- Passive Housing
- Posted
Athenry passive house
In spite of the growing interest in the passive house standard in Ireland, only a handful of Irish buildings have been certified by the Passive House Institute. Through great attention to detail during design and construction, a new closed-panel timber frame home in Athenry looks set to meet the cutting-edge low energy standard. Words: John Hearne
As Construct Ireland goes to press, Cyril Mannion of Passive House Builders is awaiting word from the Passive House Institute in Darmstadt on the certification of his latest completed project in Athenry, County Galway.
On paper, it makes the grade. U-values are all in excess of exacting passive house standards – 0.12 W/m2K in floors, 0.1 W/m2K in walls and 0.09 W/m2/K in the roof. Heating demand is 14.2 kWh/m2/yr and primary energy demand is 64.15 kWh/m2/yr. The air change rate is particularly impressive. 0.3 ACH/hr is exactly half the 0.6 required by the institute. Using Deap, Energy Matters generated an A3 BER cert and calculated annual CO2 production at 12.1 kg CO2/m2/yr.
Building what seems destined to be the first certified passive house in the west of Ireland was a major challenge for Mannion and his clients Scott and Ann Cook. Though the build itself took five months from start to finish, Mannion estimates that design and planning beforehand took a further five months. He began as a conventional builder ten years ago, before moving to low energy design in 2006. Moving subsequently from A3 to passive two years later was, he says, as big a leap as from conventional block built to low energy. “I was at a conference in Nuremberg in 07 and…it just made sense to go this route. But it is very hard to meet passive targets. There was no one who could show you exactly how it’s done. There was no template. I ended up educating myself, just as I did in building A3. There was no one who could answer the hard questions, like, what U-value do you need and how do you achieve this cold bridge detail?” Convinced that there would be more opportunities to work with designers and their clients on commercial and residential passive house projects, Mannion immersed himself in the subject, gaining a certified designer/consultant award from the Passive House Institute in the process.
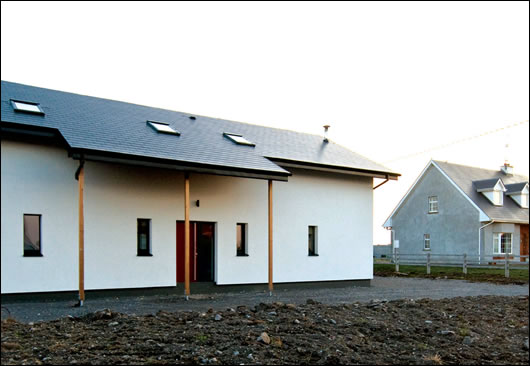
Glazing is minimised on north, east and west elevations although there are three rooflights on the northern roof
The client’s chosen site lent itself reasonably well to passive design. The back elevation lies 20 degrees off full south, and though it sits in the middle of a ribbon development with houses either side, there are no over-shadowing issues on key elevations. “The front looks like the back,” says Mannion, “but Scott didn’t mind. Traditionally, you face road but Scott put his back to the road and kept his living space to the south.”
Mannion chose the Viking House polystyrene foundation system: “I went to see it in a few places.” He says. “I thought it was a nice system; simple, not over the top. Plus you could source it locally. You can’t really compare it to a standard raft because it’s cold bridge free whereas a standard raft is one big cold bridge.” Two densities of polystyrene were used in the construction of the raft, Seamus O’Loughlin of Viking House explains: EPS 300 and 100, which take their names from the fact that they’ll take 300 and 100 kilonewtons per square metre respectively. While polystyrene is an oil-based product, O’Loughlin says this is mitigated by the fact that energy in manufacture compares well to that of conventional insulation products. “The temperature required to make rock wool is around 900 degrees. It’s similar for glass wool, whereas polystyrene requires only 110 degrees. If you use 100L of oil to make an amount of polystyrene, roughly 90/95L of that oil remain trapped in the polystyrene – it’s not carbon sinking but it’s carbon set-aside. You shouldn’t be taking oil out of the ground in the first place, but if you are going to make something with the oil, you should make insulation with it because for every gallon of oil you use to make that insulation, you can save 200 or 300 gallons in heating.” He stresses too the importance of sizing and compacting the right grade of stone underneath the raft in order to provide the capillary break which will prevent rising damp.
