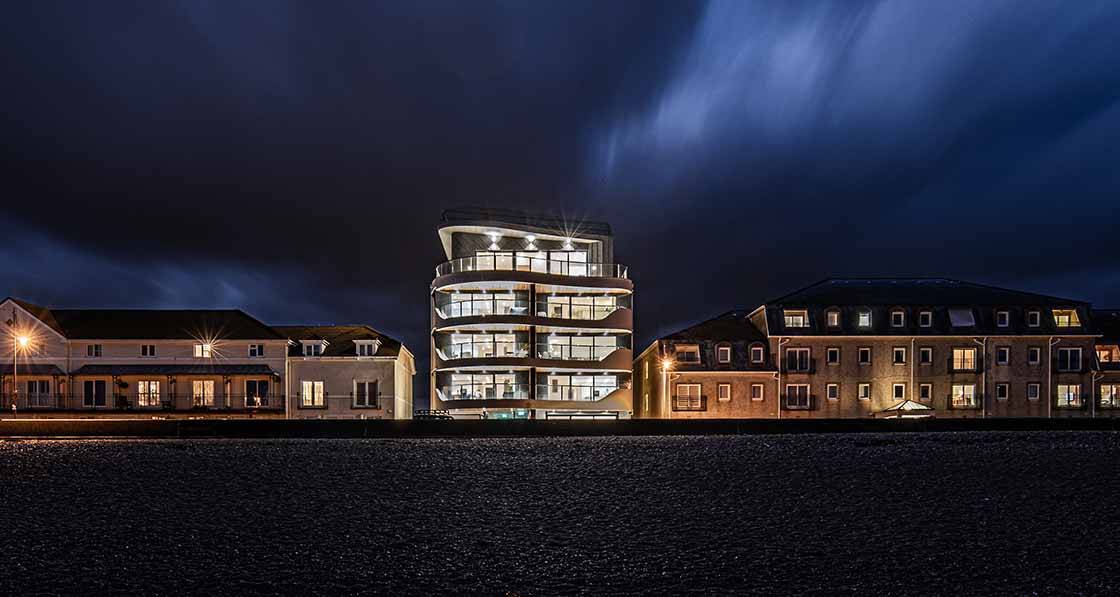
- Feature
- Posted
Sea change — luxury passive scheme on the Devon coast
Built mostly with clay blocks and sited above the sandy shores of Seaton, on the Devon coast, this new development of eight high-end apartments not only meets the passive house ‘plus’ standard — meaning it pairs the requisite ultra-low energy fabric with a substantial amount of renewable energy generation — but it also boasts serious attention to the use of ecological and healthy material.
Click here for project specs and suppliers
Energy bills £0.91 per day for all energy use*
*One apartment, based on 10 months monitored data
Building: Five-storey block of eight luxury apartments, 101 m2 to 138 m2 each
Location: Seaton, Devon
Standard: Passive house plus certified
The county of Devon has been a hotspot for passive house development for more than a decade. Exeter City Council, in particular, has backed numerous schemes, including affordable housing schemes and a leisure centre with a swimming pool. Recently, the £3 million Seaton Beach development on Devon’s coast became the first multi-unit residential building in Britain to achieve passive house ‘plus’ certification. The project also won awards for best sustainable residential development in the UK and best apartment in Devon (for its top-floor penthouse) from the International Property Awards.
The presence in Exeter of passive house architects, Gale & Snowden, has helped to accelerate the trend for large scale passive house development in the area, and the five-storey Seaton Beach was no exception. Although the original design was produced by a different architect, Gale & Snowden later worked on the passive house elements.
At the outset, however, Mike Webb, managing director of Seaton Beach Developments Ltd (SBD), had not intended to build to the passive house standard. Webb simply wanted to develop a block of eight luxury apartments with sea views in this small coastal town, near Lyme Regis.
