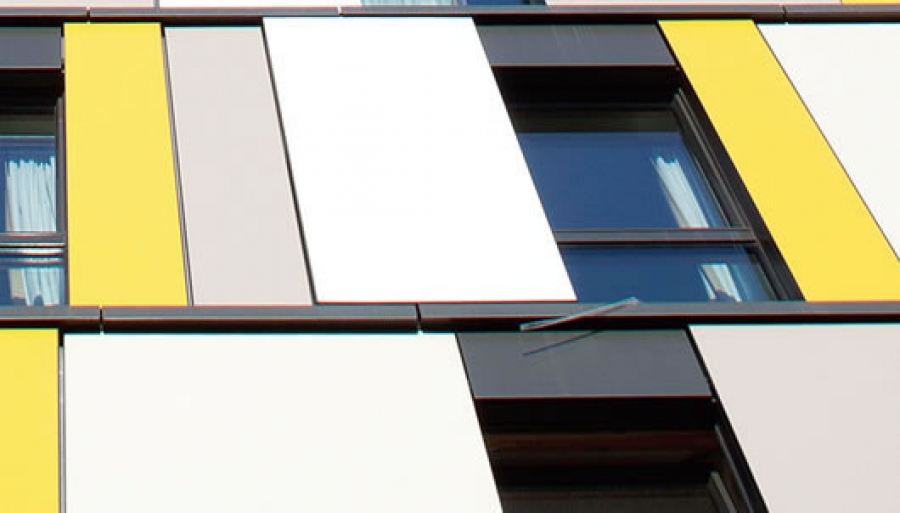
- Passive Housing
- Posted
Passive reaches new heights at UCD student halls
The winner of the sustainability award at the 2011 Irish Architecture awards, Roebuck Castle student residence at UCD’s Belfield campus is also the biggest certified passive house project built to date in Ireland and the UK. Tony Rigg of Kavanagh Tuite Architects explains how such a significant building achieved passive results.
The design process
Serving 300 students, Roebuck Hall student residence was designed by Kavanagh Tuite and completed in 2006. For its time, it was an energy efficient building relative to then current regulations. Six storeys high, the external walls were formed of structural concrete, cast with permanent magnesite board formwork which required only decoration for final finish. The windows were fixed on the external face of the concrete, and air-sealed to the concrete. The walls were then insulated with 60mm rigid foil-faced polyurethene boards, and faced with a brick skin supported on stainless steel angle supports at each floor level. This gave an effective airtight construction, reasonably well insulated, and an economical construction solution.
When design started on Roebuck Castle residence in 2008, in establishing the brief with UCD, it was decided to raise the standard and aim for an exemplary green project. Passive house was subsequently adopted as the reference standard.
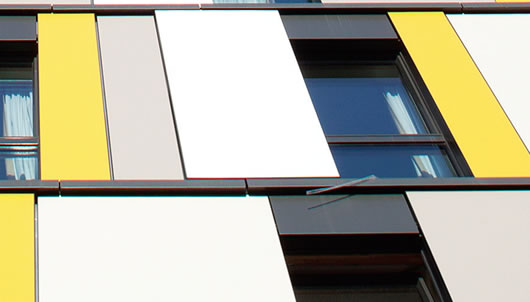
In choosing a façade material, the architects decided to exclude materials more associated with commercial buildings, such as metal panelling, and ultimately settled on Trespa Meteon cladding for the rainscreen finish. Casement windows throughout the building are Lang Fenster triple-glazed aluminium-clad timber units, certified by the Passive House Institute
Located adjacent to the first phase, the project was also to be six floors high. We examined the practical and aesthetic implications of designing to a much higher energy performance standard, and the greatly increased thickness of insulation required for this type and scale of building structure. While adjacent to the brick-clad Roebuck Hall, it quickly became apparent that it was not economically feasible to support a six-storey brick-clad façade through the 200mm plus thickness of insulation required to achieve the ambitious thermal performance levels needed for passive house. This would have required a secondary six-storey independent structure to support the heavyweight brickwork cladding.
