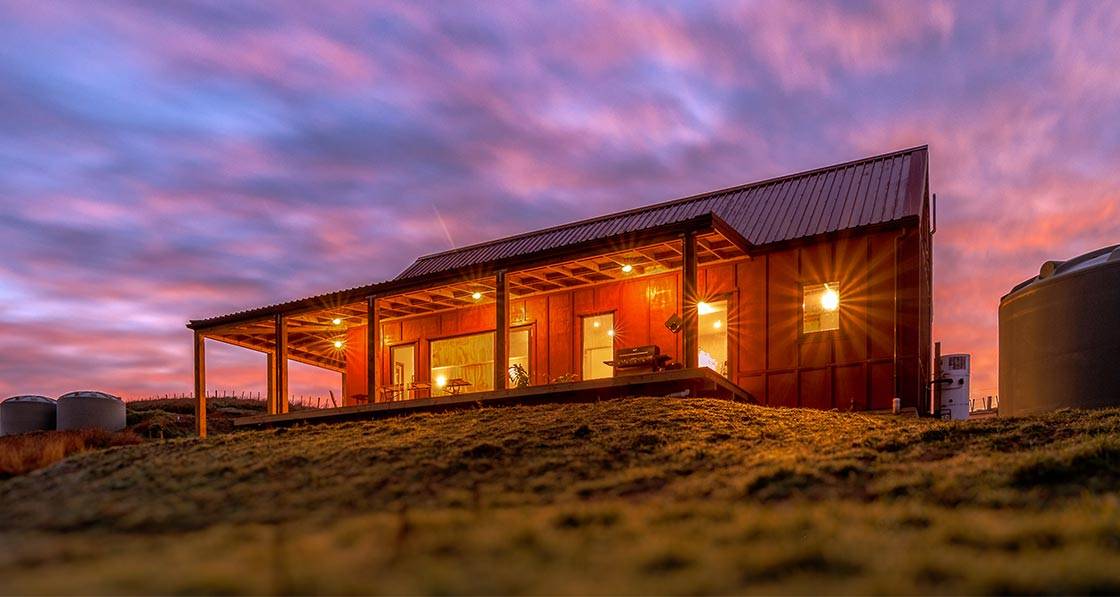
- Big picture
- Posted
Big picture - New Zealand rural passive home
In the first installment of a brand new photo essay feature, in which we profile passive houses and other eco-buildings from around the world, architect Joe Lyth writes about how the aesthetic of simple backcountry cabins inspired the design of his rural home on New Zealand’s North Island.
1. Envelope first
This article was originally published in issue 42 of Passive House Plus magazine. Want immediate access to all back issues and exclusive extra content? Click here to subscribe for as little as €15, or click here to receive the next issue free of charge
The project came about as a result of our kids getting sick in our standard, too-cold-or-too-hot, mouldy New Zealand house, and my wife Sarah and I being unable to watch any longer. We decided to put our (minimal) money where our mouths were, to prove that high performing, healthy homes can be achieved at standard budgets, while still being beautiful places to live.
Cost was the key constraint. As first-time buyers with a small deposit, prioritising and compromising were essential. An envelope-first strategy was decided on to prioritise performance: site specific insulation, good airtightness, great windows and doors, no thermal bridging.
We would develop the interior as a family once we moved in. What resulted is an unpretentious, passive house certified home that blends into its rural context, while keeping its inhabitants warm, dry and healthy year-round.
The initial design was a single-storey home that could be extended into the roof space later. But to get funding from the bank, however, we ended up having to build the first-floor bedroom and bathroom to increase the value of the house to match the build cost, but without running up the construction cost – a challenging exercise and negotiation with the contractor!
2. Of its place
Our search for a plot of land took us about 45 minutes north of Auckland, where we found a site barely within our budget.
The northwest facing saddle here has expansive views of the Makarau River valley, and the surrounding area consists of weathered rural infrastructure, traditional villas, and a growing number of new homes, all embedded into a mixture of pasture, pine wood and native bush.
The exposed site is both baked by the sun and battered by rain and winds, so the proposal had to respond to a range of environmental factors to ensure durability, performance, and habitability.
