- Special Feature
- Posted
Dublin Docklands
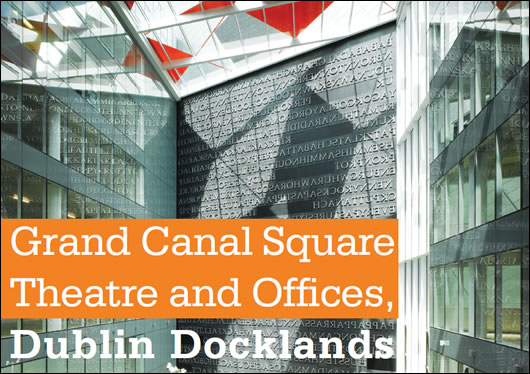
Number Two Grand Canal Square office, completed in September 2009 and substantially occupied by law firm Byrne Wallace in August this year, set a landmark in commercial office development by combining world-class design with sustainability - reconciling the architecture of Daniel Libeskind with achieving both a Breeam Excellent rating and an A3 BER certificate. Paul Dunne, sustainability and M&E director for Arup, outlines some of the project’s history and its achievements.
The Grand Canal Square Theatre and Offices is a world class cultural and commercial development located within the regenerated Sir John Rogerson’s Quay Gasworks site in Dublin City, Ireland.
The original site accommodated the former gasworks including coal stores and the former Segas plant, and the ground on the site suffered from significant contamination. Over ten years ago the DDDA undertook a major programme of site investigation and ultimately extensive remediation. This started with the construction of over 1000 metres of cut-off retaining wall around the perimeter of the development site and then the removal of soil from the site down to a level of between -1.0 and -3.0 OD (oxygen demand), and subsequently reinstatement of the soil once treated to a formation level of 0.0 OD.
In 2007, Chartered Land took the first steps to build the Grand Canal Square Theatre and Offices at Grand Canal Square. The Daniel Libeskind design included a mix of culture, shopping and offices overlooking the square and created indoor public spaces to compliment the outdoor public spaces at the waterfront.
The building shares a fantastic frontage onto the Martha Schwartz designed public square with the Grand Canal Hotel designed by Portugese architect Manuel Aires Mateus to the East and No 1 Grand Canal Square designed by Dublin Architect DMOD on the west. Arup’s building engineering teams have been involved in all of these developments.
The development as delivered incorporates a 13,768m2 2,000 seat theatre building (No 3 GCS), a 21,092m2 south office block (No 2 GCS) and a 33,320m2 north office block (Nos 4&5 GCS). The buildings vary in height reaching up to eight storeys, with a single level basement throughout predominately used for car parking and plant room space.
Construction on the project started in 2007. The curtain rose on 18 March 2010 with a performance of Swan Lake by the Bolshoi Ballet and the offices received their first major tenant when Byrne Wallace moved into their new offices in July.
The area benefits from the attraction of the theatre and the businesses which provide local employment opportunities in addition to the spin-off retail businesses locally. Connectivity with the rest of the city has been increased dramatically and the provision of a high quality venue promotes the Docklands as a destination for tourists as well as Dubliners who previously would not have had reason to visit.
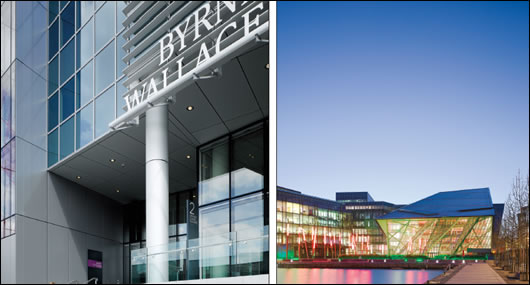
(above left) Law firm Byrne & Wallace were the first major tenants to occupy the building, having moved in this summer; (above right) the development by night
Breeam
Breeam (BRE Environmental Assessment Method) is one of the world’s most widely used environmental assessment method for buildings. It sets the standard for best practice in sustainable design and is regarded as a universal measure of a building's environmental performance. The Breeam 2006 methodology, under which the building was assessed, looks at the overall sustainability of a project considering its performance against a broad set of headings, which for this project were management, health and well-being, energy, transport, water, materials, land use, ecology and pollution.
