- Case Studies
- Posted
True to Form
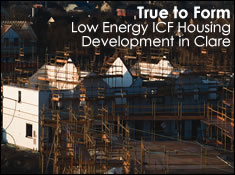
Adding to the list of developers aiming to deliver energy efficient housing, Cronan Nagle Construction are currently on site with 188 highly insulated, airtight homes in Ennis, co. Clare. The development, which also incorporates heat recovery ventilation and condensing gas boilers is surpassing the thermal requirements of Building Regulations by up to 45%, as John Hearne discovers.
Cronan Nagle Construction’s (CNC) new development, Acha Bhile in Ennis, Co. Clare claims is amongst the largest eco-friendly project in the country. With phase one now complete, the second and third phases will see the construction of fully 188 units at a greenfield site on the Lahinch road.
Incorporating a range of techniques and technologies, from airtightness to heat recovery ventilation, ICF construction and condensing gas boilers, just over half of the development is in receipt of funding under SEI’s House of Tomorrow scheme. This doesn’t mean however that the eco spec applies to half of the houses. Conor Williams of CNC confirms that every unit conforms to the same specification. “The big thing about all of this, and what we would like to get out there as CNC Ltd, is our commitment to energy conservation. We’re constantly looking at ways to get better at what we’re doing. This one is here now and the next one will be this spec plus a bit more and so on after that. That’s our message. We’re also doing a job over on the Gort road with the exact same specification, so this is not a one-off.”
One of the central innovations onsite is the construction method. All units are built using Reward Struct-Sure’s insulating concrete forms (ICF). The finished product comprises a central wall of concrete sandwiched either side by polystyrene sheeting. Oliver O’Toole of the company explains that the building block is made from two 65mm expanded polystyrene sheets held together by a reinforced plastic rib which does the job of the conventional cross-tie. The upper and lower edges of the block carry twin rows of indented teeth to allow them to slot together like Lego blocks. “Basically,” says O’Toole, “it’s a permanent formwork system where the formwork is the insulation as well for the building when completed. It comes in pre-made block form and these blocks are assembled onsite to whatever plans. It’ll adapt to basically any layout and still build up whatever type of a building is there. You put in the reinforcements and fill the wall with concrete.”
Site manager with CNC, Martin Kelly says though the product itself is more expensive than conventional building products, the fact that you can build quickly offers substantial labour cost savings. “It depends on how many gangs you have.” Says Kelly. “One gang of four would put up a block of four units in about three or four days…You pay more but you do actually save on time. This project we really only started building in August, and we have a substantial amount of structures up now.” Moreover, he points out, this method isn’t half so weather dependent. “If they were ordinary block houses, you wouldn’t have laid a block in the last three weeks. You have that factor. The rain that’s been falling here, it would have washed mortar out of every joint. So with this, you work away.”
O’Toole explains that during pouring, the forms are braced using a proprietary system. “Aluminium strongback at up to 1.8m centres with an adjustable pull/push prop that goes to that. You can push the top of the wall in or out to bring it to plum and straighten it.” The blocks are usually made to a concrete width of 150mm though 200mm forms are also used onsite; not so much for strength but to provide extra width if two precast units need to be held up by one slab. It’s a straight-forward system, says O’Toole. “All it takes is good supervision and training up the guys so that they understand how to build it and what they need to do to make the wall straight…We’ve a good number of experienced guys now and we put a dedicated engineer or site foreman on each site to look after the quality of the work.”
The prime advantage in this form of build is thermal performance. The Reward ICF delivered a U value of 0.24. Future developments of the Reward system are to bring to market a 0.2 U value product starting in March 2007. Having started small, the company has grown rapidly in recent years and is now building ten to twelve units every week. “It’s all about thermal performance and cost and speed of construction.” O’Toole asserts. “We can deliver projects quicker, and quicker is more cost effective…It reduces scaffolding time dramatically, as compared to block or timber frame construction. We’ve been told by our clients that we’re running in between; slightly more expensive than block build but cheaper than timber frame.”
All units are built using Reward Struct-sure's insulating concrete forms (aboveand below). The finished product comprises a central wall of concrete sandwiched either side by polystyrene sheeting. The building block is made from two 65mm expanded polystyrene sheets held together by a reinforced plastic rib which does the job of the conventional cross tie.
The upper and lower edges of the block carry twin rows of indented teeth to allow them to slot together like Lego blocks. "Basically," says O'Toole, "it's a permanent formwork system where the formwork is the insulation as well for the building when completed. It comes in pre-made block form and these blocks are assembled onsite to whatever plans. It'll adapt to basically any layout and still build up whatever type of a building is there. You put in the reinforcement s and fill the wall with concrete."
