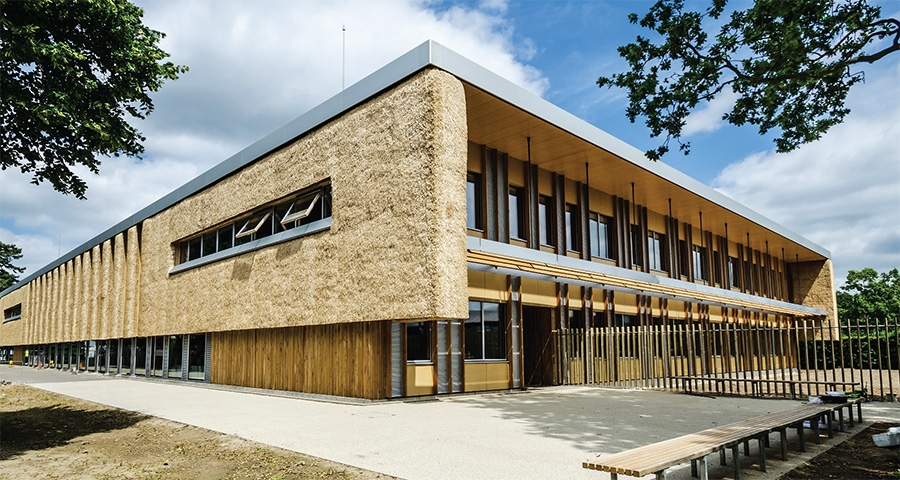
- New build
- Posted
Is this the UK's greenest building?
This summer, work was completed on the Enterprise Centre at the University of East Anglia, which might just be the most sustainable large building ever constructed in Britain.
The backstory to the Enterprise Centre at the University of East Anglia (UEA) in Norwich, arguably started many years ago in the line of UEA buildings that pushed the boundaries when they were built. UEA's continuous improvement programme is evident as a physical story, which paves the way to what must be their greatest achievement yet.
John French, CEO of the university's Adapt Low Carbon Group and project director, joined UEA in 2008. French was eager that the next generation of buildings at UEA should move away from high thermal mass and a dependence on carbon-intensive concrete, towards natural and locally sourced materials.
But UEA's ambitions didn't stop there — they wanted to achieve the highest standards across the board.
French says: "I was concerned that we could end up with a very low embodied carbon building, which was what we wanted, but not necessarily achieve high levels of performance. So we looked around and we decided after much consideration that we would adopt the passive house standard."
The thatch cladding is perhaps the most distinctive feature of this building; three hundred panels were manufactured and thatched off-site, and the panels then hooked onto horizontal battens lining the perimeter of the building. The building also features a wide array of other sustainable materials including recycled timber finishes, wood wool acoustic boards, spray-on cellulose, and wall coverings made from hemp, nettle fabric and reeds
The brief set the bar extremely high, demanding a minimum of 70% bio-based materials, a threshold for embodied carbon, passive house certification, a Breeam Outstanding rating, and local sourcing and supply of materials. Stepping away from UEA's routine procedure of appointing an architect to design a building and then putting it out to the market to see who could build it, the university decided to appoint a single-point delivery contractor and to hold an architectural design competition.
"All the entities that were bidding had to provide us with a good financial plan, a good low carbon and energy plan and a good architectural design,” explains French. “They had to put in all that simultaneously to win the commission."
Morgan Sindall was appointed as the single point deliverer, and the company worked alongside project architects Architype on the building design, passive house modelling and embodied carbon plan.
It's important to note the level of collaboration that this project demanded and achieved. Everyone bought into the ethos of performance with minimum environmental impact and worked closely to innovate around numerous practical obstacles.
No stone was left unturned during the design process. UEA's Climate Change Unit looked at the future impacts on the building with an increase in temperatures and extreme weather events. This informed the design, most notably shading.