The design developed with the location and took precedence from both its rural context, and our love of the simple robustness of backcountry huts. Lower Saddle sits comfortably into its surroundings like it was always there – belying the high-performance nature of the project. The response included careful orientation to the view, the sun and the prevailing wind, with thoughtful positioning of openings, north and western overhangs, and exterior shading.
3. High performance Lego
Cost and performance were our priorities, and to minimise thermal bridging and embodied carbon, steel and concrete were out. Due to the sloping site a suspended timber floor on piles with sheep’s wool insulation was chosen over a carbon-hungry concrete slab, and structural insulated panels (SIPs) were selected for their thermal and airtight qualities, with prefabrication reducing waste and construction time.
The panels were cut to shape in the factory from the building information model (BIM). They arrived on site all numbered, and went together like a Lego set. The walls took a couple of days to install, then the mid floor and gables, before the roof went on in a day and a half. The project achieved a final blower door test result of 0.375 air changes per hour, so the passive house airtightness target (0.6) was more than achieved.
4. Wider environment
As well as being energy efficient, we aimed to minimise the project’s impact on other resources. Large rainwater tanks and efficient sanitaryware ensure ongoing water resilience, and all sewage and sanitary waste is treated on site, in turn watering and fertilizing a growing orchard. A solar hook-up is included, and we plan to install PV in the medium term when we have the budget.
The site was open pasture when we purchased it, and is slowly being developed based on permaculture principles, with some areas being replanted with native trees, some left to re-wild, and the rest being developed into food production and a food forest to feed us, and hopefully eventually, the wider community.
5. Interior environment
All buildings need adequate ventilation to ensure good indoor air quality, but opening windows, which is relied on in NZ, only works some of the time. Mechanical ventilation works all the time, with openable windows for additional user comfort and control.
We installed a ducted mechanical ventilation system with heat recovery from Stiebel Eltron in the good-sized laundry. In the full height mezzanine I designed in a bulkhead down the spine of the building to accommodate the ducting, and to make it easier and more cost effective to install. We have been monitoring the interior with Tether environment sensors and the system has performed perfectly, with the interior almost always between 18-24C with no active heating or cooling, constant levels of humidity, and very low CO2 readings.
6. Windows, windows, windows
Standard window frames in NZ are solid aluminium, and double glazing is a relatively new thing, so anything of reasonable performance has a cost premium. We ended up working with a company to import our windows from Poland for a 40 per cent cost saving including shipping and import, with triple glazing for thermal performance and sound, timber frames for look and performance, and aluminium facings externally for durability.
Due to shipping issues and Covid they were a month late, and the process had some valuable lessons for me going forward, but they fit, the glazing performs perfectly, and the timber looks great.
7. Space and form
To keep costs in check the design utilises a simple, compact form and effi cient design of spaces to reduce the building footprint, simplify the construction, and mitigate the volume of materials. Every inch of space inside works hard, and the covered decks to the north and west provide further living space outside.
Visual connections between the rooms create a feeling of space with a double height living space and overlooking mezzanine, and high-level windows and ‘arrow slot’ openings into the upstairs rooms - they remind me of medieval castles, where a little window high in the wall of a banqueting hall would often be the most intriguing part.
8. Materials with character
Painted plywood cladding and metal roofing were selected externally, with a scoria red finish reminiscent of tramping huts and embodying the local rural vernacular.
Internally the SIPs were painted as opposed to lining them, reducing trades and cost. Plywood linings were selected for interior walls — lower carbon than plasterboard, and easier for sanding off children’s drawings.
We made the plywood kitchen, cast concrete sink and counter, and copper splashbacks ourselves, all materials that gradually gain a patina and character over time. Native Totara from a friend’s farm further north was milled into trims and skirtings. The plywood grain and textured SIPs that form the spaces are broken up by brightly painted doors, each a different colour to add splashes of joy.
9. Part of the family
We moved in at the end of May 2021 before the exterior was finished, and a couple of weeks before the hot water heat pump system was installed. (The house has no space heating system beyond a small panel heater, which we’ve turned on for an hour or two all year. We’re looking into electrical underfloor heating eventually, but we barely need it.) Since then, we’ve been developing, dressing and finishing the house together as we learn how it functions for us.
