BEMS - Building Energy Management Systems
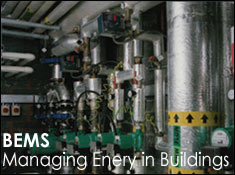
The energy-saving benefits of Building Energy Management Systems are well known. BEMS systems can improve comfort levels in buildings, enable better maintenance and deliver financial savings of up to 20%. This, in turn, reduces impact on the environment caused by emissions of greenhouse gases – giving both financial and environmental benefits. The savings created through using a BEMS can be substantial and recur year after year.
What is a BEMS?
Building Energy Management Systems (BEMS) are computer systems, which enable the system operator to monitor and control building services including heating, air conditioning and lighting. The BEMS collects information on the building including temperature, pressure, light level, water level, valve or damper position and uses this information to make decisions on when and how to operate energy consuming systems in an efficient manner. The BEMS can be configured to match any building size and to meet the user’s requirements.
Building Energy Management Systems are reliable and flexible systems that take advantage of current hardware and software technology. Additional features and monitoring points can easily be added to existing systems. Since the BEMS is computer based, the data and the decisions being made can be readily presented in graphical form on a standard PC, and can be made available on a business network or the worldwide web if desired.
Critical or urgent data can be sent via SMS text message, e-mail, or bleeper to maintenance staff either in the building or on the far side of the country. As much or as little data can be presented to as many or as few people as required, such that people receive just the information they need. Traditional controls cannot provide these features.
The computerized nature of the systems makes them capable of using sophisticated logic to make decisions, which help save energy. The systems can be re-programmed to follow new logic if required. Traditional controls use fixed hardware to control plant and are expensive and difficult to alter.
What is the “Point”?
Each item, which a BEMS monitors, or controls is called a “point”. “Points” can either be “inputs”, (for instance temperatures), pressures or “outputs” (for instance pump start/stop or open/close heating valves). A small building may have a BEMS with 10 or less points. A large BEMS may have thousands of points. An organization may have BEMS on multiple sites around the country that are linked to a central location, which can then monitor thousands of points.
Through the graphic or keypad displays, staff can input desired conditions and set operating times. Users can view diagrams or picture of the various systems with real-time information such as internal and external temperatures. As soon as conditions drift outside prescribed limits, the BEMS notifies the maintenance staff, allowing them to carry out essential maintenance.
The BEMS operator can view live or recorded data in detail in a graphical form, such as a graph of a room temperature over 24 hours, which might clearly show that the heating is operating when not required. This might be more difficult to detect if a BEMS was not in place. The BEMS can be used to identify electrical equipment that operates when not required, which typically might be at night or at weekends, as it can record electrical energy at regular intervals, such as every 15 minutes.
BEMS – Growing Technology with Shrinking Costs
Since finding its first commercial use more than 20 years ago, the BEMS technology has vastly improved while the actual costs of installing systems have made BEMS much more cost effective for smaller buildings. A small inexpensive system can be cost-effective in buildings with annual energy bills as low as €10,000. The cost of a new BEMS system is competitive with installing less efficient traditional control systems.
For large organisations with buildings of various sizes spread across a wide area – such as supermarket chains - an outstation at each site can be linked to a single overall control location via mobile phone, landline or the Internet. With the spread of always-on broadband, the BEMS data from remote sites can be also be “always available”, rather than having to dial into the system to gain access.
Recent advances in BEMS technology allow further savings in costs through innovations such as web-page serving, allowing any standard PC with a web browser to interface with the systems. This not only reduces capital costs, but also enables more people to interface with the system, with less training required.
Optimum Heating Systems Control
One of the most important areas influenced by BEMS is heating or air conditioning control and the benefits here of using BEMS can be very marked. The traditional way of controlling the on and off times of this plant was with a time clock. To cater for the coldest (or hottest) day of the year, the time clock had to be set to switch the plant on perhaps an hour or two before occupancy began, and to keep the plant on until the occupants left.
With a BEMS, the system monitors room and outdoor temperatures. The BEMS learns the characteristics of the space from this data to determine the last possible moment to bring a plant item on and the earliest possible moment to switch an item off, whilst maintaining required conditions during occupied periods. In this way, on mild days, the plant might be brought on just minutes before occupancy begins, and plant might be switched off hours before occupants leave. The energy saving are significant. Moreover, plant maintenance is reduced due to shorter plant operating hours per year.
