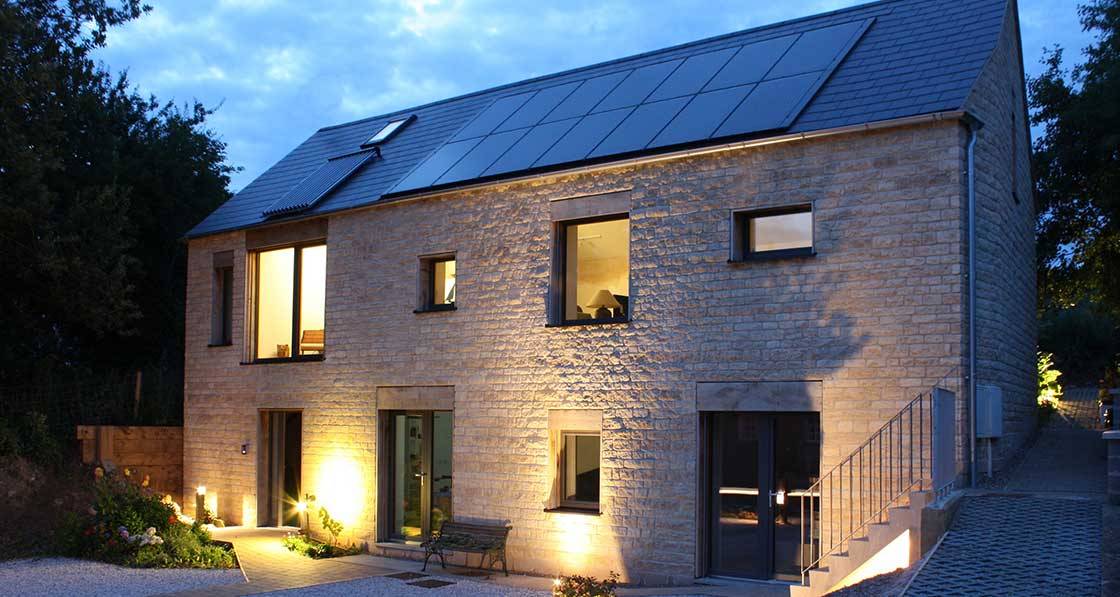

- New build
- Posted
Slope and glory
When architect Tony Godwin wandered into a seminar on the passive house standard at Ecobuild ten years ago, it was the start of a journey that would eventually see him design and build his own passive home on a sloping site — and learn some hard lessons along the way to achieving a comfortable, ultra-low energy family home with tiny energy bills.
Click here for project specs and suppliers
Building type: 221 sqm detached two-storey timber frame house
Location: Whitwell, Oakham, Rutland, UK
Budget: £508,000
Standard: Certified passive house
£250 per year (all heating & electricity minus renewable energy income)
Relocating from London to Rutland, my wife Marlen and I quickly realised that all the properties on offer would require either considerable compromise on our aspirations for a low energy sustainable lifestyle, or else radical alteration, adding considerable cost to the initial purchase price. So arose my wife’s suggestion that we self-build.
Foreseeing a sentence of several years hard labour, I suggested sites would be difficult to come by. Undeterred, her internet search found four sites within four miles of our son’s school, and so the fuse was lit.
Our brief was for a home with a minimum of three bedrooms for the family, an additional bedroom and bathroom to host parents or guests separate from the family accommodation, and a working space (as we both work from home).
We wanted contemporary spaces that would be inspiring to inhabit, and we wanted to aim for the highest standards of energy efficiency and sustainability practical.
This article was originally published in issue 25 of Passive House Plus magazine. Want immediate access to all back issues and exclusive extra content? Click here to subscribe for as little as €10, or click here to receive the next issue free of charge
I first encountered the passive house concept at Ecobuild 2008, attending a seminar with bere:architects. I arrived late as passive house expert Sarah Lewis took attendees through a lot of data sheets – and I left after 10 minutes thinking ‘this is too difficult’!
We purchased our site in December 2009 and planning permission was granted the following May. The passive house option was kept on the table, and a brief email exchange with the BRE indicated that the standard was achievable for our design. Later in 2010, a visit to Bere Architects’ Ranulf Road passive house, followed by a seminar with Professor Helmut Krapmeier, persuaded me to make the passive house standard the core requirement for our new house.