The target of achieving a Breeam Excellent rating set the agenda for the early design meetings, which included JV Tierney as the independent assessors for the Breeam process.
John Sisk and Sons implemented a wide range of management systems for the project at the outset ranging from the segregation of waste materials to measuring energy used in the construction process, and – in the later stages of the project – to the management and monitoring of the commissioning process. The systems employed were deemed equivalent to and in some respects ahead of the standards u set by the Considerate Constructors scheme adopted in the UK.
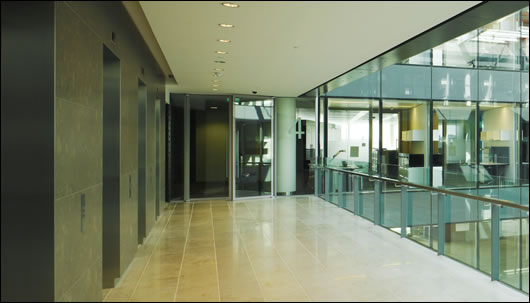
Arup used Integrated Environmental Solutions software to model combinations of glazing types, and the the final overall U-value for the glazed facade including frames is 1.6 W/m2K
Health and well-being as a heading comprises sixteen sub-headings ranging from air quality to thermal comfort and lighting zoning to microbial contamination. The building design responded to all of these headings which are focused on the health and wellbeing of the building users. The design of a well zoned lighting environment, coupled with good ventilation and control systems, all contributed to improving the internal environmental quality – the balance achieved between day-lighting and artificial lighting is discussed in greater detail later in the article.
As part of the 2006 Breeam assessment process, the building design had to demonstrate the CO2 emissions achieved in relation to a reference building, as outlined in the British building regulations part L2A. This process had not been adopted in Ireland at this time, so Arup constructed a full Simplified Building Energy Model (Sbem) model of the building to test the performance against the British standards. The resultant models achieved CO2 emissions 14.4% better than the base case building for No’s 4&5 Grand Canal Square and 11.7% better than the base case building for No 2 Grand Canal Square.
The transport credentials are strongly supported by the city centre location of the building, which is within walking distance of the Dart and mainline trains and across the river from the Luas. The building has extensive facilities for cyclists including shower and changing rooms to promote the use of bicycles.
Water is conserved throughout the buildings through the use of metering and proximity detection shut-off devices to toilets and urinals among other measures.
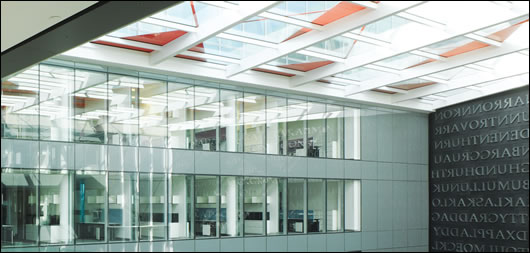
The building’s multi-storey glazed atrium were “of great importance” to the architect and developer, and the lighting team’s brief was not only to highlight the ‘letter wall’ feature but to create moods and shadows of light in the atrium space
The BRE’s Green Guide to Specification closely informed the choices made for materials and finishes. This ranges from the use of GGBS in the concrete structures to the specification of timber finishes using materials from managed forest sources.
The renewal of a derelict urban space also figured highly in the development’s sustainability credentials as it forms the closing piece to the creation of a new public space in the heart of Dublin. Although not figuring centrally in the Breeam assessment process because remediation predated the new building contract, this attribute is at the core of the success of the project and the incorporation of new green spaces at roof level on the buildings will add to the renewal of biodiversity in the area.
Pollution is minimized through the use of low global warming potential insulation, refrigerant leak detection and low NOx boilers.
All these measures were given detailed consideration by the whole design team. The case of energy usage was subject to several iterations to test alternative design solutions. Each element was ultimately a step to achieving the Excellent rating.
Energy efficiency
Energy efficiency and sustainability have been central to the building design. Chartered Land identified an Excellent Breeam rating for the office buildings as a critical target, and set the design team the task of shaping and detailing the building and its systems to achieve this standard. The target was made all the more challenging because the initial site remediation had been completed separately and it was not possible to secure vital Breeam points for this work, which consequently necessitated an outstanding response from the building in its energy efficiency to compensate.
