of people building around here. I said well, this is my opportunity, especially with the BER (Building Energy Rating) certs coming in. I’ll be ahead of it.”
Two flat-plate solar panels on each roof look ater approximately 60% of annual hot water requirements.
Though a more expensive process than the traditional, minimum-requirement block-build, the market for eco-friendly building is maturing quickly. Asked if he can charge a premium for the higher energy spec, Meeley doesn’t hesitate. “I am and I do and I get it.” In addition to entertaining potential house-buyers, he also plays host to a constant stream of window shoppers. “I spend more time educating people about insulation, solar panels and the wood pellet boilers. The amount of people you get in and they’re just thinking about putting it into their own house.”
Developer Ronan Meeley chose flat plate collectors, which he saw as being more durable, over evacuated tubes
The starting point, he says, is energy conservation. You’ve got to get the insulation right. “If someone told me, I’ve got insulation there that’ll cost €500 or I’ve got insulation there that’ll cost €1,000, I’ll put in the €1,000 because I know I’ll get my money back out of that. Guaranteed.” The timber frame for each house was designed and erected by Modern Timber Homes in Letterkenny. Tommy Ryan of the company explains that the timber, all of which is Scandinavian CLS, is first treated to prevent rot. The frames are then designed for each individual house type and once they’re signed off by the developer, they’re put into production. “Everything is done in factory conditions.” Says Ryan. “Basically what we deliver to the site is all the external walls. They come in sections and everything is assembled onsite with the help of a crane.” Tradesmen onsite avoid boring the frame itself but install all services after cross-battening. “We leave the frame in such a way that it’s ready to be rendered. It’s all in place, all fixed properly, all nailed properly, so when the block guy comes, it’s all ready for him to start.” The standard breathable membrane is attached to outer walls to prevent moisture damage.
Warm cellulose insulation, made from recycled newspapers is delivered to site
The insulation itself is supplied and fitted by the Gilmartin Group in Oranmore, Co. Galway. “It’s called Warmcel.” Paul Gilmartin explains. “It’s recycled paper, and there’s boric acid added to it to give it a flame retardant. It’s got a thermal conductivity in a wall of 0.036, which in your typical 140mm frame gives a U value of 0.25.” ertified by both Irish and British Agrément boards, Warmcel is a blown product manufactured by Excel Industries in Rhymney in Wales. “A lot of the recycled paper is sourced here in Ireland,” says Gilmartin, “and shipped over to Wales. They make it into insulation and we take it back then.” In a partnership arrangement with Excel, the Gilmartin Group actually purchase the newspaper for the manufacturer here. “We set it up for them because what was happening was we were buying the material and the lorries were going back empty, so we sourced paper here for them.” To facilitate installation into external walls at Auburn Village, a breathable membrane is stapled to the frame and the material is then pumped in, to a thickness of 140mm. 300mm is pumped into the attic space, where the horizontal lie removes the need for a membrane to hold it in place.
Warmcel cellulose insulation is pumped into the walls delivering a U value of 0.25 at a thickness of 140mm
The material provides a high degree of air tightness. Blower door tests performed on individual houses have apparently achieved highly satisfactory results. Ronan Meeley says that the fact that it’s a blown product has the added benefit of cutting down on packaging waste. “It’s a great system,” he says, “because I just ring them up and say lads, the houses are ready for insulation. They come along, you literally have nothing to do with them. The way insulation and packaging used to go around a site, you’d be forever pulling it out of it. It makes for a way cleaner site.” Even before any heat source is introduced to the houses, he says you can feel the difference the insulation makes. “The boys have a canteen set up in one of the houses, on a gas bottle. You go into it when they’re boiling the kettle and you‘ll know it. The minute you walk into the door, you’ll know the boys are boiling the kettle.” PVC Golden Oak windows are supplied and fitted by Munster Joinery. Delivering a U value of 1.5 on the glass and 1.9 on the entire unit, each one comprises a double glazed unit of 24mm of glass with a 16mm argon fill at the centre.
Space and water heating is provided by a combination of a wood pellet boiler and roof-mounted solar panels, both of which are supplied by Heat Merchants. The boilers, manufactured by Baxi in Denmark, are housed in condensation free sheds erected in the back gardens of each house. “I went with the Baxi one because it’s the simplest one.” Ronan Meeley explains. “I was looking at an awful lot of wood pellet boilers and they had electronic ignition, they had this, they had that, they had so many different controls, a lot of moving parts. I don’t like moving parts. They’ve been making them for the last donkey’s years and it’s specifically designed for burning wood pellets, it’s not a converted oil one.” Ken Lenihan of Heat Merchants says longevity also formed a large part of the company’s decision to act as agents for Baxi in Ireland. “The boiler itself is being manufactured for about forty years, so it was proven in the field.” He says. “While it’s new technology to Ireland, it’s not new to them.” The boiler is a 15kW modulating unit, allowing it to operate at a much lower output if required. “The principal of the Baxi,” says Lenihan, “is it will burn either the 6mm pellet or the 8mm pellet, and it’ll burn corn, wheat, oats, barley. They are used as fuel. The calorific value of corn wouldn’t be as good as pellets but it can burn it.”