Additional insulation is provided by Xtratherm in Navan. They supply 125mm of Xtratherm XT/UF, a polyisocyanurate product for the floors. This delivers a U value of 0.15. Fitted in the ceilings, it targets a U value of 0.11. Windows meanwhile come from Younger Homes in Derry. Featuring low emissivity glass, the entire double-glazed unit delivers a U value of 1.4.
Two separate though linked technologies together comprise one of the central innovations in Acha Bhile: airtightness and heat recovery ventilation (HRV). David McHugh of ProAir in Tuam supplies the latter. “What you’re doing is recovering the heat from the air leaving the building and using that heat to warm the air entering the building.” Warm it, he’s keen to stress, not heat it. “Even at its most efficient, which can be as high as 92%, it is going to be seemingly cool air because if you’ve a temperature of 36 degrees and something is moving towards you at 17 or 18 degrees, it will feel cool. Even if it’s 24 or 25 degrees it will feel cool.” The unit, designed by McHugh, features the most modern fan available. It incorporates a new generation low-energy EC motor, essentially the motor equivalent of the CFL light bulb. The units themselves stand approximately one metre long, 300mm high and 500mm deep. In Acha Bhile, they’re installed within dropped roof spaces in the houses and in cupboard spaces in the apartments. “You have a network of pipes hidden away in your suspended ceiling.” Martin Kelly explains. “You also have a network of pipes coming up through your wall, and they all run up into the attic where you have your mechanical HRV unit. The ducting is hidden away, the only thing you actually see is the vent covers on your ceiling.”
McHugh says that the company’s recent rapid growth has come largely on the back of the House of Tomorrow scheme. The CNC development is their biggest to date. “We’re very happy with the professionalism of Cronan Nagle. They’re determined to get it right.” Crucially, the developer made sure to involve McHugh at design stage, ensuring that each housing unit is built to get the most out of the HRV technology. To that end, airtightness was specified at a very early stage. McHugh makes no bones about its importance in any house that features HRV. “It’s crucial really. In how many places have you felt breezes coming from behind sockets and places where you wouldn’t expect to have a breeze, once air gets into a cavity? Now the thing about these systems is there is no cavity. It’s ICF and ICF in itself would be a very airtight form of build, but they’re also making the ceiling and around the windows especially airtight. And they’re spending the money on it.”
The concealed ductwork for the Irish manafactured Proair heat recovery ventilation system, which incorporates a new generation low-energy EC motor, essentially the motor equivalent of the CFL lightbulb
The airtightness system is the German made pro clima, provided by Ecological Building Systems in Athboy. It combines a high performance vapour check membrane with proprietary airtight sealing tapes, adhesives and rubber gaskets for sealing services. Installed, the system is all about the elimination of all undesigned openings within the fabric of the building. Niall Crosson of Ecological Building Systems confirms that a high mass, high density construction like ICF is essentially airtight. Vulnerabilities arise however around reveals and at the junctions of ceiling and external joists. “The pro clima system, it’s a complete system. It isn’t just a vapour barrier and a few tapes. It takes into account design details like Velux windows or dormer windows or masonry block connections to windows, services, cables, rough surfaces or smooth surfaces. There’s a whole range of tapes and glues for every conceivable area, so it’s a total solution for airtightness. It simplifies the installer’s job and it improves the quality.” A high degree of conscientiousness from all tradespeople working with or near the membrane is essential during the build, as is ongoing quality control. An Ecological Building Systems rep visited the site on the first day of application and throughout the subsequent installations to ensure everything was carried out correctly. “That’s very important,” says Crosson, “because as good as the products are, what’s essential is they’re installed correctly because for airtightness, out of sight, out of mind just isn’t a rule you can use. Inevitably, any weak point or leakage in the building envelope will be highlighted instantaneously when the test is carried out so it’s very important to get it right the first time.”
Initial airtightness tests carried out by ODM Mechanical & Electrical Engineers just before Christmas yielded mixed results. “Windows and doors performed very well with virtually no air loss around these.” Says Darian O’Donoghue of the firm. “We had been worried about the bay window but were relieved not to find any air leakage around it. We discovered that we were losing some air around sockets and switches which hadn't been fitted properly, also around door frames on the first floor and access to the attic. Cronan Nagle are planning on fitting some extra membrane around the joists which will reduce air loss at door frames. We are very confident that we will achieve much better results once these measures are carried out. Our target value is 3 air changes per hour at 50 Pascals.” A remarkable figure, when you consider that in Britain, where regulatory enforcement leads typically to greater attention to thermal detail, the Building Regulations require 10 air changes per hour.
