- Eco Housing
- Posted
Ecohouse
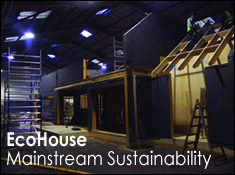
Jeff Colley: This house is interesting in that it is quite close to the cutting edge, whilst being designed with the mainstream in mind.
John Goulding: That was the idea. There are obviously changes in legislation, such as recent changes in the Building Regulations, which have been driven by Agenda 21, the Kyoto Protocol, and various European Commission initiatives, such as the EU Directive on the Energy Performance of Buildings. Certainly the government here is awake to the need to improve the environmental performance of the building stock in Ireland. Buildings account for about half of the energy that we use, if you consider the energy used to heat, light, ventilate and cool buildings, but also the energy used to make them. This is a substantial chunk of our national energy bill, but changes in the building sector can bring dramatic improvements in Ireland’s overall environmental performance. The Building Regulations are one major step in achieving that, with increases in insulation standards and so on.
JC: How do you think building design should respond to these sorts of increases in standards?
JG: Rather than just respond to requirements like that, there is a need to look at what will be required in the future; to future proof buildings. People strive to meet the Building Regulations, and sometimes they don’t actually achieve that. But even if they do manage to, all they’ve done is to build the worst possible building that the law currently allows. Why would you just strive to meet the bare minimum requirements, if you know they are going to be increased in future years, and your building will compare relatively badly with buildings built to a higher standard later on? It makes sense to future proof buildings, and to build to a higher standard. This is not just to maintain the value of the building, or to reduce emissions, but to ensure higher standards of health and comfort as well.
JC: What sorts of measures did you employ regarding the building’s energy performance?
JG: I took the approach that this should be a building that made use of ambient energies, particularly passive solar energy, to cater for most of the requirements for space heating, and hot water heating through active systems. The form of the building and the orientation of the building are crucially important. On the south facing side there are large areas of glass. The building was designed in such a way to capture as much solar heat for free as possible, to retain that within the building and distribute it so that the house remains comfortably warm day and night.
On the north side, the windows are quite a bit smaller, and I took a deliberate decision to design the house with reference to Irish vernacular architecture, to emphasize the point that you can have these low energy technologies in a house of any style. To make that point, I decided on this occasion to make it a very typically Irish house, unlike a lot of the houses that are coming in from abroad.
This was intended to go someway towards getting over people’s concerns. Many people believe that if they want to live in an ecological house, they have to accept some sacrifices, in terms of lifestyles and comfort and so on. It is quite the opposite in fact. The Eco house performs far better than most conventionally built houses. According to our calculations, it should be possible to heat the house for as little as €100 to €150 per year based on a typical family’s needs.
The house is of advanced timber frame construction, using I Studs and I Beams and so on, which are a composite stud and which use quite a lot less material for much greater strength and depth. So you can fit in more insulation in the roof and walls for instance, without problems, whereas it is quite difficult to achieve that with masonry construction. We reckon that we’re down to about 0.2 for the walls, and 0.27 is the Building Regulations requirement. We could go further, and with Century’s Formula One design, we could bring it down to 0.144 if we wanted to go all out on it, which is quite significant. The design and orientation, and the glazing ratios are important.
JC: Given that you placed such an emphasis on improving the building’s thermal performance, what attention did you give to maintaining interior air quality?
JG: The decision was to make it an airtight house, so that you can control the amount of air flowing in and out of the house. Most houses in Ireland are not airtight; they have leaky windows, floors and so on, which results in a constant infiltration of unwanted unheated air that you have to provide heating to compensate for. But you have no control over it, and even with the standard vents that are normally required, it is very difficult to control the amount of air coming in, in response to demand. If the house is being occupied by one person, there is very little fresh air required, whereas if you are having a party, it’s another matter entirely.
I designed the house to be airtight, and under normal conditions with the windows closed for instance, used air would be extracted from bathrooms and the kitchen, specifically, through ducts, and drawn into a heat exchanger, where the used air is exhausted after its heat is removed. Most of its heat is removed and given to the incoming flow of fresh air. So the incoming air is preheated, and you don’t need to provide the heating to compensate for its coldness. It is brought up to a temperature close to a comfortable room temperature, and then supplied to living rooms and bed rooms, and so on. So there’s a constant airflow through the house, and that can be controlled manually through the device, or it can be controlled in response to temperature sensors, CO2 sensors and so on.
JC: Aside from the heat recovery ventilation unit, what role did the other active energy technologies play?
JG: There are a couple of other options for heating. For instance, there is a wood pellet fuelled stove in the sitting room in place of an open fire which would tend to be very inefficient. This is quite an efficient device, it burns wood pellets automatically, fed into a hopper system, and it gives a focus to the living room, while providing quite a substantial amount of the remaining heating requirement.
We also had an evacuated tube solar collector on the roof, which was sized to provide at least half of the hot water needs of the family, at no cost, from solar energy. The heat pump or the furnace is really providing auxiliary heating.
So with systems like this, for most of the year you wouldn’t have to turn on the heating. If you do however, we chose two alternatives, one of which was a wood pellet fuel furnace, in a boiler house behind the garage. The alternative to this was to use a heat pump, which would draw heat from pipes buried in the garden for example. Either of those can supply the remaining hot water and space heating needs.
