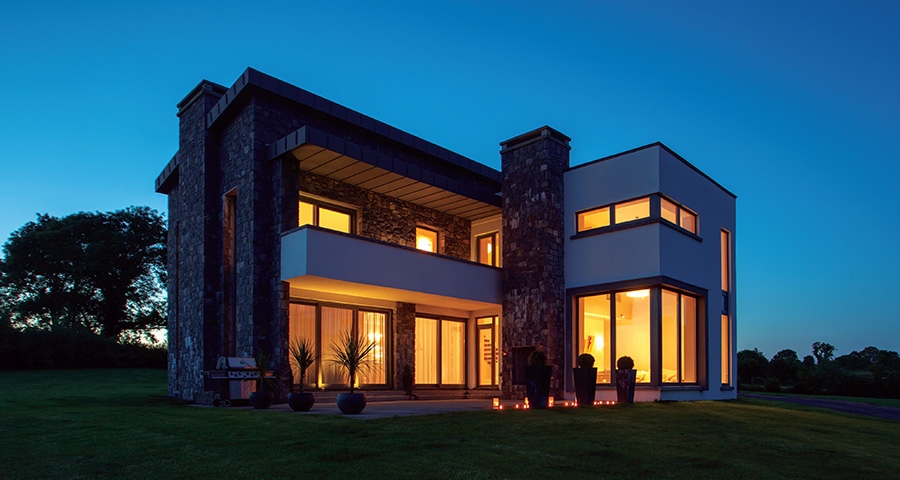
- New build
- Posted
Modern Galway home delivers ultra low energy bills
When work began on this low energy, super airtight project in Co Galway it faced a tight budget and a market for passive house products that had yet to mature. But in the end its owner Hugh Whiriskey emerged with a comfortable home with stunningly low annual heating and hot water costs of just over a euro per square meter.
Hugh Whiriskey was planning for his Co Galway low energy build long before he began designing the house. First, he planted willow trees to meet his future fuel needs on an acre and a half behind the house.
“The theory is, we’ll supply our own timber from it,” he explains. “I tried to work out how much we’d need at the time and planted accordingly. It’s three years down, so in a year and a half, we’ll be cutting one third, and then replanting.”
Heated by a combination of a geothermal heat pump and room-sealed stoves, Whiriskey also made provision for PV panels on the roof, which he expects to install down the line. Right now, with a full year’s heating and hot water costing just €375, the additional capital cost is difficult to justify.
Whiriskey works with architects and consulting engineers Corbwell Design in Galway and drew heavily on the company’s expertise when designing and building his own house. “The principal behind the company is to give a full service from planning through to construction, tender if necessary, project management and sign off, and we have a very strong emphasis on passive house principles.” Whiriskey also runs the low energy building product company Partel.
Financial considerations lay behind the decision to go with masonry build. At the time, the meltdown in construction had seen the price of block laying decline sufficiently to make it that bit more cost effective than timber frame. An engineer by profession, Whiriskey went with a wide 250mm cavity pumped with EPS platinum bead. High ceilings and an open plan design also prompted the decision to lay blocks on the flat, giving a 215mm concrete wall. “So you’re automatically getting a very high thermal mass,” he explains. “The house retains its own heat at a very comfortable temperature.”
Though the building wasn’t designed as a passive house, careful attention to airtightness using Partel’s range of tapes and membranes, with particular attention paid to key junctions such as windows, chased walls and a counterbattened service void in ceilings, leading to an impressive pressure test result of 0.48 ACH.
He found however that the detailing required to ensure airtightness and design away thermal bridges was a lot trickier than it would have been with a timber frame. Luckily, local contractor Niall Dolan of GreenTec Ecological Homes is a specialist in these areas. A veteran of several wide cavity builds, he supervised the project and worked through each airtightness and thermal detail to ensure a passive-standard building envelope. “Niall is brilliant on the details,” says Whiriskey, “he makes that side of things quite easy.”
Quinn Lite blocks were deployed at both foundation and wall plate level to deliver the necessary thermal break, while Teplo-Tie wall-ties in the cavity did the same job there. Ply boxes were used behind the windows to close the cavities, but it was detailing the balcony that took the most thought and energy.
“We were adamant we wanted to keep it cantilevered, unsupported on the far corner,” Whiriskey explains. “Structurally that makes things difficult, and then you’ve got to factor in the thermal bridging as well, so between those two, it consumed a bit of time.”