Gareth Selby, an associate at Architype and passive house designer on the project, says: "Life cycle carbon was one way to sum up the operational carbon and the embodied carbon. Everything was assessed with that attitude rather than just looking at how good is it for passive house. It was bringing the two together."
The Cygnum timber frame structure, primarily made of locally grown pine
Domestic hot water was the biggest challenge when it came to the building's life cycle carbon emissions. At first there was a lack of data available on how much hot water university buildings use, and inputting occupancy info from other building types immediately put the Enterprise Centre over a primary energy demand of 120 kwh/m2/yr, the maximum allowed under the passive house standard.
Selby explains: "The hot water usage and how we dealt with it became a critical issue. Fortunately UEA had done post occupancy analysis on the Elizabeth Fry Building and Thomas Paine Building. We were then able to data mine those projects and try to estimate what the actual hot water usage was, both in terms of energy and litres of hot water per person. So there was a blended analysis to come up with the figures."
The team also worked with UEA to drive down the amount of power usually specified for rooms such as lecture theatres.
The building’s 480 square metre rooftop solar photovoltaic array; The Isoquick insulated foundation system that eliminates thermal bridging; The Siga Majcoat wind-tight membrane on the roof provides protection from the elements while being breathable
The project also had a welcome visit from Passive House Institute founder Dr Wolfgang Feist, who was able to cast his eye over some of the plans. One quandary that coincided with his trip was whether to connect the Enterprise Centre to the university's district heating and combined heat and power (CHP) network.
The network was some distance from the building, and with heat loss on the pipe runs there was a cut-off point after which it would not be worth connecting. Feist offered practical input, suggesting that as the university was invested in its district heating network, and were maintaining and managing the system, it probably made sense to connect.
As with any construction project, it was essential to keep a close rein on costs. French pinpoints this as the biggest obstacle along with keeping the project ‘on mission.’ In autumn 2013 French faced some tough decisions that could ultimately have led to sacrificing performance criteria to keep costs in check.
Triple-glazed Protec windows allow natural light into the building, illuminating the many natural materials and surfaces
"Right in the middle of what's politely called value engineering,” French reflects, “when you've been presented with a finely tuned design and you've also been presented with the fact that the cost is way off where you predicted it to be, so you either go back to the drawing board and scrap the whole scheme or you have to find a way of delivering it on budget."
At one point, going for the passive house standard was even in jeopardy because to take that out would have cut costs, but the whole team worked together to get costs under control.
Changes such as manufacturing the trussed timber roof system off site and replacing the lecture theatre's steel frame with a timber truss system helped to save both money and carbon.
French continues: "Through very good team working and incredibly effective architects practice... Architype have been brilliant in helping us find solutions to get passive house at a sensible cost."
The Enterprise Centre is of timber frame construction. Having previously developed a relationship with Irish timber frame manufacturer Cygnum on their passive house schools, Architype was confident it could fulfil the demand to source the timber locally.
John Desmond, managing director of Cygnum, says: “With the aid of Morgan Sindall I was able to meet with the Forestry Commission and determine what type of wood was available locally in their forest, which was predominantly Corsican Pine.”
It’s common for British timber to be used for lower grade applications, while a supply for construction is typically imported from Scandinavia.
Desmond continues: “I met with a local timber processor and was able to agree a model that would allow them to take in Corsican Pine logs, process them and was able to organise to have the processed timber kiln dried and graded in Ireland.”
Despite the timber heading to Ireland and back, Desmond says it was still an effective solution compared to importing form Scandinavia. It helped to fulfil the low-carbon brief and demonstrated that it is possible to use locally sourced timber for more demanding purposes.
But producing the timber frame was still quite technically demanding. “In effect we’re producing a 3D jigsaw with thousands of components,” Desmond illustrates. “Getting every one of those components to work structurally and architecturally is what it’s all about.”