Mannion specified the U-values he wanted to achieve and put the contract for the frame out to tender, awarding the job to Eco Timber Frame in Cork. The insulated panels were manufactured offsite, then driven to the site and craned into place. All in, Eco Timber Frame were onsite in Athenry for approximately three weeks. Two independent studs were used, in order to provide sufficient thickness for insulation and to limit thermal bridging, Stephen Spillane of Eco Timber Frame explains. “It’s a double wall construction, 350mm deep and filled with cellulose.” The cellulose used is Warmcel 500 provided by Warmcel in the UK. Full wall build-up is as follows: cement board on the outside, over an air cavity, then breathable wood panel, densely packed cellulose, OSB sheathing, a service cavity and a standard plasterboard on the inside. “We were looking for innovative ways to achieve a very high quality fabric,” says Spillane, “well insulated and airtight. We spent a lot of time looking at what’s done in Germany and Austria and we’ve come up with this wall construction. The OSB board on the inside is taped for airtightness and the wood fibre board on the outside allows the house to breathe. It’s a diffusion open wall.”
All timber is from Swedish certified sustainable sources. “There were no major issues in construction.” says Spillane. “There was, naturally enough, a lot of glazing to the south. That brought a couple of structural challenges but we got around them by coming up with an alternative way of achieving the racking strength that’s needed in a timber frame house.” An open-web joisting system was used both in the intermediate floor and in the roof. The motivation here centred primarily on boosting thickness in order to take sufficient insulation – 400mm of cellulose in the roof – and again to reduce thermal bridging. An open-web system uses less timber than a traditional joist system, and it provides space to run services – u even HRV ducting. Internal studs are also insulated for sound, while the service cavity took an additional 50mm of Rockwool. Externally, the house is clad in the Aquapanel cement fibre board system from Greenspan. Boasting only around 10% of the carbon footprint of a masonry wall, the panel is fully NSAI Agrément approved with a stated design life of 60 years.
Eliminating cold bridging, says Mannion, is particularly important in passive design. Citing a patio door on the southern elevation, he points out that there’s fully eight linear metres of frame, and therefore of cold bridge. “That will be heavily penalised in PHPP if it’s not done right. We’ve got them all down below 0.3 W per linear meter.”
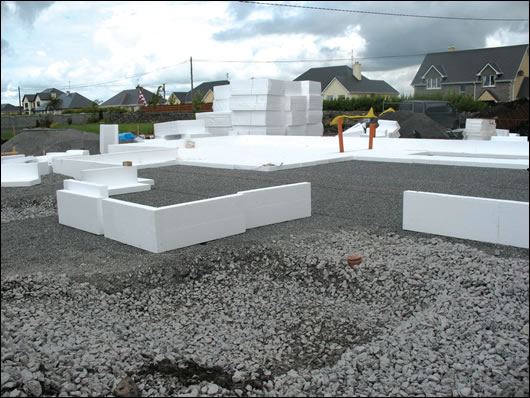
Installation of the Viking House polystyrene foundation system
Windows are the Edition range from Internorm. These are triple-glazed, spruce, aluclad windows which incorporate foam insulation on the inside. “The make-up,” says Matt Jordan of Eco Glaze, “from outside to inside is 4mm of glass with a soft low e coating on the interior, then 15mm of krypton, 4mm of standard glass on the inside, then 15mm of krypton fill again, then 4mm glass, and on the outside of that glass, there’s another soft low e coating.” The second low e coating reduces passive gains compared to a conventional double-glazed unit, though the thermal improvement of the additional pane more than compensates for that loss. The whole unit U-value is 0.68 W/m2K.
The front door is a fully certified passive house door, from Internorm’s Selection range. It delivers a U-value of 0.79 W/m2K.
“Edition windows come with triple seal as standard, and a six to eight point locking system. All are tilt and turn from a single handle.” says Jordan. “To get the airtightness that Cyril’s achieved in this house, you need a window that has a very high performance on airtightness.”
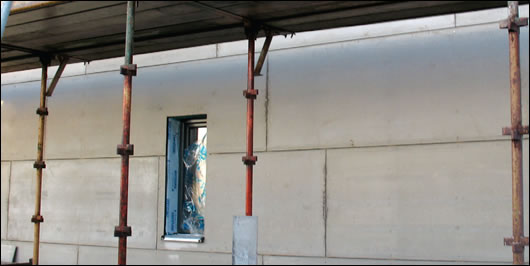
The house is clad externally in Aquapanel cement fibre board
Glazing is of course minimised on north, east and west elevations, where bedroom, bathroom and circulation areas are located, while extensive glazing on the southern elevation allows for maximum passive gains in living areas. A lot of work went into sizing and placing the windows in advance of the build, says Mannion. “You play around with PHPP,” he says. “Moving windows around and increasing and decreasing the size of them. It’s a brilliant design tool when you get to know how to use it – and you can make money with it. I think we saved between €5,000 and €6,000 here by playing with windows, by fixing panes, by making them bigger or smaller and so on.”
