- Case Studies
- Posted
Killeagh, Co. Cork
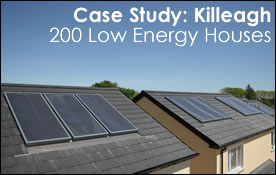
The rapidly growing public interest in sustainable building is finally starting to impact on property developers. Bill Quigley of Nutech Consultants describes an innovative 200 house development currently on site in Co. Cork where forward-thinking developers J & W Leahy Brothers have decided that the market is ready for low energy, low CO2 buildings.
Probably one of the most exciting and large scale low energy/low CO2 housing projects in Europe is presently being constructed in Killeagh, Co. Cork
The housing at Killeagh will feature the following technologies:
- A well insulated fabric with a real U-value which will match the calculated value.
- The houses are designed to be very airtight in terms of the unwanted level of air infiltration.
- A highly efficient heat recovery ventilation system is fitted which guarantees the level of fresh air ventilation.
- An air solar heating system is being used which delivers solar energy to the ventilation and heating system together with the domestic hot water system.
- Any required backup energy is being delivered by way of a wood pellet boiler that is sited in the living room and is integrated with the air solar heating and ventilation system.
NuTech Consultants, in conjunction with the Kingspan Century team have designed the low energy/low CO2 features for this housing development. The target was to design a house that could save some 95% of the CO2 emissions associated with the space and water heating demands of a standard 3 to 4 bedroom house typically built by developers
In this article we will explain the design brief for the energy systems as set out by the developer / builder, the background to the thinking behind the design, the systems and hardware being used and the results in terms of the actual construction of the houses.
The housing development at Killeagh, Co Cork
This development consists of 200 houses. There will be 2, 3 and 4 bedroomed houses on the site. Some of these will be bungalows on fairly large sites. The site size is 22 acres and the resulting density is roughly 22 houses per acre.
The developer / builder is J & W Leahy Brothers of Middleton, Co. Cork. The architect is Richard McGrath and mechanical services were designed by EDC Consultants Ltd. All of the energy calculations and systems were designed and carried out by the Kingspan Century team with NuTech Consultants.
The Builder / Developers requirements and background to the design
Initial discussions took place between Kingspan Century including NuTech Consultants and J & W Leahy Brothers to consider possible designs and systems that could be used to satisfy the space and water heating demands of the houses. Bill Leahy, Director of J & W Leahy’s, stated categorically that he did not want to use oil or gas fired systems as the primary or secondary energy supply units for these houses. His main idea was that he wanted to ‘future proof’ these houses and his clients against oil price rises and availability of supply. This did put some pressure on the design team to come up with a design and energy supply package that was practical, economical and deliverable within a reasonably short space of time.
It was explained to Bill Leahy that Kingspan Century with NuTech Consultants recently completed the Kingspan Century Formula 1 House Project. This project had received support from Sustainable Energy Ireland under its House of Tomorrow research and development fund. The team had arrived at a number of conclusions principally as follows:
Firstly,
- Typically, 1/3 of the energy required for space and water heating in a developer type house is accounted for by way of heat loss through the fabric.
- The second 1/3 is by way of energy required to counteract the heat loss due to unwanted air infiltration and the necessary air for ventilation.
- The third 1/3 is by way of the energy required for domestic hot water.
Secondly,
This meant that the energy demand for space and water heating could be reduced to as low a figure as economically possible by doing the following: - Insulate the houses to as high a level as possible. Ideally this insulation should be factory fitted. This deals with the first third of the energy demand.
- Make the houses as airtight as is practicable – a level of 0.1 air changes per hour at normal pressure was decided upon. This means that a mechanical ventilation system is required. It was decided to use a solar assisted heat recovery ventilation (HRV) system to provide adequate quantities of fresh air. This ensures that the second third of the energy demand is greatly reduced.
- Utilise the same solar heating system to supply the energy for the domestic hot water demand. This means that the domestic hot water demand can be reduced by some 60%.
- Furthermore, it is possible to use the solar air HRV system as the heating system of the house, thereby saving in costs.
- Building in highly insulated and airtight construction that is achieved with Kingspan Century’s special timber frame design is a huge advantage. Great use of the ‘balanced thermal capacity’ of timber frame construction can be made as this allows excellent use of the low level solar gains that are available in Ireland in winter.
Having reduced the energy demand to as low a figure as practicable, the energy supply side was addressed. A small wood pellet stove with a back boiler was used as the backup energy supply unit. This stove could be conveniently placed in the living room. By way of all of these techniques the Kingspan Century team with NuTech Consultants had reduced the CO2 emissions of a typical house by some 95%.
