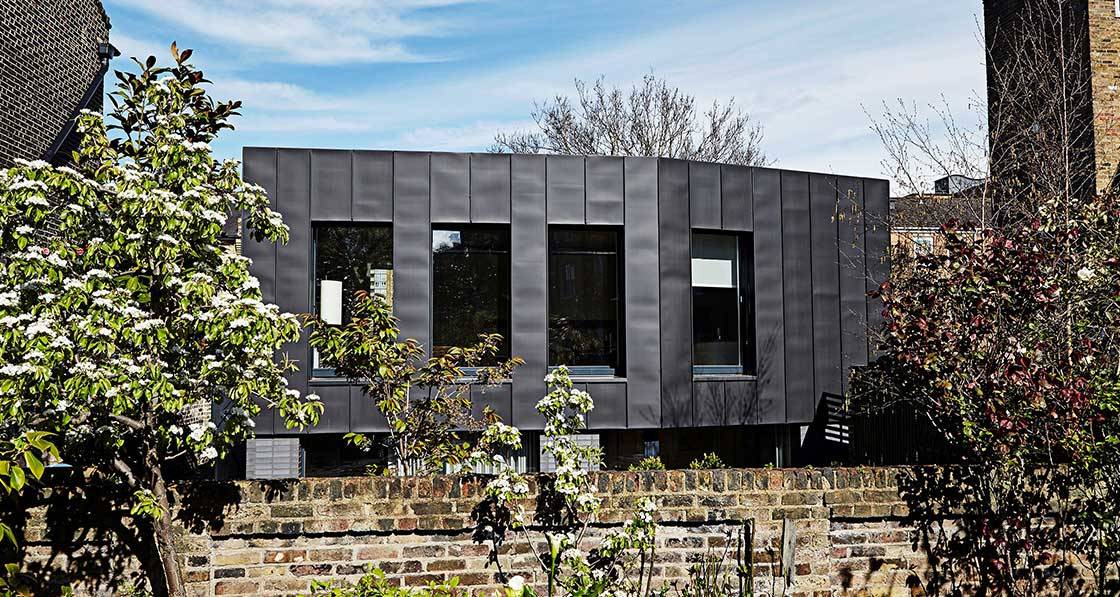
- New build
- Posted
Compact solid-timber passive house on London infill site
Built from a simple palette of timber and concrete, this diminutive but architecturally unique home managed to meet the passive house standard despite a small and awkward site.
Click here for project specs and suppliers
This article was originally published in issue 16 of Passive House Plus magazine. Want immediate access to all back issues and exclusive extra content? Click here to subscribe for as little as €10, or click here to receive the next issue free of charge
Building a new home in the tight confines of someone’s backyard brings its own set of challenges but, given the value of property in London, it’s a popular type of development and architects with skin in the ‘urban infill’ game have all sorts of tricks up their sleeve to make the most of the available light and space.
When Bernard Tulkens of East London-based Tectonics Architects, which specialises in residential projects, decided to design and construct a new dwelling in the back garden of his home in Hackney, he also elected to build to the passive house standard. The result is a highly discrete 94 square metre two-storey detached house set half a level down from the street (as per local planning rules), with the lower level built in reinforced concrete, and a prefabricated upper level structure made from cross-laminated timber (CLT). A small gate opens onto a paved area, where there is a view of the garden, and a few steps leading down to the front door on the ground floor.
Inside, the bedrooms are on the lower ground floor and the upper level has an open plan living space with kitchen. It’s bright and airy — the first impression is that it aims to be minimalist, but that wasn’t Bernard’s intention. “I like simple use of materials, and in this case it was possible and relevant to keep the construction visible [via the exposed timber and concrete inside]. It does not feel minimalist as the materials are very much present, with concrete at lower ground floor and timber above.
“I was interested in creating a nice space with a limited palette of materials. In terms of space I wanted to create a house that is flexible, with an open plan upper ground, a kind of ‘piano nobile’. I also thought it was a chance, as an owner and architect, for me to have a clear and measurable energy and sustainability standard.” He was particularly keen to use CLT and natural insulation in the form of wood fibre.
Designing a passive house in such a location shouldn’t, in theory, be a big issue. But the site, which had been extended by the previous owner to include two plots that linked it to the street behind his own home, had the distinct problem of being strongly overshadowed by a terrace of tall Victorian houses.
Indeed, one passive house designer Bernard spoke to early on indicated it would be a tough site to meet the passive house standard on. But while acknowledging the challenges posed by the site, it clearly didn’t phase the designer who ultimately took on the project, Peter Ranken of Accredited Passivhaus Design. He helped persuade Bernard to build to the standard after meeting him at the 2013 Ecobuild show in London. “When I saw the plans I liked the design, and thought the house had a good straightforward shape, suitable for passive house,” Bernard says.
