- Timber
- Posted
A-rated Cork eco home
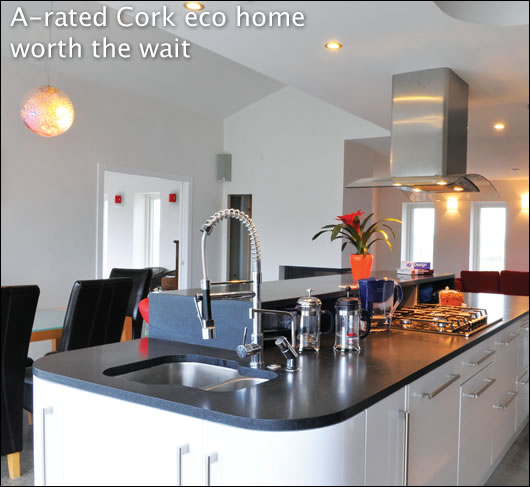
After a long struggle to build their home, Karen and Steve Ward finally got their wish — an energy efficient, timber frame house that boasts a palette of healthy and ecological materials and a fully renewable heating system.
Seven years ago, Karen and Steve Ward decided to leave their semi-detached home in Kinsale. “We kind of just outgrew it and we had to move on,” says Karen, who originally bought the house for herself. “It was very badly built and very badly insulated.”
The couple wanted to build a new home, but there were many twists and turns ahead. They spent six years trying to get planning permission on different sites in the area around Oysterhaven, Co Cork. Each time their design was re-worked to suit the site. Each time they failed to get planning permission.
The Wards grew frustrated with the planning process, which Karen says lacked consistency. One-off rural housing is often frowned upon by environmentalists — for a start, it encourages car use, often by commuters who live in the countryside and drive to jobs elsewhere. But Karen points out that that her husband — a carpenter and builder — works locally and has built and renovated many houses in the area. His mother ran a local restaurant for 20 years.
In September 2008, the Wards got planning permission for their fourth site. But then the property market crashed and Karen couldn’t sell her Kinsale home. The couple had planning permission for a house designed by Steve, but they couldn’t finalise the site purchase until Karen sold up.
Finally in December 2009 the couple sold the house, bought their new site and started planning to build. “It’s been quite a journey,” Karen says.
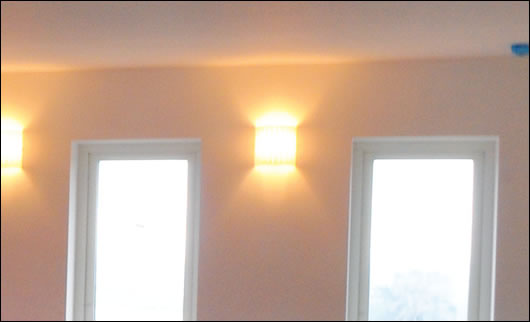
The house features low energy LED lighting throughout – the Wards avoided ceiling lights to so as not to puncture the airtight membrane
Though they originally planned to build with timber frame, they then changed to poroton (blocks produced from fired clay). Then they switched to concrete block with a wall cavity. “There were too many unknowns for us with poroton,” Karen says. “It hadn’t been tried and tested enough in Ireland.” But when they saw the price a local timber frame company — Eco Timber Frame — could offer, they reverted back to timber.
The couple chose timber frame “for insulating purposes more than anything,” says Karen. “We really wanted to use as eco friendly materials as we could. The timber frame ticked all the boxes. And we wanted to use local tradespeople as much as we could.”
Eco Timber Frame manufactured the frame — which was then insulated on site — in their Carrigaline factory. “You could see when we started talking to them early on that sustainability was important,” says Eco Timber Frame’s Stephen Spillane.
The walls of the house feature a 235mm cellulose-insulated stud with a 50mm Rockwool-filled service cavity inside this, while OSB board between the two serves as the airtight layer. Isocell supplied the cellulose insulation used in the walls and roof. The walls have a U-value of 0.14 W/m2K — better than Eco Timber Frame’s standard wall U-value of 0.16 W/m2K, which they achieve with a 195mm stud.
Inside, the walls are dry-lined with Fermacell, a high-density board produced from cellulose, gypsum and water — all of it recycled.
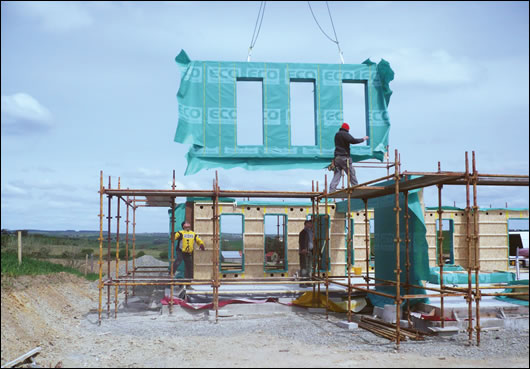
The Eco Timber Frame system being lifted into place on site
Outside the main stud there’s a 22mm woodfibre board, a 50mm cavity and an outer leaf of concrete block — not the greenest external skin, but Steve Ward mainly says they chose block based on price.