Concrete upper floors are typically hollowcore; precast slabs are craned into place on top of blockwork, but because Whiriskey wanted an open plan layout downstairs, that approach would have involved large amounts of structural steel in the slabs, which in turn would have had a major impact on cost. Because he also wanted the first floor balcony to extend unsupported over the patio area outside, that too would have required large amounts of steel. This was a non-runner not alone from a cost point of view, but also because thermally breaking the structure would have been almost impossible.
The solution was to pour the upper floor in situ, and thermally break the cantilevered balcony using a specialised Schöck Isokorb balcony connector - available in Ireland via Contech Accessories - embedded in the concrete. This, says Niall Dolan, was unquestionably the most difficult element of the build. “The airtightness here wasn’t too bad,” he says, “but the balcony and the cold bridging for the poured slab, that really was the trickiest thing.”
Airtightness comes primarily from the internal wet plaster finish, together with Partel’s suite of tapes and membranes. “We plastered down to the slabs and put a little bevel on the plaster to seal it,” says Niall Dolan, “we didn’t need to use any tape at the bottom.”
At the time Whiriskey was selecting a window and door package, the choice of passive components was limited. While triple-glazed windows were installed on other elevations, he opted to install a high performing double-glazed window on the south facing living areas. “On the pure energy side of things, you get a better thermal gain from double-glazing on south facing windows, so there was an energy balance to be made there.” These double height windows are non-opening, and don’t feature any additional mullions, features which give them a much better thermal profile.
The problem with working in the trade is that new products are always coming on stream, so you get a ringside seat for all the components and technologies you would have installed, if you were doing the job today.
“Today, you wouldn’t question [using] the passive house standard windows and doors throughout,” says Whiriskey, “but at the time, we did what we could within budgeting constraints. It’s always a balancing act.” The Whiriskey family have been in the house now for a year, and so far, so good. “We’re very happy with the build, very happy with the appearance, very happy with how the house is performing. On the whole, I’d say we’re pretty fortunate with how it’s worked out.”
Selected project details
Client: Hugh Whiriskey
Project management, M&E and civil engineering:
Corbwell Design
Contractor: GreenTec Ecological Homes
Mechanical contractor: EIL
Windows and doors: True Windows
Cellulose insulation: Ecocel
Wood fibre insulation: Partel
Floor insulation: Kingspan
Cavity wall insulation: Eurobead
Airtightness products & wall ties: Partel
Thermally broken balcony connector: Schöck
Thermal blocks: Thermal Insulation Distributors Ltd
Heat pump: Unipipe
Heat recovery ventilation: Dimplex Renewables
GGBS: Ecocem
Floor screed: Egan Screeding
Additional info
Building type: 350 sqm detached two- storey wide cavity masonry build
Location: County Galway
Completion date: June 2013
Passive house certification: N/A
Space heating demand (PHPP): 36 kWh/m2/yr
Heat load (PHPP): 16 W/m2
Primary energy demand (PHPP): 85 kWh/m2/yr
Airtightness: 0.48 ACH at 50 Pascals.
Provisional BER: A2 (46.68 kWh/m2/yr)
Energy bills: Annual running cost for heat and hot water projected at €375
Thermal bridging: Quinn Lite aircrete blocks used at foundation and wallplate; Teplo-Tie wall ties; Foamglas Perinsul under steel supports; Schöck Isokorb balcony connector
used for cantilevered balcony.
Ground floor: Raft foundation insulated with 140mm Kingspan Thermafloor PIR insulation and 50mm perimeter Kingspan Thermafloor PIR insulation. U-value: 0.12
Walls: Sand and cement render on concrete block external leaf with 250mm cavity full filled with EPS platinum bead insulation. Concrete block inner leaf complete with airtight plaster. U-value: 0.12
Roof: Trocal & zinc on two staggered layers of OSB on battens for air flow, on Partel Protecta plus membrane, on 225mm rafters with high density Ecocel cellulose insulation and Partel Variable airtight Resano membrane. Service cavity with 50mm Schneider woodfibre insulation. U-value: 0.13
Windows: triple and double-glazed timberaluclad Bug windows with U-values of 0.92 & 1.20 respectively
Heating system: Nibe 1245 ground source heat pump with underfloor heating. Thermostats in all rooms.
Ventilation: Xcel 400QVI mechanical ventilation with heat recovery. 91% efficient with summer bypass.
Electricity: planned 12 m2 solar photovoltaic array with average annual output of 2kW
Green materials: Schneider wood fibre Insulation, cellulose Insulation, Ecocem low carbon cement used in floors, sustainably sourced native timber used throughout.
Image gallery