This article was originally published in issue 34 of Passive House Plus magazine. Want immediate access to all back issues and exclusive extra content? Click here to subscribe for as little as €10, or click here to receive the next issue free of charge
“Seaton Beach was a rare chance find for a speculative development. We were visiting friends in Devon in May 2015 and happened to walk past a large Victorian property for sale on the sea front. We quickly formed a development company with a friend who backed the venture, and bought it for £515,000 two weeks later,” says Webb, who lives in Tenbury Wells, in Worcestershire, where he and his wife own rented properties and a solar installations company.
The rather downtrodden and unremarkable old building was knocked without issue, and Webb’s co-directors, Mike and Anne Dowling, selected Exeter architects Clifton Emery Design to produce plans for the new tower.
Webb was happy with Clifton Emery’s design, describing it as “beautiful, curved and artistic”, but the local planning officer was less enthusiastic and, consequently, the planning committee denied permission by one vote in July 2016. Their concerns centered on the height and depth of the building and its relationship to the properties adjoining the narrow site. But Webb believes they “failed to see the regenerative potential”.
The battle for planning permission went on for several months. In the end, SBD turned to the local design review panel for support. The panel endorsed the scheme and, finally, East Devon District Council approved planning in November 2016.
At this point it became clear that the south-facing orientation and form factor made it possible to build to the passive house standard. “Over the years I’ve become passionate about passive houses and it seemed a great way to leave a legacy to the earth,” Webb says. “I realised this development was the best chance I would ever get to do that.”
To be confident of achieving the standard, Webb needed a practical specialist in passive house design to complete the work started by Clifton Emery. In February 2017, when Webb met architect Tomas Gaertner – the man he dubs “the German genius” – he knew he had found the right man.
Gaertner was at that time a director at Gale & Snowden. He had trained and worked as an architect in Germany, the birthplace of passive house. But he had only designed a handful of residential passive houses there before moving to the UK in 2007. Gartner’s arrival in Exeter proved timely, as his skills in energy efficient design were in great demand.
The influential Emma Osmundsen, managing director at Exeter City Living group — the local authority’s development arm — provided the political clout that made a lot of passive house development possible. Gaertner’s first passive house scheme in Exeter was the influential Knights Place affordable housing scheme, in 2010. Now working for SE3Design, he has continued to collaborate with Osmundsen, mainly on larger commercial developments (Gaertner left Gale & Snowden part way through this project and Lawrence Millyard took over as project architect).
Gaertner did not need to make major structural changes to Clifton Emery’s design for Seaton Beach. His main role was to take charge of the passive house detailing. “There were no drastic changes, although the final design was a bit higher to allow for [more] insulation in the penthouse, and to make space for the roof terrace,” he says. Clifton Emery’s plan, however, had proposed using a concrete frame for the entire structure, but Gaertner says this would have been more expensive and made the detailing of airtightness junctions more difficult.
Instead, Gaertner proposed building the ground floor in concrete, using poroton clay blocks from the first to the third floors, then installing a timber frame for the penthouse on the fourth floor.
He explains that with a concrete frame, structural elements such as columns and floors are separated from the space-enclosing elements (i.e., the external walls) by movement joints and gaps between infill wall panels and ceilings, to allow for deflection.
1 Work begins on the project with the knocking of the existing structure, a large, unremarkable Victorian property on the seafront; 2 & 3 construction under way of the ground floor structure, which features 300 mm Dow XPS insulation; 4 the bulk of the structure was built using poroton clay blocks, which are aerated and thus provide insulation; 5 plastering of this blockwork internally provided a straightforward way to make the walls airtight; 6 windows are Norrsken composite timber and marine grade aluminium triple glazed units, with solar shading provided by the defining aesthetic feature at Seaton Beach – the building’s generous curved sea-facing balconies; 7 the fourth floor penthouse apartment was built with a timber frame, and steps back from the rest of the building below to reduce its weight; 8 ductwork for the Genvex combined ventilation and air-toair heat pump, installed in each apartment; 9 the roof of the building, five floors up, is insulated with Warmcel cellulose insulation and finished with a Bauder membrane; also seen are the openings for two Velux tripleglazed rooflights
For airtightness, this would require flexible junction details using membranes and tapes. “Tape details — especially in a wet, dusty construction — are higher risk as substrates are often not adequate and tapes are prone to delaminate and fail,” Gaertner says. “The block construction allowed for a simple plaster detail for airtightness without any junction tapes.”