The house’s ground floor has five inches of Kingspan rigid insulation, and all partition walls were insulated with Isover’s Moy Plus acoustic insulation. The attic has a 400mm cellulose-filled stud in its floor, with an airtightness membrane under the joists and an uninsulated 30mm service cavity below that, giving a U-value of 0.1 W/m2K. The attic was designed to be habitable in future, though the roof rafters will need to be insulated. “The clients need to tell us they want that option and we’ve got to design for that,” says Eco Timber Frame’s Stephen Spillane. Outside, the roof is finished with slate made from recycled rubber, with Roofblock fascias and soffits – a maintenance-free masonry product made from 70% pre-consumer aggregates.
The airtightness strategy of using taped and sealed OSB board in the walls and a membrane in the roof worked well — a blower door test conducted by Eco Timber Frame gave the house a result of 1.25 m3/hr/m2.
The Swedish Trade Centre in Cork supplied all the house’s windows and doors. Manufactured by Markfonster, the windows are triple-glazed, argon filled and have two low-e coatings with an overall U-value of 0.9 W/m2K. Produced from slow growing timber from Sweden’s cold north — timber grows slower in colder climates, making it stronger and denser — the windows are clad with aluminium externally.
Markfonster also manufactured a large folding door at the back of the house, and the house’s two sliding doors. All are double-glazed, with two layers of low-e glass and a 16mm argon-filled gap. They have an overall U-value of 1.3 W/m2K. Another Swedish manufacturer, Bordorren AB, made the insulated front and back doors, which feature triple glazing and have overall U-value of 1.1 W/m2k and 1.2 W/m2k respectively.
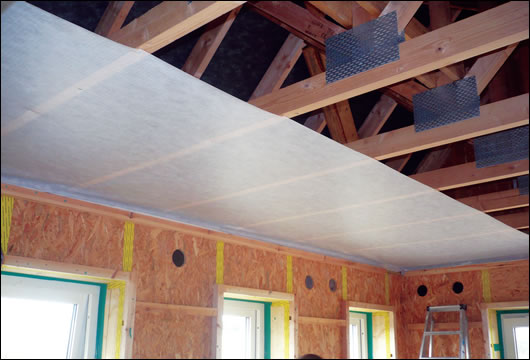
OSB board in the walls was taped and sealed to provide an airtight layer
Heat Merchants designed and supplied the house’s entire heating set-up, which includes a Wodtke Ray wood pellet stove. The stove supplies 80% of its heat to the house’s underfloor heating system and 20% to the surrounding air. Many similar stoves supply up to 40% of heat to the air but that risks overheating, says Heat Merchant’s Martin O’Connell.
The stove heats water that’s stored in a 300 litre buffer tank at about 60C before being delivered to the Rehau underfloor heating system. The house is divided into eight heating zones — one for each main room — with digital Heatmiser controls in each. “Each one of those has a time and temperature control,” says O’Connell. “They can turn it on manually, turn it off manually or work it on a time clock, and they can monitor the temperature in those rooms.” The house has an exposed and polished concrete floor throughout, which allows for more efficient heat transfer from the underfloor pipes to the room, allowing water in the pipes to be kept at a lower temperature.
If the temperature in the house drops below 15C, the underfloor heating draws hot water from the buffer tank. Once the temperature of the tank drops below 50C, the stove kicks on automatically. The house also has an array of 30 Kingspan Thermomax HP200 solar evacuated tubes — connected to a separate 300 litre domestic hot water tank — which heat water along with the stove. The house also has an Itho heat recovery ventilation system with rigid insulated ducting, supplied by Control Aer.
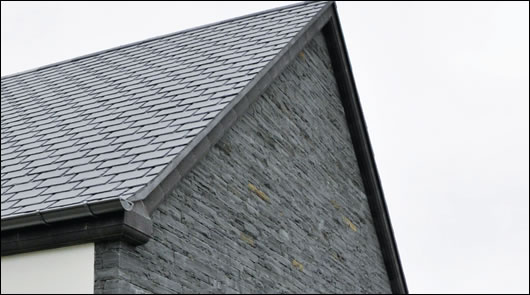
The roof features Roofblock fascias and soffits – this is a maintenance-free masonry product made from 70% pre-consumer aggregates
The house features a rainwater harvesting system too, supplied by Ireland Waste Water. Rainwater is collected on the roof and runs to a 7,200 litre underground tank, where it’s filtered for leaves and debris and pumped to a tank in the attic before it feeds toilets and outdoor taps. The underground tank can hold enough water for a ten day dry period.
“We can leave the tanks overground in existing houses, but 80% of the time they’re put underground,” says Ireland Waste Water’s Niall Mulcahy, who says that homeowners retrofitting rainwater harvesting systems sometimes opt to avoid the disruption and digging that comes with an underground tank. Ireland Waste Water can also install a UV filter that enables the system to supply sterilised water to washing machines and dishwashers.