Disappointment followed as the first calculations in the passive house design software PHPP predicted a heating demand of 22 kWh/m2/year — well outside the passive house standard of 15 — because the proposed T-shape with single-storey projections resulted in a poor form factor. There was also a large proportion of glazing to the northerly aspect. These factors were compounded by the East Midlands climate zone, which has one of the longest heating seasons in the UK.
So our passive house advisors WARM suggested reconfiguring the house — essentially swapping the single-storey studio in front of the house for the garage. The redesign featured improved U-values with fabric thicknesses of up to 600mm, and required a new planning permission.
While it was still mid-recession and funds were locked up in our unsold London house, the revised scheme was approved and the lesson that passive house principles have to be integrated with the design process from the beginning was learnt — the hard way.
Building fabric
With the lower floor of the house built into the slope of the site, the external envelope had to have detailing for both above and below ground conditions, maintaining continuity of waterproofing, insulation and airtightness over a variety of external finishes while allowing for differential movement.
The wall solution comprises a 300mm double-stud structural timber frame filled with Warmcel set on the ground bearing concrete slab, and in front of a reinforced concrete retaining wall. Detailing was a challenge for both architect and, in implementation, the builder. With the exception of the epic ‘Details for Passive Houses’ book written by the Austrian Institute for Healthy and Ecological Building, published information in English was scarce, and I relied heavily on advice from pioneers in the UK passive house sector.
The build-up of the ground floor meanwhile, with the power-floated concrete slab sitting over EPS insulation, is designed to expose the slab internally and provide thermal mass that buffers against temperature fluctuations outside.
Sustainable development
The site – which is three-quarters of an acre, orientated north-west to south-east – slopes seven metres to the main road, and was blighted by previous development attempts.
The upper 70% of the site is zoned as ‘significant open space’ in the village and was not open for development. Excavated material from the foundations was spread over this paddock area, rather than removing it from site – also a cost saving. From the outset we consulted with the village community via the parish clerk, which in a conservation area undoubtedly assisted with our planning application.
A 1,500 litre tank under the front drive collects all the rainwater from the roofs, and from there the water is pumped up to a larger storage tank at the top of the site which gravity feeds four garden taps. As far as possible we used local contractors and suppliers based within a 30 mile radius of the site, supporting the local economy and reducing site travel miles. We also have a solar thermal panel and a 3.5kW solar photovoltaic installation.
-
The view south-west over the three-quarters of an acre site, which slopes seven metres to the main road The view south-west over the three-quarters of an acre site, which slopes seven metres to the main road
-
The floor build-up features 200mm EPS insulation, increasing to 350mm under the reinforced concrete slab The floor build-up features 200mm EPS insulation, increasing to 350mm under the reinforced concrete slab
-
The retaining walls are tanked with Visqueen self-adhesive tanking membrane, insulated externally with 100mm of expanded polystyrene, and protected with Visqueen Protect and Drain membrane. The retaining walls are tanked with Visqueen self-adhesive tanking membrane, insulated externally with 100mm of expanded polystyrene, and protected with Visqueen Protect and Drain membrane.
https://passivehouseplus.ie/magazine/new-build/slope-and-glory#sigProId21c3abd07e
Construction, procurement and cost
Of the project team of consultants, constructors and suppliers, I had only worked with the structural engineer previously. All were new to passive house except WARM and Green Building Store. As I expected, the contractor insisted that we use a quantity surveyor for valuations to avoid conflict of interest, and our QS became the contract administrator (we used a standard JCT contract with quantities), leaving me free to concentrate on site supervision and supply of information – and with hindsight, it was well worth the fees we paid.
I avoided nominating subcontractors so that the main contractor would remain responsible for all aspects of the project except for unfamiliar items critical to the passive house standard. We only sourced imported items though UK distributors who we assessed could provide reliable support during design and construction.
Prices obtained for the timber frame during the design stage revealed an apparent premium for systems developed for super-insulation and airtightness, and as timber frame is such a well-established building method, I reckoned we could get a better price by going through the main contractor. This proved to be a false economy, as it locked us into a manufacturer who would not modify their system, which was only designed to meet UK building regulations, and this ended up creating airtightness detailing difficulties.
In hindsight, if we had chosen the timber frame supplier in advance, it would have allowed us to prepare the design of the frame before appointing the main contractor, thus avoiding the delays that resulted.
Procuring the triple glazed windows from the manufacturer Katzbeck in Austria was a lengthy process due to indirect communication through the UK installation representative.