The upper level is constructed with crosslaminated timber panels, which is a more flexible way of prefabricating with fewer materials involved and allows for simple assembly. The large building elements involved also mean fewer joints, which means less likelihood of air leakage, improving the airtightness of the building
The overshadowing issue stems from the convention that passive buildings rely a good bit on the heat gain from south-facing windows to achieve the annual heating demand target of 15 kWh/m2 per year. Bernard’s house has only one south-facing window, which in turn is at the lower ground floor level where it receives no direct sunlight, while the east-facing windows were partly overshadowed by a street tree (since heavily pruned by the local authority).
(left) Excavation works were carried out and a retaining wall constructed as local planning rules required the house to be set half a level down from the street; (right) the lower level is built in reinforced concrete, the cross-laminated timber panels are also used for partition walls
“The major source of solar heat gain is the west-facing windows, and therefore [the house is] more prone to evening overheating,” says Peter. “So it was a balancing act to achieve sufficient solar gains in winter whilst preventing overheating in summer.” Part of the strategy was to include enough insulation to retain the limited heat gains that were available. As well as the 300mm of Isoquick load-bearing polystyrene under the floor slab, the team added extra insulation above the slab under a layer of polished concrete as the internal finish.
At one point, railings outside the windows added too much heat loss through their fixings, and overshadowed the west facing windows, so they were designed out and the windows revised, according to Peter. “There was also a delicate moment when I had to suggest to Bernard that a north-facing window giving a view of a favourite flowering camellia would need to be omitted,” he adds.
The Isoquick insulated foundation system eliminates any thermal bridges between the floor and walls
Bernard concedes the house is better without that window, and adds that during the design process they cut down on the number of openings at lower ground floor. “I had more windows as I wanted to make the lower ground floor feel open, connected to the garden and bright — but it feels still very glazed and open. Bedrooms do need walls somehow, and even in the study it feels right as it is.”
To maximise the winter heat gains, the glass in the west facing windows was changed to a less insulating type with a higher g factor to increase heat gains. Bernard was also keen to create a purely electric house but the shadows from the tall Victorian terraced houses ruled out the use of solar hot water panels or photovoltaics as part of the initial specifications.
“I will put some PV in, but they are not part of the basic passive house design,” he says. The lack of solar gains from the south also necessitated a highly efficient MVHR unit — a Paul Novus 300 unit that was supplied by Total Home Environment, and which required careful installation. ”I was concerned about the noise of the system but that proved not to be an issue at all. It is very quiet, we can’t hear it at all,” says Bernard.
Although he did not intend to be the main contractor, the number of specialist sub-contractors involved (for the CLT, wood fibre and taping, MVHR, roof, zinc etc) and their respective costs prompted Bernard to take on this role. Being the client, architect and project manager was a “big enough task” but, as this was his first passive house project, Peter Ranken’s input was essential, “not only to have the calculations done independently but also an exchange of ideas and a dialogue about the project”.
The prefabricated CLT for the upper floor was supplied and fitted by London-based firm Eurban. What was the appeal of using CLT? “Cross-laminated timber was interesting for me because is it a natural product, and allows for a breathable construction,” says Bernard. In short, he says it’s a more flexible way of prefabricating with fewer materials involved, and simple and controllable joints at the point of assembly.
‘I had to suggest to Bernard that a north-facing window giving a view of a favourite flowering camellia would need to be omitted’
“I was still free to use it in combination with any other building material, such as the wood fibre, the windows, the zinc etc. Having a single point of engineering, manufacturer and installer was also a good system for this building,” he adds. The large building elements involved also mean fewer joints, which means less likelihood of air leakage. ”It provides continuous surfaces with little joints that can be left exposed if desired, which in the case of this simple building was ideal.”
Peter adds: “Cross-laminated timber panels have few joints that could cause air leakage, and a continuous airtightness membrane on the outside of the panels prevented leakage through these.”
The excellent airtightness score (0.29 air changes per hour) is surely testament to their attention to detail – and the involvement of one of Ireland’s leading airtightness contractors, Clioma House. The house was air tested twice, and was well below the passive house requirement on both occasions, with the final test better than the first, according to Peter.
Although he didn’t commission the building for himself or his family as it’s quite small, his parents-in-law were looking to downsize and move to London and so asked if they could move in shortly before construction began.
He didn’t have to change too much for his in-laws — he upgraded some of the finishes like the kitchen, and bathroom, and installed more fitted joinery, Vitsoe shelving and curtains for the lower ground windows. He modified an opening to the second bedroom so that it is wider and more connected to the hallway.