Low-energy LED lighting features throughout the house. Steve Ward says cheap LED bulbs tend to blow out quickly, and he’s had to return more than a handful of faulty bulbs. But he says that while good ones are expensive, they certainly last. “When you get a good one they have something ridiculous like 15,000 hours [lifespan],” he says. “But if you get a bad one they’ll break your heart,” he says. The couple opted against ceiling lights to avoid puncturing the airtight membrane.
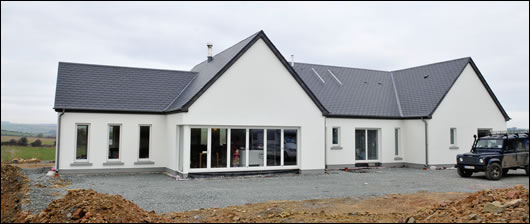
The aluminium clad timber windows are triple-glazed and argon filled, and are produced from slow growing timber from Sweden’s cold north, which results in denser and stronger wood
The Wards aimed to choose healthy materials throughout the house too, shunning products high in volatile organic compounds. “We used the Fermacell board in the walls, Rockwool, and cellulose insulation,” Steve says. “Even the paint was made from clay [they used Earthborn clay paints].”
Karen says they’ve “tried to stay true to the plan of building a healthy home.” They also plan to install a reed bed wastewater treatment system in future.
The Wards moved in just before Christmas, and had been living in the house for less than a month when Construct Ireland spoke to them. They’d brought the heating on slowly over the previous few weeks to gradually bring up the temperature of the concrete slab, which could be damaged if the heat was turned on suddenly to full temperature.
But on Christmas Day the heating was off. “When we started putting the ovens on and getting a few bodies in it went up to 25C and that was with the outside doors open. We couldn’t even light the fire,” Steve says. They’ve since fine-tuned the system to prevent overheating, and Steve reckons they’re using about 10kg of wood pellets a day.
A BER assessment of the house gave it a provisional A3 rating – an achievement made all the more difficult given the planners’ insistence that the house be just one storey, therefore increasing the surface area through which heat loss could occur. For Steve, to actually be living in the house seems surreal. “I designed the building and everything,” he says. “It's been an ongoing project and to finally be living in it is mad."
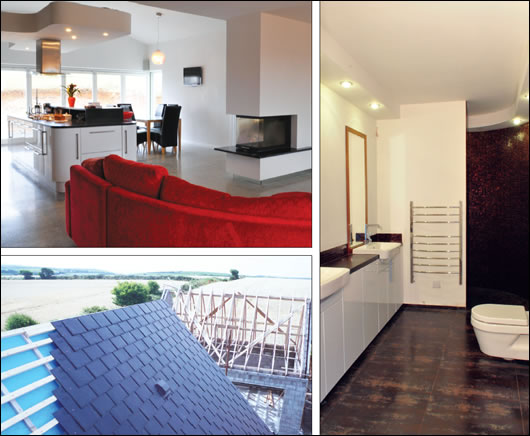
(clockwise from right) Toilets are supplied with rainwater collected on the roof and pumped into an attic tank; the roof is finished with slate made from recycled rubber; the main living area has a Wodtke Ray wood pellet stove that supplies the underfloor heating system
Selected project details
House design: Steve Ward
Timber frame: Eco Timber Frame
Additional wall insulation: Rockwool & Isover
Windows and doors: Swedish Trade Centre
Heating system: Heat Merchants
Rainwater harvesting: Waste Water Ireland
Roof slate: Authentic Slate
Fascias & soffits: Roofblock
Natural paint: McDonnell Paints
Overview
Location: Oysterhaven, Co Cork
Building: 1500 square foot detached bungalow
Build method: timber frame
Provisional BER: A3 (74.6 kWh/m2/yr)
Provisional CDER: 5.77 kg CO2/m2/yr
Airtightness: 1.25 m3/hr/m2 at 50 Pa
Walls (from the outside in): concrete block outer leaf, 50mm ventilated cavity, 22mm woodfibre board, 235mm stud insulated with cellulose, airtight OSB layer, 50mm service cavity insulated with rockwool, Fermacell board
Roof (from the bottom up): 30mm uninsulated service cavity, airtight membrane, 400mm cellulose filled joists in walkable areas of the attic (900cm+ in un-walkable areas)
Ground floor: five inches of rigid Kingspan insulation
Windows: triple-glazed timber Markfonster alu-clad, argon filled with two low-e coatings and an overall U-value of 0.9W/m2K
Sliding and folding doors: double-glazed with an overall U-value of 1.3W/m2K
Heating: Wodtke Ray wood pellet stove supplying Rehau underfloor heating and 300L buffer tank with 30 Kingspan Thermomax HP200 solar vacuum tubes supplying to a separate 300L domestic hot water tank
Heating controls: eight zone heating system with Heatmiser controls
Ventilation: Itho mechanical heat recovery ventilation unit with rigid ducting
Green materials: Fermacell dry lining board, recycled slate, cellulose insulation, clay-based paint