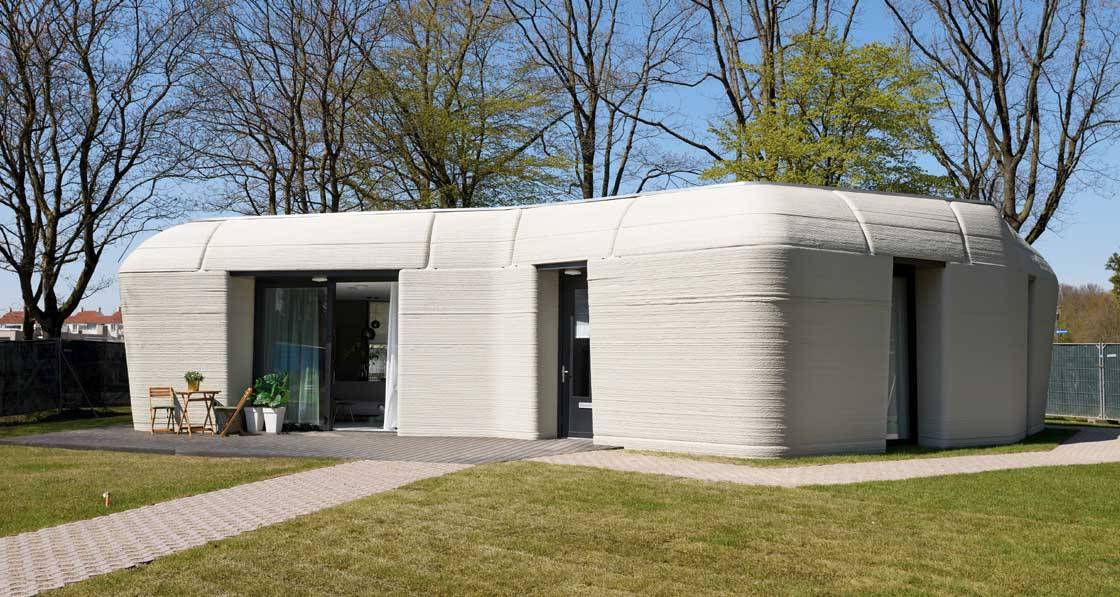
- Blogs
- Posted
On the 3D printing of buildings
This article was originally published in issue 38 of Passive House Plus magazine. Want immediate access to all back issues and exclusive extra content? Click here to subscribe for as little as €10, or click here to receive the next issue free of charge
To the already long list of unfashionable opinions which I have put forward, I need to add the following: when it comes to 3D printing, I can’t see what all the fuss is about. Sure, it’s a useful means of making prototypes, and the small number of one-off products or parts that need very little strength – but there seems to be a distinctly finite number of those. 3D printers mostly seem to churn out little toy boats more likely to pollute our oceans than sail on them.
Some argue that 3D printers are inexpensive enough to represent a democratisation of the manufacturing process, but I don’t buy it. There is still a skill threshold to reach in the digital design stage, time which one could spend learning how to use a metal working lathe, hobby versions of which aren’t much more money than a half decent 3D printer. Or think of the stunning architectural models that have been made with little more than a craft knife. So, while 3D printing is an interesting tool to add to our collective arsenal, the popular obsession with it is baffling to me.
You will be therefore unsurprised to read that I have reservations when it comes to the recent flurry of attention around 3D printed buildings. The one doing the rounds on the socials at the time of writing is the Dutch “boulder house” featured in the Guardian (30 April 2021). This detached house is the latest in a string of prototypes and is designed to resemble a boulder. Exactly which boulder served as a model has not been disclosed.
Proper sustainable building is all about the boring stuff.
I understand that the process is still in development, but if this is the sort of architectural expression we can expect to be unlocked, I am unmoved. Even if more ‘interesting’ shapes become possible, are they a good idea? Frankly, assuming for a moment that such forms are so essential to architectural expression, all this is possible with more boring techniques. Then there is the subject of form versus function in passive buildings, which I won’t rehash here.
This is Passive House Plus after all, so we turn next to the thermal performance. Those involved are coy about the exact performance, and though I’d be delighted to be proven wrong I doubt that the energy performance is being measured. It’s difficult to find out exactly how the walls work in the Dutch example, but we can see in Matt Risenger’s recent video (‘Is this the future of Construction? 3D Concrete Printed Homes’, YouTube, 4 May 2021), that we have two leaves separated by a zigzagging ‘core’ like an extruded truss-joist. The window reveals are formed by simply continuing the leaves from inside to out. I therefore raised an eyebrow when the engineer claimed the construction to be ‘thermal bridge free’.
In other words, as far as I can tell, to actually add insulation to any of these structures, you’d have to stick it on the outside afterwards (and clad to taste), which seems to defeat the object somewhat. Airtightness wise, OK it is monolithic but it’s at junctions (windows, floor, services) where one finds leaks, so I’m unconvinced the method of construction is inherently airtight.
As printed, the internal walls are rough, but Matt Risenger assures us it’s not a bug, it’s a feature. Anyhow, good luck keeping all those crevices clean. We should also consider the claim that this technology speeds up construction. I’m willing to accept it might save some time on the superstructure compared to standard masonry, but anyone that has experienced a build from beginning to end knows that the superstructure is far from the most time-consuming element – it’s the groundworks, services, fixtures and fittings and finishing that take the real time.
Finally, there is the issue of embodied carbon. Most of the examples I’ve seen are some sort of very clever concrete, though an earth-based example has also been finished (with only a tiny bit of ‘binder’). The builders attempt to justify the Dutch example by observing that we must use less concrete, and the boulder house uses less. I’ll go out on a limb and say maybe – stay with me – you might use less concrete if you didn’t build the entire house out of it.
The waste of resources is perhaps the most frustrating thing – not just the concrete but the human effort. I’ve no doubt that it was a great technical achievement to develop this technology, but it has the feel of a solution looking for a problem. One of those ideas that look great in the sketch book and are sexy enough to get some cash thrown at them, but aren’t really moving us forwards.
In contrast, proper sustainable building is all about a solid strategy, the fine detail and quality of execution – some might say, the boring stuff. If you’re reading this magazine, you probably know all this and spend your time worrying about precisely which type of airtightness tape is best to join material A to material B, rather than whether we can equip a drone with a tube of silicone. And I salute you and your quiet dedication to getting on with delivering sustainable buildings.