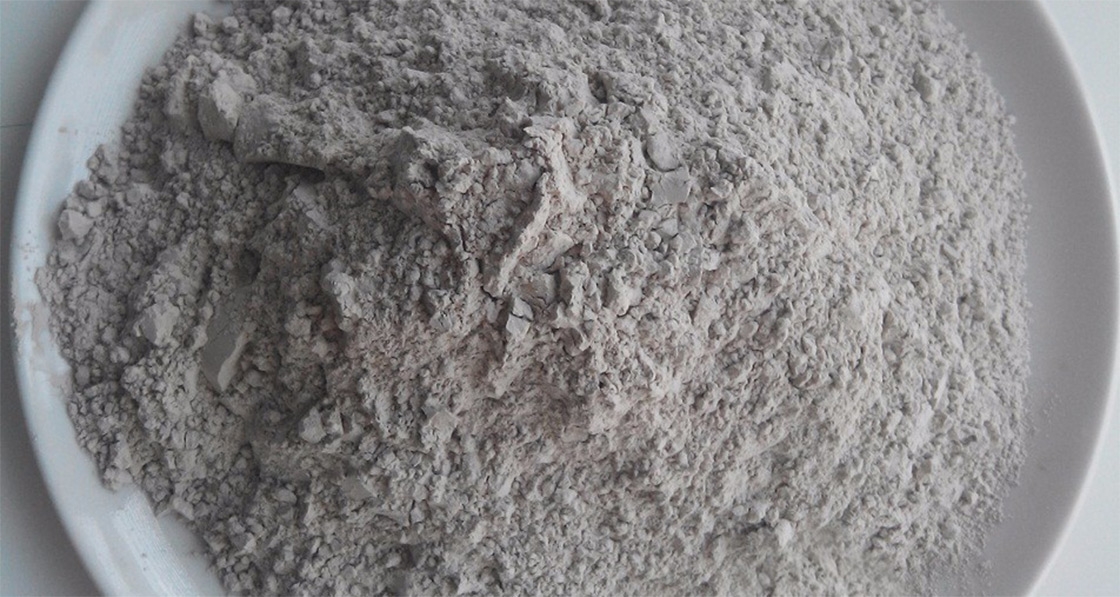
Sustainable Cement
The cement industry is well known as being amongst the worst culprits for emitting CO2, a seemingly unavoidable side effect of its production. However, as Peter Seymour, Business Development Manager with Ecocem Ireland Ltd explains, there is a strong, eco-friendly competitive alternative to Portland cement that is being specified in a variety of high profile construction projects in Ireland.
Ground Granulated Blastfurnace Slag (GGBS) cement is a by-product of the steel industry. Molten slag lying on top of the molten iron in the blastfurnace comprises silicates (glass), and is the raw material for GGBS cement. The molten slag - of no use to the steel making process - is cooled and then finely ground to form GGBS cement.
GGBS cement has exactly the same chemical constituents as ordinary Portland cement, only in slightly differing proportions. Thus it can replace Portland cement by up to 85% in making ready-mixed concrete. GGBS cement is widely used in the UK and on the continent for making concrete. It has been used in the UK for over seventy years where the annual usage is now about 20% of the total cement market. In continental Europe approximately 17.7 million tonnes of GGBS cement are used annually in making concrete. The leading user of GGBS is the Netherlands, where 54% of cement used in making concrete comprises GGBS cement. Belgium (25%), Italy (27%) and Germany (14%) also have high GGBS cement usage levels. GGBS cement is a recycled product and it replaces the use of Portland cement in concrete on a one-for-one basis. By replacing Portland cement it replaces a product that has very high CO2 emissions, has high embodied energy and involves a significant amount of quarrying. Used appropriately, GGBS cement will reduce the CO2, NOX and SO2 emissions of concrete by over 50%, it will reduce the embodied energy in concrete by over 40%, and it will significantly increase the service life of concrete, enhancing sustainable development.