Super-insulated pre-cast concrete panels were examined, but were found to be neither technically feasible nor economic; GRC faced panels were not competitive in the Irish market, so we proposed a lightweight insulated framed wall panel with rainscreen cladding.
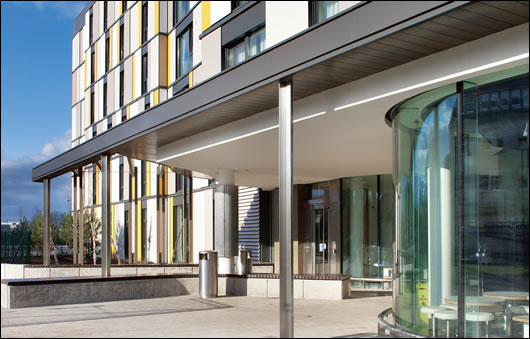
At six-storeys high, the latest phase of Roebuck Hall will be home to hundreds of UCD students
As a university residence, we excluded façade materials more related to commercial building, such as metal panelling. Terracotta, while attractive, proved too costly. After examining several external board alternatives, Trespa Meteon was selected as the preferred rainscreen finish. This could be applied on both the externally insulated concrete walls, and on the lightweight metal-framed structural wall panels.
This process of design, through exploration of practical available options to achieve a new and different standard of building construction and performance, influenced and informed the whole detail design process, and the final aesthetic quality of the building.
The project
The plan for hall of residence style accommodation contains en-suite student rooms and kitchenette, living and study rooms on either side of a spine corridor, arranged in two ‘apartments’ on either side of a central lift and stair core.
This basic simple plan form is off-set and articulated around the central core, where at ground level the main entrance and cafeteria face onto a walkway through the building, providing a link with previous and future stages of the Roebuck student village. Secondary escape stairs at each end of the building are expressed, again articulating the simple, compact building form. The roof-top plant room housing, containing the central plant (heat recovery ventilation, water storage tanks and other plant) is external to the insulated building volume, but is expressed as a vertical extension of the central lift and stair core, again articulating the built form.
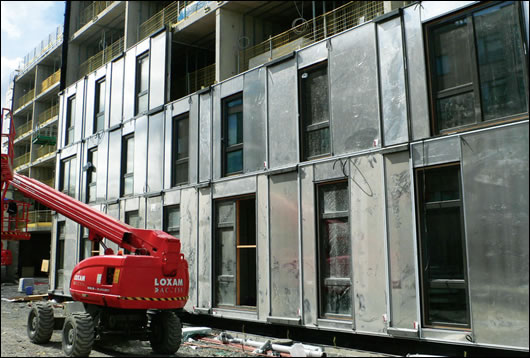
The building was constructed with GGBS concrete cross wall, stair core and floor structures, with lightweight insulated framed wall panels to all the student rooms
The building is of GGBS concrete cross-wall, stair core and floor structure, with lightweight unitised metal-framed external wall panels to all the student rooms. The unitised panels create an airtight façade – point fixed to the slab edges for minimum cold bridging – and together with wood-framed curtain wall façades to the three stair core volumes, provide large sealed elements that are then easily air-sealed to the basic concrete structure with EPDM membranes. This strategy largely designed-out problems of air sealing the project.
The student rooms have passive house certified triple-glazed windows. They are foam-sealed and taped into the unitised panels, and while openable, they have an interlock control, closing the local heating circuit when the window is opened.
The corridors and stair cores are not heated, and are glazed with wood-framed, high-performance double-glazed curtain walls.
All concrete walls are insulated externally with 130mm foil-faced and taped PIR boards, and clad with the Trespa Meteon boards on Eurofox rainscreen support system. This same cladding system runs over all the unitised light weight wall panels, giving a uniform external appearance to all. The cladding has a limited number of earthy colours, relating to adjacent buildings and the natural context, helping to give the building an understandable and human scale.
