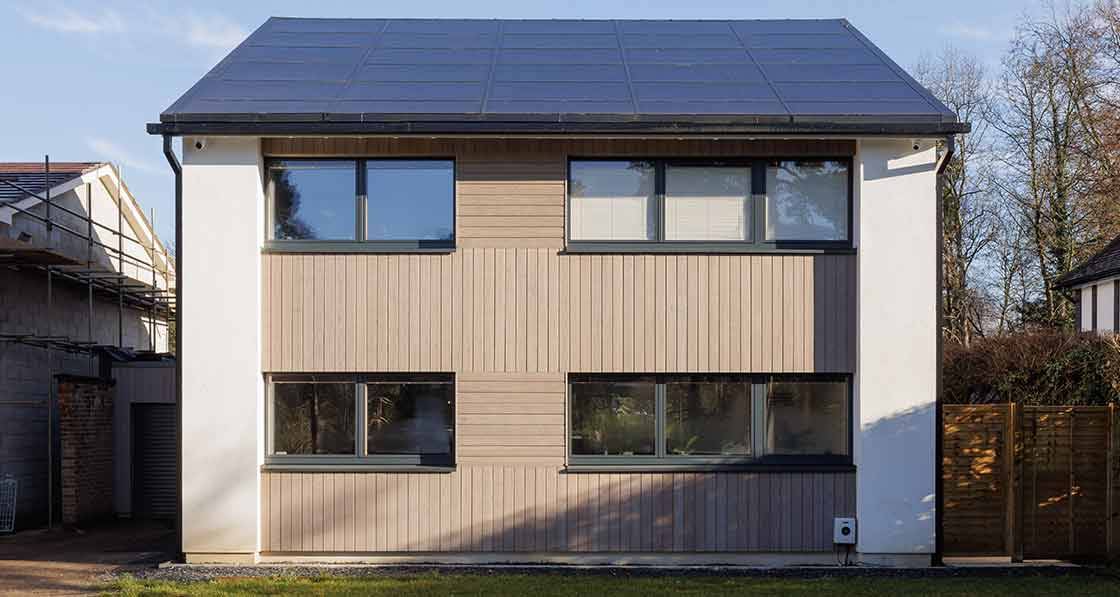
- Upgrade
- Posted
Phit the bill
A passive house, by its nature, requires a much smaller amount of energy than a typical home, and when its heating demand is met by electricity, and you cover it in solar PV panels, you can start to see the potential for a whole new generation of passive homes that are semi-independent of the electricity grid. This is the case for Carrstone House in Bedfordshire, which generates so much solar energy it had to be registered as a power station.
Click here for project specs and suppliers
Building: : Deep retrofit & extension of 151 m2 detached 1960s house
Method: External wood fibre insulation, timber frame, air-to-water heat pump
Location: Harpenden, Hertfordshire
Standard: Enerphit Plus (certified)
Heating cost: £23/month*
* Based on monitored energy use for space heating – adjusted to current UK energy price cap and ignoring PV reduction.
See ‘In detail’ panel for more information.
A radical retrofit in a conservation area sounds like a recipe for trouble, but despite challenges including planning and a general lack of understanding in the national market, one project in Harpenden, St Albans, Hertfordshire has led the way, demonstrating just how much energy performance can be improved in old houses.
Owners Jonathan and Emma Dixon were inspired to take on the challenge by a number of factors including their own professional backgrounds as well as experiences abroad.
“I guess, it came from a few different aspects. Since we bought our first house in 2005, I’d always been interested in generally reducing energy use and using decarbonised energy sources, solar and so on,” Jonathan Dixon said.
Both engineers by profession, the Dixons were not only keenly aware of issues around energy consumption and embodied energy, but were also inspired by travels around Europe, and in comparison to what they saw, they found UK housing stock lacking.
“We saw better quality houses, particularly in Switzerland. We [also] lived in California and saw how terrible houses were there: drafty and not well-insulated,” he said.
The differences in mainland Europe were twofold: on the one hand a greater understanding of energy issues and sustainability, but also better production processes and onsite controls.
“In countries like Germany there is a basic level of building control and standards. They’re years ahead of us in the UK,” he said.
On returning to Britain the couple decided to do something about it. However, on moving back the couple were living in London but planning to move out to Hertfordshire to stay within a relatively easy commute of the capital. A partial rebuild was considered, but proved too costly in terms of time, so the couple settled on a retrofit and small extension on a 1960s house.