Zone and Time Control
BEMS are used to great effect in controlling the central heating or other systems in buildings, which can be divided into various zones. Using any networked PC, staff can schedule room occupancy times in advance and have a room (such as a conference room or cafeteria), an area (such as function rooms of a hotel open to the public only part time) or floor (such as particular floors in a high-rise building rented out to tenants) of a building at conditions most beneficial to user needs. When zones are not occupied the heating for that zone or area can be easily turned off without affecting the remainder of the building.
Bank holidays can be programmed using the BEMS. In many buildings with conventional controls, the plant continues to operate on bank holidays because it is too time consuming to switch plant off. This alone can lead to 8 working days out of about 200 per year where the plant might be operating unnecessarily.
The Electronic Engineer - Alarm Reporting
The BEMS allows system engineers to monitor all the systems without the need to visit the various plant rooms. It notifies the engineers of problems often before the occupants are aware of them. For example, as soon as a temperature is higher or lower than prescribed limits, the building maintenance staff are alerted either at a PC, via text message, or bleeper. The problem can be corrected before the building occupants are aware of a noticeable temperature difference. By monitoring system faults from the various specialist systems around the building from a central point, maintenance is faster and more responsive.
The Electronic Engineer - Monitor and Targeting
Throughout an organization, electricity meters can monitor electricity use in various areas such as lighting, compressed air or air conditioning. Using the information, graphs of electricity usage can be plotted which allows management to formulate the optimal electricity usage plan. The usage can be analyzed against other parameters appropriate to the building such as number of residents in a hotel, units of production in a factory, or number of occupied beds in a nursing home. Similarly, fuel meters, water meters, heat meters and so on, can be monitored and analyzed against similar parameters. Once a norm is established, such as electricity usage per bed-night, the BEMS can be programmed to alert when energy usage drifts away from the norm. The data can also be used to see the effect of operational changes or energy saving investments.
The Electronic Engineer - Maintenance
BEMS bring together the various engineering systems in a building under a single system to report faults and adjust controls remotely. These can include areas such as food refrigerator temperatures; gas detection systems, water treatment and emergency lighting.
The BEMS monitors the air filters in air-handling units indicating when the filter needs changing or cleaning. This not only reduces the need for routine maintenance checks, but also ensures that filters are not allowed to clog up, helping to maintain air quality and reduce fan energy use.
The number of hours each item of plant operates can be counted and preventative maintenance carried out after a fixed number of running hours.
The Electronic Engineer – Procuring a BEMS
A wide range of European and Irish companies manufactures the hardware and software that go into BEMS. Usually systems are bought from local distributors who design the system including hardware and software for each particular building. These distributors, sometimes referred to as system houses, provide all the necessary equipment, install, test and commission the system, train the client in its use, provide operation and maintenance manuals, and provide an ongoing maintenance service.
There are two main routes to procuring a system. Either the user can approach system houses themselves and invite tenders, or ask a consulting mechanical and electrical engineer to prepare a specification which describes what is required against which tenders can be obtained.
In the first case, care should be taken to ensure that the user understands what is being offered from each company. One company may offer a lower cost system but this may have fewer monitoring and control points and less features than other systems.
In the second case, the consulting mechanical and electrical engineer will obtain tenders, compare them, recommend a contractor, administer the contract, and see through the installation, commissioning and training.
BEMS – Keeping the Business Fit
A BEMS can act as a master system that combines all of the different engineering systems in a building under a unified control. All aspects of energy usage and plant items costs can be monitored and kept functioning optimally.
BEMS – Further Reading
Several Good Practice Case Studies are available on the Sustainable Energy Ireland web site, or directly from Sustainable Energy Ireland (SEI), including ones covering BEMS use at University College Dublin and the Mater Private Hospital Dublin. BEMS have been central to controlling energy costs and improving the reliability of systems at these exemplary sites and at numerous other locations. These users have been able to save energy and money whilst guaranteeing the highest level of building occupant comfort and a healthy environment. A booklet, BEMS Good Practice Guide 1, is also available from SEI