“They like the space. It is full of light, feels spacious, peaceful and I think they like the exposed materials of wood and concrete,” Bernard says. “It is also very comfortable from an acoustic and temperature point of view as well.”
Selected project details
Architect: Tectonics Architects
Passivhaus Design/PHPP: Accredited Passivhaus Design
Passivhaus Certifier: WARM
Structural engineers: Michael Hadi Associates
Cross-laminated timber engineers & contractors: Eurban
Sub floor insulation: Isoquick
Airtightness & wood fibre insulation contractor: Clioma House Ltd
Lower ground floor insulation & brick slips: Alsecco / Meti Building Services
Windows: Internorm UK
Zinc: Peters Roofing
MVHR: Paul, via Total Home Environment
Air testing: Jennings Aldas / Paul Jennings
Electrics / KNX installation: Sagar Smart Homes
Rigid insulations: Kingspan Insulation UK, Jablite
Wood fibre insulation / airtightness products: Ecological Building Systems
Gas boiler: Worcester Bosch
Additional info
Building type: 94 sqm (treated floor area) detached house constructed with cross-laminated timber panels.
Completion date: April 2015
Budget: Confidential
Passive house certification: Certified
Space heating demand (PHPP): 13.64 kWh/m2/yr
Primary energy demand (PHPP): 99 kWh/m2/yr
Airtightness (@ 50 Pa): 0.29 air changes per hour
Measured energy consumption: Measuring in progress
Thermal bridging: Accepted as thermal bridge free by passive house certifier. All insulation is external to structure, including: insulated raft foundation, larsen type timber and plywood framing to support upper floor zinc cladding and parapet, adhesive fixed brick slips on external polystyrene insulation.
Ground floor (from inside): 75mm polished concrete, on 25mm Kingspan TF70 insulation, on 300mm reinforced concrete, on 300mm Isoquick expanded polystyrene insulation. U-value: 0.094 W/m2K
Lower retaining wall (from inside): 175mm reinforced concrete on 300mm Kingspan Styrozone H350R insulation. U-value: 0.101 W/m2K
Lower wall (from inside): 175mm reinforced concrete, on 250mm Jablite insulation, on 8mm render, on 15mm brick slips. U-value: 0.146 W/m2K
Pavement wall retaining (from inside): 13mm plaster, on 175mm reinforced concrete, on 250mm Kingspan Styrozone H350R insulation, on 215mm reinforced concrete. U-value: 0.119 W/m2K
Upper ground floor wall (from inside): 100mm Eurban cross-laminated timber, on Pro Clima DA breathable vapour control membrane, on 140mm Gutex Thermosafe Homogen wood fibre insulation, on 120mm Gutex Thermosafe Homogen wood fibre insulation, on 60mm Gutex Ultratherm wood fibre insulation, on 50mm air gap, on 12mm plywood, on Zinc cladding. U-value: 0.106 W/m2K
Roof: Single-ply membrane, on 240mm (average) Kingspan Thermataper TT47 insulation, on vapour control layer, on 160mm cross-laminated timber. U-value: 0.080 W/m2K
Windows: Internorm triple-glazed aluminium clad windows, argon fill. Whole window U-values: 0.70 to 0.89 W/m2K; higher g value in west-facing windows.
Heating system: Two electric heated towel rails in bathrooms – Bard & Brazier DRW 52-120 & 75-50. One electric connection heater in living room – Meinertz K60-123-12.
Hot water: Worcester Bosch Greenspring high efficiency condensing gas boiler
Ventilation: Paul Novus 300 heat recovery ventilation system, circular galvanised steel ductwork. As installed efficiency (PHPP): 90.9%
Green materials: Cross-laminated structural timber panels for upper floor external walls, roof, intermediate floor and lower floor partitions provide structure and internal finish. Wood fibre insulation to CLT panels. Osma wax finish to CLT panels internally (no internal wall linings).
Image gallery
-
Typical wall build up Typical wall build up
-
Glazing detail upperground Glazing detail upperground
-
Presentation sheet Presentation sheet
-
Plots 1-2 Floor plans Plots 1-2 Floor plans
-
Plots 1-2 Elevations Plots 1-2 Elevations
-
Ground floor junction brick Ground floor junction brick
-
Window-Junctions---Head--Cill Window-Junctions---Head--Cill
-
Corner-Bay-Post---Horizontal-Section Corner-Bay-Post---Horizontal-Section
https://passivehouseplus.ie/magazine/new-build/compact-solid-timber-passive-house-on-london-infill-site#sigProId8e3e42da80