Before
(inset) Before
This article was originally published in issue 43 of Passive House Plus magazine. Want immediate access to all back issues and exclusive extra content? Click here to subscribe for as little as €15, or click here to receive the next issue free of charge
What was not yet obvious, however, was just how comprehensive this project would be. Experience of low energy housing and a chance conversation drove the project toward a deep retrofit and passive house standard.
“We envisaged a relatively small project, but it grew in the process as I started to think about what they do in other countries. I hadn’t heard of the term passive house in 2018, but a friend of mine was doing a retrofit and I started to research it,” Dixon said.
Finding skills and support
The single most important part of the research was finding an architect who could create the design and complete the project, no small task given how rare such deep retrofits have been in Britain.
The answer to this conundrum was Heather McNeill of A D Practice in St Albans, to whom the couple turned having considered nine different practices.
“We found Heather, a qualified passive house architect. She spearheaded it and helped us to get it over the line,” said Dixon.
“We spoke to nine different architects, four local without passive house experience [and] four regional ones with passive house experience. We were really struggling to choose and then we happened to see Heather on Facebook. We really liked the things she said to us, pointing out aspects of the way the house was built and ways the quality of the build could be improved. She was really thinking outside of the box,” he said.
Indeed, McNeill is an experienced architect with a background in sustainability. She also has unusual experience in retrofits. After taking her first job working in CAD at the A D Practice she studied for her Part 1 at the University of Bath, and had a stint in practice before completing her Part 2 at the Centre for Alternative Technology in Machynlleth in Wales, demonstrating a strong interest in sustainability.
“I did my Part 2 there because that was the direction I wanted to go,” she said. Now a certified passive house designer, the Dixons’ Harpenden house formed the basis for McNeill’s Part 3 case study at Kingston University, a happy coincidence that drove the project forward.
“You learn all the theory, but there’s a lot more to it than that. I got the job almost by accident: we were the ninth architect they’d spoken to and this being a retrofit it’s arguably more difficult to do. As it was my case study for my Part 3 exam, I lived and breathed it,” she said.
The first challenge McNeill faced was planning: the house is in the Harpenden Common conservation area.
“It’s a very notable house where it is, so people would notice it [and] it was the end of a row of six, so it had to keep similar proportions to the existing houses,” she said.
As is typical with 1960s buildings, a lot of work was required to get the house up to modern standards of energy efficiency, let alone Enerphit Plus.
(inset) Before
I might well make an operating profit on energy generation in the next year
“When we turned up outside, we found it had a very thin curtain wall and our first thought was to put in proper, insulated walls.”
In the end, the existing brickwork walls were externally insulated using wood fibreboard and finished with a painted render, and the curtain walls were removed and replaced with new highly insulated timber I-beam walls with cellulose insulation and clad in larch. The rear single-storey extension was also constructed in this way and finished with either render or timber cladding. The existing ground floor was removed and replaced with a new highly insulated slab with underfloor heating.
Planning was not a problem, with McNeill describing the planners as relaxed. This despite the entire roof being a solar array.
“The classic [planning] problem is where renewables come in, but they [the authorities] were really keen,” she said.
“It was about aesthetics as well as getting maximum performance. We’re in a conservation area and the south-west pitch directly faces the road and no one else had solar installed,” said Dixon.
Like many aspects of the project, this array did require some extra care, but it was nonetheless a success.
“For the contractors it was their first retrofit [and] the fully integrated solar needs a fully square and true roof. The undulations meant it needed that bit of extra work,” said Dixon. “They’ve [the local planning authority] now got a default position of favouring sustainable measures, but we never wanted the retrofit look.”
Unexpected stop
However, before any of this work could be completed, external factors intervened in the form of the world’s largest spanner in the works: the coronavirus pandemic.
“We started in January 2020 and then, in March, the pandemic hit, and everything shut down. We had just done our demolition and had a house with no front wall, everything had to stop. That was a slightly hairy moment,” said Dixon.
As a result of strict regulations, not only did work have to stop, but the owners were prohibited from visiting the site until distance restrictions were lifted.