Overheating is dealt with primarily by structural shading and natural ventilation. Roof overhangs upstairs reduce passive gains from the high summer sun, while balconies to be installed above living areas will fulfil the same function downstairs. Opening doors and windows provides cross ventilation downstairs when required, while the HRV system is also equipped with summer bypass.
Three Farko rooflights on the northern roof were the subject of some debate between client and builder. “They were one thing I would have loved to have eliminated but Scott wouldn’t have it,” says Mannion. “I was very worried about them ahead of the blower door test – I thought they’d make or break us, but in the end they were perfect. I was very impressed with them. They’re triple-glazed, airtight and have an overall U-value of 0.97 W/m2K.”
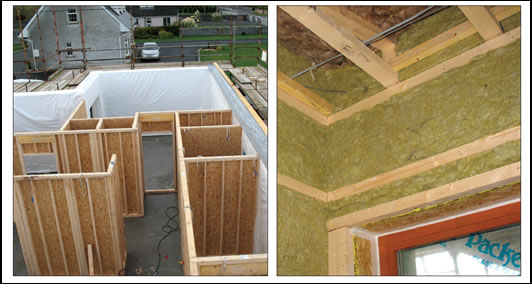
The closed panel timber frame house starts to take shape; the walls include a 50mm Rockwool filled service cavity inside the airtight layer – Siga tapes fixed to OSB, visible here at the window reveal
As mentioned, the Medite Smartply OSB board, an FSC product, installed between service cavity and insulated cavity provides the airtightness layer. This was then taped across all joints with a Siga tape. Airtightness, says Mannion, is important with low energy houses, but with passive building, it’s vital. “This is the first time I used OSB as an airtight layer,” says Mannion, “but it makes sense from a structural point of view. You’ve got racking and airtightness in one hit. Also u if you ever go to fix a picture and don’t know where to stop with the drill, if there’s a membrane there, it’s punctured, whereas they can fix a screw in the OSB and that’ll stay airtight.” While OSB is a very robust solution, Mannion is keen to emphasise that that doesn’t mean you can get complacent about it during construction. “Airtightness is a team effort. No one individual is going to make a house airtight. It could be airtight today but to keep it airtight tomorrow, you have to be vigilant. It’s fully achievable, but you have to be interested and onsite and you need good lads…It helped too that the trades that we used have been with us doing A3 houses; they didn’t just land in on top of passive with no experience.”
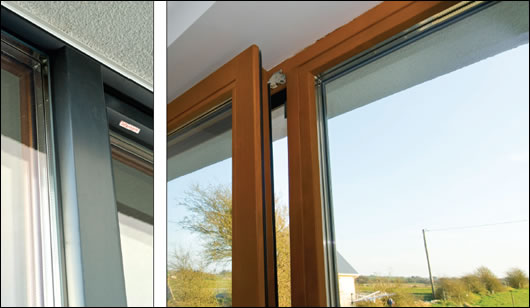
Supplied by Eco Glaze, the windows are the Edition range from Internorm. They are triple-glazed, spruce alu-clad windows which incorporate foam insulation on the inside
Ronan Rogers of Energy Matters conducted two airtightness tests on the building, as well as the BER assessment. He says: “The preliminary test in November 2009 achieved a result of 0.405 ACH/hr – translating to an air permeability of 0.61 m3/hr/m2 at 50Pa. The dwelling was under construction at the time but most of the air permeability measures had just been installed. The final test was conducted in February 2010, when the dwelling was fully constructed. This was both a pressurization and a depressurization test, achieving an average result of 0.30 Ach/hr – a permeability of 0.38 m3/hr/m2 at 50Pa. This is an exceptional result and far in excess of any dwelling I have tested previously.”
The HRV unit was a Paul Thermos 200, supplied by Pure Renewable Energy and installed and commissioned by ProAir Systems. Cyril Mannion explains that this unit was chosen because it’s certified by the Passive House Institute. “If we had used a non-certified ventilation we’d have to take 12% off the efficiency and we couldn’t afford that here.”
David McHugh of ProAir Systems points out that HRV is the only technology that’s essential in passive house construction. “It’s a whole new learning curve to do things the way the Passive House Institute want things done,” he says. “The main thing is, the unit is sited inside the insulated envelope, so the connections to outside from the unit are crucial. They have to go through the airtightness membrane, so you have to be very careful around it. Those pipes have to be kept as short as possible because they basically bring the outside in, so you have to insulate them almost to the level you insulate the walls. As a result, we had to make sure that they were going through in an airtight fashion and we had to make sure they were highly insulated.” Similarly, commissioning is a highly rigorous, tightly controlled process under PHPP.
