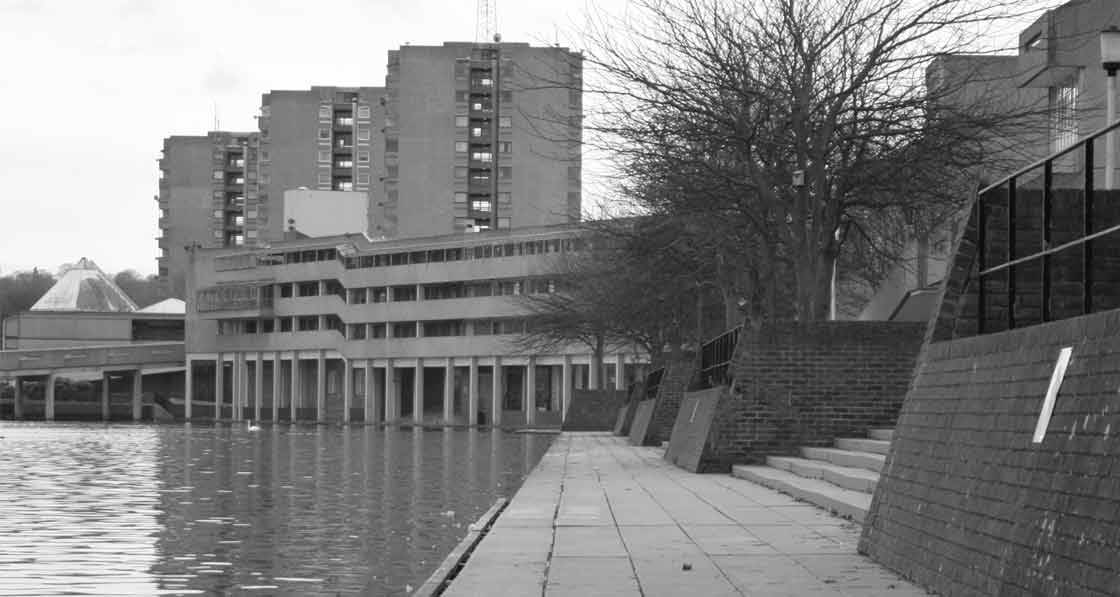
- Blogs
- Posted
Breaking the mould in Thamesmead
The net effect of poor insulation levels, underheating and under-ventilation in buildings poses a major public health threat. Peter Rickaby describes one pioneering London project that’s taking a practical, methodical – and scalable – approach to solving the problem.
This article was originally published in issue 25 of Passive House Plus magazine. Want immediate access to all back issues and exclusive extra content? Click here to subscribe for as little as €10, or click here to receive the next issue free of charge
One day two years ago I visited Thamesmead for the first time. Architecturally, it was an eye-opening experience. Built in the 1960s and 1970s by the GLC, this huge estate in south-east London, if overlaid on central London, would stretch from St Paul’s Cathedral to Marble Arch. It is home to thousands of households and has all the iconic features of mid-twentieth century social housing: a line of high-rise tower blocks with views over the Thames estuary; medium- rise deck-access blocks, one of them half a kilometre long; courtyards, alleyways, a ribbon of parkland; and a lake surrounded by housing, which featured evocatively in the original architects’ drawings. Thamesmead pre-dates the Thames barrier, so circulation was originally above potential flood level, via raised decks and walkways that are still in use; the ground level accommodated only garages, now colonised by residents’ downward extensions. The construction is reinforced concrete with pre-cast concrete panels; a few of the original metal-framed single glazed windows remain.
Thamesmead was the perfect setting for Stanley Kubrick’s 1971 film of Anthony Burgess’s dystopian novel A Clockwork Orange. Not much has happened there since then. Now Crossrail (the Elizabeth Line) is bringing investment to Thamesmead, land values are rising, old homes are being demolished, new homes are being built. There is an ambitious regeneration plan for the area, and a legacy of problems.
I was invited to Thamesmead that day by Peabody’s sustainability manager. Would I like to join a team to develop and deliver a condensation, damp and mould (CDM) strategy for Thamesmead? This request proved to be not only an opportunity to make a positive difference to people’s homes, but a big challenge. Subsequent visits to Thamesmead homes revealed the worst condensation and mould I have seen in thirtyfive years as a consultant: homes with mould covering walls and ceilings in living rooms and every bedroom; bathrooms that at first looked as though they had been painted black; parents cleaning mould daily with bleach and trying to keep their toddlers away from both; even in summer, mould-stained paintwork everywhere.
How could social housing be in this condition in the UK in the twenty-first century? Peabody recently acquired the estate through a merger with Gallions HA, who had themselves acquired it through stock transfer. Other than new windows there has been almost no investment in Thamesmead for forty years: the most significant change was replacement of the visionary but inefficient and worn-out district heating system with individual gas-fired central heating systems. Before that change most residents were warm and dry, perhaps over-heated; since then many of them have been overtaken by fuel price rises and become fuel-poor, and their poorly insulated, underheated and under-ventilated homes have become cold, damp and mouldy.
Thamesmead was the perfect setting for Stanley Kubrick’s 1971 film A Clockwork Orange. Not much has happened there since then.
For the last two years our team of Peabody staff, surveyors, consultants, contractors, suppliers and installers has walked the length and breadth of Thamesmead several times over. We have made room-by-room CDM and ventilation surveys. We have risk-assessed the stock, classified homes into three levels of mould risk and devised three levels of intervention. We have initiated a programme of energy advice that will eventually reach every household. We have applied mould washes, replaced boilers and undercut doors.
We have tested and adopted a smart heating controller that not only reduces resident’s fuel costs but also allows us to monitor conditions inside their homes, before and after improvement.
We wrote a challenging ventilation specification that only one ventilation supplier could meet, and they have configured their demand controlled mechanical extract ventilation (MEV) system to each of the dwelling types on the estate. We have tried (and failed) to cut holes for ventilation ducts through 190mm thick reinforced concrete floors. We have re-routed ventilation ducts to avoid penetrating panels containing asbestos.
We have installed external air inlet grilles at height without scaffolding or ladders. We have used data from smart heating controllers to target homes for improvement, to monitor the effectiveness of interventions, and to brief the energy advisor. We have also rigorously evaluated everything we have done. More subjectively, I recently visited some of the homes that were improved last year, to reassure myself that the mould has not returned this winter.
Naively, I thought at first that Thamesmead’s mould problem must be unique, but many other, similar examples in the UK and Ireland have come to my attention. The award-winning Thamesmead CDM strategy has established a model of best practice. It demonstrates the strength of a dedicated, multi-disciplinary team taking an evidencedbased, systematic approach and using new technology to address a wicked problem that has frustrated landlords and householders for decades. I am proud to be part of Peabody’s team tackling the CDM problem at Thamesmead, but I am ashamed that there is such a problem to be tackled, in Thamesmead or anywhere else.