-
Original rear elevation with curtain wall panels removed and extension slab laid Original rear elevation with curtain wall panels removed and extension slab laid
-
Existing rafters underlined with rigid woodfibre board and opening trimmed out for rooflight over stairs Existing rafters underlined with rigid woodfibre board and opening trimmed out for rooflight over stairs
-
Airtight membrane taped around original roof trusses in loft space housing MVHR Airtight membrane taped around original roof trusses in loft space housing MVHR
-
Airtight taping and service void around flat roof light in rear extension Airtight taping and service void around flat roof light in rear extension
-
Insulation upstand below service void prior to screed being poured Insulation upstand below service void prior to screed being poured
-
I-stud construction to rear extension lined with Smartply I-stud construction to rear extension lined with Smartply
-
PIR plinth insulation and stop bead up to DPM level ready for external woodfibre insulation to be installed above PIR plinth insulation and stop bead up to DPM level ready for external woodfibre insulation to be installed above
-
Vent penetration through external wood fibre insulation Vent penetration through external wood fibre insulation
-
New window installed in existing cavity wall, protruding from brickwork to link into external insulation layer New window installed in existing cavity wall, protruding from brickwork to link into external insulation layer
-
External woodfibre insulation installed on the rear extension around the picture window External woodfibre insulation installed on the rear extension around the picture window
-
Render beads and base coat applied to woodfibre insulation around window opening Render beads and base coat applied to woodfibre insulation around window opening
-
Plywood stop plate installed at end of woodfire insulation/ thermal line Plywood stop plate installed at end of woodfire insulation/ thermal line
-
Woodfibre sheathing board installed over the insulated doubled-up rafters Woodfibre sheathing board installed over the insulated doubled-up rafters
-
Roof membrane taped and installed over exposed rafter feet to be lapped into gutter Roof membrane taped and installed over exposed rafter feet to be lapped into gutter
-
Aluminium frame installed on front roof pitch for seamless solar pv array Aluminium frame installed on front roof pitch for seamless solar pv array
-
Tiles on rear roof pitch Tiles on rear roof pitch
https://passivehouseplus.ie/magazine/upgrade/phit-the-bill#sigProIdf7a9e5318f
Construction Photos: Jigsaw Design and Construction Ltd
Once work resumed, McNeill found more remedial work was necessary. “We ended up removing every partition upstairs. It was clinker block, built off floorboards with no support,” she said.
It only takes a fleeting comparison of the before and after photos of the house’s exterior and interior to get a sense of how extensive the remodelling and renovation works to the building were. The budget - £378,000, excluding VAT, site purchase and fees – is not insubstantial. But readers should pause for thought before drawing conclusions from this project about the cost of deep retrofit. The house was gutted from top to bottom, and completely remodelled.
The pertinent question would therefore be: what would the marginal extra cost be for the energy efficiency measures – or more precisely, the marginal extra cost for the extra energy efficiency measures beyond those required under building regulations for renovations of this nature?
Such a question may be beyond the scope of this case study – in truth it may require a significant article or academic paper in its own right. But the question of energy use and costs does bear asking, in spite of the energy crisis making price estimate hard to gauge.
We’re in a conservation area and the south-west pitch directly faces the road and no one else had solar installed
“Financial break-even was never the goal – simply energy and ideally CO2 net zero,” says Jonathan Dixon.
The use profile is key to understand. Sharing the house with their two cats, Jonathan and Emma Dixon both work from home.
“I have a lot of energy use for my work – several computers for software development projects,” says Jonathan Dixon. “Our overall usage is well outside the PHPP model for normal users.”
Aside from the energy saving elements that characterise passive and Enerphit projects – airtightness, high levels of continuous insulation, triple glazing and heat recovery ventilation – the project benefits from a number of other elements to reduce exposure of a household and office with high energy utility needs, to volatile energy prices.
The mammoth PV array has recently been paired with a 10 kW battery, and the house’s heating and hot water is generated by a Mitsubishi air-to-water heat pump, with a Showersave wastewater heat recovery system stopping precious energy from literally going down the drain. The net effect? Ultra-low energy use at the heat pump of 1,247 kWh per year. Even with the substantial contribution the PV array would be making to help meet that demand, particularly for hot water, the cost would be £424 per annum based on the UK’s current energy price cap.
But this doesn’t tell the full story. Taking account of the building’s extraordinary energy efficiency, export tariffs for selling spare electricity back to the grid, and the Dixons’ efforts to reduce the house’s baseload, Jonathan makes a startling claim in an energy crisis. “I might well make an operating profit on energy generation in the next year, but I’ll need to wait a year to really tell,” he says.
From London dirt and damp to fresh air
Retrofit is something I’ve always wanted to do, and it’s really not taught in architecture school
Although the decision to install heat recovery ventilation is effectively a precondition for passive houses in UK climate zones, Dixon was never going to object, based on his previous experience of older British houses.