How GGBS cement is used
GGBS cement is added to concrete in the concrete manufacturer's batching plant, along with Portland cement, aggregates and water. The normal ratios of aggregates and water to cementitous material in the mix remain unchanged. GGBS is used as a direct replacement for Portland cement, on a one- to-one basis by weight. Replacement levels for GGBS vary from 30% to up to 85%. Typically 40 to 50% is used in most instances. GGBS cement is used for its environmental benefits, improved appearance for exposed concrete and technical benefits, including resistance to sulphate and chloride attack and reduced heat of hydration. The use of GGBS cement in concrete in Ireland is covered in the new Irish concrete standard IS EN 206-1:2002. This standard establishes two categories of additions to concrete along with ordinary Portland cement: nearly inert additions (Type I) and pozzolanic or latent hydraulic additions (Type II). GGBS cement falls in to the latter category. As GGBS cement is slightly less expensive than Portland cement, concrete made with GGBS cement will be similarly priced to that made with ordinary Portland cement.
Architectural and engineering benefits
Appearance
GGBS cement is a near-white powder. It imparts a lighter, brighter colour to concrete, in contrast to the stoney grey of concrete made with Portland cement. The colour of the finished concrete is lighter, the concrete has a smoother surface finish, and the addition of GGBS to the mix prevents the formation of efflorescence. The near-white colour of GGBS cement permits architects to achieve a lighter colour for exposed fair-faced concrete finishes, at no extra cost. To achieve a lighter colour finish, GGBS is usually specified at between 50% to 70% replacement levels, although levels as high as 85% can be used. GGBS cement also produces a smoother, more defect free surface, due to the fineness of the GGBS particles. Dirt does not adhere to GGBS concrete as easily as concrete made with Portland cement, reducing maintenance costs. GGBS cement prevents the occurrence of efflorescence, the staining of concrete surfaces by calcium carbonate deposits. Due to its much lower lime content and lower permeability, GGBS is effective in preventing efflorescence when used at replacement levels of 50% to 60%.
Strength
Concrete containing GGBS cement has a higher ultimate strength than concrete made with Portland cement. It has a higher proportion of the strength-enhancing calcium silicate hydrates (CSH) than concrete made with Portland cement only, and a reduced content of free lime, which does not contribute to concrete strength. Concrete made with GGBS continues to gain strength over time, and has been shown to double its 28 day strength over periods of 10 to 12 years (1).
Durability
GGBS cement is routinely specified in concrete to provide protection against both sul phate attack and chloride attack. A 70% replacement of Portland cement with GGBS provides protection against sulphate attack. GGBS has now effectively replaced Sulphate Resisting Portland cement (SRPC) on the market for sulphate resistance because of its superior performance and greatly reduced cost compared to SRPC. Most project in Dublin's Docklands, including Spencer Dock, are using GGBS in subsurface concrete for sulphate resistance.
To protect against chloride attack, GGBS is used at a replacement level of 50% in concrete. Instances of chloride attack occur in reinforced concrete in marine environments and in road bridges where the concrete is exposed to splashing from road de-icing salts. In most NRA projects in Ireland GGBS is now specified in structural concrete for bridge piers and abutments for protection against chloride attack. The use of GGBS in such instances will increase the life of the structure by up to 50% had only Portland cement been used, and precludes the need for more expensive stainless steel reinforcing.
GGBS is also routinely used to limit the temperature rise in large concrete pours. The more gradual hydration of GGBS cement generates both lower peak and less total overall heat than Portland cement. This reduces thermal gradients in the concrete, which prevents the occurrence of microcracking which can weaken the concrete and reduce its durability, and was used for this purpose in the construction of the Jack Lynch Tunnel in Cork.
GGBS Cement was used in the Luas Bridge in Dundrum, for durability and appearance
Photo: William Murphy
Environmental benefit
CO2 and other pollutants
In Ireland, cement manufacture is currently the second largest industrial source of CO2 and NOX emissions, after the generation of electrical power from fossil fuels. Almost one tonne of CO2 is generated in the manufacture of one tonne of Portland cement, along with 2kg of SO2, 3.5kg of NOX and 2kg of CO.
On the other hand GGBS cement is manufactured from an industrial by-product, and has a minimal CO2 footprint, and zero harmful pollutant emissions such as SO2, CO and NOX. The following chart (see p. 61) illustrates the difference in CO2 emissions between GGBS and Portland cement, and demonstrates the savings that can be made by using GGBS cement
Energy savings
In addition to CO2 savings, the embodied energy of GGBS is only some 7% to 8% of that of Portland cement. The manufacture of Portland cement is a high energy use process, involving three separate processes: - Quarrying, crushing and blending limestone and shale
- Burning the limestone and shale in a rotating kiln to produce clinker
- Grinding the clinker to make cement The energy consumption per tonne of Portland cement produced equals 4,000 MJ (1,100 KW.hrs) In contrast, the manufacture of GGBS cement only involves the transport, drying and grinding of an industrial by-product, and is a low energy operation. In addition, it is a recycling operation and has downstream benefits in that it eliminates the need for landfill disposal. The energy consumption per tonne of GGBS produced equals 307 MJ (85 KW.hrs). Thus the energy saved by replacing Portland cement with GGBS cement equals 3,693 MJ (1,015 KW.hrs) per tonne.