JC: You also opted for an adaptable design for the Eco House, therefore giving the option of change of use.
JG: Indeed. To make it a little more interesting, I designed it in three phases. The version at the show was the middle phase; the expanded family version. The first phase would be a stripped down version of that. The idea was that a young couple, who want to live in a particular area, and plan to continue living there, could buy the house, in a more affordable form. Then when they have children and the space needs increase, they can add on additional rooms, mostly to the exterior, but in the case of the fifth bedroom, this involves what you might term an internal extension, over what would have been double height space, above the living area, whilst the double height space over the dining room remains. So the building has the capacity to expand to a five-bedroom family home with a garage.
Furthermore, when the kids leave the nest, and the space needs are lessened, then you can subdivide the house, for example into a two bedroom apartment, a ground floor apartment, and a three bedroomed house. The idea is that it could be used as a granny flat, perhaps for an elderly relative; it could be used as a geriatric carer’s accommodation, if the people in the main house are elderly. It could also be used as an apartment to rent out to give additional income, or one of the kids might want to start a home.
There was a sunroom in the house, beside the living room, and normally that wouldn’t be a heated room. It would take in solar heat, through the windows and so on. It has an insulated roof, like the main roof, so that unlike a conservatory it doesn’t overheat in summer and it doesn’t lose heat in winter through the roof.
There is also a conservatory on the south side, which would be operated in a slightly different way, particularly in autumn and spring. You would close the doors between that and the rest of the house, and allow it to heat up to perhaps a higher level than you would find comfortable to sit in, to soak up as much heat as you can during the day. That heat can be transferred to the house at night time. But if you wanted to you could sit in there as well, by opening the windows and letting the temperature drop.
Paul MacDonald, Director of Century Homes, speaks to Jeff Colley about the concept behind the Eco House, and the advances in structural technology that add to the house’s sustainability credentials.
JC: What was the reason for going into the Eco House project, from Century Homes’ perspective?
PMcD: Well, for some time now we have been trying to develop a product, a concept in a house, by equating it to a formula one car. There is a range of research and development, resulting in skills, resources, and certain product, which we would in someway try to incorporate into the house. The goal of this is to achieve the top performance that one could from a house. This involves reducing the U-Value to the lowest possible degree, while at the same time allowing a level of comfort in the house, a level of user-friendliness and of general accessibility for the public. This is something that they can actually adopt, maybe not in all its forms, but certainly the best points out of it. The reason we equate it to a formula one car is that car manufacturers put all their research and development; everything that they can into that car. Now, you will never buy a formula one car, but we would hope that through developing this, we are able to bring items to the market place that will make houses better.
JC: Aside from the many energy efficient technologies in the house, how was this research and development approach reflected in Century’s involvement?
PMcD: There are a number of aspects that we incorporated, that if you like, are a step on from what we do currently. First and foremost, one of the things we included was the use of I Beam walls, floors, and roof panels. From an ecological point of view, a sustainable point of view, I Beam is an engineered wood product, and if you can imagine a 300 millimetre section of plywood, on its edge, with a top and bottom flange on it, that forms the structure of the joists and the studs. What it means is that, in the manufacture of that product, something like 50% less wood is used. It’s using the best, and in fact the centre section that is used is not plywood, it’s OSB which itself is a product made up from waste product, before being mulched, and pressed into boards which are then put up and used, and there is a huge advantage in this.
We’re currently working on FSC and PFC certification. In my understanding, if you cut down one tree, it’s a good idea to plant ten more. However the consequence of cutting down trees without planting, has several impacts, including the effect on wildlife, and the effect on local communities that have lived in forested areas, so the more we can do with less resources, the better.
JC: Did this approach lend itself towards furthering the energy efficiency benefits that conventional timber frame offers?
PMcD: For starters, as you don’t have a solid section of timber between the top and the bottom, the cold bridging effect in the house is reduced significantly. It means that you don’t have a bridge by which cold can come across the cavity, and affect the performance of the house inside, which is a huge advantage. We use this as a standard in floor joisting at the moment right across the board. Where it’s not so usual to use them is in wall sections, in studs. It allows you to reduce cold bridging, and therefore get better U Values. It also allows you to get deeper sections of wall, much more so than you would with standard timber studs. You can go anything up to 600 deep, which is twelve inches. So for people who want to create the old style of deep reveals in the house, it’s very easy to do it now, using this technology.
- Eco House
- John Goulding
- century
- timber frame
- energy efficient design
- EU Directive
- Energy Performance of Buildings
- environmental performance
Related items
-
Up to 11
-
It's a lovely house to live in now
-
Passive house isn’t just about efficiency – it’s about social justice
-
We Build Eco flat pack timber frame partnership gathers pace
-
Mass timber masterwork
-
AECB conference to showcase timber innovation
-
Heart of oak
-
Welsh social housing to embrace passive house, timber & life cycle assessment
-
Cambridge chooses passive house comfort for Kings’ College students
-
Pitch perfect - Beguiling Dundee passive house puts wood into woodland
-
Above the curve - Limerick passive house showcases precision timber engineering
-
COP26 house to showcase fabric first, low carbon build methods