This had to be achieved in the context of creating a modern, fully air conditioned, city centre building which could meet ever increasing standards for occupant comfort, flexibility and adaptability.
The areas targeted for energy savings include all the normal approaches such as lighting control, heat recovery and high efficiency boilers, but also adopt a number of key additional steps which have contributed to the building’s outstanding performance. These include the following measures:
• Low pressure hot water flow and return temperatures of 70C/50C were chosen. When compared with the use of 82C/71C design temperatures the principle benefits to the user include energy savings due to the use of condensing boilers, which operate at higher efficiency compared with conventional boilers, lower fluid flow rates using more efficient pumps and lower pipe work losses.
• A high performance active façade has been provided to meet and indeed exceed Part L requirements as detailed on p34.
• A chilled water loop was designed to avoid the use of glycol as an antifreeze – up to 20% glycol is typically added to chilled water systems to protect pipes from water freezing during the cold winter months. The addition of glycol reduces the specific heat capacity of the water from 4.2 kJ/kg°C to kJ/kg°C, which necessitates a 20% higher flow rate to deliver the same energy transfer in the chilled water systems. The higher flow rate results in higher associated energy consumption. This energy is saved by a design that avoids the need for glycol.
• When the design was being assessed the building was to be air conditioned using conventional fan coil units. To minimize the energy these units would absorb, they were all selected with single phase electronically commutated direct current (ECDC) motors in lieu of traditional AC single phase motors to optimise energy efficiency. The use of ECDC motors reduces fan energy consumption by approximately 60% to 70%. Water-side control of the fan coils was chosen to eliminate energy losses from hot deck and cold decks associated with airside controls. The use of waterside controls also permits the use of variable flow circuits with associated pump energy savings. Later on when negotiations began with the future tenant further efficiencies were realized by the switch to chilled beams but these did not form part of the Breeam assessment for the building.
• Demand based ventilation was selected ¬– modulating dampers are fitted on the supply and extract ducts to each office zone. The dampers modulate in response to tenants’ CO2 sensors in the extract duct to optimise the flow of fresh air to each zone. Dampers to each zone close during unoccupied periods. Variable speed fans will slow down as more and more zone controls close, matching ventilation delivery to demand. This demand based ventilation ensures that the treatment (heating, cooling energy) and delivery (fan energy) are optimised at all times. The mechanical ventilation system has also been configured to allow night purging of the office spaces, thereby reducing mechanical cooling loads during occupied periods.
The Façade
In developing the façade design and energy efficiency strategy Arup used the 2005 Technical Guidance Document L (Conservation of Fuel & Energy) to provide base thermal performance requirements. The aim was to achieve maximum daylight transmittance and to minimise heat loss and excessive solar radiation entering the space.
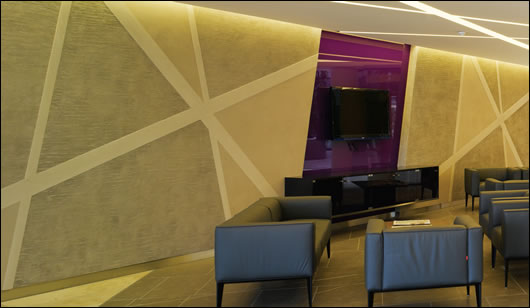
These are often conflicting requirements but through the design stage, Arup used Integrated Environmental Solutions software to model combinations of glazing types and fixed and moveable shading to arrive at the optimum design. Arup provided performance requirements for all elements of the façade and reviewed contractor proposals to ensure the delivered solution met the design intent. The final overall U-value for the glazed façade including frames met the target of 1.6 W/m2K while the G values achieved their target of 0.35.
The result of the process: the heat loss through the façade was 18% lower than required under Part L and together with the artificial lighting, achieved an average of 500lux over the office floor plates for an electricity consumption of only 9W/m2. The use of moveable shading within twin skin glazing and a façade management system ensures that during the heating season solar gains are admitted by retracting the shading which reduces boiler energy, and with the shading deployed unwanted solar gains are prevented from entering the space in order to minimise chiller energy consumption.