The poroton blocks are also aerated and thus provide insulation, which appealed to Gaertner as it meant he could avoid the use of plastic insulation for most of the building. The top floor steps back from the rest of the building below, so to reduce its weight and allow it to be built without additional steel beams or lintels, it was built with a timber frame.
Gaertner’s approach to passive houses has been influenced by building biology, the construction philosophy that emerged in Germany in the 1960s. “It’s an attempt to look at the living environment more holistically. We consider the impact of the materials on both the living environment and the ecological environment. We try to be energy efficient and use renewables, but at the same time not compromise on materials. It’s about avoiding poor air quality and mould. We also follow the World Health Organisation’s standards for healthy indoor environments,” he says.
At Seaton Beach, for example, the use of monolithic clay block follows the principles of building biology. “It’s highly hygroscopic [meaning it can absorb and release moisture] and moves moisture around in the building, which will help to regulate internal humidity,” Gaertner says.
Another feature of Seaton Beach in keeping with building biology was the use of AURO natural mineral paints. “They contain no additives, such as fungicides. The higher lime content means the paint acts as an anti-fungal and doesn’t create a chemical problem. In contrast, when you use non-permeable emulsion paints, the moisture cannot move into the walls quickly enough. The only way to get rid of it then is with ventilation. It’s especially important in winter to have the buffering potential in the walls.”
Following building biology principles is easier in the south west of England than in some other parts of the UK because the region has a mild climate, Gaertner says. This means it’s possible to reach the passive house standard with less insulation.
“It’s inevitable when you push for higher insulation levels, especially on commercial developments, that you end up using some petrochemical materials because the projects otherwise become too expensive,” he says.
“With the milder climate, we can get away with much less insulation… [the poroton walls here for example have a U-value of 0.26).” Rather than install a lot of insulation at Seaton Beach, Gaertner maximised the free energy savers from the block’s good orientation and form. It was especially critical to pay attention to the window detailing. The original design had curved triple glazed windows, which had to be replaced with straight-edged ones. The biggest problem with the original design was a three-metre-high, three-sided glass window in the penthouse. It provided beautiful sea views but would have acted like a greenhouse. Gaertner designed a lot of solar shading to prevent overheating, reducing the glazing to a more sensible proportion while retaining the views.
That solar shading was provided by the defining aesthetic feature at Seaton Beach – the building’s generous curved sea-facing balconies from Surrey-based specialists Balconette – including curved glass balustrades and marine grade chrome handrails to make the most of the sea views.
This feature serves as a striking counterargument to the notion that the passive house standard, which is easier to achieve with simpler, box-like forms, leads to prosaic buildings, even where the envelope remains box-like, as in Seaton Beach. Good architecture embraces restrictions. With a little design ingenuity, and the use of Schoeck Isokorb thermally broken balcony connectors, a box-like building is wrapped in beautiful yet functional curves, while enhancing rather than compromising the building’s energy performance.
A mechanical ventilation system further enhanced energy saving. “All these various measures meant we were able to compromise on the U-values and use materials with benefits for the environment, ecology and health,” he says. Each apartment has a Genvex Combi 185 BP combined ventilation and air-to-air heat pump, which can heat up 185 litres of stored water. To back it up, there are three electric towel rails and two wall-mounted electric radiators in case of extreme weather.
On the roof, there are 49 solar PV panels with a maximum output of 16kW and an annual yield of 14,234 kWh. The addition of the solar panels along with the Genvex heat pump took the PHPP calculations into the “plus” category.
Webb attributes the success of the Seaton Beach project to what he calls “education and collaboration”. The “collaborative” element came from the close cooperation of all parties, many of whom had already worked together on other passive houses. Meanwhile, the “education” of the on-site workers in how to build passive houses was important because the building contractor Classic Builders SW was not an experienced specialist in the field.