Moving into a ‘shell’ has given us the chance to experiment – I’m installing Woodtex panels between beams in the downstairs bedrooms for sound attenuation, and for texture. To keep costs down the finishing of the plywood was left to us, so we’re slowly filling, sanding and varnishing the interior walls.
The house is truly growing with us.
10. For the future
New Zealand has some of the lowest performing, unhealthiest, yet most expensive housing in the world. Lower Saddle shows that this doesn’t have to be the case — all Kiwis can have healthy, affordable homes with low operating costs, and a light impact on the planet.
The project balanced priorities with what could be added or upgraded later – a kitchen is easier to upgrade than your windows and walls, for example.
In following an envelope first approach, the high-performance home provides a healthy enclosure, with an interior that can be developed alongside our growing family, delivered on a budget lower than most minimum code homes. Materials and construction methodology reduced the amount of embodied carbon and construction waste through prefabrication, setting out of materials to mitigate waste and minimise cost, and ongoing reuse of offcuts and materials in the project.
11. Performs as designed
Since we moved in the house has absolutely ‘performed as designed’ with energy bills of $100-$130/month for everything (around 40 per cent lower than a standard NZ home, which would usually also include gas too), while maintaining comfortable temperatures year-round with no active heating or cooling, and the children’s respiratory issues have disappeared.
12. A learning resource
Since completion we have been able to grow into the home, but also use it to help educate others (thanks to Sarah’s incredible patience!). It’s been part of the international passive house open days, and the Superhome Movement tours, and will be again this year; I’ve used it as a vehicle to explain building performance in presentations to universities and product suppliers, and it’s fantastic to be able to invite clients up to show them what a passive house looks, feels and sounds like.
As a model for other homes in NZ applied at scale, this would provide a warm, dry, healthy and affordable home for all New Zealanders, with minimal ongoing maintenance and operational costs; and as our home, we couldn’t be happier.
Embodied carbon excellence
The project has achieved excellent embodied carbon results, based on analysis by Elrond Burrell of Via Architecture, performed using PHribbon. It blitzed the RIBA 2030 Climate Challenge target for embodied carbon of 625 kg of CO2 equivalent per square metre, scoring a miniscule 120 kg CO2e/m2, and achieved an A+ for upfront carbon and A++ for embodied carbon on the LETI scale.
The house is below the BRANZ detached house (embodied and operational) carbon budget for a 2C warming limit.
How did the house achieve such low figures? A combination of factors contributed, including the lack of concrete for foundations or superstructure, and the lack of rendered block or brick cladding, and the lack of a heating system. One other key factor played a part: the timber used for the structure was covered by an Environmental Product Declaration (EPD) from the Wood Processors and Manufacturers Association, which included New Zealand-specific figures for the end of life of timber. Because the timber was assumed to be landfilled upon the building’s eventual deconstruction and – unlike the RICS methodology in the UK – the majority of the timber is assumed not to biodegrade as methane – a substantial amount of CO2 sequestered in the timber is assumed to remain sequestered.
This hints at an inconvenient truth about life cycle assessment: if that timber had been assumed to be salvaged and reused in the future, the sequestered CO2 would have passed outside of the boundary conditions of this building’s life cycle assessment and onto the next use – giving the same embodied CO2 result as if the timber had been incinerated. Had that been the case, the building would still have achieved a superlative score of 238 kg CO2e/m2.
Joe is a registered architect and certified passive house designer at Respond Architects in Takapuna. Originally from North Yorkshire in the UK, Joe studied and worked in London from early 2007 before making the move to New Zealand in 2016 with his wife Sarah, and has since welcomed three little Kiwis into the world.
He is especially passionate about high performance and healthy buildings, and finished his own passive house certified home on a tight budget in May 2021, to show healthier, affordable buildings are possible for everyone in New Zealand.
https://passivehouseplus.ie/magazine/big-picture/big-picture-new-zealand-rural-passive-home#sigProId28a3705abb