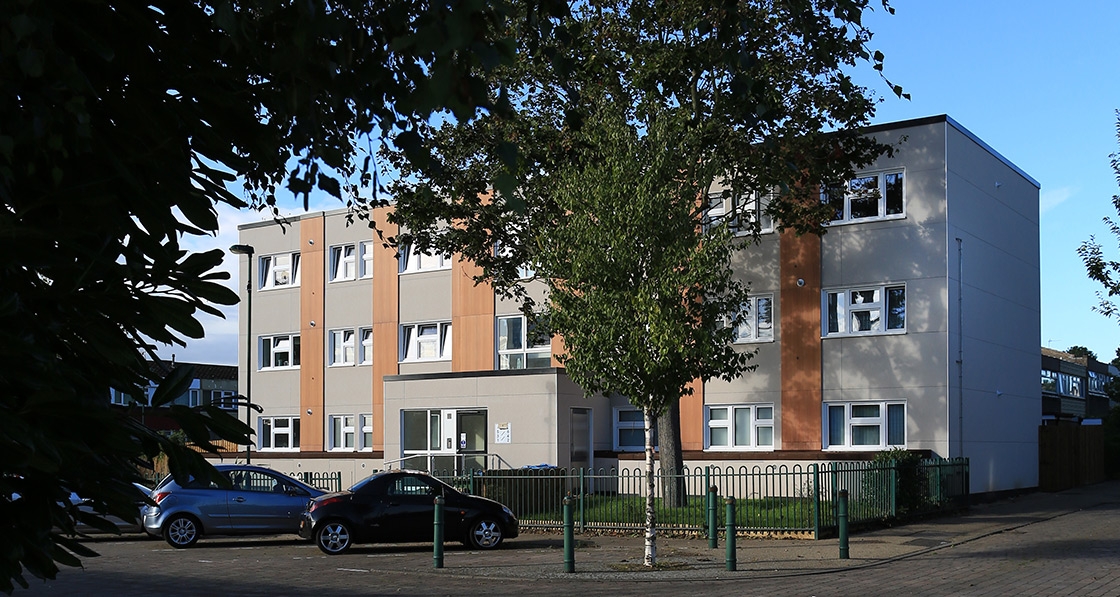
- Upgrade
- Posted
Solihull upgrade trials revolutionary retrofit approach
An exciting and innovative new deep retrofit project in Solihull has drastically cut the energy consumption of a small block of flats by smoothly and efficiently wrapping the entire structure in both insulation and ventilation ducting, delivering huge energy savings and minimal disturbance to the residents.
Click here for project specs and suppliers
This article was originally published in issue 18 of Passive House Plus magazine. Want immediate access to all back issues and exclusive extra content? Click here to subscribe for as little as €10, or click here to receive the next issue free of charge
We’re all well aware that our existing housing stock is not up to scratch and that — for reasons including climate change, comfort, health and wellbeing — mass retrofitting is essential. A few exemplar projects have shown us the light. There have also been government initiatives encouraging us to take action, yet progress is minimal and certainly not at the rate needed to make all of our housing zero carbon by 2050. That is also putting to one side the hundreds of thousands of new buildings that do little to get beyond building regulations and therefore will ultimately need to be retrofitted at some point in the future. It’s a painful situation.
So what is going wrong? Matthew Rhodes, managing director at passive house consultancy Encraft, believes that economics is one of the key barriers. “It is simply very expensive to design and deliver bespoke solutions for every existing building in the country, given the tremendous variety in our housing stock. I also think there is a paradigm problem, in that we do tend to look for one-size fits all solutions, and shortcuts on quality to minimise cost, and this approach simply won’t work when crudely applied to existing buildings,” he says.
On site during the retrofit of Grandys Croft, including a view of how the building looked prior to the installation of the new TCosy system and render board externally.
An opportunity arose to pilot a new approach when Innovate UK launched their Scaling-up Retrofit competition, which encourages applicants to re-think supply chains and deliver a price-focused deep retrofit proposal with performance guarantees for customers.
Encraft submitted a proposal, alongside partners Beattie Passive, Solihull Metropolitan Borough Council, Solihull Community Housing and Coventry University – to trial a whole building retrofit solution called OWLS (off-site wrap-around large scale retrofit) and this project in Solihull went on to become one of only nine projects in the UK to receive funding.
Matthew Rhodes explains how it works. “The core idea of the OWLS project is that instead of looking for a single system or technical solution to work for as many buildings as possible, we focused instead on simplifying the process of retrofitting to reduce cost as much as possible, while being rigorous around quality.”
As part of the competition this all-in-one solution, which minimises thermal bridging and aims to achieve the Passive House Institute’s retrofit standard, Enerphit, would be applied to a low-rise block of flats.
Encraft was keen to work with Beattie Passive on the project because they liked the simplicity and adaptability of Beattie’s timber-frame building system— and also the way Beattie are willing to work with local people to transfer construction skills. But while Beattie Passive’s system has been used hundreds of times for passive house new builds, it’s early days for its use in retrofit.