In future, I would always make time to visit the manufacturer. Note that tilt or lift-and-slide windows are difficult to make totally airtight due to the mechanisms involved. We now have two in our living area, and it is noticeably cooler here on really windy winter days.
Fortunately the contractor’s site agent, as well as being a skilled builder, remained open-minded and collaborative on the unfamiliar territory of a passive house build. But only previous experience could have prepared us for the level of airtightness detailing required. We air-tested on completion of the airtight layer, and – mistakenly measuring the internal volume according to the UK building regulations – thought we had passed the passive house target. We then carried out three further tests, with many hours spent finding and rectifying leaks before finally achieving the required value of 0.6 air changes per hour.
Another lesson we learned is that proposed substitution of specified insulation material must be reported and agreed.
In our case, the mineral wool in the roof was built up in layers of different thicknesses with different lambda values and the contractor varied these, resulting in a loss of U-value.
For the sake of certainty, I selected a passive house certified Paul MVHR system, designed and supplied by the Green Building Store, and would still look no further if I was choosing one again.
-
The view south-west over the three-quarters of an acre site, which slopes seven metres to the main road The view south-west over the three-quarters of an acre site, which slopes seven metres to the main road
-
The floor build-up features 200mm EPS insulation, increasing to 350mm under the reinforced concrete slab The floor build-up features 200mm EPS insulation, increasing to 350mm under the reinforced concrete slab
-
The retaining walls are tanked with Visqueen self-adhesive tanking membrane, insulated externally with 100mm of expanded polystyrene, and protected with Visqueen Protect and Drain membrane. The retaining walls are tanked with Visqueen self-adhesive tanking membrane, insulated externally with 100mm of expanded polystyrene, and protected with Visqueen Protect and Drain membrane.
-
The retaining walls are tanked with Visqueen self-adhesive tanking membrane, insulated externally with 100mm of expanded polystyrene, and protected with Visqueen Protect and Drain membrane. The retaining walls are tanked with Visqueen self-adhesive tanking membrane, insulated externally with 100mm of expanded polystyrene, and protected with Visqueen Protect and Drain membrane.
-
The retaining walls are tanked with Visqueen self-adhesive tanking membrane, insulated externally with 100mm of expanded polystyrene, and protected with Visqueen Protect and Drain membrane. The retaining walls are tanked with Visqueen self-adhesive tanking membrane, insulated externally with 100mm of expanded polystyrene, and protected with Visqueen Protect and Drain membrane.
https://passivehouseplus.ie/magazine/new-build/slope-and-glory#sigProIde64f42541b
Real-world performance
A teenager in a small room with an Xbox doesn’t need further heating either.
There is no doubt that designing and constructing to the passive house standard requires a cultural shift from normal UK industry practice. The process is unforgivingly rigorous, and allows none of the ‘ducking and weaving’ possible under Part L. ‘There or thereabouts’ certainly will not do. If your building does not perform as modelled, look for deficiencies in the design and construction — not PHPP.
That the topic of ‘summer overheating’ was a favourite on the seminar circuit last year indicates that architects have perhaps been taking design licence from the PHPP criteria that internal temperatures must not exceed 25C for more than 10% of the year, and that this could be tightened up. In our case, with quite large south-west facing windows, I built external aluminium horizontal louvre electric blinds into the façade, which are controlled by a simple sunlight sensor. With these deployed the maximum summer temperature we’ve recorded in the living area is 26C, and then only for a few days (PHPP gave our frequency of overheating as just 0.3%, or about one day).
If your design, as mine does, has a poor form factor (and if you want a vaulted ceiling!) you will have to achieve better U-values. That our master bedroom and guest bedroom — at opposite ends of the L-shape plan with a higher proportion of external envelope — are cooler than the rest of the house is perhaps logical but nonetheless wasn’t expected (even temperatures being promoted as a benefit of living in a passive house). However the differential is never more than 2C.
In comparison our studio is heated nicely by us and our office equipment during the day, and a teenager in a small room with an Xbox doesn’t need further heating either.
We have a traditional gas-based central heating system with three heated towel rails and three radiators, all thermostatically controlled, and we have a frost protection heater battery on the ventilation system.
Temperature readings taken indicate that heat is only required when the external temperature falls to 7C or below, and we’ve found it is better to set the boiler programmer to ‘on’ all the time, and let the remote digital thermostat call for heat and fire up the boiler when required. The thermostat is left in the living area at 21C and moved to the master bedroom (which has a radiator) at night and set at 19C.