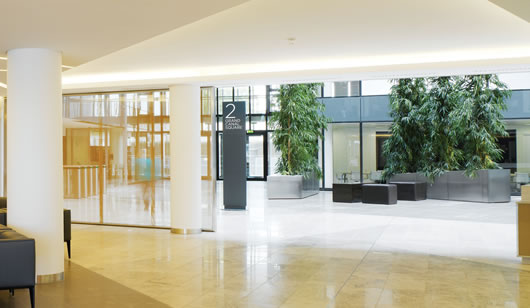
A combination of motion and daylight sensors maintain the required lighting levels at maximum efficiency, while the entrance space also features light fittings in the planter boxes to help give correct lighting levels in the circulation spaces and walkways, as well as highlighting the glass structure and the ‘letter wall’
Lighting
The lighting design for the offices was developed through a series of iterations with the façade design to model the actual lighting design needed to maintain appropriate lux levels in the working areas. While aiming for low energy lighting as a principle, the team had to validate the actual energy used by the lighting to allow a real figure to be substituted for a default value in the energy usage and carbon analysis calculations within the Sbem models.
The fitting modeled in the design has twin T5 lamps which provide both up and down lighting, and the lamps in combination with the reflector and high quality optics account for the fitting efficiency.
The final design was modeled to illustrate the final solution and verify the actual energy consumption of the design, resulting in a lighting energy demand of 9W/m2.
An automatic lighting control solution was used to maintain the required lighting levels at maximum energy efficiency. This is achieved by using a combination of motion and daylight sensors for daylight sensing, automatic dimming and presence detection.

The building shares a fantastic frontage with the theatre onto the Martha Schwartz designed public square
Lighting design calculation
The building’s multi-storey glazed atrium and lift lobby entrance spaces were of great importance to Chartered Land and the architect, and the lighting team’s brief was not only to highlight the ‘letter wall’ feature, but to create moods and shadows of light around this multi-storey glazed entrance space. This was achieved by mounting fittings on the glass structure, installing floodlights in the tiled floor, recessing fittings in the ceiling above the lifts and locating fittings in the planter boxes scattered around the entrance space to give the correct lighting levels in the circulation spaces and walkways, as well as highlighting the glass structure and the letter wall.
Tenant interface
It was recognised early in the shell and core design process that the tenant’s needs would have significant influence on the final M&E design. Arup’s design approach was to retain sufficient inherent flexibility in the shell and core systems to allow the tenants’ needs be accommodated. By way of example, the M&E systems to No 2 Grand Canal Square were adjusted to facilitate the installation by the tenant of chilled beams to the offices and a central tri-generation system. This necessitated elevating chilled water temperatures, installing de-humidification at central plant and completing enabling works to accommodate the tri-generation plant. The services design solutions for No 4 Grand Canal Square was adjusted to include an ice bank installation among other modifications. These tenant enhancements were adopted in the shell and core designs for each of the buildings. The interaction between Chartered Land and their respective tenants ensured the shell and core M&E installations avoided unnecessary waste or duplication and led to an M&E installation mutually agreeable to all parties. As these enhanced measures were not part of the original Breeam assessment process the final carbon footprint of the building will be even lower than projected in the design of the base building.
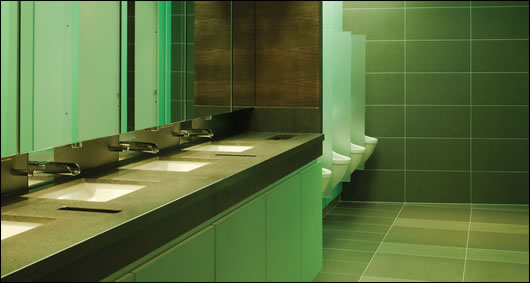
Water is conserved through the use of metering and proximity detection shut-off devices to toilets and urinals
Awards
The final buildings represent a very successful coming together of low energy building principles explored in recent owner occupied offices and now applied to a commercial development.
The buildings as constructed have been assessed using the Breeam protocol and have achieved an Excellent rating. They have also been measured through the Building Energy Rating system and have achieved an A3 rating. These measurements are testament to the standards reached by these commercial office buildings and show what can be achieved through a clear design focus on quality and energy efficiency from the start of a project.