At the start, Webb took a team of 30 building workers for a day’s training with the passive house specialist Peter Warm, in Plymouth. “It taught them everything they needed to know about building passive houses, which put everyone’s minds at rest as they were under a lot of pressure to deliver,” he says. Additionally, Robin Pike, the Classic site manager, took on the role of airtight champion and delivered some exceptional airtightness results. Webb also engaged quantity surveyors Randall Simmonds and structural engineers StructureHaus, who had previously worked with Tomas Gaertner in Exeter.
Despite the well-informed team, the project overran by six months. It was completed after 18 months in October 2019. Some of the delays were down to the strong, squally winds that blew in from the sea. “One example was when five articulated lorries arrived from Bristol in March last year carrying concrete planks, but we had to send them back as it was too windy to lift anything,” Webb says. “Using higher quality products drove up the price and led to time overruns, but we wanted to use the best materials, such as the zinc shingles that clad the penthouse.”
Webb already had several years’ experience of working with renewable technologies and qualified as a passive house consultant during the build. He acted as clerk of works, travelling regularly from Worcestershire to Devon.
In July 2019, one of the apartments became a show home and in August, the first permanent resident moved in.
Webb also decided in January 2020 to turn the penthouse apartment into an art gallery, partly to showcase local artists, but also to attract potential buyers. To date, Webb has sold five of the eight units, and another potential sale is on hold because of the fallout from Covid-19. The penthouse was put on the market in time for summer, but again it had to be postponed due to Covid-19.
Once the Covid-19 crisis is over, Webb will resume his plans for more passive house developments near his home in Worcestershire. He also acts as a consultant for potential passive-house builders. “With everything I’ve learned on the Seaton Beach project, I could save people a fortune on architects’ fees and help them work closely with the designers of their homes,” he says.
Selected project details
Client: Seaton Beach Developments
Architect: Gale & Snowden
Initial/planning architect: Clifton Emery Design
M&E engineer: Gale & Snowden
Passive house & building biology
consultants: Gale & Snowden
M&E contractors: Total Home Environment & Fords of Sidmouth
Civil & structural engineer: StructureHaus
Main contractor: Classic Builders (SW) Ltd
Quantity surveyors: Randall Simmonds
Mechanical & electrical contractor: Fords of Sidmouth
Airtightness tester: New Barton Contracts
Heating & ventilation system: Total Home Environment
Passive house certifier: WARM
Timber frame: Allwoods
Cellulose insulation: Warmcel, via Smart Construction SW
External wall insulation: McCarthys Contractors Ltd
Poroton blocks: Wienerberger
Thermal break: Schoeck
Balcony systems: Balconette
Floor insulation: Dow
Airtightness products: Green Building Store
Airtight OSB: MEDITE SMARTPLY
Windows & doors: Norrsken
Roof windows: Velux
Shading: RSL Roller Shutters
Zinc cladding: Pace Roofing & Cladding
Carpets: Axminster Carpets
Roofing: Bauder
Solar PV: Wind & Sun Ltd
Lighting: Fords of Sidmouth
In detail
Building type: Five-storey new build apartment block of 8 units with 870.7 m2 total floor area. Apartments ranging in size from 101 m2 to 138 m2.
Location: Seafront site in Seaton, Devon
Completion date: November 2019
Budget: £3.5 million (inc. site purchase of £515,000)
Passive house certification: Passive house plus certified
Space heating demand (PHPP): 12 kWh/m2/yr
Heat load (PHPP): 11.2 W/m2
Primary energy demand (PHPP): 100 kWh/m2/yr
Primary energy renewable (PHPP): 54 kWh/m2/yr
Overheating (PHPP): 1% of year above 25C Number of occupants: PHPP based on 20.1. Actual to date 6-10 as some are second homes.