In 2014 the project went onto site. James Knox, senior engineer for single point deliverer Morgan Sindall, explains how things differed to most projects: "There are many different materials that we're not used to using and completely innovative materials on the project which have never been used before. The low-carbon concrete, for example, was designed specifically for this project and the thatching method, which our team conceived, is a world-first.” The concrete makes substantial embodied carbon reductions, replacing 70% of Portland cement with ground granulated blast furnace slag (GGBS), a fine ash created as a by-product of the steel smelting process, along with with recycled sand and certified responsibly sourced aggregates.
The thatch cladding is perhaps the most distinctive feature of this building. But the ancient craft of thatching is time-intensive, so a more modern approach was needed.
Morgan Sindall proposed the idea of off-site manufactured thatch panels that could be delivered to site and lifted into place. Working together with master thatcher Stephen Letch, they created a sample on site and mocked up how the panels would be fixed. Then, threehundred panels were fabricated at a local joinery shop and sent to Stephen's barn to be thatched.
Morgan Sindall's James Knox says: "Normally over the winter period he doesn't really have much work on. We gave him and four other thatchers a couple of months' work while it was wet, windy and snowing outside. He was working in the warm, pre-thatching our panels off-site."
This worked well. The panels hooked onto horizontal battens lining the perimeter of the building. As all the panels weren't identical, they were delivered to site in a special sequence. Once attached to the building they were trimmed in situ or given a 'haircut' if needed.
Knox was also the passive house champion on this project, which achieved a superb final airtightness test of 0.21 air changes per hour at 50 pascals.
"If there was anything we weren't 100% sure on with regards to passive house, he'd [Selby] come out and brief us on it,” says Knox. “We had a passive house induction presentation he gave to us and in turn we gave the same to our supply chain as and when they were inducted."
The Enterprise Centre was completed in June 2015. The building was designed for a 100 year life span, and is expected to be responsible for less than 500kg of CO2 per square metre over this time. Knox commented: “The quality of the finished article is one of best I have ever worked on.”
It seems that this is a view that is shared not only by those who’ve been working on the project but those who are now using the building.
John French observes: “Everybody who’s using the building now absolutely loves it. The feedback on how the building feels to the user, the ethos, air quality, natural materials, the spaces we’ve created. Everybody is completely wowed and blown away by the building.”
Gavin Napper, Morgan Sindall area director, adds: “This is a building which is deeply rooted in its surroundings. Our team’s commitment to using indigenous materials, like reed, clay, and hemp, coupled with its focus on utilising local suppliers, contractors and craftspeople, gives the building a real sense of identity and enhances its connection to Norfolk.”
The story of the Enterprise Centre is far from over. It will take several months to optimise the building’s performance, and in-depth performance monitoring and analysis is planned. The project may also be the first in the UK to track almost every square millimetre of timber used, along with many other aspects. These findings will all be published in due course.
Selected project details
Client: University of East Anglia
Single point delivery & contractor: Morgan Sindall
Architect: Architype
M&E, structural & acoustic consultants: BDP
Lifecycle cost analysis: BSRIA
Landscape: Churchman Landscape Architects
Timber frame: Cygnum
Insulated foundation: Isoquick
Cellulose insulation: PYC Insulations
Windows & curtain walling: Protec
External doors: Raico
Roof windows: Fakro
MVHR: Swegon
Gypsum plaster: British Gypsum
OSB boards: Medite Smartply
Wood fibre insulation, earth & clay plasters
& natural paints: NBT
Airtightness products: Siga
Thatcher: Stephen Letch
Timber cassettes: Fox Joinery
Spruce ply: Wisa Plywood
Cellulose acoustic finish: Sonaspray
Acoustic panels: Troldtekt
Wood finishes: Osmo Oil