Natural resources
In the production of Portland cement, 1.6 tonnes of clay and limestone are removed from the landscape for every tonne of Portland cement produced. However, there is zero depletion of natural resources associated with the manufacture of GGBS.
The raw material for GGBS production is an industrial by-product. This means no extraction of limestone or clay in large-scale quarries that both deplete natural resources and disfigure the landscape, and no associated traffic, noise and dust problems that are also generated by large-scale quarrying operations.
Steel Blast furnace - the source of GGBS Cement
Kyoto Protocol and the Emissions Trading Scheme
The recent ICL/BOC report(2) highlights the costs Ireland faces from non-compliance with its Kyoto obligations. The excess of emissions over the Kyoto target is forecast at 8.1mt p.a. of CO2 over the period 2008-2012. This excess will need to be covered by buying carbon credits: at today's cost of e23/tonne this will cost the Exchequer e930m, with a considerable risk of escalation if carbon credit prices rise.
Because of its significantly lower CO2 footprint, the use of GGBS can reduce this cost to the Exchequer by e31m over the period 2008-2012, based on availability to the market of around 300,000 tonnes GGBS per annum. So in addition to a saving on pollutant emissions, there are also fiscal saving to be achieved for the taxpayer by using GGBS cement.
Reducing the environmental impact of concrete
It is well established that about half of the environmental impact of concrete delivered to site derives from the cement in the concrete. Therefore, reducing the Portland cement content will reduce the environmental impact of concrete.
*Eutrophication is where elevated levels of mineral and organic nutrients in ponds promote a proliferation of plant life, especially algae, which reduces the dissolved oxygen content and often causes the extinction of other organisms
Overall Environmental savings
To summarize the environmental savings that can be made by using GGBS cement, take the example of a mid-sized engineering project, such as a shopping centre, using some 5000m3 concrete.
*PM10 is very fine dust, passing 10 microns in size, that is harmful to health
It is clear from the above that the CO2, energy and other environmental savings using GGBS are significant. These savings are far greater that can be made by simple individual lifestyle changes. Professionals who are in a position to make choices - architects, engineers and any specifiers should see this as an excellent opportunity to make a contribution to the environment, as significant environmental benefits are very easy to achieve at no additional cost.
Contribution to sustainable development
In addition to its many environmental and environmental cost benefits, concrete made with GGBS cement, by nature of its greater strength and durability, has a longer service life than that of Portland cement. This means that the time to replacement of concrete products and structures is extended. Specifying GGBS to replace Portland cement in concrete is an essential requirement on all projects carried out under the aegis of sustainable development.
The longer service life of concrete containing GGBS reduces the demand on natural resources to meet the requirements of the construction industry. This applies to all ingredients in concrete: for every tonne of cement there are approximately 6 tonnes of sand/aggregates that also need not be replaced as long as the concrete remains in serviceable condition. Extending the useful life of concrete has a major impact in reducing the demand for the extraction of new natural resources from the landscape, thus GGBS cement offers a significant contribution to sustainable development.
GGBS cement produces a stronger and more durable concrete than that made (like for like) with ordinary Portland cement. It also has architectural benefits in that it produces a lighter coloured concrete finish, and can prevent the occurrence of efflorescence. It is a recycled industrial by-product, and has a much smaller environmental footprint than that of Portland cement. Specifying the use of GGBS in concrete brings significant reductions in CO2 and other harmful pollutants, it reduces the embodied energy of concrete, and saves on the depletion of natural resources. It will also bring fiscal savings in reducing Ireland's financial obligations under the Kyoto Protocol's Emissions Trading Scheme, and it will extend the service life of concrete. All in all it is the ideal building material for sustainable development.