Bill Leahy decided, following discussions with his fellow directors, to use these techniques to build the houses at Killeagh such that they would be low energy/low CO2 houses that did not rely on oil or gas as the fuel to supply the space and water heating demand. Furthermore, because the energy demand of these houses is low it would not require a large tonnage of wood pellets per year. This meant that the supply of wood pellets could be by way of the standard 18kg bags rather than by way of requiring a delivery of 3 tonne lots to a storage room.
Bill Leahy had considered the use of ground source heat pumps but rejected for a number of reasons. Firstly, if the instantaneous design heat load was reduced from as much as 10 kW to as little as 3 kW it did not make sense to go to the expense of a heat pump and heating system for such a small load. Secondly, Bill Leahy was not happy with the potential CO2 savings with such a heat pump. For example, if the heat pump achieved a seasonal coefficient of performance of as much as 4 and with electricity delivered by the ESB at a primary efficiency of 30% then this meant that the CO2 emissions were only reduced by approximately 20% - this was not what he had envisaged as being the best result. NuTech Consultants pointed out to Bill Leahy that heat pumps do have a role to play in certain circumstances but not particularly in this case.
In short, Bill Leahy saw that with this package he would be supplying houses to his clients that would offer the following major benefits:
- Very low running costs for space and water heating by way of the house construction and the fully integrated air solar heating, ventilation and hot water system.
- Houses that are ‘future proofed’ against fluctuating oil prices and indeed the supply of fossil fuels.
- High levels of comfort in terms of the average house temperature and humidity in autumn, winter and spring.
- An increase in the level of comfort by way of fresh filtered air and a consequent reduction in the risks from dust, pollen, and so on.
- A degree of cooling in summer during both the day and night by way of the fresh air intake.
Finally, the project was put forward to Sustainable Energy Ireland for funding under House of Tomorrow.
Support under House of Tomorrow
The House of Tomorrow Programme administered by Sustainable Energy Ireland (SEI) grant aids projects whose main aim is to save energy. Basically, energy savings of at least 40% are required over the base case house to qualify and the houses must be built to incorporate certain minimum standards of insulation. The base case house is defined as the house being built that would just satisfy the requirements of Part L of the 2002 Building Regulations when considered under the Overall Heat Loss Method or the Heat Energy Rating Method. This means it could have U-values as poor as the following:Ground Floor < or = 0.37 W/m2.K
External Walls < or = 0.37 W/m2.K
Roofs < or = 0.25 W/m2.K
Windows < or = 2.20 W/m2.K
To comply with the rules of House of Tomorrow the U-values for the various elements must be as good as or better than the following:
Ground Floor < or = 0.20 W/m2.K
External Walls < or = 0.27 W/m2.K
Roofs < or = 0.16 W/m2.K
Windows < or = 1.90 W/m2.K
The elements of the fabric of the houses at Killeagh have been built to satisfy and in some cases are better than the U-values demanded by SEI. NuTech Consultants examined the houses using their hour-by-hour energy analysis computer model. This model takes account of the following:
- The U-values of the elements of the house
- The level of airtightness of the house
- The use of heat recovery ventilation
- The use of various areas of air solar collectors to reduce the energy demand for heating ventilation and hot water
- The amount of hot water used per day
- The level of occupancy in the house
- The utilisation of passive solar gains and energy attributable by way of gains from occupants
- Energy supplied by the boiler with an applied efficiency
Using this model NuTech Consultants demonstrated that houses being constructed by Leahy Bothers would have a gross saving in energy for space and water heating amounting to 75% when compared to the base case house.
This meant that the maximum grant aid of €8,000 per house was awarded for the first 50 houses in this scheme. Results from this project will be fed through to SEI over the next few years. The main items of interest are the actual running costs in terms of the number of kilograms of wood pellets used per year and the level of airtightness achieved by way of the construction methods used.
The House of Tomorrow programme is a most welcome development in encouraging builders to build low energy/low CO2 houses. It allows builders to become familiar with the principles involved in designing low energy houses and helps them to see the benefits not just for themselves but also for their customers. Under the requirements of the Energy Performance of Buildings Directive all houses will soon be energy rated and certified. This will allow the prospective homeowner to assess how energy efficient their new home is. Most builders will want to deliver an A-rated house to their clients in the same way as a company such as Siemens deliver an A-rated fridge to their customers – Siemens do not manufacture any C-rated fridges.
The technologies being used
The basic concept is as described previously. The technologies used are as follows:
- The Kingspan Century special package of pre-fitted insulation that has been shown be effective in terms of its calculated U-value is the same as its U-value in practice.
- This special package has factory fitted air tightening seals which ensures that the house can achieve an air infiltration rate of less than 0.1 Air Changes per Hour.