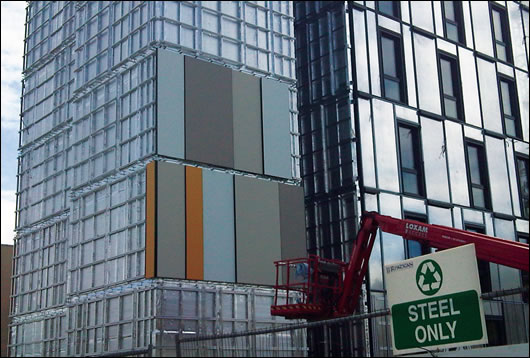
The project makes extensive use of renewable or recycled materials, such as acetic-acid modified timber (Accoya), recycled sorghum strand board (Kirei Board), water-based paints, linoleum floor finishes (Marmoleum), and GGBS (ground granulated blast furnace slag) cement based concrete.
Heat recovery ventilation is provided through two central roof-top heat-wheel air handling units, and heating is provided from spare capacity in the adjacent Roebuck Hall condensing boilers, supplying mini-radiators in the student rooms, with cut-off controllers linked to opening sensors in the windows.
Domestic hot water (the largest heat load in the building), is partially – 33% – supplied by a drain-back flat plate solar water heating system on the roof. This covers the 20% renewable energy requirement stipulation in Dun Laoghaire Rathdown’s County Development Plan (ed. – resulting from a successful Construct Ireland campaign).
Rainwater is harvested from the building roofs, and used for toilet flushing.
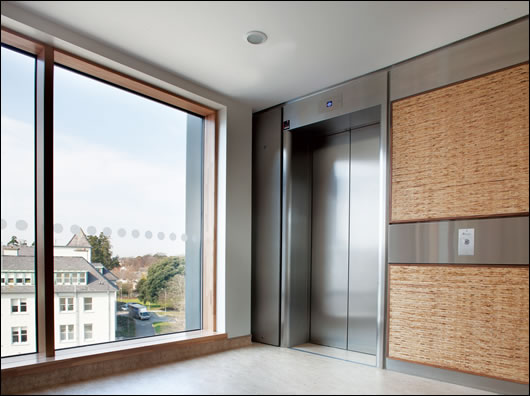
Post completion
Post completion commissioning and occupants’ reviews, monitoring of actual systems and comfort performance are essential for us to study and learn from the actual results, and to develop our skills and expertise going forward.
In line with this, UCD Energy Research Group, funded by SEAI, has commenced a two year programme of monitoring post occupancy evaluation of the building. A roof-top weather station provides full climatic data, and monitoring equipment installed in 16 student rooms in the building provides data on indoor temperature, humidity and CO2 levels, electrical use and lighting loads. It also records overall energy required for space heating and domestic hot water; heat flows from the heat recovery ventilation system and solar collectors. The data will be analysed by UCD Building Environmental Lab to inform on actual savings from individual systems, provide data for further research in the application of the passive house standard in Ireland, and ensure that the students are residing in a comfortable and healthy environment.
Conclusions
We have reached a stage where both regulatory changes and rising operational energy costs are giving a major push towards better, greener building design standards. Improved building materials, elements and systems added to a developing professional knowledge and expertise, combine to give a huge opportunity for skilled designers to create better buildings, better architecture – advanced environmental performance, efficiency, and functional, well detailed, good looking solutions.
Through a process of better environmental design, detail attention to building element interfaces, use of performance analysis and modelling, and learning from our developing experience, at Kavanagh Tuite we aim to keep raising the bar on our design skills and abilities.
This project, an example of Kavanagh Tuite’s continuing commitment to, and expertise in, sustainable and green design, demonstrates that fine architectural design can be achieved together with exemplary high-performance building construction. It is necessary however, from the conceptual design stage, to design-in thermal performance, and to design-out thermal bridging and airtightness problems. This is both a challenge and an opportunity, with no more shortcuts (any more…) to success!