“The 1930s house we previously owned in London was always damp and we were always opening and closing windows. With this, we wanted to keep the noise out, keep the dirt out and have better air quality. There’s so little dust in the house it’s something we just never think about and obviously there’s no damp. It doesn’t build up from even internal sources.
“One thing it doesn’t do is completely solve overheating risk. And that’s the one thing we didn’t model on a room-by-room basis” he said, though the issue was modelled in PHPP on an overall building basis.
Both client and architect agree that the final result was worth the effort, however. For example, Dixon says the performance of the building exceeds any expectations people typically have of retrofits. “We’re twice as airtight as we need to be for a retro. It’s as good as a new build. That required a constant attention to detail,” he said.
For McNeill, the house, and indeed the experience of the project, serve not only as proof that deep retrofits could transform the country’s housing stock, but also as a means for her to explain how retrofits should be approached and even taught.
“Retrofit is something I’ve always wanted to do, and it’s really not taught in architecture school. Explaining it to other people really helped me understand what I was doing,” she said.
Selected project details
Architect & passive house designer: A D Practice Ltd
M&E design: Enhabit Ltd
Civil/structural engineer: Phil Harvey and Pat Roberts
Thermal bridge calculations: Heatflux
Main contractor: Jigsaw Design & Construction Ltd
Airtightness tester/consultant: Aldas
Wood fibre insulation: Pavatex, via Soprema
Cellulose insulation: Warmcel, via PYC
PIR: Celotex & Xtratherm
OSB: Medite Smartply
Render: Baumit
Timber cladding: Sivalbp, via Vincent Timber Ltd
Windows and doors: Internorm
Roof lights: Fakro
Heat pump: Mitsubishi, via Solid Renewables
Heat recovery ventilation: Zehnder, via Green Building Store
Wastewater heat recovery: ShowerSave
PV: GB Sol
Lighting design: Focalglow
EMBODIED CARBON
The embodied carbon of the house was calculated by Tim Martel, author of the AECB’s PHribbon calculation tool, and assessed against the RIBA 2030 Climate Challenge targets. The partial scope included the substructure, superstructure, roof, windows and external doors, heat pump, heat recovery ventilation system, solar PV array, and ceramic fittings for three new bathrooms. Items that were omitted included ductwork and piping, new internal walls and partitions, internal doors, stairs, and finishes for internal walls, floors and ceilings.
The results, as ever need careful interpretation. The cradle-to-grave total for the building came to a whopping 1,161 kg CO2e/m2 – approaching double the target of 625 kg CO2e/ m2 set for new homes by RIBA. But closer inspection gives a clearer sense of why.
The biggest issue by far is the 48 m2 solar PV array. In the absence of an Environmental Product Declaration (EPD) for the specific modules used for the roof, default values for PV from the ICE database were used, and assuming the modules had a 25-year lifespan – meaning two full replacements within the 60-year building life assumed for RIBA 2030 Climate Challenge calculations. If the PV modules are assumed to be the Sunpower Maxeon 3, which currently have an EPD showing the lowest embodied CO2e of any PV module on the market, the total drops to 761 kg CO2e/m2, and if the PV modules are excluded, the whole building total drops to 575 kg CO2e/m2. It’s worth noting that the PV array calculations included the modules only – and therefore excluded the mounting system, inverters, and the 10 kWh battery recently added by the Dixons. A recent report, ‘Whole life carbon of photovoltaic installations’, by LCA consultants Elementa for Willmott Dixon showed that the inverter, mounting system, ballasts and optimisers can be roughly equivalent to the embodied carbon of the PV modules over 25 years, with optimisers in particular having a big impact.
Optimisers weren’t used in this project, but a large battery was. Critically, that report also showed that the PV arrays in the study saved roughly double the amount of carbon emissions embodied in the arrays, due to reduced operational energy use.
Windows, doors and roof lights added 95 kg CO2e/m2, but again caveats must be added. In the absence of an EPD for the Internorm windows used on the project, an EPD for NorDan aluclad windows was used for the calculations. NorDan’s EPD includes a 60-year reference service life. The NorDan EPD also includes a figure for the estimated emissions cleaning the windows during the 60-year lifespan. The emissions for the windows and doors added 39 kg CO2e/m2 to the building’s upfront emissions, 29 kg CO2e/m2 in the use phase and 13 kg CO2e/m2 assumed to be released at the building’s end of life.