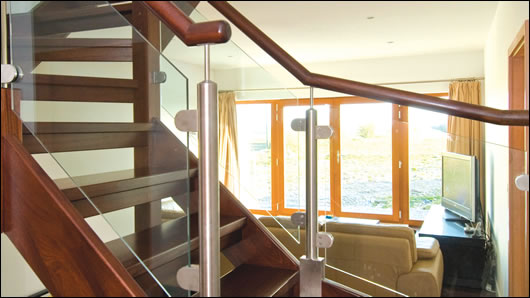
A timber staircase links the ground and first floor spaces, allowing heat to circulate through the house without fear of heat loss to the external
Two Dennen Boss Solar 40 evacuated tube panels with a rated heat output of 3.796 kW and a total aperture area of 3.796m2 are mounted on the roof. These feed a 300L tank backed up by conventional immersion. Client Scott Cook also intends to install a solar PV system to mitigate the electrical load and become fully self-sufficent – even to the extent of u charging an electric car. “If he installed PV and used electricity to heat his house,” says Cyril Mannion, “it would keep his BER in shape and cost him very little. It’s clean, it’s efficient and it works.” All lighting fixtures are 2w and 2.3w LED fittings from CT Electric, and were installed by electrician Sean Gavin.
Scott and Ann Cook are now four weeks in the house. “I always wanted something energy efficient.” says Scott. “I didn’t want to have an oil burner, I didn’t want radiators, so I started looking into it and I found out about this style of building. I believe it makes a lot of sense.” And how are the family finding the experience of living in a passive house? “It’s brilliant,” says Scott. “The way it holds the temperature all the time is amazing – without spending any money on heating. Cyril did a great job. This house went up in five months and we didn’t have any hassle. He did an awful lot of work in the design phase. It’s just a great place to live – it’s always comfortable. We deliberately don’t have any real heating system. Even in the cold days you burn a couple of logs and the heat goes through the whole house.”
Cyril Mannion estimates that passive building added between 8 and 10% to the cost of this 200m2 house. He believes that while designers generally are moving towards more sustainable building methods, the pace of change is slow. He also believes that there’s a lot of misinformation out there around both low energy and passive building. “People are being bombarded with sales guys coming at them from all sides. They put two panels on the top of a roof and all of a sudden it’s an energy efficient house. It’s not. You have to educate the designers first and not until they’re educated can you educate the public.”
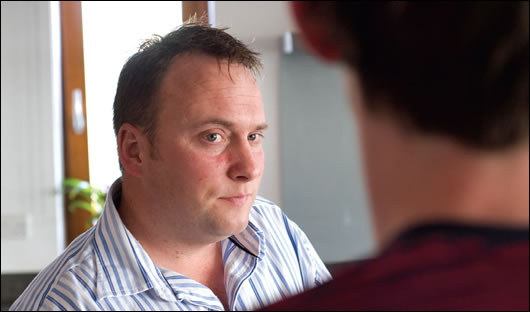
Cyril Mannion, of Passive House Builders, estimates that passive building added between 8 and 10% to the cost of the house
Selected project details
Design/main contractor: Passive House Builders Ltd
BER/airtightness testing: Energy Matters
Structure: Eco Timber Frame
Cement fibre board cladding: Greenspan
Windows & doors: Ecoglaze
Airtight tapes: Siga
OSB board: SmartPly
Wall and roof insulation: Warmcel
Service cavity insulation: Rockwool
Insulated foundations: Viking House
MVHR system: PURE Renewable Energy
MVHR installation and commissioning: ProAir
Solar thermal: Dennen Boss
- Articles
- Passive Housing
- Athenry
- passive house
- cement
- Fibre Board Cladding
- Siga
- Airtight
- Mannion
- Internorm
- Farko
Related items
-
Most polluting cements ruled out in Irish public procurement
-
Up to 11
-
Ecocem announces cement breakthrough to cut CO2 by 70 per cent
-
Big picture - New Zealand rural passive home
-
Podcast: what we've learned from 20 years in green building mags
-
45,000 more Irish homes face radon risk, new maps reveal
-
Passive house 30 years on: qualified success or brilliant failure?
-
Kilsaran launch lower carbon cement with CarbonCure
-
Above the curve - Limerick passive house showcases precision timber engineering
-
International passive house conference kicks off
-
Ecocem gets €22m investment from Bill Gates's climate fund
-
Strong demand for GGBS from Irish market