High efficiency condensing gas boilers provide the space and water heating for the development. The Ideal Icos HE boilers are installed in all houses by plumber Seán O’Loughlin. “They all comply with the new SEDBUK rating.” He says. “That’s the new standard for condensing gas boilers…They give a net efficiency of 90.2%.” Ideal Isar Combi boilers installed in the apartments deliver an efficiency rating of between 94.6% and 98%. “It’s a combi boiler which means that you’re not storing hot water. You’ve very small storage on the boiler but what you’re doing is you’re heating the water more or less on demand which would make it very efficient and since they’re both condensing boilers, that too boosts the efficiency.” A condensing boiler works by recovering much of the waste heat which would normally be expelled into the atmosphere by a conventional, non-condensing boiler. So why go for Ideal? “Net efficiency for the end user basically,” says O’Loughlin, “in terms of running costs and system operation.” All run on natural gas. “It’s more efficient with the natural. You’ve got no unsightly storage, you obviously don’t have the problem of changing bottles, you don’t have external pipe-work or things like that. The gas metre is just below your electric metre, all your pipes are concealed, it goes straight to boiler. Just fit it and forget it basically.” Thermostatic radiator valves fitted to all radiators also facilitate better temperature control throughout the house.
Darrian O'Donoghue of ODM Mechanical and Electrical Engineers conducting a blower door test to check the building's airtightness
All units in the development also feature the i-Homes cable management system. Householders get a range of communication innovations to facilitate basic phone and TV services along with surround sound, broadband, wireless access and PC networking.
As phase two nears completion and groundworks begin on phase three, site manager Martin Kelly explains how the company turned a problem with the site into a major advantage. The unyielding Clare limestone sitting just below the surface of the soil is now being recycled to provide building materials. “We have an onsite crusher that makes everything from four inch down to dust.” Says Kelly. “We’re about the only site around that’s completely self-sufficient in stone. We don’t buy in, we haven’t bought in any stone of any kind.”
High efficiency condensing gas boilers provide the space and water heating for the development, giving a net efficiency of 90.2%
According to site manager Martin Kelly the unyielding Clare limestone sitting just below the surface of the soil is now being recycled to provide building materials. "We have an onsite crusher that makes everything from four inch down to dust," says Kelly. "We're about the only site around that's completeley self sufficient in stone. We don't buy in, we haven't bought in any stone of any kind."
Conor Williams of CNC says right now, the company can’t quite charge a premium for the fact that these are low energy homes. As the house buying public becomes more aware of these innovations, that premium will become available, but for now, CNC have to price with one eye on basic, minimum requirement houses down the road. So if you were choosing materials and technologies purely on financial grounds, would you go this route? “You mightn’t.” Williams concedes. “But people are slowly coming round to this idea; let’s get a better house energy-wise. People are coming round to it. The market is moving up a learning curve.” With the introduction of the building energy rating, he anticipates a speedier move up that curve.
In any case, CNC have no intention of returning to conventional construction methods. The Acha Bhile development exceeds the thermal requirements of current regulations by between 40% and 45%. It’s anticipated that all future developments will push those percentages higher again. “We have another project coming on line this year.” Says Williams. “At the moment, we’re looking to try and add more energy value to that.”
“Between ourselves and ODM, we’ve built up the technical specification for the job on the energy side, and they’re working with us on our next scheme. We’re looking at more savings, more efficiency…All the bits and pieces are all being thrown up in the air at the moment, we’re just seeing what we can possibly do to make the houses more efficient. For the moment this is what we have and we’re quite happy with it.”
Selected project team members/suppliers:
Developer: Cronan Nagle Construction
M & E engineers/energy consultants: ODM
Insulating Concrete Forms: Reward Struct-Sure
Additional insulation: Xtratherm
Airtightness system: Ecological Building Systems
Heat recovery ventilation: Proair
Windows: Younger Homes
Plumbing and heating: Sean O’Loughlin
All photos by David Ruffles
- Articles
- Case Studies
- True to Form
- ICF
- clare
- cronan nagle
- heat recovery
- Ventilation
- condensing
- gas boilers
- insulated
- concrete forms
- formwork
- thermostatic
Related items
-
Why airtightness, moisture and ventilation matter for passive house
-
It's a lovely house to live in now
-
ProAir pioneers with EPDs for ventilation systems
-
Let’s bring ventilation in from the cold
-
45,000 more Irish homes face radon risk, new maps reveal
-
ProAir retooling for the future
-
Ecological launch Inventer decentralised ventilation
-
Poor ventilation a Covid risk in 40 per cent of classrooms, study finds
-
Efficient ventilation key to healthier indoor spaces – Partel
-
Evidence emerges of endemic ventilation regs breaches
-
Window-opening unreliable for ventilation, study finds
-
Study confirms “systematic inequalities” in indoor air pollution