Selected project details
Client: UCD
Architects: Kavanagh Tuite
M & E engineers: Delap & Waller
Civil / structural engineer: Hanley Pepper
Main contractor: JJ Rhatigan & Co
Passive house consultants: DW EcoCo
Airtightness testers: Building Envelope Technologies
Drywall: Lafarge
Roof insulation: Xtratherm
Floor insulation: Styrisol
Windows/curtain walling: Lang Fenster
Cladding /rooflights: Williaam Cox
Wood louvres: QEF
Airtightness products: Isover
Solar thermal: Zen Renewables
Heating controls: Comeragh Controls
Marmoleum flooring: Forbo
Carpets: Milliken
GGBS: Kilsaran
Rainwater harvesting tank: KMG Killarney Plastics
Heat recovery ventilation: FläktGroup Ireland
PROJECT OVERVIEW:
Building type: Student residence, 4,300 square meter six-storey detached, concrete structure
Location: UCD Belfield Campus, Co Dublin
Completion date: September 2010
Passive house certification: certified
Space heating demand (PHPP): 12 kWh/m2/yr
Heat load (PHPP): 12 W/m2
Airtightness: 0.6 air changes per hour at 50 pascals pressure
Building Energy Rating: A3
Ground floor: precast concrete plank floor, insulated generally with 140mm Styrisol extruded EPS insulation and under bathroom pods with 25mm Vacupor RB2 insulation.
U-value: 0.15 W/m2K
Walls, unitised: Trespa Meteon and Eurofox rainscreen cladding externally, on 210mm Schueco aluminium-framed unitised structural wall panels, filled with Celotex PIR insulation, lined with 45mm foil-faced and taped Celotex PIR insulation board, 50mm metal stud and uninsulated service cavity, and 15mm plasterboard internally.
U-value: 0.17 W/m2K
Walls, concrete: Trespa Meteon and Eurofox rainscreen cladding externally, on 130mm foil-faced and taped Celotex PIR insulation board, 215mm concrete structural wall, lined with 45mm foil-faced and taped Celotex PIR insulation board, 50mm metal stud and uninsulated service cavity, and 15mm plasterboard internally.
U-value: 0.20 W/m2K
Roof: 50mm stone pebbles, on 20mm 2-coat mastic asphalt waterproofing on isolation membrane, on screed laid to falls, on 160mm Xtratherm foilfaced polyisocyanurate foam insulation boards, on DPM, on 275mm structural concrete slab, followed underneath by 25 mm uninsulated service cavity, 12.5mm plasterboard ceiling.
U-value: 0.15 W/m2K
Windows, casement: Lang Fenster triple-glazed aluminium-clad wood windows, Passive House certified.
Overall U-value: 0.80 W/m2K
Windows, curtain wall: Lang Fenster high performance double-glazed wood-framed curtain walling.
U-value: 1.20 W/m2K
Heating system: heat supplied from spare capacity in 96% efficient Rendamax R30/85 condensing gas boilers in adjacent Roebuck Hall I building, supplying mini radiators in student rooms, and underfloor heating in cafeteria. Student rooms have individual controllers, linked to cut-off sensor in openable windows. Domestic hot water system supplemented by 160m2 Zen Renewables flat-plate solar collectors, supplying a stainless steel, 2000 litre calorifier for domestic hot water storage and supply
Ventilation: Fläkt Woods type eQ central heat recovery ventilation system, Eurovent certified efficiency of 76.5%
Electrical use: high-efficiency light sources used throughout, with fluorescent and LED fittings
Green materials: structural concrete with 30% GGBS cement, wood-fibre based Trespa Meteon rainscreen cladding panels, timber windows and curtain wall timber from certified sources, Accoya timber cladding and external louvres, water based paints used internally, Marmoleum linoleum flooring to common areas, Milliken carpet tiles to student rooms, Kirei Board wall panelling
Airtightness preparation: Surpassing passive house airtightness levels does not just happen by testing the building at the end of a project. Building Envelope Technologies, an ISO:17025 INAB accredited testing laboratory, carried out CIBSE CPD approved training seminars to main & all sub-contractors, reviewed the initial drawing & product specifications and conducted site inspections & airtightness workshops throughout the project. Building Envelope Technologies also provided sample room testing & building defect diagnostics during construction, an INAB accredited final airtightness test to ISO 17025 on completion and 12 months later, and a level three certified thermographic survey on completion.