The Timber frame for each house was designed and erected by Modern Timber Homes. The frames are designed for each individual house type and once they're signed off by the developer, they're put into production in factory conditions
During the winter, the boiler is on 24/7. It retains 80L of water which is kept at a constant temperature while in idling mode. The logic here is that it’s more efficient to heat warm water than cold. In order to maintain this temperature, the augur which carries the pellets from the hopper to the boiler turns for one second once every fifteen minutes. Inside the house, three zones have been set up: upstairs, downstairs and water heating. Ken Lenihan explains what happens: “If at 8am, the time-clock downstairs calls for heat, it will open a motorized valve inside in the house…The water will now leave the boiler and go into the house. The temperature of the boiler will subsequently drop. When it drops, the boiler will detect that and it will fire up to 30% of its rated output…and if it’s not able to meet the heat requirement inside in the house, it will then go to 100% mode, and it will modulate between the two of them depending on the heat demand inside in the house. There are thermostatic radiator valves on all the radiators so if one room picks up the temperature faster than the rest of them, that rad will automatically knock itself off inside in the house.” While low maintenance, the boilers need to be cleaned out once a month, a job similar to cleaning out a fire. The pellets themselves boast a very high burning rate, leaving only 0.02% ash, which must be removed on average once a week.
There were teething troubles, Meeley explains. “When I started the first ones up there I was green as grass. They set it up, it was grand, radiators all piping, but then I noticed that I was using so many pellets. I was asking why am I using so many pellets? I was told that I’d be using so many kilos a week, and now I’m using more and the house is insulated the way I was told. I was saying, God, am I after buying a pig in a poke? So I got the fella over from Denmark, the actual production manager. So he came over and we went through it with me, and sure, they’re using hardly any pellets now and they have the heat. When the boiler goes full tilt, it’s absolutely eating pellets, but it never needs to go all the way up to the top.”
Two flat-plate solar panels on each roof look after approximately 60% of annual hot water requirements. The panels are German made Wikora units, each one covering 2.34m2, giving a total coverage per house of 4.68m2. Planning and other considerations prevented the roofs on which the panels were mounted from facing full south, leading to a slight, but not significant reduction in efficiency. Flat-plate panels, while not quite as efficient as tubeless panels, have the advantage of being more robust. “There’s less moving parts in it.” Says Meeley. “I’m not into moving parts because I’m putting on seventy-two solar panels and if something goes wrong with one of them, if you’re living in one house and you see me up rooting around at a solar panel on another one, you’ll be saying well if that solar panel is wrong, what’s wrong with mine, so I’m not willing to take the chance on that.”
“I think solar panels are absolutely top drawer. I’ve been keeping a close eye on them. What I love is when a punter comes in and they say you’ve all these solar panels, what are they like? I can say the water’s at 61 degrees, and they say sure how could it be? 61 degrees is fierce hot, there’s hardly any sun outside, and I say come here a minute and put your hand on that pipe and their whole expression changes. Once a person can touch it, that makes all the difference.”
The panels are hooked up to the lower coil of a dual coil 300L hot water cylinder in the upstairs hot press. The upper coil is linked to the wood pellet boiler. “In winter time,” Ken Lenihan explains, “when you’ve poor solar gain, you’re only heating the top part of your cylinder with the wood pellet stove. That’s timed to come on say for an hour in the evening to heat the top half of the cylinder but if tomorrow morning was fine, your cylinder is able to take heat from the sun because it goes to the bottom coil. Naturally enough when you heat the top half of your cylinder, hot water rises so you’ll never heat the whole cylinder, you’ll only heat the top half, so you always leave room for heat to go from the solar to the bottom coil. There’s a thermostat on that cylinder; suppose you have your water timed to come on at 7 o’clock in the evening through a thermostat. If the cylinder is up to temperature the valve won’t open.” The cylinder itself is very highly insulated. If there’s no draw off of hot water, it will only lose one degree in twenty-four hours. “As a back-up,” says Meeley, “if they ran out of pellets and they ran out of sunlight, I have an immersion but I have the immersion just on a switch, I have it as basic as you can get it. They can’t set the time but they have to literally go out and press the switch and it has a big neon light on it. You’d say that’s really gammy looking but that’s why I have it that way.”
With several of the houses now occupied and initial difficulties with the boiler sorted out, there are no further problems to report. “Anyone that’s in there is happy with the amount of money they’re spending on the heating, and the electricity bills, they’re tiny. When you take an immersion out of it, what do you use? The cooker and the kettle. That’s all…I’ve all grade A appliances fitted in them houses too, I thought it would go against the ethos not to. I supply the oven, the hob, the extractor, fridge freezer and the washing machine, they’re all grade A, Whirlpool appliances.”
Selected project team members/suppliers:
Developer: Bespoke Construction
Timber frame: Modern Timber Homes
Cellulose insulation: Gilmartin Group
Solar panels & wood pellet boilers: Heat Merchants
Windows: Munster Joinery
- Articles
- Case Studies
- Out of the Woods
- ballymahon
- longford
- bespoke construction
- airtightness
- house of tomorrow
- newspaper insulation
- solar panels
- wood pellet
- cellulose
Related items
-
Why airtightness, moisture and ventilation matter for passive house
-
Airtight delight
-
It's a lovely house to live in now
-
Solar panels to receive VAT drop in aim to boost uptake
-
Partel’s airtight membranes now certified for passive house construction
-
Mass timber masterwork
-
Partel obtains EPDs for airtight membranes
-
Ecocel supplying English developer Bell Blue
-
Manhattan modular apartments feature Wraptite membrane
-
Ecocel on site with 56 homes in Cork
-
Partel’s Izoperm Plus achieves passive house ‘A’ cert
-
Superb airtightness result for Manchester ICF house