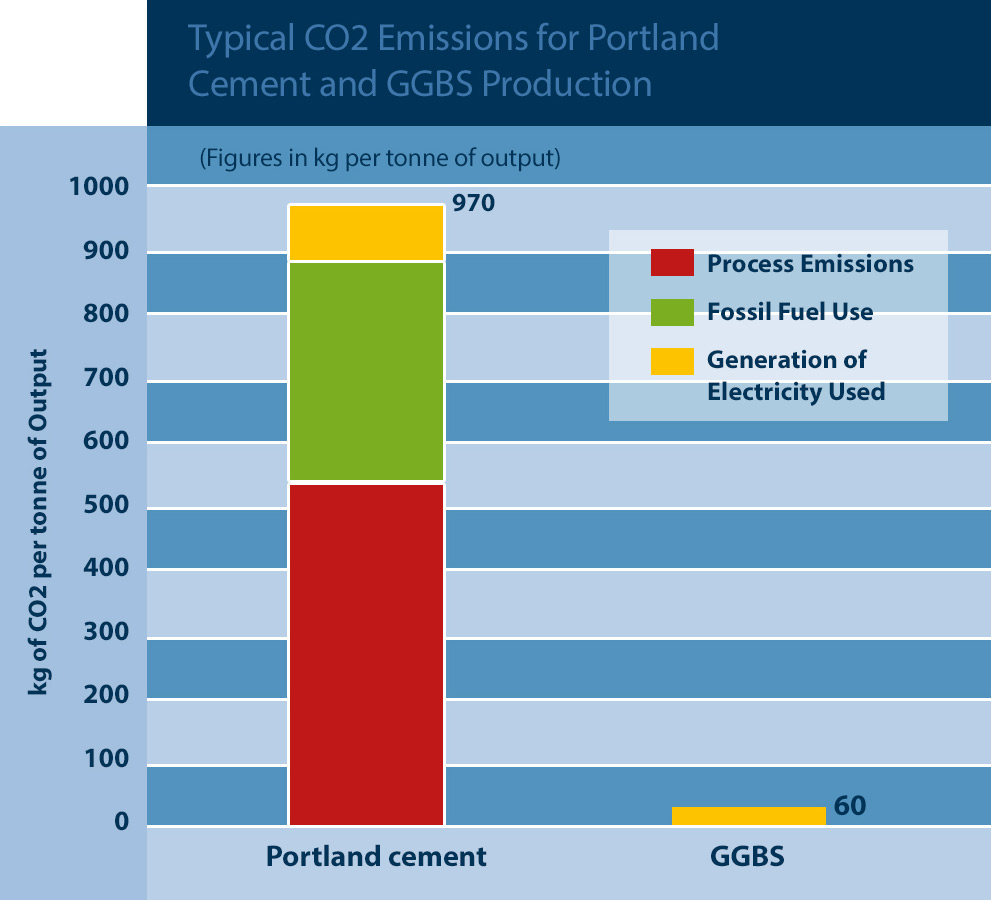
References
1. Smolczyk, H.G. Durability and pore structure on very old concretes (Dauerhaftigkeit und Porenstruktur von sehr alten Betonen), Beton-Informationen 26, Heft 1, 1986.
2. Determining the Share of National Greenhouse Gas Emissions for Emissions Trading in Ireland 2008-2012, Report for Public Consultation, submitted to Department of the Environment, Heritage and Local Government, ICL Consulting and Byrne Ó Cléirigh, October 2005.
3. Concrete Industry Alliance, "Interim Environmental Report for the UK Concrete Industry, 1994 to1997", CIA/DETR Partners in Technology Project (April 1999).
- Articles
- Sustainable Building Technology
- Sustainable Cement
- cement
- ecocem
- OPC
- sustainable building
- portland
- GGBS
- ground
- granulated
- blastfurnaced
- slag
Related items
-
Enniscorthy to host ‘make or break’ sustainable building summit
-
Most polluting cements ruled out in Irish public procurement
-
Up to 11
-
Ecocem announces cement breakthrough to cut CO2 by 70 per cent
-
Kilsaran launch lower carbon cement with CarbonCure
-
Ecocem gets €22m investment from Bill Gates's climate fund
-
Strong demand for GGBS from Irish market
-
Mannok announces new product names after rebrand
-
The PH+ guide to greener concrete - reducing the climate impact of cement and concrete in buildings
-
New issue of Passive House Plus free to read
-
Low carbon concrete blocks now available in Ireland
-
10 million tonnes of carbon saved by low carbon cement — Ecocem