Ron Beattie, managing director of Beattie Passive, says he has always envisaged that the company’s new build system would transfer to retrofit. “What we needed to come up with, and what the innovation that we did was, how we get a new building over the top of an old building, and how we can incorporate the MVHR system.”
A common analogy when explaining how passive house insulation works is that it’s like putting a tea cosy around a teapot. Well, Beattie Passive has created their own retrofit system which they’ve called TCosy (a term they’ve trademarked). It’s a deep retrofit and upgrade ventilation system all in one.
Having first been applied in Oxfordshire to extend and retrofit a private dwelling, it was now ready for a bigger trial on one of Solihull Community Housing’s properties.
(left to right) The MVHR units are located outside of the flats to avoid disturbance to tenants when maintenance is necessary; installation of the Beattie Passive TCosy retrofit system that was installed externally; MVHR ductwork was incorporated into the TCosy system to minimise the internal works normally required with the retrofitting of such systems.
Mark Pinnell, head of asset management at Solihull Community Housing, explains how they got involved: “We were asked to participate in this collaborative project designed to test out retrofitting of a passive standard insulation system on an existing residential block of flats. We had no previous experience of installing this type of insulation but were aware of the benefits so were very keen to be involved. We have a strong commitment to improving the energy efficiency of our homes and this project makes a real contribution.”
Finding a suitable candidate building was actually quite challenging. Dr Sarah Price, senior consultant at Encraft, explains the type of building they were looking for. “It had to be hard to treat so it had to be one of the sort of post-war system builds which are often just concrete, brick, a mixture of all sorts of things, nobody really knows how they were built. We wanted a low rise flat because all their high rises have been done, or are in the process of being done. And there’s a lot of solutions out there for high rise and a lot of funding for high rise so we needed something for the smaller blocks.”
Ultimately it came down to a choice of two buildings where all of the occupants were Solihull Community Housing tenants. Other blocks of this type, for example, had one or two flats in private ownership. Grandys Croft, a rectilinear building comprising six flats, was chosen.
The process for this retrofit started with a survey of the existing building, including a thermal survey and airtightness test, to assess its structural condition.
Ron Beattie outlines the next steps: “We then do a project plan with the client and we look at digging a hole around the external part of the building and that’s going to go 600mm down to the foundations. And that means that of course all our existing drains and services that are in around that area, need to be repositioned because what we’re going to do is we’re going to drop a new TCosy, a new house form, over the top of the existing building.”
An inspection of the foundations can then establish whether the new structure can be hung off the existing foundations or whether some new foundation blocks might need to be introduced. “Once that’s done we then create a DPM [damp proof membrane] that runs around the building and is sealed off at damp course level. And damp course level is the level just underneath your door plate, the sill in your door which normally runs and stops any moisture rising up the building. We don’t want to bridge that DPM so we seal our new box up to that point and that stops any moisture then rising up above the DPM.”
“We then put a shoe which is either bolted or connected to the foundation brickwork, or a new foot that sits down to a new foundation.”
This is where the prefabricated panels, complete with ventilation ductwork, doors and some of the finishes, can be dropped in.
The TCosy system at Grandys Croft was constructed on site. And the innovation of integrating the MVHR externally was in response to a specific problem.
Sarah Price says: “The ventilation actually changed from natural ventilation to mechanical ventilation halfway through the build because really Beattie Passive system is an airtight system, and they always have MVHR in all of their new builds. So they really wanted MVHR but the problem was we couldn’t put it inside the flats. We couldn’t install the ductwork inside the flats. So they were trying to find a way to get the ductwork into this retrofit and it wasn’t until quite late on that they actually came up with these designs. So that was a real change.”
By creating a void around the outside of the building and then incorporating the MVHR system within that, it became possible to alter the ventilation strategy.
Sarah continues: “Total Home Environment did all the calculations for the ductwork, flows and the pressure drop and the noise levels, they are really experts in MVHR design. They estimated that actually it would work with the long ductworks. So we trusted their calculations and their experience and they came and installed it and commissioned it.”
A benefit of locating the MVHR units outside of the flats is that maintenance – including replacing filters in the units – can be done without disturbing tenants. But there are also filters on the kitchen extract valve in each flat to prevent grease getting into the ductwork.
As Solihull will be accessing the flats once a year to service the boiler and to run gas safety checks, replacement of these filters has been built into that regime.
Part of Coventry University’s monitoring will ascertain whether each flat has the desired indoor air quality, given the unusual MVHR configuration. If so, it offers a tantalising prospect for deep retrofits: the ability to keep occupants in their homes during the retrofit and limit disruption.
Mark Pinnell from Solihull Community Housing says: “As with any major retrofit or refurbishment project the key is managing the impact on the residents and ensuring there is constant and proactive communication with them. We were fortunate in that Beattie Passive managed this part of the project extremely well.”
