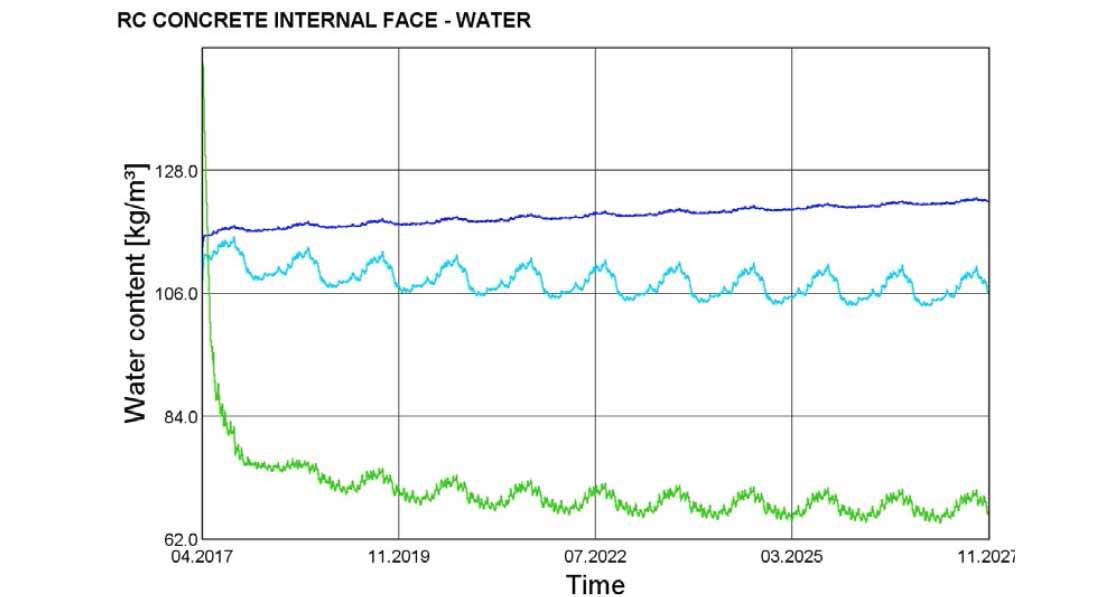
- Feature
- Posted
Basements in low energy buildings - key issues to avoid moisture and heating problems
Where basements are present in low energy buildings, they can prove a weak spot without particular care and attention, as Passive House Association of Ireland board member John Morehead of Wain Morehead Architects Ltd explains.
This article was originally published in issue 36 of Passive House Plus magazine. Want immediate access to all back issues and exclusive extra content? Click here to subscribe for as little as €10, or click here to receive the next issue free of charge
Our temperate climate in Ireland can let us off lightly in achieving passive house levels of performance with above ground dwellings. However, once we build below ground, our advantages are lost due to the condensation risk caused by humid exterior conditions.
Whether commercial or domestic, achieving NZEB with basements in Ireland challenges the design team with a series of sometimes conflicting demands that must all be fully addressed. With basements, thermal excellence is the new kid on the block that structural, moisture, radon and ventilation demands need to befriend.
Basements in North America and Northern Europe are commonplace and evolved from simple foundation systems to the provision of storage and conditioned space.
Insulation of basements took hold in the 1980s as 25 per cent of building energy losses were understood to be through these areas. Although exterior insulation clearly had both technical merit and reduced risks, the cheaper more convenient approach of using interior insulation became common and was associated with many failures.
Heat and moisture in basements
Heat transfer in basements is generally outwards, vapour transport generally inwards, except in summer. Only when moisture transfer within basements is understood, should the appropriate thermal solutions be considered.
Moisture from ground is in the form of liquid (saturated) and vapour. It can enter via breaches and through capillary action. Vapour is also introduced into the construction by air leakage and by vapour diffusion (higher to lower pressure) through the fabric itself.
C35/45 concrete at construction stage holds 116 kg/m3 of moisture1. Low water content mixes are preferable. Concrete can absorb and retain significant moisture, but the incorrect placement of vapour tight materials can upset the balance.
Once insulation is placed on the warm side of a concrete retaining wall, the risk of condensation increases as the concrete surface temperature lowers. Moisture permeable internal insulation and finishes permit the natural drying of the concrete retaining wall to the interior once mould-inhibiting materials are employed.
The use of internal thermal solutions in basement construction requires a much higher standard of vapour control to be practical, whereas externally insulated basements, with the correct barrier protection placement and drainage strategies, make sense.