Overall, this is more efficient than setting the boiler to turn on and off during the day, because if we switch the boiler off it takes ages to bring the temperature up again, even though we are only dealing with a drop of 1 or 2C.
However, this heating provision has struggled to keep up with sudden changes of temperature this winter, and in the very cold weather front from Russia earlier this year, it took a day to shift the temperature in the living area from 19.5C to 20.5C. This was not helped by the north-east wind finding the unsealed end of our four-metre wide lift and slide window. It should be noted that the stated occupancy of the house for PHPP was six, but is now normally two (meaning there are less internal heat gains from the body warmth of occupants than designed for).
Our energy bill averages £900 or £4 per square metre, and is offset by earnings from renewables, leaving us with a net annual energy bill of £250. What’s more, our energy usage now is well within that predicted by PHPP.
In my opinion, if there is one disadvantage with living in a passive house, I think it is that as an occupant one’s body comes to expect the high standard of thermal comfort the standard delivers — and becomes physiologically less tolerant of lesser environments, especially draughty ones.
But as one of our visitors exclaimed during an International Passive House Open Day: “why would anyone not want to build a passive house?”
Selected project details
Clients: Tony and Marlen Godwin
Architect: FCD Architecture
Passive house designer: WARM Low Energy Building Practice
Quantity surveyor: ADM Surveyors Limited
M&E design: EDP Consulting limited
Main contractor: DW Hicks Building Co Ltd
Timber frame: Harlow Ltd (design, manufacture, erection)
MVHR: Paul, supplied by Green Building Store
Ventilation system installation: Dave Manby
Cellulose insulation: Warmcel
Glass & mineral wool insulation: Knauf & Rockwool
Windows & doors: Katzbeck, supplied by JLH
Roof window: Fakro
Airtightness products: pro clima supplied by Green Building Store
Solar evacuated tubes: Worcester Bosch via Envirogen Ltd
Solar photovoltaic panels: Solarworld via Envirogen Ltd
Rainwater harvesting: Rainwater Harvesting Ltd
In detail
Building type: 221 sqm detached two-storey timber frame house with semi-basement.
Completion date: April, 2015
Budget: £508,163
Passive house certification: Certified
Space heating demand (PHPP): 15 kWh/m2/yr
Heat load (PHPP): 9 W/m2
Primary energy demand (PHPP):79 kWh/m2/yr
Heat loss form factor (PHPP): 3.38
Overheating (PHPP): 0.3%
Environmental assessment method: Nil
Airtightness (at 50 Pascals): 0.6 ACH @ 50 Pa
Energy performance certificate (EPC): A93
Measured energy consumption: Measured average annual gas consumption of 4,587.44 kWh and electricity consumption of 6,964.33 kWh (total of 11,551.77 kWh or 55 kWh/m2/yr. Adding back estimated contribution from solar thermal (estimated as per MCS methodologies) and solar PV (50% of generation as per SAP 2009) of 3,084 kWh/yr combined gives a total energy consumption of 14,636kWh (or 66kWh/ m2/yr) compared to PHPP design figure of 17,476kWh (or 79 kWh/m2/yr).
Thermal bridging: Thermal bridges were designed out by careful detailing with the assistance of the passive house designer. The edges of the raft floor slab are wrapped with a minimum of 200mm EPS insulation; the junction of slab and retaining wall was wrapped with an additional 100mm of EPS (total 300mm); retaining walls extending beyond the building were disconnected from the main structure and masonry built off the top of the retaining wall was isolated using Marmox blocks. There is no steel in the superstructure although there was a concern about the extent of gang nails plates used in the truss forming the main vault. The mass was calculated and the effect was negligible. The windows frames are solid Spruce and lapped with insulation externally. Y-value: 0.003 W/(m2K)
Energy bills (measured or estimated): Average annual gas bill (heating and hot water) of £267.85 and electricity bill of £633.49 (averaged over three years) = total average annual energy bill of £946.73. Average annual feed-in-tariff (for solar PV £429.69) and renewable heat incentive (for solar thermal) of £220.26. Subtracting these figures from £946.73 yields a net average annual energy bill of £251.39 or £21 per month.