Beattie Passive also injected quite a bit of finance into this project, but see this as an important investment for the future. Ron says: “The lessons we’ve learned have let us jump two or three years.”
With so much variation in our existing buildings Ron believes flexibility is essential in future manufactured retrofit solutions. “The future of retrofit is going to be a very simple process that will use 3D printing machines. We will look at façades, we will stand them up in front, and then we will inject them with insulation. And that will be a very quick, fast process down to a couple of days of on-site work. Looking however you want it to – brickwork, render, stonework. It will all be able to be reproduced in the future.”
For Encraft, this project highlighted the human side of things too. Matthew Rhodes explains: “The key thing is to focus on skills and standards in the project team, not just on technologies and systems. This includes soft skills, like dealing with occupants so that they co-operate during the project and can get the best out of the building once the project is complete.”
As part of Encraft’s work into scaling up and rolling out retrofit, they produced a paper looking into the cost of retrofit. Sarah Price recalls: “This three-storey block of six flats is on the borderline of what would pay back. So it would pay back in about 30 years on tenants’ bills.”
This assumes being able to recoup the savings on the tenants’ bills. “There’s a lot of nervousness out there from social landlords about service charges in particular. Because if you get into rent arrears you can’t recoup the costs of the service charge in court.” Making retrofit stack up financially is still a core issue when it comes to wide-scale uptake.
For now, everyone is pleased with this outcome. By all reports the residents at Grandys Croft have been very positive about the refurbished building, though they have yet to experience the benefits during the colder winter months.
Selected project details
Client: Solihull Community Housing
Architect: Beattie Passive Retrofit
Main contractor: Beattie Passive Retrofit
Build system supplier: Beattie Passive Retrofit
Energy consultant: Encraft
Civil & structural engineering: Canham Consulting
MVHR: Total Home Environment
Electrical contractor: Corrigan Electrical
Airtightness tester & thermal imaging: Air Testing UK
Wall insulation: Springvale
Roof insulation: Springvale
Airtightness products: PYC Systems
Airtightness products: EH Smith
Windows: Elwiz SA
Entrance door: Warrior Doors
Cladding: Steni
Roofing: JMG Roofing
Additional info
Building type: A three-storey block containing six low rise flats of concrete and brick construction. Retrofitted to the Enerphit standard using the Beattie Passive TCosy system. Innovate UK funded project.
Location: Chelmsley Wood, Solihull, UK
Completion date: June 2016
Budget: £625,000
Passive house certification: Enerphit certification pending
Space heating demand (PHPP): 24 kWh/m2/yr
Heat load (PHPP): 14 W/m2
Primary energy demand (PHPP): 121 kWh/m2/yr
Airtightness (at 50 Pascals): 0.93 ACH at 50Pa
Energy performance certificate (EPC): Pending
Measured energy consumption: Monitoring equipment in place will allow post-completion data to be compared to a year of pre-project data
Thermal bridging: Thermal bridging was eliminated by use of the TCosy system, with a continuous layer of insulation around the building. Insulation continued below ground and windows were installed in the insulation layer.
Ground floor: 150mm Concrete ground floor uninsulated as before. U-value: 4.082 W/m2K
Walls: Beattie Passive timber frame system, as below. U-value: 0.099 W/m2K Above ground: Pre finished render board externally followed by battening, breather membrane, 50mm Kingspan Insulation UK Kooltherm K5 insulation, 12mm Versaliner, timber frame filled with platinum Ecobead, airtight membrane to existing masonry.
Below ground: 12mm plastic skirt, followed inside by battening, breather membrane, 50mm EPS insulation, 12mm Versapanel, timber frame filled with platinum Ecobead, Monarflex DPM membrane lapped with airtight membrane on existing masonry.
Roof: Beattie Passive timber frame system. Felt roof covering, followed underneath by 12mm plywood, 75mm EPS insulation, 12mm plywood, timber construction 220mm Ecobead insulation, air tightness membrane, 18mm plywood, 50mm wood wool insulation, on 220mm concrete. U-value: 0.1 W/m2K
Windows: Triple-glazed Elwiz Energio passiv PHI certified PVC window. U-value: 0.9 W/m2K
Entrance door: Fully welded stainless steel communal entrance door with an African close grain cedar core, including double-glazed argon filled sealed units. Glazing U-value: 1.1. Frame U-value: average of circa 4.3. There were some very significant thermal bridges as part of the construction of the door, which was chosen for secutity purposes. Care was taken to ensure the seals – rubber gaskets around the frame and the magnetic locking system – were as airtight as possible.
Heating system: 90% efficient individual gas boilers to each unit, supplying existing radiators
Ventilation: Heinemann Vallox KWL90 MVHR system. PHI certified heat recovery efficiency of 79%. Ductwork installed in insulation layer with MVHR units in external insulated cupboards accessible by the housing association.
Image gallery
Passive House Plus digital subscribers can view an exclusive image gallery for this article