Some mineral board solutions applied to the interior are particularly useful in tandem with other moisture and vapour control techniques in the transitional areas such as where basement walls break ground to meet the upper walls. Below this level systems with better vapour permeability and control should be the first choice.
Graphs generated by Wain Morehead Associates using the WufiPro dynamic hygrothermal simulation tool calculate the potential consequences in terms of relative humidity and water content at the internal face of a reinforced concrete basement wall, using different approaches to insulation. Relatively humidity and water content both end up significantly lower with the external XPS (green) than the internal closed cell (purple) or internal mineral (blue) insulations.
Guidance and achieving NZEB
The lack of contemporary guidance available to the Irish practitioner on basements is worrying. Indeed, our academics should be encouraged to study issues of moisture and thermal management as a matter of urgency. Our own research in the area has been supported by empirical measurement on site, supported by hygrothermal analysis using Wufi Pro, with site-specific climate data.
The standard BS-8102:2009 (Code of practice for protection of below ground structures against water from the ground) offers guidance on preventing the entry of water from surrounding ground into a structure below ground level but fails to address vapour transport mechanisms or condensation in any depth. It is civil engineering focused and discusses external moisture ingress potential, drainage and mitigation strategies.
This iteration identifies three classes of external moisture protection of which types A (barrier) and C (drained) or a combination may be considered applicable for NZEB projects, but alternative syphon drainage systems need to be considered so as not to compromise air permeability requirements.
The standard advises early engagement of a well-informed multidisciplinary team including tanking specialists in the design process.
The document advocates contingency planning and acknowledges that defects may occur. It promotes the concept that feasible remedial measures be integrated.
Although not limited to Parts A, C, F and L of the building regulations, these are the primary focus. Radon protection must not be overlooked.
Thermal performance
Once the building form has been determined, try a quick DEAP 4.2 (Dwelling Energy Assessment Procedure) spreadsheet assessment to see how the building complies with Part L and in particular to the MPEPC (maximum permitted energy performance coefficient) and MPCPC (maximum permitted carbon performance coefficient). In parallel, to assess the design performance of the building, assess the performance in the Passive House Planning Package (PHPP). Identify what you believe to be the performance targets for the external envelope and components.
U-values for basements are calculated following BR 443 conventions for U-Values 2006 for Part L, and the methodology set out in ISO EN 13370:2017 section seven.
Basement calculation methodologies use different boundary conditions, surface resistances and temperatures to those for typical ground floors or walls. The calculations addressing walls and floors are intertwined.
As with calculations for rainscreen systems, simplistic calculation methods can be significantly inaccurate.
An initial calculation to ISO EN 6946 is initially carried out to assess the floor (Uf) and wall (Uw) simplified losses. Once the ground equivalent thickness and average depth below ground for the entire basement is assessed, the additional influences of losses through the ground are then calculated in ISO EN13370. It is critical that the correct category of ground type and thermal conductivity from Table 7 of this standard is considered in any calculations.
A real-world example from a semi basement gives some indication of the variance encountered. In this case the wall U-value of 0.18 W/m2K is increased during the calculation and will require improved performance in the upper floor (above ground) walls to meet the area weighted average for the wall performance for the project.
In an existing basement, where the average basement wall height is above 1.2 m, the basement walls and floors are both entered in the floor section of DEAP as separate entries.
In an existing basement, where the average basement wall height is below 1.2 m, the basement walls are entered in the walls section of DEAP and the floors in the floor section of DEAP. This can cause significant difficulties where under floor heating Uf requirements need to be met.
In a new basement, the basement walls and floors are entered as an area weighted average value in the floor section of DEAP as per Table 1 above.
Conclusion
With basements it is critical to get your design team involved, together with a damp proofing specialist, early in the process to develop a coherent strategy suitable for the indoor and external environmental conditions and performance requirements.
Front load your passive house and Part L compliance assessments early on in the design so as to ensure compliance can be achieved.
A continual external insulation strategy is my first choice, but, if you must consider hybrid or internal insulation strategies, it is imperative that the appropriate hygrothermal analysis informs your solution.
Specifications need to take account of the potential moisture levels the fabric will need to tolerate during the build, during drying out and beyond.
Although simulation tools such as Wufi might inform the level of risk, a commonsense approach must always prevail, and you will find post occupancy monitoring an invaluable assurance that you have made the right choice.
This article was published with the support of the Passive House Association of Ireland, a membership-based non profit organisation established to educate and inform people about evidence-based approaches to low energy building as characterised by the passive house standard. For more information visit www.phai.ie.