External grade MDF: Medite Tricoya
Lime renders: Baumit
Recycled rubber flooring: Jaymart
Hemp & nettle fabrics: Camira Fabrics
Recycled glass screed: Ecoscreed
Low carbon concrete: Lafarge Tarmac
Recycled sand for concrete: JT Few
Natural linoleum: Forbo
LED Lighting: Fagerhult
Rainwater harvesting: Pipex PX
Solar PV & bitumen roofing: Bauder
Additional info
Building type: 3,400sqm (gross internal floor area) detached two-storey timber frame enterprise centre/ business hub
Location: University of East Anglia Campus, Norwich
Completion date: June 2015
Budget: £11,600,000
Passive house certification: pending
Space heating demand (PHPP): 8 kWh/m2/yr
Heat load (PHPP): N/A
Primary energy demand (PHPP): 115 kWh/m2/yr (figure may improve further once the efficiency of UEA's CHP network is incorporated)
Environmental assessment method: Designed to Breeam Outstanding
Airtightness (at 50 Pascals): 0.21 ACH
Thermal bridging: Thermal bridging was modelled where glulams sat within the cassette (2 locations only). In all other areas a minimum 200mm insulation band was maintained. The following steps helped to achieve this: timber construction throughout, insulation under slab used as formwork, larsen truss zone in the timber frame to create a continuous 200mm duvet layer, overhangs created by cantilevering glulam beams on top of the roof deck rather than in the i-joist zone, mid level bride soleil is fixed to the facade breather/ sheathing board zone via a stress plate so it does not penetrate the duvet zone, high density insulation used to form door thresholds, high density insulation used to support ground floor glazing directly.
Ground floor: Raft foundation with 250mm Isoquick slab underneath. U value: 0.128 W/m2K
Walls: Cygnum factory-built timber frame featuring, from the outside in, cladding on battens and counter battens (cladding consisting of either thatch cassettes, recycled chemistry lab tables, Medite
Tricoya, Baumit lime render or reclaimed oak from local council felling, Sarket breather board. 200mm larsen truss with Warmcel insulation (blown cellulose), 140mm structural stud zone insulated with Warmcel, 18mm OSB3 airtight layer, 50mm service cavity zone, Birch faced ply, lime render or timber slats to internal surface. U-value: 0.122 W/m2K
Roof: Cygnum factory-built timber frame with (outside to in): Bauderflex bituminous roof membrane, 25mm ply deck, ventilation zone, Siga Marcoat breather membrane, 15mm breather sheathing,
300mm I-joist fully filled with Warmcel insulation, 18mm OSB3 airtight layer, 2 x layers of 15mm Soundbloc plasterboard. U-value: 0.132 W/m2K
Windows: Protec aluminium/timber composite windows. Overall U-Value of 0.77 W/m2K, G-value 0.49. Doors are Raico Frame + Passive House Institute certified units with overall PHI certified Uvalue
of 0.8 W/m2K. 6 x Fakro DEF DU6 electrically-opened flat roof windows. Triple-glazed 120x220cm units, with a U-value of 0.81 Wm2K.
Heating system: Custom built heat interface unit linked to UEA's district heating and combined heat and power network
Ventilation: 3 x Swegon Gold RX Passive House Institute certified MVHR units with efficiencies ~85% using thermal wheel. Auditorium AHU also fitted with cooling coil with condensers in exhaust air duct.
Electricity:A 49.6 kW 480 sqm Bauder solar photovoltaic array, divided between 160 modules, predicted to generate 43.58 MWh in the first year.
Green materials: Low carbon concrete using 70% GGBS & recycled sand, recycled sub-base from local demolition, most timber for framing sourced from local forest, local larch used for glulams, lift shaft made from cross-laminated timber, domestically sourced OSB, local straw used for thatching (and by-products used for local flour and beer production), external grade MDF for courtyard cladding, Iroko
cladding from old lab desks at UEA, recycled reception desk, wood wool acoustic sound boards, sprayon cellulose acoustic finishing treatment, recycled car tyre flooring, solvent free natural-based paints and oil finishes, ecological wall coverings (including hemp, nettle fabric, earth board, reed boards), low maintenance and long life diamond-ground concrete floor (incorporating low carbon cement), upper floors finished in Marmoleum (linseed and hessian matting on recycled glass screed).
Image gallery
Passive House Plus digital subscribers can view an exclusive image gallery for this article. Click here to view