The figures for the heat pump and air-towater heat recovery ventilation – once again in the absence of EPDs – were based on default data, in both cases from industry association Product Eco Passports which included 17- year reference lifespans, therefore including three replacements each within the 60-year lifespan, adding a combined total of 119 kg CO2e/m2 to the building’s score (24 upfront, 94 in the use phase, and 1 kg CO2e/m2 at end of life).
The substructure – including new concrete slab, PIR insulation, concrete floor screed and timber floorboards – adds 109 kg CO2e/m2. The external walls and roof added 105 and 49 kg CO2e/m2 respectively, but this does not tell the whole story. At the point of practical completion, the wood fibre insulation and timber products used meant that the 162 kg CO2e/m2 to manufacture and transport these elements to site was offset against a whopping 424 kg CO2e/m2 stored in the fibres of the timber – a net figure of -262 kg CO2e at this stage. At the end of the building’s 60- year reference life period, it’s assumed that the building is taken down, and that the CO2 sequestered in these elements is either released into the atmosphere, or passed onto a future use in the event of materials being salvaged – meaning the benefit of that sequestration would reside with that future use. But dwellings can last much longer than 60 years – the historic average housing stock replacement of dwellings in the UK is 0.5 per cent per annum, indicating a 200-year life span. In a world where issues like resource use are bound to become increasingly significant, it doesn’t seem unreasonable to hope and expect that a high-quality building such as this will remain in use for centuries, meaning there must be a good chance that the CO2e sequestered in the building fabric is not allowed to escape.
In detail
Project overview: A 1960s four-bed detached property in the Harpenden conservation area, which has been retrofitted to the Enerphit Plus standard. The original house was a typical cross-wall construction with cavity brick/block flank walls. To provide the required levels of insulation, the ground floor was removed and replaced with a new insulated slab. The external flank brick walls were externally insulated, the original infill structure to front and back was replaced with site constructed timber insulated framing. The triple glazed windows have additional glazing with integrated blinds on the south side, to avoid overheating. The roof was insulated over the existing frame, with tiling to the rear and a complete roof integrated solar PV system forming the entire front roof slope. The final airtightness testing showed a figure of 0.59, well within the Enerphit requirement. The use of sustainable materials was very much to the fore, with most insulation being cellulose, or woodfibre based and using timber glulam beams instead of steel for structural elements.
Building type: 151.4 m2 detached house from 1960s. Renovation including Enerphit Plus retrofit and single-storey rear extension.
Site type & location: Suburban site, Southdown Road, Harpenden, Hertfordshire
Budget: £378,000 (construction only, not including VAT, site purchase or professional fees)
Completion date: November 2021
Passive house certification: Certified Enerphit Plus
Space heating demand (PHPP): Before: N/A
After: 23 kWh/m2/yr
Actual energy usage: 8.2 kWh/m2/yr
Heat load (PHPP):
Before: N/A
After: 12 W/m2
Primary energy non-renewable (PHPP):
Before: N/A
After: 84 kWh/m2/yr
Primary energy renewable (PHPP):
Before: N/A
After: 35 kWh/m2/yr
PV generation: 43.8 kWh/m2/yr
Heat loss form factor (PHPP): 3.32
Overheating (PHPP): 3 per cent of year above 25 C
Number of occupants: 2 adults & 2 cats
Energy performance certificate (EPC)
Before: D 60
After: N/A
Measured energy consumption*
Before: N/A
After: 8,056 kWh/yr total electricity consumption, including 5,011 kWh imported from grid, 6,630 kWh generated by PV, of which 3,585 kWh was exported to the grid.
(*Based on electricity bills March 2021 – March 2022)
Measured energy consumption for heating: 765.7 kWh (space heating) and 481.8 kWh (domestic hot water), measured directly from the heat pump – irrespective of whether imported or self-generated electricity. Ignoring the contribution the PV array is making to help power the heat pump, and therefore assuming only grid electricity – at the current energy price cap for England of an average of 33p, the cost would be £281.40/yr for space heating and £177.96 for hot water. In reality both figures will be lower, due to the contribution from PV.
Solar payment:
Profit from excess solar sales: £225 (March 2021 – March 2022)
Airtightness (at 50 Pascals)
Before: 7.7 air changes per hour
After: 0.6 air changes per hour
Ground floor:
Before: Uninsulated concrete floor
After: 65 mm screed on vapour and airtight barrier with 160 mm Celotex GA4000 PIR insulation in main house, 260 mm in extension (thermal conductivity 0.022 W/mK), DPM, 100 mm concrete slab on 150 mm compacted hardcore with concrete trench foundations. U-value: 0.127 W/m2K / 0.08W/m2K in extension.
