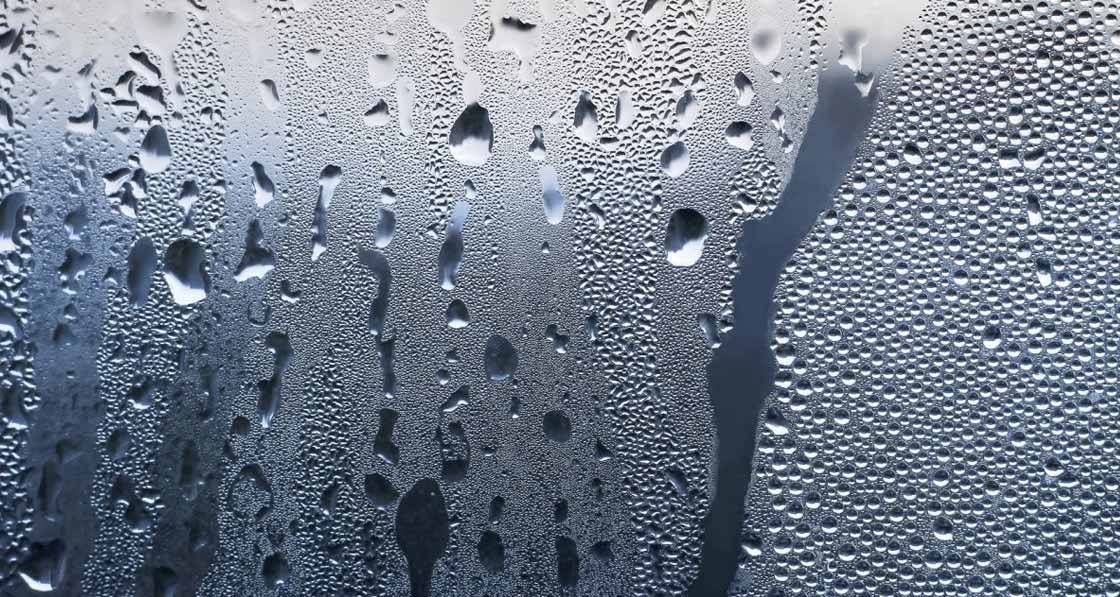
- Blogs
- Posted
The condensation myth
Condensation within the structure of buildings is a lot more complex than condensation in a sweaty pub on a Friday night, writes building physics expert Toby Cambray.
This article was originally published in issue 35 of Passive House Plus magazine. Want immediate access to all back issues and exclusive extra content? Click here to subscribe for as little as €10, or click here to receive the next issue free of charge
In lieu of the real thing, I invite you to join me in an imaginary trip to a packed pub on a Friday evening. If convenient may I suggest The Crown, Cricklewood, whence we may return to discuss building physics on subsequent occasions. The tribute band are on the stage and several tipsy people are dancing away, sweating profusely.
The windows are closed in an attempt to keep the noise in and the wind out. You order a bottle from the fridge, and as you hand over your cash, droplets of water condense on the cold, impervious surface of bottle.
Condensation, in the sense that most people understand the term, is pretty rare in buildings. You might be surprised to hear that as a specialist in moisture risk, I don’t often worry about it (at least not with respect to this popular definition).
A simple definition of condensation is moisture forming into liquid drops when warm moist air hits a cold surface. This is more an observation than a definition and doesn’t tell the whole story.
Air can hold a certain amount of water vapour, but that amount varies with temperature. Warmer air can hold more, colder air less. Relative humidity (RH) is the degree to which this carrying capacity is used. If you take some moist air and cool it down, the absolute amount of moisture doesn’t change but the RH goes up; cool it enough and you’ll get to 100%, at which point the moisture will form a liquid wherever’s convenient.
A more thorough definition considers the matter in terms of vapour pressure. Vapour pressure is a tricky concept. Another name for vapour pressure is partial pressure, which means the fraction of pressure in air (or another mixture) due to water vapour or another gas. So at one atmosphere of pressure, water vapour might be ‘responsible’ for say 2.3 % of that total pressure, and therefore have a partial or vapour pressure of 0.023 atm or about 2,300 Pa, which happens to be the saturation vapour pressure of air at 20 C. If you try to add more moisture to the air under these conditions, it will condense out as liquid.
The term condensation is probably most often abused when it’s immediately preceded by the word ‘interstitial’. I will not discuss the pros and cons of the Glaser method or EN 13788 here but would encourage you to read about this if you have not done so already. This approach is based on the concept of vapour flux, analogous to the more intuitive heat flux. Apply a higher temperature (or vapour pressure) to one side of a material, and heat (or water vapour) will diffuse though it at a rate dictated by the resistivity of the material and its thickness.
It’s essential to differentiate between this process and the movement of bulk air around or through a material – this is also important and often problematic, but it is fundamentally different to diffusion. Therefore the simple ‘cooling air down’ definition doesn’t help here, and we must think in terms of vapour pressure.
If vapour (or heat) is diffusing through a wall, driven by a vapour pressure (or temperature) differential, and it encounters a higher resistance – a piece of glass say (or insulation in the analogy), there is a pile-up. There’s still the differential, so the vapour or heat ‘wants’ to move from one side to the other, but it gets stuck.
At this interface the vapour pressure increases as more vapour tries to move through, until the vapour pressure at the interface approaches that inside, reducing and ultimately (in theory) cancelling out the vapour pressure differential. But if this location is cooler than inside, because of some insulation, the vapour pressure can exceed the local saturation pressure before it cancels out the pressure to the inside, and water will condense out of the air onto the most convenient nearby thing.
A building can in principle go mouldy without ever experiencing condensation.
This is why conventional design would have us avoid putting impervious (highly vapour resistant) barriers on the cold side of our insulation. A common and not entirely correct secondary conclusion is that we should instead, always have something impervious on the warm side of the insulation.
I agree with the first statement to a much greater degree than the second one. So now we have an understanding of ‘classical’ condensation and its interstitial variety. Why would I say that I don’t generally concern myself about it? Well, for one thing there’s enough understanding out there to avoid this in most cases. I can of course provide an ‘interstitial check’ if you insist on calling it that, but the sort of problems I’m usually asked to investigate are much more interesting.
As a very general rule of thumb, mould growth can initiate at about 80% RH, and timber decay at 95% or so. Convention suggests that 80 and 95 are less than 100, indicating that a building can in principle go mouldy and rot away without ever experiencing a drop of condensation.
Finally, and most complex is the reason (or rather one of them) that also renders EN 13788 unsuitable in many circumstances. Porous materials exhibit much, much more complex behaviour with respect to moisture than the idealised materials mentioned above. Solid metals, sheet glass and many membrane products for example can be reasonably accurately represented in simple terms, but the majority of materials we build with cannot, to a greater or lesser degree. This is because they are somewhat porous, and somewhat hygroscopic.
Hygroscopic materials have an affinity for moisture, which will bind to them across the spectrum of relative humidity. This means that as vapour pressure increases, these materials will absorb moisture, moderating the increase in humidity.
If materials such as brick and plaster are present under these conditions they will more often than not absorb moisture fast enough to avoid condensation as you might see on the side of your beer bottle. Students of building physics may (correctly) point out that there is indeed condensation of a different type – capillary condensation, but this is a more complex process than this column allows (being based on the ‘lies to children’ type of simplifications necessary to meet the word count).
So as with many things, when it comes to condensation in real buildings, I must deploy one of my most over-used expressions, or simply point to the phrase on my T-shirt: I think you’ll find its more complicated than that.