Airtightness (at 50 Pascals): 0.5 ACH
Energy performance certificate (EPC): All units A-rated (97-99)
Measured energy consumption: Unit X is occupied full time by a single person and from 4 August 2019 to 4 June 2020 (10 months) total electricity imported was 2,009 kWh. A further 744 kWh was used direct from the 2 kWp solar PV array. When PV production exceeded the apartment’s demand, a further 1,184 kWh of PV produced electricity was exported. The other apartments & the communal areas can use this first, before being exported to the grid. From the 10 months actual consumption (and applying May data for June and July), an annual use of 2,753 kWh can be forecast. The Genvex Combi MVHR & heat pump unit in Unit X uses 1,457 kWh/yr (121 kWh per month avg). The remaining 1,295 kWh includes 3 x towel rails which are designed to meet 50% of heat demand. See below for solar PV electricity production.
Energy bills: For Unit X above, the total annual energy costs are £333. Thermal bridging: All thermal bridges were numerically modelled to demonstrate compliance with the passive house standard.
Ground floor: 250 mm compacted base followed above by 25 mm sand blinding, 1 mm DPM, 300 mm Dow XPS insulation, separating layer, 200 mm reinforced concrete slab, 10 mm acoustic mat & 65 mm screed. U-value: 0.141 W/m2K
Walls
Ground floor: 16 mm Alsecco render externally followed inside by 200 mm Neopor EWI, 215 mm concrete block, 15 mm plaster. U-value: 0.194 W/m2K
First to third floors: 16 mm Alsecco render externally followed inside by 365 mm Poroton T10 block by Wienerberger, 15 mm Plaster. U-value: 0.259 W/m2K
Fourth floor: Factory-built timber frame by Allwoods with marine grade zinc cladding externally on 22 mm ply, followed inside by 50 x 50 mm treated battens and counter-battens, pro clima Solitex Plus membrane, 12 mm OSB board, 180 mm Warmcel-filled TJI stud, 15 mm taped and sealed Smartply Propassiv, 50 mm service cavity and 15 mm plasterboard & wet plaster skim internally. U-value: 0.141 W/m2K
Roof: Factory-built timber frame by Allwoods with Bauder membrane externally on 22 mm ply, followed inside by 50 x 50 mm treated battens, 22 mm ply, 310 mm Warmcel-filled TJI stud, 15 mm taped and sealed Smartply Propassiv, 50 mm service cavity and 15 mm plasterboard & wet plaster skim internally. U-value: 0.081 W/m2K
Windows & external doors: Norrsken composite timber and marine grade aluminium triple glazing, with argon filling and an overall U-value of 0.82 W/m2K average.
Roof windows: 3 x Velux GGU triple glazed roof windows. U-value: 1.01 W/m2K
Heating & MVHR combined system: Genvex Combi 185 BP MVHR unit combined with micro air source heat pump (330W) with 2 x 71W fans provides 50% of heat demand. This is topped up by 3 x 150W direct electric towel rails & then for extreme weather 2 x Dimplex wall-mounted radiators. The Genvex Combi unit also heats 185L of stored hot water & also has a 1 kW immersion for faster recovery. The Genvex Combi 185 is Passive House Institute certified to have heat recovery efficiency of 71.2%.
Water: Above ground rainwater harvesting tanks, low flow fixtures in all areas.
Electricity: 49 panel REC 320W solar photovoltaic panels (covering 80.2 m2) with maximum output of 16 kW & annual yield of 14,234 kWh. The array feeds the 8 x 2 kWp inverters, one for each apartment. Sample unit: Based on the first 10 months data – again with May data applied to June and July - Unit X is projected to produce 2,034 kWh of electricity, of which 1,184 kWh is exported to other units/ communal facilities before any excess is exported to the grid. The full building receives a £1,000 feed-in tariff each year which is used to subsidise residents’ service fees.
Green materials: Recycled wood from demolished house used for pergola, stone from demolition used for boundary wall, Warmcel cellulose (recycled newspaper) insulation, Auro natural paints, 100% wool carpets locally sourced from Axminster carpets, all timber from PEFC certified sources, clay blocks recyclable at end of life.
Image gallery
https://passivehouseplus.ie/magazine/feature/sea-change#sigProId1e1d7c5e29