Existing walls
Before: Brick and concrete block cavity walls with retrofitted full filled 75 mm cavity at gable walls. Front and rear walls were thin curtain walls.
After: Render/timber cladding on 200 mm Pavatex Isolair woodfibre insulation (thermal conductivity 0.041 W/mK), existing full filled cavity wall, Smartply Propassiv for airtight layer, 25 mm service void, plasterboard and skim. U-value: 0.129W/m2K Curtain walls/extension: Render/timber cladding on 80 mm Isolair (thermal conductivity 0.041 W/ mK), 300 mm I studs with Warmcel cellulose blown in between (thermal conductivity 0.038 W/mK), Smartply Propassiv for airtight layer, 25 mm service void, plasterboard and skim. U-value: 0.109 W/m2K Existing roof
Before: Concrete tiles on trussed rafter roof, 200 mm mineral wool insulation at ceiling level
After: Pitched roof with concrete tiles on battens/ solar PV array over 30 mm Isolair (thermal conductivity 0.041 W/mK). This was fixed to new timbers placed on top of existing structure to increase the depth to allow for 240 mm Pavaflex woodfibre insulation (thermal conductivity 0.038 W/mK) and underlined with 60 mm Pavatherm Combi (thermal conductivity 0.041 W/mK). Airtight membrane, battens to form service void, plasterboard and skim. U- value: 0.135 W/m2K
Flat roof: EPDM membrane on ply over 100 mm Isolair (thermal conductivity 0.041 W/mK), 200 mm Pavatherm (thermal conductivity 0.038 W/mK), 220 mm timber joist, Smartply for airtightness, service void, plasterboard and skim. U- value: 0.103W/m2K
Windows & doors
Before: Poorly fitting aluminium framed double glazing
After: New triple glazed Internorm HF310, HV350, HT 410 timber aluclad windows and doors. Overall U-value: 0.85 W/m2K
Roof windows: Fakro FTT U8 thermally broken quadruple glazed roof windows with thermally broken timber frames. Overall U-value: 1.01 W/m2K
Fakro DEF DU8 quadruple glazed flat roof window. Overall U- value: 0.71 W/m2K
Heating system
Before: 20+ year old oil boiler & radiators throughout entire building
After: Mitsubishi Ecodan PUZ-WM85VAA (COP 4.62 @ 35C) with underfloor heating downstairs and dual fuel towel radiators in bathrooms. Immersion element powered by solar PV in Oso Delta Geocoil DGC 300 cylinder to aid with hot water.
Ventilation
Before: No ventilation system. Reliant on infiltration, chimney and opening of windows for air changes.
After: Zehnder ComfoAir Q350 enthalpy heat exchanger heat recovery ventilation system — Passive House Institute certified to have heat recovery rate of 86 per cent.
Water: Low flow fittings and ShowerSave heat recovery to main shower room. Rainwater harvesting for garden use via water butts.
Electricity: 48 m2 GB-Sol Roof Integrated Solar photovoltaic array to entire front roof pitch with average annual output of 6.6 MWh, with 3.4 MWh exported to the grid. No storage, prioritised for ASHP, domestic hot water heating via immersion and electric car charging, excess electricity exported.
Sustainable materials: Timber frame using FSC certified timber, woodfibre and cellulose insulation, all timber furniture from PEFC certified sources. All new structural members in FSC certified glulam rather than steel.
Image gallery
-
Construction Issue Floor Plans Construction Issue Floor Plans
-
Construction Issue Elevations and Sections Construction Issue Elevations and Sections
-
Construction Issue Site Plan Construction Issue Site Plan
-
Flat Roof Details Flat Roof Details
-
Pitched Roof Details Pitched Roof Details
-
Ground Floor Details Ground Floor Details
-
Wall Junctions and Intermediate Floor Details Wall Junctions and Intermediate Floor Details
-
Window and Door Details - Sheet 1 Window and Door Details - Sheet 1
-
Window and Door Details - Sheet 2 Window and Door Details - Sheet 2
-
Windows and Doors Windows and Doors
-
Garage Details Garage Details
-
MVHR Layout and Details MVHR Layout and Details
https://passivehouseplus.ie/magazine/upgrade/phit-the-bill#sigProId9f4a4ea1a7