Ground floor: 150mm compacted base followed above by 50mm quarry stone fines as blinding, DPM / radon barrier, 200mm EPS in 2 x 100mm layers (increasing to 350mm under the slab), 150mm reinforced concrete slab with 300mm deep x 600mm perimeter beam and 300mm x 1200mm structural ‘toe’ reinforced up into the retaining walls. Slab is power floated with a dry shake surface hardener topping. U-value: 0.148 W/m2K WALLS
The house is cut into a sloping site. The structure comprises a double stud timber frame bearing on a concrete slab located in front of reinforced concrete retaining walls made structurally integral with the slab. Timber frame is clad externally with three different finishes. Main front elevation (from inside to out): 12.5mm plasterboard, 37mm battened service void, 12.5mm P5 Durellis vapourblock (airtight) OSB board, 63mm non-loadbearing stud + 97mm void + 140mm loadbearing stud forming a 300m void filled with Warmcell recycled newsprint insulation, 12.5mm P5 Durellis OSB board, 100m mineral wool insulation, 50mm airgap, 110mm local Clipsham limestone. U-value: 0.099 W/m2K
Rear elevation: Timber frame structure as above but clad with 150mm mineral wool insulation between cross battening, moisture barrier membrane and Rockpanel boards in shiplap arrangement. The wall to the boundary is similar, with thin-coat through-colour render on 10mm cement board. U-value: 0.088 W/m2K The retaining walls are tanked with Visqueen self-adhesive tanking membrane insulated externally with 100mm of expanded polystyrene protected with Visqueen Protect and Drain membrane. U-value: 0.087 W/m2K
ROOF
The main roof structure is a vaulted truss fully insulated. The build-up from inside to out is: 12.5mm plasterboard, 37mm service void, 12.5mm P5 Durellis OSB board, 550mm glass mineral wool, 60mm Rockwool Hardrock Multifix (DD) board, counterbattens + breathing moisture proof membrane + battens (70mm), plain fibre cement slates. The wing to the rear has a similar attic truss with a void over the insulation. The build-up is similar but with 40mm counterbattens (providing a ventilation airgap), 12.5mm plywood, geotextile membrane and standing seam aluminium roofing. U-value: 0.074 W/m2K
Windows & doors: Linea by Katzbeck windows sealed with pro clima tapes. Frame: Spruce wood-powder coated aluminium with Uf-value of 1.1 W/m2K. Glazing: Interpane iplus E, 90% argon filling, Ug-value of 0,5 W/m2K, g-value of 5%.Turn & tilt window overall U-value: 0.78 W/ m2K. Fixed window overall U-value: 0.72 W/m2K. Front door overall U-value: 1.2 W/m2K
Roof windows: 2 x Fakro FTT U8 Thermo passive house-certified quadruple glazed roof windows. Whole window U-value: 0.58W/m²K Heating: Worcester Bosch gas boiler 12i 24Kw ‘wet’ distribution to 3 Uniline panel radiators and 3 MHS heated towel rails. Gas boiler also serving Worcester Bosch 210L hot water cylinder with dual coil indirect heating. Worcester Bosch Solar-Lux 12 (12 evacuated tube) solar thermal system also serving same hot water cylinder via indirect heating coil. Estimated annual output of 1,112 kWh.
Electricity: 3.5kWp solar photovoltaic array with 14 Solar World mono crystalline panels in-roof mounted. SMA inverter: Sunnboy 3000HF. Estimated annual output using SAP of 3,363 kWh. Ventilation: Paul Novus 500 mechanical ventilation heat recovery system with frost protection.
Water: All rainwater is collected for garden irrigation in a 1,500L tank with an automatic pressure switched pump. A 5,000L tank located at the top of the site is fed from the lower tank. Water is then distributed by gravity to locations in the garden and paddock as required.
Sunshading: Hunter Douglas aluminium horizontal motorised venetian blinds controlled by manual switch or sun or temperature movable sensors stuck to the glazing located according to user preference.
Green materials: The overriding criteria in the selection of insulation materials was to avoid the use of those based on petro-chemicals. Thus Warmcel recycled newsprint was used on the walls and mineral or glass wool elsewhere. Petrochemicals could not be avoided below ground and EPS was specified as it has a more environmentally friendly manufacturing process. The timber frame superstructure was chosen to avoid steel or masonry.
Image gallery
-
Concrete profiles Concrete profiles
-
Details 1 Details 1
-
Extention works rear Extention works rear
-
FIrst floor plan FIrst floor plan
-
Ground floor layout plan Ground floor layout plan
-
Key plans Key plans
-
Roof Roof
-
Section elevation 2 Section elevation 2
-
Section elevation Section elevation
-
Site plan south Site plan south
https://passivehouseplus.ie/magazine/new-build/slope-and-glory#sigProIdcfcef0f546