- The NuTech Consultants designed air solar heating and hot water system with an integrated Heat Recovery Ventilation module. A 3-panel Sunwarm air solar heating system is used here linked to the unique 140 Air Handling Unit designed by NuTech Consultants. A Mitsubishi Lossnay Heat Recovery Ventilation unit is integrated into the system and is controlled by the Sunwarm controller.
- A Wodtke wood pellet boiler is used as the backup energy supply system.
This overall system is the heating system of the house—the ventilation system is oversized in order to be the heating system of the house also. However, in the first fifty houses a radiator heating system is being installed on the ground floor. The bedrooms are heated by way of the Sunwarm system.
The controls for the system are simple in that the Sunwarm system is thermostatically controlled and will control whether warm air is delivered to the house or not. On a warm sunny day in summer, cool ventilation air will be delivered to the house while the solar panels will deliver energy to the domestic hot water cylinder. On a sunny day in winter, energy from the solar panels will be used to provide both heat to the domestic hot water cylinder and heat to the house by way of the ducted air system. The system is completely automatic and all the householder has to do is set the thermostat to the house temperature required. The boiler is also automatic and will be enabled to fire by way of the boiler timer and the required temperatures in the house and hot water cylinder.
Construction of the houses
The construction of the houses has gone very smoothly. The onsite management team of Oliver Leahy and Alan Harty has resulted in some impressive targets being met.
It was found that the Kingspan Century / Leahy Brothers team could deliver and erect six houses per week quite easily. It should be remembered that these timber frame houses come pre-insulated and with the airtightening seals pre-fitted – this speeds up the building process enormously. With levels of airtightness of 0.1 Air Changes per Hour being achieved in practice, this is indeed a remarkable level of progress in low energy house building in Ireland. It has to be said that the level of site supervision by the Leahy Brothers’ team and the attention to detail by their sub-contractors has paid handsome dividends.
The roofing sub-contractors employed by Leahy Brothers have installed the Sunwarm air solar collectors. Similarly, the Sunwarm air handling unit, together with the Mitsubishi Lossnay HRV unit and all of the ducting and controls have been installed by both the plumbing and electrical sub-contractors to Leahy Brothers. This utilisation of the normal on-site trades has been a huge benefit to the efficient building of the houses. NuTech Consultants trained these personnel in the fitting of the various systems which on completion will be commissioned by NuTech.
In conclusion
This project has gone extremely well because of the ‘build speed’ of this special timber frame construction from Kingspan Century with factory fitted insulation and airtightening seals.
The utilisation of the existing site trades also added to the efficiency. The determination of the builder, the suppliers, designers and the site team to build the house as designed such that it will perform in practice has been a key element of this project.
In order to ensure this teamwork Leahy Brothers with Kingspan Century and NuTech Consultants organised a conference in the Midleton Park Hotel to explain to all concerned what technologies were involved and how each sector was interdependent with the other. This conference was attended by all concerned with the project – the design team, the build team, all of the sub-contractor trades involved, the mechanical services team and very importantly the auctioneers involved in selling the houses. It was also attended by personnel from the Department of the Environment and from HomeBond.
It was felt that, with the attractive design of the houses and the careful integration of the technologies involved, these houses offer the buying public a wonderful opportunity to own a house that is ‘Future Proof’ branded by Kingspan Century against the energy supply and price fluctuation situation.
Proof positive of the success of the approach taken by Leahy Brothers is the fact that all of the houses in this House of Tomorrow Project have been sold. Bill Leahy offered houses with the option that they could choose either the ‘low energy/low CO2’ package as described above or a standard oil-fired heating system. All of the clients opted for the low energy house with the wood pellet boiler as backup. As Bill Leahy says …..’I did have to explain to all of our clients how all of the systems worked and the technologies being used in the houses. It took a lot of talking but, with the high oil prices and concerns over supplies, all of them were most pleased to find we were offering such a well-developed solution being supplied by large reliable companies such as Kingspan Century, NuAire Ltd and Mitsubishi Electric Ireland. Once they saw the benefits they all went for the low energy package on offer’.
- Killeagh
- Bill Quigley
- Nutech
- Kingspan
- Ventilation
- solar panels
- heat recovery
- airtightness
- wood pellet
- boiler
Related items
-
Why airtightness, moisture and ventilation matter for passive house
-
Airtight delight
-
Solar panels to receive VAT drop in aim to boost uptake
-
Partel’s airtight membranes now certified for passive house construction
-
ProAir pioneers with EPDs for ventilation systems
-
Mass timber masterwork
-
Partel obtains EPDs for airtight membranes
-
Let’s bring ventilation in from the cold
-
45,000 more Irish homes face radon risk, new maps reveal
-
ProAir retooling for the future
-
Manhattan modular apartments feature Wraptite membrane
-
Ecological launch Inventer decentralised ventilation