The awards are a reflection of characteristics which underpin the fundamental sustainability of the Grand Canal Square Theatre and Offices. They are recognition that these buildings u set a standard for urban regeneration, which can be a model for such projects in the future.
Selected project details
Developer: Chartered Land
Project Manager: Lafferty Project Management
Design Architect: Daniel Libeskind
Executive Architect: McCauley Daye O’Connell Architects Ltd
Interior architect: Arcology Design
Building Services Engineers: Arup
Civil and Structural Engineers: Arup
Acoustics Consultants: Arup
Quantity Surveyors: Davis Langdon PKS
BREEAM Assessors: JV Tierney
Main Contractor: John Sisk and Sons
Mechanical Sub-contractors: HAO Neill (Theatre) and Lynskey Engineering (Offices)
Electrical Sub-contractor: Precision Electric
Facade Sub-contractor: Permasteelisa
Byrne Wallace fit-out, No 2 Grand Canal Square
Words: David Feighery, Delap & Waller consulting engineers
![]() |
Leading law firm Byrne Wallace recently moved into their new headquarters at No 2 Grand Canal Square. A low energy building was a key part of the design brief for the fit-out design. To fulfil this requirement the challenge for the fit-out team was to design the building services to provide a low energy, low carbon building, while still maintaining a superior level of occupant comfort. The design of the building was assessed holistically to determine the final solution. This assessment included air conditioning, ventilation and lighting systems to reduce the demand and overall energy usage for the client.
The air conditioning system installed in the building consists predominantly of a passive chilled beam installation, located within the ceiling void. Each chilled beam comprises of a unit complete with a linear cooling coil, supports and a supply skirt. The system is installed above the ceiling grid with perforated sections of ceilings located below.
The system operates as follows: cold or chilled water passes through chilled beam coils, the warm room air rises and is cooled against the surfaces of the beams. The chilled air – which is now heavier – flows through the beam and then falls into the room space itself, creating a circulation process whereby warm air is continuously replaced by colder air.
In addition to the convective heat transfer, the radiant effect of the beam also cools the ceiling, which in turn re-radiates this cooling into the space. This provides a comfortable environment for the building occupants and less chance of draughts. The passive beam provides the comfort and aesthetic benefits of a chilled ceiling at significantly lower costs with higher cooling capacities. The environment created is unrivalled with no noise or draughts. Air movement is reduced to 0.25 m/s to comply with the appropriate standards.
The passive chilled beam installations was installed in conjunction with a displacement fresh air system, with fresh air introduced into the floor void or plenum and distributed across the floor plate. Incoming fresh air is tempered to provide heating to the building during the heating season. Additional heating is provided to offset fabric or glazing losses to the perimeter zone by trench heating.
Aside from low energy consumption, the passive chilled beam system provides additional key benefits. It operates at low ambient noise levels, provides a responsive A/C system that reacts to the internal causal load, and has a low maintenance, lower life cycle cost than a traditional fan coil system.
All of the building’s mechanical and electrical systems are controlled via the landlord/tenant BMS to provide the optimum level of thermal comfort with minimal energy input. In addition to controlling the M&E Systems, the BMS monitors the energy consumption – including both fossil fuel and electrical usage.
High frequency dimmable luminaires with PIR control constitute the lighting system for the fit-out. The PIR control triggers automatic switching to turn lights off or on based on natural daylight levels and presence detection.
- Articles
- Special Feature
- Dublin Docklands
- Grand Canal Square
- Theatre
- Byrne Wallace
- Daniel Libeskind
- Arup
- BREEAM
- Gasworks
- Basin
- Martha Schwartz
- Manuel Aires Mateus
- Sisk
Related items
-
Adaptation sensation
-
Bicester centre is UK’s first nondomestic passive house ‘plus’
-
Major office scheme passes DLR’s passive house or equivalent policy
-
BREEAM excellent building marries sustainability with world-class design
-
IGBC launches Ireland’s sustainable homes label
-
Daikin achieves responsible sourcing standard
-
Is this the UK's greenest building?
-
Private Enerphit homes come to London rental market
-
Passive research centre acts as living showcase for green tech
-
Pioneering passive office surpasses expectations
-
Opinion
-
Thermal bridging